南京航空航天大学
机电学院
课 程 设 计
课程名称:机械制造技术及装备课程设计 设计课题:小连杆机械加工工艺规程设计
专业:机械工程
班级: 0513107
姓名: 朱闫
学号: 051310732
评分:
指导老师:(签字)
2016年 6 月 20日
绪论
机械制造业是一个古老而永远充满生命力的行业“机械制造工艺”和“机床夹具设计”课程设计是机械类专业学生的重要实践性环节之一。这次设计是我们在学习完了大学的全部基础和专业课程之后进行的。这是我们在走入社会走上工作岗位之前对所学的课程的一次深入的综合性的复习。是一次理论联系实际的训练,也是我们大学的全部所学的考察。
就个人而言,我希望通过这次课程设计对自己将来从事的工作进行一次适应性的训练。从中锻炼自己处理生产工艺问题的能力。掌握机械加工工艺规程设计和机床夹具设计的方法。从而进一步巩固有关的理论知识,提高独立工作的能力,为将来从事专业技术工作打好基础。当然无法期望通过一次课程设计就成为合格的工程师。但起码可以籍此领略机械工程专业的大概,为今后参加工作打好基础。由于能力有限。设计尚有许多不足之处,请各位评申老师给予指正。
目录
第1章零件工艺的分析
1.1零件的分析-----1 1.1.1零件作用的分析------------------------------1 1.1.2零件的工艺性分析----------------------------1 1.2工艺规程设计----2 第2章拟定零件加工的工艺路线
2.1定位基准的选择---2
2.1.1粗基准的选择--2 2.1.2精基准的选择--3 2.2制定工艺路线-----4 第3章机械加工余量及工序尺寸的确定
3.1确定毛胚的尺寸---4 3.2 铣端面---------6 3.3 钻ф7.94mm孔---6 3.4 钻倒角----------7
3.5钻φ3.15mm孔---7 3.6 钻φ3.7孔-------7 3.7 铣1mm槽-------8 3.8攻螺纹-----------8 3.9钻φ2.5mm孔-----9 3.10 工时定额-------9
第4章
夹具设计
4.1专用钻床夹具设计 ----------------------------18 4.1.1 定位方案 ---18 4.1.2 夹紧机构 ---18
结论----------------19 参考文献----------21
第1章零件工艺的分析
1.1零件的分析
图1 1.1.1零件作用的分析
题目所给的零件典型零件的一种—连杆。连杆在机械运动中起着传递动力和连接运动的重要作用。其在各类机械中都有着广泛的应用,如;车辆的转向连接处、起重机的推杆等等,而且他还可以承受一定的拉力,具有良好的平均载荷的能力。连杆的截面积很小,但是,却可以传递很大的力,且加
1
工简单,因此,在传递动力的场合大多选用连杆
1.1.2零件的工艺性分析
连杆结构总共有两类加工表面。现分述如下; 1.两连杆接头处的平面,即图中尺寸8和尺寸14两个厚度以及期间的距离1100.15.都是在加工两端面的过程中要考虑到的。其中尺寸线都出自小端的一边可以将该面作为端面加工的基准从而对与其相联系的相关尺寸进行控制及验收。
0.0162两个主要受力面即两个∮7.940的孔,两个孔是本零件的关键尺寸,和其位置尺寸39.35±0.1需首要保证的。以它们为基准加工其他部分才能保证本件的正确性。再就是三个润滑孔Ф
1、Φ2.5、Φ3.7和M3.5×3.5-H。由以上分析知道,对于这两组加工面而言,可以先半精加工其中两个Φ0.0167.940的面,找到该零件的精基准,然后借助于专用的夹具加工另一组表面,和打润滑孔,从而保证它们之间的位置精度要求。
3两个φ7.94mm 孔的孔面平行度应为 100:0.1; φ7.94mm 孔与外圆之间的同轴度为 0.006mm。
1.2工艺规程设计
确定毛坯的制造形式,零件材料为45钢,零件为连杆用来承受一定的拉压力并且受变换的载荷,再者考虑其生产纲领为大批量生产。而且它,的内外形状亦非太复杂,而且外型尺
1
寸不大。故选用金属型浇注成型,其大体形状铸出 。
第2章拟定零件加工的工艺路线
2.1定位基准的选择
2.1.1粗基准的选择
粗基准的选择主要影响不加工表面与加工表面的相互位置精度.以及加工表面的余量分配。选择粗基准时必须注意以下几个问题
① 如果必须首先保证工件上加工表面与不加工表面之间的位置精度要求应以不加工表面作为粗基准。如果工件上由很多不需加工的表面则应以其中与加工表面的位置精度要求较高的表面作为粗基准。
② 必须首先保证工件上的某种要表面的加工余量均匀则应选择该表面作为粗基准。
③ 选作粗基准的表面应尽量平整光洁不应有飞边、浇口、冒口等缺陷。
④ 粗基准一般只能使用一次。
按照粗基准的选择原则,为保证不加工表面的和加工表面的位置要求,应选择不加工表面为粗基准,故此处选择杆壁左侧(无凸出)为第一毛基准;在加工φ7.94mm 孔时,为保证孔壁均
2
匀,选择φ12mm 的外圆表面为第二毛基准。
2.1.2精基准的选择
精基准的选择应重保证零件的加工精度,特别是加工表面的相互位置精度来考虑,同时也要考虑到装夹方便,夹具结构方便。选择精基准应遵循下列原则;
①“基准重合”原则:即应尽可能选用设计基准作为精基准。这样可以避免由于基准不重合而引起的误差。
②“基准统一”原则:即应尽可能选择加工工件的多个表面时都能使用的一组定位基准作为精基准。这样就便于保证各加工表面的相互位置精度避免基准变换说产生的误差并能简化夹具的设计制造。
③“互为基准”原则:当两个表面相互位置精度以及他们自身的尺寸与形状精度都要求很高时。可以采取互为基准的原则,反复多次进行加工。
④“自为基准”原则:有些精加工或光整加工工序要求加工余量小而均匀,再加工时就应尽量选择加工表面本身作为精基准,而该表面与其他表面之间的位置精度则有先行工序保证。
综上所述,在φ7.94 mm 两孔加工以后,各工序则以该孔为定位精基准.这样就满足了基准重合的 原则和互为基准的原则.在加工某些表面时,可能会出现基准不重合,这时需要进行尺寸链的换算。
3
2.2制定工艺路线
由于大批大量的生产,故采用专用的夹具及尽量使工序集中来提高生产率,以降低成本。
工序1:下料 工序2:铸造 工序3:调制 工序4:磁性探伤
工序5:同时粗铣2-ф12mm的一端面 工序6:同时粗铣2-ф12mm的另一端面
工序7:精铣小头ф10mm的一端面至Ra20μm,大头ф10mm的一端面至Ra2.5μm 工序8:精铣小头ф10mm的一端面至Ra2.5μm,大头ф10mm的一端面至Ra20μm 工序9:钻、扩、铰ф7.94孔至ф7.94~7.956mm、Ra12.5μm 工序10:钻、扩、铰另一个ф7.94孔至ф7.94~7.956mm、Ra12.5μm 工序11:倒角至0.5mm、Ra10μm 工序12:钻ф3.15mm孔,扩孔至ф3.7mm 工序13:铣1mm槽 工序14:加工螺纹M3.5mm 工序15:钻ф2.5mm孔
4
工序16:清洗 工序17:检验、入库
机械加工工艺卡片见附录。
第3章机械加工余量及工序尺寸的确定 3.1确定毛胚的尺寸
此小连杆材料为 45钢。毛坯铸出后应进行调质,消除应力。查机械加工工艺手册确定铸件主要尺寸的公差,调整过后的零件毛胚图如下:
5
图2 零件的毛胚图
3.2 铣端面
端面由粗铣、精铣两次加工完成,采用三面刃圆盘铣刀(高速钢),铣刀的规格为φ80*12(齿数为10)。 由《机械加工工艺手册》查得精加工余量为0.5mm,粗加工余量为2.5mm。取粗铣的每齿进给量为0.2mm/z,取精铣的每转进给量为0.5mm/r,粗铣走刀一次αe=2.5mm,精铣走刀一次αe=0.5mm。取粗、精铣的主轴转速分别为235r/min和475r/min,又由前面选定的刀具直径φ80mm,故相应的切削速度分别为:
υ粗=πDn/1000=π*80*235/1000m/min=59.06 m/min υ精=πDn/1000=π*80*475/1000m/min=119.38 m/min 3.3 钻ф7.94mm孔
由钻扩铰加工完成,采用高速钢钻头,直径分别为φ7.5mm,φ7.94mm,尺寸8mm由钻模保证。钻孔:查文献(1)表5-21得进给量f=0.20mm/r,切削速度为20m/min。
转速n=1000v/πD=1000*20/π*7.5=848.83r/min 钻床为Z5025,九级主轴转速:250,300,420,620,740,850,1400,1800,2600。因此由机床选取实际转速为850r/min
6
实际切削速度为v=πDn/1000=π*7.5*850/1000=20.03m/min 扩孔:同上得f=0.20mm/r,n=850r/min v=πDn/1000=π*7.94*850/1000=21.20m/min 3.4 钻倒角
f,n与钻ф7.94mm孔相同
v=πDn/1000=π*8.5*850/1000=22.70m/min 3.5钻φ3.15mm孔
钻削加工,采用直径φ3.15mm高速钢钻头,尺寸8mm由钻模保证。查文献(1)表5-21,由工件材料为45钢,碳含量约为0.42%~0.50%,得进给量f=0.13mm/r,切削速度为20m/min。 转速n=1000v/πD=1000*20/π*3.17=2021r/min 由机床选取实际转速为1880r/min 实际切削速度为:
v=πDn/1000=π*3.15*1880/1000=18.60m/min 3.6 钻φ3.7孔
钻削加工,采用直径φ3.7mm高速钢钻头,尺寸8mm由钻模保证。查文献(1)表5-21,由工件材料为45钢,碳含量约为0.42%~0.50%,得进给量f=0.13mm/r,切削速度为20m/min。
7
转速n=1000v/πD=1000*20/π*3.7=1721r/min 由机床选取实际转速为1880r/min 实际切削速度为:
v=πDn/1000=π*3.7*1880/1000=21.85m/min 3.7 铣1mm槽
1mm的槽面可用盘铣刀加工,铣刀规格为φ80*10。取每齿进给量为0.1mm/z,αp=1mm,αe=1mm;取主轴转速为375r/min,则相应的切削速度为:
υ=πDn/1000=π*80*375/1000m/min=94.25m/min 3.8攻螺纹
采用φ3.5mm精度6h的高速钢机动丝锥加工,尺寸8mm由钻模保证。由文献(1)表5-37,切削速度v=5~10m/min 由表5-38:选用精度高的高速钢机动丝锥,另v=9m/min,底孔为φ3.15mm,背吃刀量a =3.5-3.15=0.35mm,进给量即螺距,f=0.35mm/r.主轴转速n=1000v/πD=1000*9/π*3.5=812r/min 由机床选取实际转速为850r/min 实际切削速度为:
v=πDn/1000=π*3.5*850/1000=9.35m/min
8
3.9钻φ2.5mm孔
钻削加工,采用直径φ2.5mm高速钢钻头,尺寸8mm由钻模保证。 查文献(1)表5-21,由工件材料为45钢,碳含量约为0.42%~0.50%,得进给量f=0.08mm/r,切削速度为20m/min。 转速n=1000v/πD=1000*20/π*2.5=2546r/min 由机床选取实际转速为2600r/min 实际切削速度为:
v=πDn/1000=π*2.5*2600/1000=20.42m/min
3.10 工时定额 3.10.1铣削
3.10.1.1粗铣端面
A.机动时间
由文献表5-43得铣削的计算公式为 T=(L+L1+L2)*i/fMz L1=【αe(D-αe)】0.5+(1~3),L2=2~5,L为铣削长度 fMz为工作台的水平进给量 fMz=nf,i铣削次数
D=80mm,αe =2.5mm,αp=10mm,n=235r/min,f=2mm/r,i=1; 取L1+L2=17mm
9
Tb =(10+17)*1/(2*235)=0.06min B.辅助时间由文献确定 开停车 0.015min 升降铣刀 0.015min 对刀 0.02min 主轴运转 0.02min 清除铁屑 0.04min 卡尺测量 0.10min 装卸工件 1min 所以辅助时间
Tα=(0.015+0.015+0.02+0.02+0.04+0.1+1)min=1.21min C.作业时间
TB= Tb+ Tα=(0.06+1.21)min=1.27min D.常量工作场地时间Ts取α=3%,则 Ts= TBα=1.27*3% min =0.038min E.休息与生理需要时间Tr取β=3%,则 Tr=TBβ=1.27*3% min =0.038min F.单件时间
Tp=2*( Tb+Tα+ Ts+ Tr)=2*(0.06+1.21+0.038+0.038)min=2.69min 3.10.1.2 精铣端面
D=80mm, αe =0.5mm,αp=10mm,n=475r/min,f=0.5mm/r,i=1;
10
取L1+L2=12mm 同理
Tb =(10+12)*1/(0.5*475)=0.09min Tα=1.21min TB=0.09+1.21=1.3min Ts=1.3*3%=0.039min Tr=1.3*3%=0.039min Tp=2*( Tb+Tα+ Ts+ Tr)=2*(0.09+1.21+0.039+0.039)min=2.76min 3.10.1.3 铣1mm槽
D=80mm, αe=1mm, αp=1mm,n=375r/min,f=1mm/r,i=5 由文献表5-44 L1+L2=11mm Tb=(10+11)*5/(1*375)=0.27min Tα=1.21min TB=0.27+1.21=1.48min Ts=1.48*3%=0.044min Tr=1.48*3%=0.044min Tp= Tb+Tα+ Ts+ Tr=0.27+1.21+0.044+0.044)min=1.57min
11
3.10.2 钻削
3.10.2.1钻ф7.94mm孔
钻孔: A.机动时间
由文献表5-43得钻削的计算公式为 T=(L+L1+L2)/fn L1=(1/2)Dcotk +(1~2),L2=0 D=7.5mm, k =15°,f=0.2mm/r,L=8mm; Tb =(8+(1/2)7.5cot15°+1)/(0.2*850)=0.14min B.辅助时间由文献确定 开停车 0.015min 升降钻杆 0.015min 主轴运转 0.02min 装工件 0.5min 所以辅助时间
Tα=(0.015+0.015+0.02+0.5)min=0.55min C.作业时间
TB= Tb+ Tα=(0.14+0.55)min=0.69min 扩孔: A.机动时间
12
由文献表5-43得扩孔的计算公式为 T=(L+L1+L2)/fn L1=(1/2)*(D-d)cotk +(1~2)
D=7.94mm, k =15°,f=0.2mm/r,L=8mm,a =(7.94-7.5)/2=0.005mm,查表得L2=3mm; Tb =(8+(1/2)*(7.94-7.5)cot15°+1)/(0.2*850)=0.07min B.辅助时间同上 C.作业时间
TB= Tb+ Tα=(0.07+0.55)min=0.62min 铰孔: A.机动时间
由文献表5-43得绞孔的计算公式为 T=(L+L1+L2)/fn f=0.2mm/r,L=8mm,a =(0.016)/2=0.008m,查表得L1=0.1mm,L2=11mm; Tb =(8+0.1+11)/(0.2*850)=0.11min B.辅助时间同上 C.作业时间
TB= Tb+ Tα=(0.11+0.55)min=0.66min 总的:
D.常量工作场地时间Ts取α=3% Ts= TBα=0.69*3% min
13
E.休息与生理需要时间Tr取β=3%,则 Tr=TBβ=0.69*3% min F.单件时间
Tp=(1+6%)*(0.69+0.62+0.66)min=2.24min
3.10.2.2 钻φ3.15mm底孔
A.机动时间
由文献表5-43得铣削的计算公式为 T=(L+L1+L2) /fn L1=(1/2)Dcotk +(1~2),L2=0 D=3.15mm, k =15°,f=0.13mm/r,L=14.2mm; Tb =(14.2+(1/2)3.15cot15°+1)/(0.13*1880)=0.09min B.辅助时间由文献确定 开停车 0.015min 升降钻杆 0.015min 主轴运转 0.02min 装工件 0.5min 所以辅助时间
Tα=(0.015+0.015+0.02+0.5)min=0.55min C.作业时间
TB= Tb+ Tα=(0.09+0.55)min=0.64min
14
D.常量工作场地时间Ts取α=3%,则 Ts= TBα=0.64*3% min E.休息与生理需要时间Tr取β=3%,则 Tr=TBβ=0.64*3% min F.单件时间
Tp=(1+6%)*(0.64)min=0.68min
3.10.2.3 钻φ3.7mm孔
A.机动时间
由文献表5-43得铣削的计算公式为 T=(L+L1+L2) /fn L1=(1/2)Dcotk +(1~2),L2=0 D=3.7mm, k =15°,f=0.13mm/r,L=4mm; Tb =(4+(1/2)3.7cot15°+1)/(0.13*1880)=0.04min B.辅助时间由文献确定 开停车 0.015min 升降钻杆 0.015min 主轴运转 0.02min 清理铁屑0.04min 卡尺测量0.10min 卸工件 0.5min
15
所以辅助时间
Tα=(0.015+0.015+0.02+0.04+0.10+0.5)min=0.69min C.作业时间
TB= Tb+ Tα=(0.04+0.69)min=0.73min D.常量工作场地时间Ts取α=3%,则 Ts= TBα=0.73*3% min E.休息与生理需要时间Tr取β=3%,则 Tr=TBβ=0.73*3% min F.单件时间
Tp=(1+6%)*(0.73)min=0.77min
3.10.2.4 攻螺纹
A.机动时间
由文献表5-43得铣削的计算公式为 T=(L+L1+L2) /fn+(L+L1+L2) /fn L1=(1~3)p,L2=(2~3)p L1=2p=0.7mm,L2=2p=0.7mm,f=0.35mm/r,n= n =850r/min,L=10.5mm; Tb =2*(10.5+0.7+0.7)/(0.35*850)=0.08min B.辅助时间由文献确定 开停车 0.015min 升降钻杆 0.015min
16
主轴运转 0.02min 清除铁屑 0.04min 卡尺测量 0.10min 装卸工件 1min 所以辅助时间
Tα=(0.015+0.015+0.02+0.04+0.10+1)min1.19min C.作业时间
TB= Tb+ Tα=(0.08+1.19)min=1.27min D.常量工作场地时间Ts取α=3%,则 Ts= TBα=1.27*3% min E.休息与生理需要时间Tr取β=3%,则 Tr=TBβ=1.27*3% min F.单件时间
Tp=(1+6%)*(1.27)min=1.28min
3.10.2.5 钻φ2.5mm孔
A.机动时间
由文献表5-43得铣削的计算公式为 T=(L+L1+L2) /fn L1=(1/2)Dcotk +(1~2),L2=0 D=2.5mm, k =15°,f=0.08mm/r,L=2.1mm;
17
Tb =(2.1+(1/2)2.5cot15°+1)/(0.08*2600)=0.04min B.辅助时间由文献确定 开停车 0.015min 升降钻杆 0.015min 主轴运转 0.02min 清除铁屑 0.04min 卡尺测量 0.10min 装卸工件 1min 所以辅助时间
Tα=(0.015+0.015+0.02+0.04+0.10+1)min1.19min C.作业时间
TB= Tb+ Tα=(0.04+1.19)min1.23min D.常量工作场地时间Ts取α=3%,则 Ts= TBα=1.23*3% min E.休息与生理需要时间Tr取β=3%,则 Tr=TBβ=1.23*3% min F.单件时间
Tp=(1+6%)*(1.23)min=1.30min 第4章
夹具设计
从前述的基准选择的分析及制定的工艺规程和工序卡。现选 择工序5工序9和工序10工序13来设计对应的专用夹具。
18
我的夹具是工序9的。
4.1专用钻床夹具设计
4.1.1 定位方案
由于工件被加工孔的轴线对两端面没有严格的垂直度要求, 为了简化夹具结构,采用大端台阶端面作为主要定位基准,在小端端面采用辅助支承,以此限制三个自由度;另选择工件外形两端圆弧在活动V形块和固定V形块之间定位。 活动V形块限制一个自由度,固定V形块限制两个自由度.实现工件正确定位.
对于两个加工孔φ7.94 而言,固定 V 形块,活动 V 形块定位基准都与工序基准重合,定 位误差Δdw(2-φ7.94 )=0 由上述分析可知,该定位方案合理,可行.
4.1.2 夹紧机构
针对大量生产的工艺特性,此夹具利用固定手柄压紧螺钉和活动V形块的一套夹紧机构把工件夹紧.本夹具结构简单,操作方便,适用于大量生产小型连杆类零件
结论
为期两个星期的课程设计结束了,在本次设计中,我查了大量的资料,在网上也搜索了很多相关的典型零件的工艺规程等内容,在我设计困难的时候,我得到了我的指导老师
19
和多位同学的指导和帮助,同学们也给了我很大的支持和启发,因此,我的设计与老师同学的帮助是分不开的,在这里,我对帮助过我顺利完成课程设计的老师和同学表示真挚的感谢。我的课题题目是,小连杆的工艺规程,这是我第一次全方位的对所学科目的运用,从中发现了很多以前没有注意到的问题,也学到了很多的处理生产问题的技巧和方法,我觉得本次课程设计对我而言非常重要。既是对我大学三年的学习总结,也是为以后在工厂工作打下基础。在本次设计中,在老师的指导下,我完成了本次设计,学习了新的知识,很感谢学校为我创造这个学习设计的机会。 本次设计中,我查阅了大量的书籍,在此:对所有机械书籍的作者表示感谢。没有他们的辛勤劳动,不可能完成我的课程设计。由于我的知识有限,而且设计中实际生产的知识,因此,有很多缺点和错误,希望答辩时专家和老师们能给我指出,对此表示感谢。
在本次课程设计中,我们将设计主要分为两大部分进行,工艺编制部分和夹具设计部分。 在工艺部分中我们涉及到要确定各工序的安装工位和该工序需要的工步加工该工序的机车及机床的进给量,切削深度,主轴转速,和切削速度,该工序的夹具,刀具及量具,还有走刀次数和走刀长度,最后计算该工序的基本时间,辅助时间和工作地服务时间。其中,工序机床的进给量,主轴转速和切削速度,
20
需要计算并查手册确定。 在夹具设计部分,首先需要对工件的定位基准进行确定,然后选择定位元件及工件的夹紧,在对工件夹紧的选择上,我用了两种不同的夹紧方法,即粗铣下平面用的是螺钉压板夹紧机构,粗铣前后端面时用的是气动夹紧机构,两种方法在生产中都有各自的优点和不足但都广泛运用在生产中。然后计算铣削力以及夹紧工件需要的夹紧力,这也是该设计中的重点和难点。通过这次课程设计,我对大学三年所学的知识有了一次全面的综合运用也学到了许多上课时没涉及到的知识。尤其在利用手册等方面,对今后毕业出去工作都有很大的帮助。另外,在这次设计当中,指导老师武星老师在大多数时间牺牲自己的宝贵休息时间,对我们进行细心的指导,我对他们表示衷心的感谢,老师,您辛苦了。 在这次课程设计中,我基本完成了课程设计的任务,达到了课程设计的目的,但是,我知道自己的设计还有许多不足甚至错误,希望老师们能够谅解谢谢.
参考文献
[1]陈蔚芳、梁睿君 主编 机械制造工艺学课程设计指导书 南京航空航天大学机电学院 2014年1月
[2] 叶文华 陈蔚芳 马万太 主编 机械制造工艺与装备 哈尔滨工业大学出版社 2011年2 月出版
21
[3]机械夹具设计手册 电子版
[4] 于大国 主编 机械制造技术基础与工艺学课程设计教程 国防工业出版社 2013年6月出版
[5] 任青剑 主编 精密机械制造工艺设计 北京理工大学出版社 2013年4月出版
[6] 刘品 张叶晗 主编 机械精度设计与检测基础 哈尔滨工业大学出版 2013年3月出版
[7] 徐龙祥 主编 机械设计 高等教育出版社 2008年1月 [8] 吴拓 主编 现代机床夹具设计 北京 化学工业出版社2011年9月出版
22
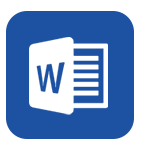