装配生产线平衡问题的研究
安大伟(通辽市工业经济技术服务管理中心,内蒙古 通辽 028000)
张继红(通辽职业学院,内蒙古 通辽 028000)
摘要:针对汽车装配生产线平衡,结合最新技术,介绍了相关的基本概念、研发特点、生产流程等问题,并对其应用进行了论证。
关键词:装配平衡流程
汽车装配是将已制造或采购到的合格零件、成品件、标准件按照图纸及技术要求装配在一起组成组合件、部件或成品,并达到规定的质量标准,经检验合格转入下一装配工序或下线报交,准备交付客户。装配线平衡就是为了设计出合理的工艺流程,均衡各工位间负荷,并不断完善和改进,减少生产环节中不增值的浪费;根据产品产量、品种的变化调整装配线的流程、生产节拍、工位位置等,是产品装配生产流程中乡党重要的一个管理环节。
一、工作要素
工作要素,有时也称为作业步骤,是产品装配过程中全部工作内容的一部分,是完成某项操作所进行的最小工作单元。通常在流水线平衡时,由工业工程师根据经验人为设定。理论上将工作要素分得申详细,填补了工位空闲时间,从而减少总的空闲时间。但如果划分得过细,随工作要素总量的增加,其相互间的组合方案呈几何级数增长,增加运算、调整时间;如果工作要素分得过粗,受前后装配关系限制,就可能只有很少的方案可供选择,因此需要工业工程师根据现场经验将关联性强的动作组合在一起作为一个工作要素。
二、操作工位
简称为工位,是在装配生产线上操作工人的工作场地。操作工在此工作场地上重复性地完成制定的一个或几个工作要素的操作。在汽车整车装配生产线上,通常按车身在装配流水线行进方向划分左、右工位,车身安装位置分车头、车尾和车中.为了减少相互间交叉干扰、避免安全事故的发生和操作时的相互影响,通常在一个工位上,只安排一名操作工。
三、流程图
流程图是描述各作业加工次序的图。通常产品的作业之间存在一定的技术上的约束关系,有些作业必须在其他某些作业完成之后才能进行,这种先后顺序关系称为作业先后关系,它反映了生产过程中作业完成的先后次序。生产线平衡过程效率就取决于优先次序的复杂程度。
四、生产能力
简称产能,是指一个工厂、一个车间,一条生产线、一个操作工位或某一台机器在一定的时间内的产品产出数量。产能的单位基本可分为四种,即:标准加工时间(小时、分、秒等)、数量(件数)、重量(千克、吨等)、长度(米等)。在汽车整车厂,以流经报交点的合格车辆数量作为装配生产线的产能单位。以单件生产时间作为每个工位的产能目标。在流水线生产规划时,先根据市场需求预测确定装配线的产能要求,并以此作为设备采购、改造、人员配备和物流规划的依据。一般按以下公式换算成单件生产时间要求的下限。
T=t*η/n(2-1):
T---单件生产工时
t---装配流水线开动时间
η---装配流水线开动率,在整车装配线上综合设备停机、零件问题和在线问题解决等影响,在总装生产线一般以90%开动率作为考核目标。
n---产量需求在生产稳定的情况下,流水线开动时间和开动率波动不会很大.在作产能分析时,一般根据装配流水线实际情况设定为常数,由此简化可知,流水线需求节拍时间与产量成反比关系。分析产能是为了能正确掌握生产线的生产能力.如果理论设定的产能比实际产能高,会导致生产节拍的混乱,订单不能及时完成,延误交货期,降低客户的满意度,从而降低产品的市场份额;反之,会导致开工率不足,设备闲置,应该能完成的订单被取消,失去市场机遇,同样也会失去市场份额。通过产能与负荷的平衡,在进行生产线平衡的时可以为该作业分配到并行操作工位,增加资源,降低作业时间,提高整体生产运作效率。从局部上看,生产线平衡以后,生产线的生产能力便确定下来,这时仍可以对已得到的生产能力进行调整.通过产能分析可以发现瓶颈环节,并可通过采取适当措施改善瓶颈环节,获得新的平衡方案,以满足生产的需要,同样提高生产运作效率。与此同时,产能分析还可以为MRPII/ERP中的能力需求计划提供依据。
四、单件生产工时
指在流水线上连续生产两件相同产品的时间间隔,即作业速度。单件生产时间是每个操作工位时间负荷的上限,生产线平衡必须在节
拍时间的约束下进行,最终分配到各操作工位负荷不能超过单件生产时间。有效生产就是要使各道工序的时间尽可能地接近节拍时间,否则就会在装配线上产生瓶颈工位,影响整个流水线的生产效率。单件生产工时是以最终客户的需求为基础,是动态的。如果顾客每天所需求的产品数量是400辆,单件生产工时就应设在68.4秒。单件生产工时设得过低,在满足客户需求后,继续生产,单纯的生产效率是提高了,那也只是在增加库存,会产生生产过剩的弊端,积压企业的周转资金;在最终客户的需求产品数量减少了的情况下,就应该在完成任务后停止生产,去做其它的工作或者是减少各道工序的作业人员来调整作业速度来符合生产要求。如果不通过人员配置调整的,而单纯降低生产线速度会造成人浮于事,破坏掉扎根于努力提高生产效率的企业文化。设定了单件生产工时后,再根据现有的条件来确定作业速度和工作量的分配。由于每个人在作业熟练度上存在着差异。这就要制订以技术熟练工为基准的作业标准书,对作业人员进行彻底的教育、训练,以期达到操作时间和操作结果与工艺过程设计的一致性。通过发现工序中的浪费、开展持续改进活动逐步降低单件工时也是很重要的。此外还应考虑在计划作业外的休息时间、早会、晚会时间,机器运转率不高造成的故障损失,调整作业程序的变换所造成的时间损失等对单件工时的影响。
参考文献:
[1] 吴竞昌.供电系统谐波(第一版)[M].北京:中国电力出版社,1998.
[2] 郑人杰,殷人昆,陶永雷.实用软件工程(第二版)[M].北京:清华大学出版社,2001.
[3] 张昆生,晓黄.APIfor Windows详解[M].北京:清华大学出版社,2001
作者简介:安大伟(1970—),男,汉族,内蒙古通辽市人,内蒙古通辽市工业经济技术服务管理中心书记,1990年毕业于浙江大学材料系,高级工程师,从事自动化控制专业研究。
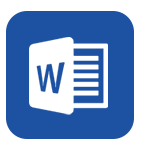