LDPE\\生产技术
高压低密度聚乙烯(LDPE)是用高压工艺生产的,压力为110~350MPa,温度为130~350℃,聚合时间非常短,一般为15秒到2分钟。乙烯聚合反应放出大量的热,热量主要通过循环过量的冷单体实现撤热,系统基本上在绝热条件下操作。1:1.15
LDPE高压反应主要采用两种聚合反应器:一种是带搅拌器的高压釜式反应器,该工艺最早是20世纪30年代由ICI公司开发的;另一种是管式反应器,最早是由巴斯夫公司开发的。后来,杜邦、陶氏化学、USI、住友和CdF化学(现在的埃尼化学)都对工艺作了若干改进。两种工艺生产的聚合物略有差别,主要因为反应器的温度分布不同。
釜式法和管式法两种工艺的生产流程大体相同,一个工业化的LDPE装置通常由以下几部分组成:乙烯压缩、引发剂制备和注入系统、聚合反应器、分离系统、挤出造粒。除聚合反应器外,釜式法和管式法的工艺步骤相似。现已建成的管式法最大单线反应器能力为32万吨/年,是巴塞尔公司建在法国的装置;釜式法最大单线反应器能力为18万吨/年,是QGPC公司用Orchem(CdF)技术建在卡塔尔的装置。
LDPE市场价格较HDPE高,一般专利费也较少,因此LDPE投资开发又开始活跃。LDPE开发主要集中于管式法工艺中,釜式法的开发进展较少。LDPE生产技术主要进展体现在以下几个方面。
(l)管式法技术及进展。管式法工艺的主要专利商有巴塞尔、DSM、等星和埃克森美孚等。
(a)巴塞尔管式法技术。巴塞尔管式法技术包括LupotechTM和LupotechTS两种。LupotechTM技术的特点是有多个单体进料点,反应器的这种构造适合于生产EVA;只有一个进料点的巴塞尔技术称为LupotechTS。
不同高压管式法设计的区别主要在于引发剂和反应器压力控制阀的差别。巴塞尔的Lupotech工艺以过氧化物作引发剂,Lupotech TM型工艺用压力控制阀控制乙烯的侧流,没有侧流的简单模式是LupotechTS型。为提高热传导,使用高气体流速;取决于所需要的聚合物牌号,反应器末端的压力控制阀或为脉冲式、或为非阀冲式。
LupotechTM型特别适合于生产重装袋牌号、共聚物和电线电缆牌号(即熔体指数小于1的产品),两种构型的单程转化率范围均为24~35,转化率的差别主要取决于所要生产的牌号。
Lupotech工艺可在较高转化率的情况下直接从反应器生产很宽范围的牌号。可以工业化生产VA含量高到30%的共聚物,也可以生产丙烯酸酯含量高到20%的共聚物。
(b)DSM公司高压管式法技术(CTR)。DSM公司清洁管式反应器(CTR)工艺的主要特点是:一级压缩机出口压力高达25MPa;聚合压力仅为200~250MPa,且无脉冲,保持恒压;反应热用于预热原料;反应管直径保持恒定,有4个过氧化物注入点;转化率大约为32%~40%;使用混合的过氧化物引发剂,这种引发剂与管式法常用的氧引发相比,可得到较高的单程转化率,反应管不易结焦,产品具有更好的光学性质,对分解的敏感性小。另一个优点是生成的低聚物较少,这样就可简化循环气的回收流程。CTR技术中反应器保持恒压以及热传导效率高的主要优点是:容易控制反应器的排料控制阀;无低循环疲劳现象,可降低投资和维护费用;产品质量稳定;薄膜拉伸性能好,可降低厚度;以及耗能低等。
该工艺产品的熔体指数(MFl)范围0.3~65g/10min,密度范围0.918~0.930g/cm3,适于生产VA含量为10%的EVA,最大单线设计可达40万吨/年。
(c)等星公司的高压管式法技术。等星高压工艺的改进主要集中在降低能耗、不结焦的管式反应器设计、先进的工艺控制、模拟搅拌器设计和催化剂进料装置的改进。利用等星管式法工艺可以生产VA含量高达28%的EVA,如果VA含量9%以下,生产EVA不需要增加设备。LDPE产品的密度范围0.917~0.932G/cm3,MFI 0.18~35。反应用有机过氧化物作引发剂,可以用空气,也可以不用空气。转化率高达30%,利用其不结焦技术,装置的能耗可减至最小。与其它工艺不同,反应器不要求溶剂洗涤。由于采用先进的控制仪表,最终产品的均匀性很好。
(d)埃克森美孚公司的高压管式法工艺。埃克森美孚开发了普通的LDPE管式法技术,燕山石化公司购买该公司技术建设的20万吨/年装置已于2001年投产。目前位于美国路易斯安那州巴吞鲁日的装置是使用该技术最大的装置,脱瓶颈后能力达到22万吨/年。埃克森美孚管式法技术的主要特点是:象巴塞尔技术一样,用排放阀作脉冲阀,但正常操作时不使用;使用有机过氧化物作引发剂;设有加热反应管的脱焦系统;采用实时监控熔体性质的技术,优质牌号比例高;反应器设计有很高灵活性,一个月内可生产全部牌号,一年可转变牌号600次,即使这样频繁切换,仍能保持较高的生产效率;单程转化率可达34%~36%;装置可靠性高,虽然额定运转8 000小时,但实际可运转8400小时。
该工艺产品的密度范围为0.918~0.935g/cm3,熔体指数范围是0.3~46。一套36万吨/年管式法装置可生产VA含量达15%的EVA,正在开发生产VA含量达28%的EVA技术,用较小的装置可生产VA含量达40%的EVA。埃克森美孚设计了36万吨/年的反应器,投资成本据说比22.5万吨/年反应器高25%~35%。
(2)釜式法技术及进展
釜式法工艺的反应是绝热过程,工艺中没有明显的热量从反应器移出。乙烯聚合是高度放热的,如果温度超过350℃,就会发生爆炸性的分解,因而要通过仔细地在反应器几个点注入新鲜的冷乙烯来控制反应。高压釜式反应器几乎全部用有机过氧化物作聚合反应的引发剂。阿克苏诺贝尔、Peroxid化学(Laporte)和埃尔夫阿托化学都可以提供很多类型的引发剂。
埃克森美孚公司已经在高压釜式反应器中使用茂金属催化剂,在巴吞鲁日的一个釜式法反应器中,几乎全部使用茂金属催化剂。现代釜式反应器的单程转化率为19.5%~21%,不同牌号有所不同。
釜式法工艺技术的主要专利持有者是埃尼化学、等星、埃克森美孚和ICI(SimonCarves)。
(a)埃尼化学的高压釜式法工艺。埃尼化学通过20世纪80年代末收购法国阿托化学(原CdF化学),成为欧洲最大的LDPE和LLDPE生产公司。埃尼化学对釜式法技术的主要改进体现为装置的大型化(理论上最大反应器可达3m3)和将产品范围扩大到LLDPE/VLDPE和EVA的能力。
埃尼化学认为用该工艺生产LLDPE时反应器可放大到5m3。与ICI/Simon~Carves技术的不同之处在于,埃尼化学技术的单线生产能力达20万吨/年,可明显降低投资费用,但操作灵活性略低。
该工艺采用齐格勒~纳塔催化剂可以转换生产LLDPE/VLDPE。继续开发釜式法工艺技术的目的在于降低能耗,提高单线产量,提高安全性和减少环境问题。然而PolimeriEuropa很可能将更多的投资用于Unipol工艺的实施,用于釜式法工艺开发的投资明显少于以前。
(b)埃克森美孚的高压釜式法工艺。尽管埃克森美孚主要致力于管式法工艺,但其釜式法技术还是有一些不同于ICI/SimonCarves和埃尼化学技术的特点。其主要特征为:反应器是埃克森美孚自行设计的1.5m3釜式反应器,并用它替代了用氧作引发剂的管式法反应器;反应器具有较高的长径比,有利于生产质量类似管式法工艺的薄膜产品;压力范围很宽,可生产低MFI的均聚物和高VA含量的共聚物。
(c)等星公司的高压釜式法工艺。埃克森美孚技术的前身就是等星的高压法技术。该技术最初由USI开发,然后转让给匡图姆化学,1997年8月千年石化(以前的匡图姆)和莱昂戴尔宣布成立有限合资公司即等星公司。
等星的技术开发集中在工艺控制、建立模型、高压釜搅拌器设计和催化剂进料设备。以达到适应挤出涂层市场要求的长链支化和分子量分布的平衡;而管式法产品则被优化适应吹塑和流延薄膜及成型应用的要求。反应的引发剂可以是空气,也可以是有机过氧化物,不包括添加剂,该工艺生产的LDPE/EVA的密度范围是0.912~0.951g/cm3,MFI是0.2~34。
(d)ICI/SimonCarves的高压釜式法工艺.ICI/SimonCarves技术是高压聚乙烯工艺的先驱,其独特之处是能较好地控制决定聚合物链性质的主要参数,即分子量、分子量分布和长链及短链支化度。这种技术适宜生产高度差别化的牌号,例如电线涂层和薄膜牌号要求较低的熔体弹性,要求长支链数较少;反之挤出涂层牌号要求较高的熔体弹性,需要有更多长支链的产品。管式LDPE工艺和LLDPE工艺不易生产这些产品。
釜式法工艺的操作压力和产品转化率均低于管式法,但投资成本和能耗很接近。用ICI工艺更容易生产那些LLDPE构成较少竞争威胁的产品。
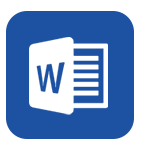