1 目的: 为更加规范生产现场发生异常时,能及时准确地反映并能通过相关人员确认、分析、及时解决,确保生产顺利进行特制订此规定。 2 范围:适用公司生产中心下辖所有生产线上发生的异常现象。 3 权责:
3.1 生产管理人员:负责提出异常,并确认异常是否属实,协助相关人员处理异常;
3.2 工程部:负责生产线上异常分析,找出异常原因,提出改善对策。 3.3 品质部:负责跟进改善结果及效果确认,对来料进行管控,并对此类异常制定纠正预防措施。
3.4 总经办:负责生产过程中重大异常的方案决策、处理稽核。 3.5 采购部:负责来料异常商务方面的异常处理。
3.6 计划部:负责异常发生时的总体计划的协调和异常发生产生的工时和物料的核实,组织相关部门一起分析、处理异常。
4 异常处理作业流程:
4.1生产部按生产排期表提前到仓库领料并安排做首件并量产。
4.2生产部在生产中发现产品、物料与样品不符,生产出的成品达不到标准要求或来料无法使用等现象时,及时上报生产领班、品质部等相关人员确认。
4.3生产领班、品质部确认异常可接受,通知生产线继续生产,如确认异常不能接收则由生产领班或IPQC在异常发生的10分钟内开出《制程异常报告》,所有的《制程异常报告》由车间的IPQC拿到相关部门签字确认,最后由品质文员将单据发出,
4.4经技术部分析,给出初步分析结果,结果分为工艺问题、设计问题、来料问题。
4.5由PE分析是来料问题、制程问题还是设计问题,并将分析的原因及解决方案记录在《制程异常报告》表上,并写给到工程部主管签名确认,如果需要返工或改变工艺则由工程部PE做出两块样品给到品质部确认,品质判定方案可行后,PE要在现场跟进生产部员工的作业方法、品质是否与样品一致。PE必须要等到生产员工做出2件合格品后方可离开现场,整个过程品质部要跟踪监控确认。
4.6如果确认是来料问题,《制程异常报告》采购部也要确认签字,并按照解决方案的意见与供应商沟通退货、换货、或由我司加工挑选扣除供应商相
1 应费用。并要求在一个工作日内对来料问题给予回复处理意见(临时解决办法),生产部要给予相应的配合和支持。同时品质检部应该协助采购部协商解决分析。
4.7如果由于异常原因造成的待工、返工工时,生产线应记录在当天的《生产日报表上》,计划部统一汇总。
5 出现异常时生产线处理规则及注意事项
5.1.1当生产线不良超过20%,品质部要立即开出《停线报告》要求生产停线,《停线报告》同时要给到计划部一份,以便于计划部调整计划。不良率超过10%则由生产或品质开出《制程异常单》,处理方法同4.1-4.7项。低于不良品率低于标准时,由生产、品质管理人员协商解决。
5.1.2生产现场异常发生时必须由PE或生产管理人员及时确认,并马上反馈给相关人员给予指示,如果生产管理人员将异常反馈给相关人员后在1小时内没给出指示,生产有权停线、待工。
5.1.3生产线异常发生时,PE须在2小时内给出短期解决措施,如需要更改工艺或做工装、夹具的须在4个小时内给出解决措施,如果出现重大异常,PE不能很完善的解决问题,由PE反馈给工程部经理,由工程部经理通知计划部,再由计划部组织相关部门开会商讨解决。
5.1.4 PE分析异常原因必须要正确,专业,给出的解决方案必须要具有可操作性,还要能通过相关部门签字同意方可有效。如果有一个部门不同意观点,PE需要重新分析。最终结果要达到相关部门都没有意见的效果。
5.1.5 PE给出解决方案前要自行或找生产协助PE先做两个样品确认方案是否可行,并将样品交给相关部门确认。相关部门同意后,生产部就按照样品作业,生产在作业时PE要现场跟进前两个产品的作业方法是否与样品一致,确认无误后方可离开现场。
5.1.6出现异常后如果需要更改工艺或返工,生产、品质有权要求PE作出指导文件,PE要在4个小时内做出简易的作业指导书或返工流程给相关部门确认,生产按照PE的指导文件作业,品质部现场跟进、监督生产作业。 5.1.7当出现异常时各个部门对解决方案有意见的时候,工程部要知会计划部,由计划部召集相关部门开会商讨,意见统一后由计划部分配各部门的工作任务,相关部门必须配合完成。执行过程中有任何问题要及时向计划部提出,由计划部协调处理。如果该异常各个部门无法达到统一意见,计划部有权将该异常交给某个部门或某个人主导负责,其它相关部门必须服从听取他的安排,配合执行各项任务。执行过程中有任何问题要及时向主导部门负责人汇报。主导部门负责人要及时给予解决。
2 5.1.8以上整个过程品质部要监督跟进,有任何问题要及时汇报。 5.2异常物料的处理
5.2.1经品质部或PE判断归属物料不良的由生产部在在一个工作日内开退料单到仓库进行退换料。
5.2.2由于设计或工艺造成的物料不良,按照《制程异常报告单》签核的物料损耗评估进行退换料。 5.制程异常报告要求
5.1报告内容:型号、单号、工序,时间、异常描述。
5.2异常描述要求:要描述详细的不良现象、总生产数量、不良数量、不良比率、不良确认人、有条件最后。
5.3原因分析及确认:PE提供的原因分析必须是准确、客观、详细的。 5.4改善措施:PE决策的解决方案必须要经过生产部、品质部、计划部的认同,相关部门负责人要签字确认,PE可提出临时的改善措施,以保证生产,若商讨结果需要生产部门协助挑选,计划部要在异常单上批注清楚,明确工时费用及物料损耗。 6.设备异常处理流程
6.1设备出现异常,整个过程由设备工程师主导跟进处理,如在能力范围内不能解决的汇报给工程部经理主导解决,所有处理过程参照设备异常处理流程图。其它事项参照异常处理规则及注意事项
7、附件
7.1《制程异常报告单》
8、流程图
发现异常10分钟内IPQC/生产领班开出异常单5分钟内PE分析异常原因,及异常解决方案30分钟内来料不良设计不良制程不良NG品质负责人确工程/研发负责人确认OK由品质主导并跟进异常处理过程认OKNG生产负责人确认OK由PE指导生产执行解决生产部按照异常解决方案处理异常,并记录返工、待工工时计划部汇总异常工时品质部跟时处理结果是否可行NGOK要求责任部门给予出长期纠正预防措施,并监督实施结果验证NG结案
OK4
设备出现异常10分钟内生产领班反馈给设备工程师5分钟内设备工程师到现场解决OK30分钟内30分钟内没解决生产领班开出设备异常单,并反馈到上级,计划部PIE主管解决2小时内2小时内没解决,由PIE主管反馈给工程部经理1小时内工程部经理1小时内没解决,组织相关人员开会商讨解决OK解决OK生产部统计异常计划部修改生工程部未完成的原工时,给相关人产计划因反馈到总经理确认,并汇总给计划部工程部负责给出处理方案及跟进处理结果结果验证NG结案OK
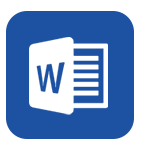