精益生产在生产现场改善中的应用研究
摘 要:本文为解决企业中出现的一些资源浪费及如何降低成本,通过对精益生产的相关理论的研究,分析了精益生产的特点及其优越性,并以精益生产理论体系为基础,对现场改善理论进行了研究,对于有效的减少作业过程中的人员浪费,均衡工作地负荷,提高生产线的生产效率具有一定的指导意义。
关键词:精益生产;现场改善;瓶颈工序;平衡产线
0 引言
从十九世纪二十世纪初,以有管理学之父之称的泰勒首先引领了工业工程的管理思想的开始,人们开始逐渐的认识到现场改善的重要性,其动作分析理论中的\"动作经济原则\"和\"基本动作要素分析\"至今仍被广泛运用到需要现场改善的各个领域中。
随之从二战后,日本的大野耐一和丰田英二创立的全新丰田生产模式(TPS),到1985年美国麻省理工学院创立的\"精益生产\"理论体系。以及在之后衍生出来的\"5S\",\"6sigma\"的管理方式,到九十年代提出的业务过程再造概念(BPR),二十世纪末的\"现场低成本改善永恒论\",现场改善的理念随之越来越追求精益化,同时也为世界的生产发展提出了更加苛刻的要求。
目前随着世界经济的飞速发展,作为以生产模式为主的企业逐步面临市场带来的压力。尤其是对于我国的发展状况来说,自从我国加入WTO后,面向世界诸多竞争,企业的发展方向逐步转变为适应个性化、多样化、随机化的趋势,由以前的生产主导企业到后来的市场主导企业到现在的顾客主导企业,我国国内的生产模式也不断的在面临新的挑战,如何在同类的生产企业中脱颖而出,如何在竞争全球化的现状中生存,更快速的适应趋势,适应新的环境都是企业所要解决的问题。
本文通过对企业的现场分析,将精益生产的理论与现场改善的方式进行紧密的结合,根据一定的思想归纳,从而达到说明问题,改善问题最终达到实现企业生产的低成本、高效率、高质量的目的。
1 精益生产和生产现场改善概述
(一)精益生产
精益生产(Lean Production)是以遵循\"消除浪费\",\"关注流程,提高总体效益\",\"建立无间断流程以快速应变\",\"降低库存\",\"全过程提高质量\",\"基于客户需求拉动生产\",\"标准化与工作创新\",\"尊重员工,给员工授权\",\"团队合作\",\"尽可能满足顾客需求\",\"精益供应链\",\"自我反省,深入现场\"等原则来实现提高生产效率,增加顾客满意度,降低企业生产成本的目的。
精益生产是以人为本,以消除浪费为核心,以零库存、高柔性、零缺陷为目标,用最经济的方式进行生产和制造。并通过系统结构、人员组织、运行方式和市场供求等方面的变革,使生产系统能很快适应用户需求不断变化,并能使生产过程中一切无用、多余的东西被精简,最终达到包括市场供销在内的生产的各方面最好结果的一种生产管理方式。与传统的大生产方式不同,其特色是\"多品种\"、\"小批量\"、\"低消耗\"、\"低成本\"、\"高效率\"。精益生产的实施同时可以大幅度的减少在制品的积压,降低机器等待时间,挺高生产效率,因而被誉为继手工业生产方式、大量生产方式之后的第三个里程碑。
(二)生产现场改善
对于生产现场,它是生产型企业的重要的一部分。其指实地,行动发生的场所。而对于现场的改善则是一种直接缩小企业生产成本的最有效,也是最容易掌控的方法。其意义也就是对工作场所的所有要素进行优化改良,以提高工作效率以及产品质量。而企业要实现现场的高效率运行,就必须着重保证现场的管理以及深化。
2 精益生产在生产现场改善中的应用
(一)基本思想
(1)改善效率
现场的改善效率手段主要包括劳动生产效率、物流效率、管理效率。通过改进生产工艺,改善工作地布置,发挥人的能动作用等对生产系统进行优化。着重于减少生产过程中出现的等待停滞问题,抓住生产的\"瓶颈\"来平衡生产线,保持一定的生产同步。在此基础上也通过合理分配作业人员数量,避免出现工作量不均,同时也尽可能提高设备的利用率。
(2)降低成本
生产成本是由生产的原料、人员的合理利用、管理费用等几个方面组成。通过对现场的掌控、调整,做到尽量控制发生在生产过程中的缺漏而带来相应的库存成本、采购成本、人力资源成及管理成本等。通过提高原材料的利用率,降低原材料库存率及半成品的库存,以及采购原材料过多等一系列的采购成本。通过合理分配作业人员,培养多技术人才,充分挖掘每个人的潜能,从而降低人员成本。通过改善工艺流程,调整现场布局,使生产中尽可能少出现因流程不清或因人员的疏忽而造成的管理成本。
(3)提高质量
分析表明大量的生产产品的质量问题90%都是在生产中发生的。通过对生产流程的全程监控在可以保证质量的基础上加强对生产现场的环境、工艺要求、设备等的合理持续改善,可以从根本上减少甚至消除产品的质量问题,始终做到一切以产品质量为中心。而现场改善已成为高质量最有效,也是最根本的手段之一。
(4)提高市场竞争力力
在当今以服务为主的企业中,发展动力源自于对顾客满意度的提高。而基于企业之间外部的服务趋势在当今也是处于同步发展,不断效仿之中,所以顾客对于怎样去选择企业的产品归根到最根本还是源自于企业内部的生产管理及环境。从而对于企业之间的竞争也归结到对于怎样控制生产成本,提高效率,提高质量中去。
(5)准确掌控交期
交期对于企业与客户之间的信誉度、合作意向都产生着重要的影响。对于企业掌控交期主要通过两个方面进行:一是通过足够的生产力和相互的紧密沟通加强与合作伙伴的关系;二是通过对现场实时的掌控能力。从以上两个方面可以看出企业对于通过持续改善的方式提高生产率所带来的价值。通过不断改善更新的生产模式,及时准确的对生产的各个环节下达指令,把握企业生产的准时性、准确性,从而确保准确的交货日期。
(二)基本方法
现场改善的方法中会大量涉及到与\"工业工程\"和\"精益生产\"两类的方法体系,其中分别包括设备布局优化、方法研究与作业测定、生产平衡、\"5S\"管理、看板管理、持续改进流程等内容。
(1)设备布局优化
设备布局指在操作现场对多种设施的一种科学布置方法,其优化主要指将设施更好的成组匹配使用,使其可以达到能按工艺方法连续进行生产,使生产过程更加便捷,操作流程更加顺利,同时为工作人员提供了舒适的操作环境,最终达到可以提高生产效率的目的。
(2)方法研究与作业测定
方法研究即通过程序分析和动作分析追求简洁、高价值、高效率、安全和低成本的目的。对工作流程中出现的不合理、低效率、浪费等缺陷环节,加以改进,为操作人员提供舒适的工作环境。作业测定则是与方法研究相结合,通过运用标准测时法、预定时间标准法(PTS)、工作抽样法等技术手段对工人合格作业量进行时间的测定。两者主要是为了通过研究分析,制作出最佳作业系统、改善系统及制定标准时间。
(3)生产平衡
生产平衡就是通过对生产现场的研究分析,用一定的方法测量工作流程中的闲置、高负荷的不均衡生产,而其影响的因素也有多种,如操作人员分配不合理、生产节拍紊乱、作业时间、排序等。并通过一定的改进方法使其达到减少在制品的积压、生产浪费、低效率等负面影响,以下为平衡生产的有关步骤方法:
①确定生产节拍
生产节拍又称线速,他是控制生产速度的指标。而生产速度的目的则是保证各工序按统一时间生产加工零件,以达到生产的平衡与同步化。其含义是顾客每隔多少秒有一个产品的需求。而其计算的关键则是确定有效生产时间和一定周期内顾客的平均需求。
需求周期则是建立在一定时间范围内生产数量相对稳定的基础之上的,并且需要考虑计划内停工与计划外停工的时间影响。
其计算公式为:生产节拍=有效生产时间/顾客需求
②比较生产平衡率
δ=■
δ:生产平衡率 n=作业元素的个数 m=各工位人员数
C=生产节拍 单位:分 ti=各个工序标准作业时间(i=1,2…)单位:分
当生产线的平衡率处于60%~70%这个区间,则该生产线并没有存在一定的科学管理的意识;当平衡率在70%~85%区间时,则改生产线的控制基本上采用的是科学管理的原则;当生产线的平衡率超过85%时,则该生产过程便可认为是最优生产方式下进行的。
(4)\"5S\"现场管理
①整理(Sciri)
对现场摆放的物品及在生产现场出现的生产用料、半成品或成品进行有无用的区分,将需要的物品留下,其它物品全部清除现场。其目的是为生产提供足够空间以便物流的进行,并且可以防止物品的误用、错用的发生。
②整顿(Seiton)
对现场生产中需要物品进行科学合理的整齐摆放,并加以标识。目的是为消除物品的寻找时间,做到可以对现场物品摆放一目了然,减少等待时间。
③清扫(Seiso)
对现场的设备、工具、物品及地面进行清扫维护。目的是为了保证现场环境对工人工作情绪的影响,同时保证设备的精度,消除因杂乱而导致的生产事故的发生。保证现场干净整洁,运行流畅。
④清洁(Seiketsu)
是对生产工作人员进行自身的提高。强调好的工作环境,对设施的维护。目的是营造一个良好的工作环境,使生产可以有序的进行,从而迎合\"5S\"的管理方式。
⑤素养(Shitsuke)
对生产工人的自身素质的提高,使其养成良好习惯,遵守规章制度。目的是为了培养出一个有素质、有纪律、积极向上的工作团队。
(5)看板管理
①意义:看板管理是对企业JIT生产方式一个重要的保证,其对MRP的正常准确运作也起到重要的作用。其适应拉动式的生产方式,根据客户的需求进行全面的生产信息的归结、显示。其信息包括零件型号、数量,以保证完胜相关生产。②目的:保证供货与生产之间的一致性,使生产可以正常运转,以保证加工的稳定,原料的充足,减少料品积压。③原则:按看板生产,减少看板数量。④优点:可以更好控制生产现场的管理并及时发现问题并解决问题。保证生产质量,降低了库存。
(6)持续改进流程
持续改进流程是进行精益生产的最有效方法之一,其主要是通过以下几点来实施完成的:
①不断发掘企业缺点并及时进行改善,以减少生产中的浪费,降低生产成本。
②通过对生产人员的培训,提高生产人员的自身素质。使其每一个人首先能做到发现自身的不足。③循序渐进的改进方式以使企业从实践中需找的自身的不足,防止盲目进行过多,不当的改善,以至于适得其反。④领导的支持与重视,企业通过领导激励员工,选择优秀的项目负责人。掌握持续改善的宏观掌控和决策。
3 结论
通过精益思想的现场改善方式,使生产企业在短时间内减少了在制品、库存成品的积压,使企业生产建立起一定的优化思想,并且在此次过中对于生产线的变化,以及产线中瓶颈工序的产量效率有了明显的提高,并且实现了以改变重点带动生产整体的效率和产量,使减少了人力资源成本。利用科学的理论程序分析,在生产企业中寻找生产过程的瓶颈工序,通过平衡生产线的方式,将生产节拍与生产制造流程工艺相结合,平衡生产线。以点出发,将精益生产的思想,融入到了生产现场改善上。通过此方法的实施,不仅能降低生产中所需要的成本,更重要的是为企业开辟了一条宝贵的经验之路。
参考文献:
[1] 谢丽萍.LM家具公司基于精益生产的现场改善活动研究[D].北京林业大学,2010.
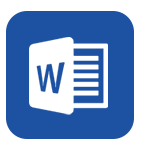