第五章
常见废旧塑料的回收与再生
第四章已着重介绍了废旧塑料的回收与再生技术,本章则在此基础上从几种常见的大品种塑料出发分别叙述其废弃物的回收再生方法,并有实例可供参考。 第一节
聚乙烯废弃物
聚乙烯是塑料中产量最大、用途极广的热塑性塑料,它是由乙烯聚合而成,是部分结晶材料,可用一般热塑性塑料的成型方法加工。聚乙烯可分为高密度聚乙烯、低密度聚乙烯和线型低密度聚乙烯三大类,其区别在于其密度、结构和制造方法的不同。高密度聚乙烯的密度一般高于0.94g/cm3,而低密度聚乙烯和线型低密度聚乙烯的密度在0.9l—0.94g/cm3之间。废旧聚乙烯薄膜主要来源有两方面:
①薄膜生产中产生的边角料、残次品等。这些废料清洁,品种明确,可粉碎压缩后直接送入挤出机造粒,回收过程较简单。
②来自化学工业、电气工业、食品与消费品工业等的废弃薄膜。这些废膜均已被污染、有的已着色并印有商标,有的还含有砂子、木屑或碎纸等杂质。
典型的回收工艺过程如下:
①喂料与粉碎。首先用金属检测器检出金属及粗重的杂质,然后送入粉碎机,进行切断、研磨。
②贮料。设置有3个储料仓,料仓中各有1台不对称旋转的进料螺杆。薄膜碎片进入料仓后,由螺杆强力混合、均化,然后由传送带分别或同时送入脱水装置。
③洗涤与分离。传送带上装有称量装置,定量输送薄膜碎片。进入洗涤槽,根据其污染程度确定洗涤时间;然后送入水分旋流器进行强力清洗,在离心力的作用下不同材料实现分离;再送入摩擦清洗机进行摩擦清洗,并分离出剩余的污物。
④干燥与贮存。清洗后的薄膜碎片通过离心机分离比水分,再经过热空气干燥,使含水量下降到0.5%以下。随后送入带混合螺杆的料仓储存。
⑤挤出。将清洁的薄膜碎片通过螺杆和空气压缩机出料仓送至挤出机中,经喂料螺杆预压缩,使碎料压实,防止形成“架桥”。
⑥真空排气,挤出机中设置有真空排气段,固体料块或热塑熔体中的挥发分,如空气、水蒸气、氧化物和残余单体,均由此排出。
⑦熔体过滤。挤出机前端装有过滤网,可使熔体中滞留的杂质清除掉。
⑧造粒。采用热切造粒或冷切造粒均可。
废旧聚乙烯薄膜的一般回收流程如图5—1所示。
首先打开废膜包,进行预切割,由传送带输送,用磁铁除去铁类金属,通过清洗槽除去砂石等重物,然后用湿式切碎机将薄膜切成碎片、并使细屑浆化,再送人清洗罐,加温水和消泡剂搅拌,摩擦清洗,脱去油脂,除去较重杂质,上浮的薄膜碎片流入离心脱水机,脱去大部分水,然后经切碎机进一步切碎并疏松碎片,进入热空气干燥器烘干,使水分含量低于l%,最后送入储料罐储存。干燥的薄膜碎片可直接出售。
若需加工成粒料,可将干燥的碎片与所需助剂和色母粒一
同由填塞式进料器连续送入挤出造粒机,切下的粒料在水中冷却,然后进入离心分离机脱去水分。冷却后送入混合罐,最后装袋销售。
由于农用薄膜的使用量相当大,所以下面着重谈谈废农膜的回收。
农用塑料薄膜主要包括塑料房、塑料棚和地膜,主要材料为聚氯乙烯和聚乙烯。农膜使用的环境恶劣,要经受日晒、雨淋、霜冻,所以使用寿命短,一般不越过3年。废旧农膜如处不当,会导致严重的环境污染,使土壤板结、酸化,废膜碎片还会影响农作物根系的生长。
废旧聚乙烯农膜回收工艺过程与一般废旧聚乙烯薄膜基本相同,国内由于废旧农膜收集上的困难,所以还没有专用的生产流水线。图5-2和图5-3分别是日本制钢所和日立造船(株)的废农膜再生流水线。
其特点:采用密闭圆筒形卧式洗涤器,筒内壁和中心搅拌轴上均装有叶片,使废料充分搅拌洗涤,全部物料使用管道输送;装有磁选装置,清除废农膜中的铁渣。
日立造船(株)的再生装置的特点为全系统无加热装置,破碎后的碎片经多次离心脱水,然后在粉碎机中粉碎,并利用粉碎时产生的摩擦热使剩余的水分蒸发。干燥后的粉料含水量为1%一5%。装有磁选装置。
废旧聚乙烯农膜回收再生料的性能一般都较差,适用于制造粗制件。
聚乙烯由于价廉易得、成型方便,所以其制品应用范围很
图5-3 日立造船株式会社废农膜再生装置
广,但用得最多的还是包装制品,估计在60%以上。低密度聚乙烯的最主要用途是包装用膜和农用膜;高密度聚乙烯则主要用于包装用膜和瓶类、中空容器上;线型低密度聚乙烯主要用于薄膜、模塑件、管材以及电线电缆上。
目前聚乙烯再生利用方法有直接利用、填充改性、交联改性等,但最常用的是直接利用。且巳大规模商业化操作。本节也着重介绍这种方法。
一、直接利用
直接利用是指将废旧塑料先鉴别分类除去异物,然后粉碎到所需的尺寸,再清洗以除去表面异物,干燥后的粉碎料就是再生料或再进行塑化造粒。用这种方法制成的再生料件能差别很大,主要取决于原料的老化程度和回收厂约设备与技术。如普通城市废弃物中的中空容器回收到的高密度聚乙烯再生料,其机械性能损失较小,而断裂伸长率和耐应力开裂性损失很大,远不如新料。
直接利用是现阶段最常用的方法,以下将介绍常见聚乙烯制品的回收再生方法。
1,聚乙烯薄膜
聚乙烯膜已大量应用于日常生活、工农业生产上,国外对聚乙烯薄膜的回收已很成熟,已形成了一套完善的投放、收集、加工体系。我国由于收集、分离上操作复杂,成本较高,所以回收利用率还较低。
[例1] 用再生聚乙烯生产农用地膜
(1)原料:老化程度较轻的废旧聚乙烯农膜或包装袋。
(2)再生工艺流程:见图5—4。
图5—4 聚乙烯废料的再生工艺流程 (3)工艺特点:
①采用低温、高速挤出工艺; ②挤出机选用大直径、小长径比;
②第一阶挤出机比第二阶挤出机的直径与长径比均小,具体见表5-1。
表5-1 挤出机的规格
④机头内腔截面加大1—2倍,使用多层细过滤网,以有效滤除杂质,减少更换滤网次数;
⑤添加抗氧剂;
⑥添加新树脂,以线型低密度聚乙烯为佳,添加量以25%一30%为宜。 (4)吹塑工艺:
①挤出温度从加料口至机头依次升高,210℃、220℃、210℃、220℃;
②改用圆柱形滤网,以增大过滤面积;
③采用大吹胀比,有利于提高薄膜的横向拉伸强度和纵向直角撕裂强度。当口模直径为100mm,吹胀比约为5.6时,薄膜的纵向和横向强度接近,吹膜易于控制;
④控制膜泡形状和冷却线高度,可使薄膜的纵向、横向强度趋于—致。膜泡形状以至高脚杯状(参见图5—5)为佳;冷却线高度以530mm左右为宜;
⑤主机转速以100r/min为宜:
[例2]用废农膜制育苗软盘
(1)原料:废[日聚乙烯农膜和低密度聚乙烯废膜: (2)工艺流程:见图5—6。
图5-6 用废农膜制育苗软盘的工艺流程
(3)生产工艺:
①洗料,先将大块膜料剪成lm2以下的小块,然后用大涡轮洗料机搅洗2次。
②挤条。用挤出机将洗后的湿料填入进料口,在适当有温度下挤出条料。
③切粒。用切粒机切成5mm以下的短粒。
④配料。严格按配方操作,配料时计量不得有误。
⑤混炼。用3台挤出机连续混炼、使料混炼均匀,塑化温度合理。 ⑥挤片。用挤出机挤片,片料挤出后入水冷却,经牵引机收卷成捆。
2.聚乙烯中空制品
聚乙烯中空制品在我们的日常生活中很常见,如各种牛奶瓶,盛放食品、洗涤剂、化妆品等的各种容器,大都是由高密度聚乙烯制成的,与薄膜不同,这些制品往往带有标签,标签一般是纸质的或是塑料膜。分离这两种异物有湿法和干法两种工艺。湿法工艺是用水(往往是热水)强烈搅拌,使标签上的粘结剂软化并与之分开、纸质标签会被机械搅拌成浆状,纸浆和塑料可用过滤装置分离。如果是塑料标签,则可用空气分选装置分离。干法工艺则是用热空气流向上吹粉碎料,这足以使较薄的标签材料从较厚的容器碎料中分离出来。
除标签外,废旧制品中可能还会带有泥土、油及其他异物,这些都可用水分离和清洗,根据污染物和污染程度,可用清洁剂和热水来加强效果。
典型的聚乙烯废旧中空容器的回收工艺流程如图5—7所示。
有些厂家在分选和粉碎时另附加一装置以除去某些异物,比如用振动斜坡来分离玻璃、金属和纸屑等异物。
粉碎的目的有两个:一是满足回收厂下序工艺的要求:二是适合挤出机的喂料。一般典型的粉碎尺寸是160一320mm2。要达到该尺寸要求,简单的可用粉碎机,也可与研磨机联合使用。
空气分选装置可以分离去或部分除去标签等异物,也可再次除去尚未除去的玻璃、金属等异物。
图5—8是消费后奶瓶的回收流程图。
二、填充改性
填充改性比较适用于对外观和力学性能要求不高的聚乙烯粗大制品。由于回收料的性能已有不同程度的下降,所以填料的添加量要适量。如有必要,还可用表面活性剂处理填料。下面是两个实例。
[例1]用聚乙烯再生粒料制造柑桔包装箱
(1)配方:参见表5-2。
表5—2 用聚乙烯再生粒料制柑桔包装箱的配方
(2)工艺流程:见图5-9。
(3)主要设备:
SBP300塑料薄膜破碎机
CH-200A塑料高速捏合机; 5HM—30密闭式炼塑机; SK—400开放式炼塑机; TL—200塑料切粒机; Φ80挤出机。 (4)生产工艺:
①废旧聚乙烯用人工洗涤。 ②自然干燥或烘干。
③凭手感和外观进行选择分类。
④将经选择的干净废旧聚乙烯薄膜直接投到SK-400开放式炼塑机的两个辊筒上,一次投料约20一30kg,控制的辊转速为14r/min,后辊速度为19r/min。切成厚度在5mm以下,宽约200mm的长条片。
⑤将双辊炼塑并经自然冷却的长条片直接喂入JL-200塑料切粒机即得粒料。
⑥每釜捏合时间为30一40min,每釜投料量一般为150一210kg。投料顺序如下: 木屑一石棉粉一滑石粉—硬脂酸钙一炭黑一聚乙烯再生粒料。 ⑦挤出塑化。挤出机的加料段、压缩段和均化段的温度分别为120—130℃、130一150℃和200一220℃。
⑧压制压力控制在15MPa(表压)左右,保压时间在3l一62s之间,模具不通冷却水。制品成型后,要自然冷却,目的是让制品均匀冷却以改善强度。
⑨经修整、组装后的包装箱即为成品。 (5)性能:包装箱的性能如表5—3所列 表5—3 再生聚乙烯柑桔包装箱的性能
[例2〕用聚乙烯再生料生产钙塑包装箱 (1)配方:见表5—4。
表5-4 聚乙烯再生料生产钙塑包装箱的配方
(2)生产工艺:将聚乙烯废料投入粉碎机,粉碎成8mm以下的颗粒,再把原料按配方要求准确称量,一起加入捏合机中混合均匀,然后送入挤出机中熔融塑化,挤出料坯;再将熔融状坯料放进油压机模具内加压定型即可制得制品。
挤出机的供料段、压缩段,计量段和机头的温度分别为120—130℃,180—190℃和150℃。
(3)设备:主要有粉碎机、捏合机、挤出机、油压机等。挤出机螺杆形式为等距不等深渐变型,蜗杆直径为Φ85mm,长径比为18,压缩比为3。
三、交联改性
聚乙烯再生料还可以进行交联改性,提高其拉伸强度和模量,以及耐热性、耐候性、耐磨性和尺寸稳定性等。交联的程度不同,其力学改性程度也不同,聚乙烯在充分交联后形成三维结构,从热塑性塑料变为热固性塑料,力学性能大大改善。对于回收聚乙烯来说,只需使之轻度交联,即可保持其热塑性能的同时又适当提高其力学性能,而且回收的聚乙烯制品再废弃后还可再生利用。
聚乙烯的交联改性有化学交联和辐射交联两种,聚乙烯再生料主要采用化学交联法。化学交联所用的交联剂为有机过氧化物(如过氧化二异丙苯)等。
其操作步骤为:用挤出机将过氧化二异丙苯与粉碎后的聚乙烯废料混合,在适当高温下进行交联,其温度控制在170一180℃,所得粒料为轻度交联改性的聚乙烯再生料,用它加工成的制品不仅力学性能有所提高,而且仍保持了热塑加工特性。所用挤出机的螺杆长径比以35为宜。
交联改性聚乙烯有两种加工成型方法: ①在聚乙烯软化点之上使之充分塑化,同时混入交联剂,在交联剂的分解温度之下进行造粒,在模压工艺中使交联反应与成型一步完成;
②在交联剂分解温度以下制成坯型,再加热到产生交联反应的温度之上完成固化,此法为两步法。
[例1]用交联聚烯烃泡沫边角料生产鞋底
交联聚烯烃泡沫是以乙烯—醋酸乙烯共聚物、聚乙烯为主,并加入改性剂、发泡剂、交联剂和活化剂等,在高温加压下交联发泡而成。主要用于制鞋业及工业上。用该塑料生产鞋底,会产生20%一30%左右的边角料,可回收再用。但这些边角料由于已交联成网状结构,给再利用带来因难。
通过下述处理办法,并添加部分添加剂及改性材料,可使交联聚乙烯泡沫边料再制成型,生产出泡沫片材、聚烯烃硬板和卷材,用于制鞋、建筑、包装方面。
(1)降低交联聚烯烃边料的交联度:采用机械剪切方法破坏其交联键,使交联度降低,提高再加工性。
①设备。Φ160mm×320mm开放式辊压机,速比为1:1.22,转速48r/min。 ②工艺参数 辊压温度70一80℃,时间10一15min,辊距0.5—0.7mm。
(2)边角料处理后的再成型:经剪切处理的边角料,通过高分子分散剂与其再交联,再发泡成型。
选择高分子分散剂须考虑到与边角料的相容性,即分子结构要相同,溶解度参数要近似等。
采用Φ450mm×1200mm开放式炼塑机,Φ450mm×1200mm二棍压延机,XSM-30密炼机和800t油压层压机,2000t水压层压机等设备。
(3)泡沫片的配方与性能:参见表于5-5。
表5-5 泡沫片配方与性能
(4)聚烯烃硬板配方与性能:见表5—6。
表5—6 聚烯烃硬板的配方与性能
在生产泡沫片材时,使用80%一90%的边角料也可制成片材,但在相同发泡剂情况下,随边角料含量增加,泡沫片的发泡倍数(膨胀率)降低,密度也随之增大,硬度增高。交联剂用量过高或过低都会影响制品质量,需严格控制。
[例2]废旧塑料与木屑共混 (1)配方:见表5—7。
表5-7 废旧塑料与木屑共混的配方
(2)生产工艺:将原料(除交联剂外)—次加入混合机中,于l60—180℃下混合均匀,或直接在开炼机上于165℃下塑炼加入邻苯二甲酸二壬酯,造粒。
成型采用冷料热压或热料冷压两种方法。 第二节
聚氯乙烯废弃物
聚氯乙烯是由氯乙烯单体聚合而成,是一种热塑性塑料。纯聚氯乙烯出于熔程短,分解温度与熔化温度差距不大,所以几乎不能加工,一般都需要加稳定剂以提高其分解温度。另外通常还需要加增塑剂。增塑剂的多少赋予了聚氯乙烯制品形式的多样化。
聚氯乙烯历史上曾经是使用量最大的塑料,现在某些领域上已被聚乙烯、PET所替代、但仍然在大量使用,其消耗量仅次于聚乙烯和聚丙烯。聚氯乙烯制品形式十分丰富,可分为硬聚氯乙烯、软聚氯乙烯、聚氯乙烯糊三大类。硬聚氯乙烯主要用于管材、门窗型材、片材等挤出产品,以及管接头、电气零件等注塑件和挤出吹型的瓶类产品,它们约占聚氯乙烯65%以上的消耗。软聚氯乙烯则主要用于压延片、汽车内饰件、手袋、薄膜、标签、电线电缆、医用制品等。聚氯乙烯糊约占聚氯乙烯制品的10%,主要产品有搪塑制品等。
聚氯乙烯的回收利用率一直都不高,这是因聚氯乙烯制品品种多,而不同品种的又不能混在一起回收,而且绝大多数制品是用在建筑上的,其使用寿命长,收集困难。
聚氯乙烯不适合焚烧和填埋处理,原因有:
①焚烧聚氯乙烯产生的废气中含有氯化氢和二恶英,前者是形成酸雨的主要物质之一;后考是致癌物质,人体或动物摄入后无法分解和排出。
②焚烧时产生的气体和烟尘中可能含有稳定剂带入的铅、铬等有毒重金属。 ③填埋时,有毒的稳定剂和其他助剂会随着污水而渗入地下水。
不同于聚烯烃塑料,聚氯乙烯在回收时,往往要根据其老化程度和回料的用途,加入适量的助剂,以改善再生料的性能。
聚氯乙烯塑料的回收方法主要是直接回收,此外,填充剂共混改性回收也有一些小规模的回收厂在应用。
一、直接回收
1.硬聚氯乙烯的回收
硬聚氯乙烯的回收再生主要集中在瓶类和压延或挤出片材,尽管在建材产品上的应用量很大,回收再用的潜力很大,但由于其使用寿命长,回收率还相当低,瓶类和片树的回收工艺相差不大,这里主要介绍瓶类的回收再生。
聚氯乙烯瓶大量应用于饮料、食品、农药等的包装上,尽管现在由于PET等材料的兴起,其使销量已有所减少,但绝对数量还是很可观。
聚氯乙烯瓶回收时最大的困难是分选,尤其是与PET,两者的密度相近,都是1.30—1.35g/cm3,无法用一般的密度法分选,而两者的加工温度相差很大,在PET的加工温度下,聚氯乙烯早已分解,而在聚氯乙烯的加工温度下。PET则尚未熔化。
聚氯乙烯被分离后,由于是热敏性材料,可能要加些稳定剂和润滑剂等助剂,并尽可能减少其受高温的时间。另外的回收过程与其他塑料一样,不需要特别的设备和工艺。典型的聚氯乙烯瓶再生工艺见图5—10。
首先打开瓶包,由传送带输送,人工拣出大块杂质、铝盖和铝环等,铁质金属由磁性滑轮分出,再由x射线自动分拣机拣出其他塑料瓶,将聚氯乙烯瓶送入轧碎机破碎成13mm以下的碎片,经空气分选机除去纸屑和灰尘等,在预洗机中除去油性残渣后进入洗涤槽,用含洗涤剂的热水清洗,然后在振动筛上脱水,再送入浮选罐,除去胶粘剂、标签等,碎片在离心干燥器中干燥,再经热空气滚动干燥,可与新聚氯乙烯料混合挤出造粒。
回收废旧聚氯乙烯瓶所需主要设备在表5—84中列出。 表5—8 回收废旧聚氯乙烯瓶所需主要设备
下面介绍的是硬聚氯乙烯回收的应用实例,此方法同样适合于回收聚氯乙烯建筑材料,如管材、门窗型材等。
[例]用废旧硬质聚氯乙烯生产农具 (1)配方:见表5—9。
(2)设备:在生产塑料农具时,小制品用Φ50mm挤出机及30一50t机械压机,较大制品用Φ90mm挤出机及100t左右机械压机。
(3)生产工艺: ①选择和清洗。回收的硬聚氯乙烯塑料主要是工业配件、硬板管、容器等,须捡出其他材质的塑料及杂质,特别是附加在这些废旧制品上的金属件,同时要进行清洗,除之上面附着的污物及粘着物。
②粉碎。较大的废塑料应先用铁锤敲成小块。利用粉碎机进行粉碎,应避免未除净的金属物进入粉碎机,以免损坏设备及飞出伤人。
③混合配料。在常温下进行机械搅拌。根据废旧塑料组成不同,添加一定量的稳定剂、增塑剂、填充剂。
制品中加入填充剂的目的是降低成本,此外对提高制品耐热性、刚性等也有一定的作用,但填充过量,会使制品强度下降,且需相应增加增塑剂用量。干燥的木粉也可作为硬聚氯乙烯塑料的填充剂。
④热挤出。混合好的物料,加入挤出机初步塑化成条状,目的是进一步混合均匀并除去水分,以利于下步成型加工。挤出温度在170一180℃左右,由于是初塑化,故挤出的条状物宁可生一些,而不可有“焦”的现象出现。
⑤粉碎和磁选。初步塑化后的条状料加入粉碎机再一次粉碎,料碎后的粒度不宜过大,然后再次磁选。
⑥塑化压制。经上述处理后的物料,经挤出机塑化后切下,放下压力机内进行压制,物料在模具内冷却成型。
挤出机出四段加热,温度在190一195℃左右。
模具需通入冷却水冷却,模温一般在40一45℃,制品出模后放入冷水槽冷却,或用风扇冷却、以免制品变形。压制品成型时间为1—2min。
2.软聚氯乙烯的回收
软聚氯乙烯的产品形式很多,且大多要分离后才能回收,所以比硬聚氯乙烯的回收要困难。回收得比较好的制品是农膜,尤其是在日本等聚氯乙烯农膜产量较大的国家。
废农用聚氯乙烯薄膜往往粘附大量的泥土、矽石,污染相当严重,在回收再生之前洗涤是一道重要的工序。其基本步骤是:将废膜包打开,破碎成碎片,放入热碱水浴液中浸泡一定时间,进行机械搅拌,使膜片相互摩擦和撞击。除去污物,清洗干净。清洁的碎膜片经干燥后即可挤出造粒。
其他软聚氯乙烯制品的回收情况较复杂。由于来源不同,处理方法也各不相同。下面举一实例加以说明。
[例]用聚氯乙烯微孔拖鞋边角料和废旧薄膜生产微孔泡沫鞋片。
(1)配方:配方中应加入各种助剂,其用量可用计算法或根据经验初步确定,再经试验加以修正。
表5—10为用聚氯乙烯微孔拖鞋边角料和废旧薄膜生产微孔泡沫鞋片(厚底)的配方。
(2)原辅材料:
①聚氯乙烯微孔拖鞋边角料。边角料有坡跟、薄底和厚底3类,各种原辅材料配比不同,颜色有深有浅。因此,必须进行分类选择。
②废旧聚氯乙烯薄膜。由于聚氯乙烯微孔拖鞋边角料或回收废旧薄膜一般附着泥土少沙和油污,必须进行清洗。洗涤干净的聚氯乙烯拖鞋边角料或聚氯乙烯废旧薄膜,干燥后进行破碎,颗粒度控制在4mm以下(主要指边角料),以增大颗粒的比表面积。颗粒相差太大,会影响各组分分散的均匀性,从而影响制品的质量。
③聚氯乙烯树脂。为使聚氯乙烯微孔拖(凉)鞋的微孔细致、外观美观、色泽鲜艳、富有弹比和穿着舒适,以及达到物理性能和加工工艺的要求,应使用—定数量的聚氯乙烯树脂。一般选用XS—3型,粘度为0.0918—0.0019Pa·s。
④增塑剂。聚氯乙烯微孔拖鞋宜选用邻苯二甲酸二辛酸和邻苯二甲酸二丁酯为主增塑剂,氯化石蜡为辅助增塑剂。通常增塑剂用量为60%一65%。
⑤稳定剂。可使用三盐基硫酸铅和二盐基亚磷酸铅。二盐基硫酸铅,还可作为偶氮二碳酰胺(AC)发泡剂的活化剂。三盐基亚磷酸铅对合氯增塑剂类有特效稳定力,故使用氯化石蜡为辅助增塑剂就必须采用它。
⑥发泡剂,选用AC发泡剂。再生过程中,必须考虑降低边角料原体系中所存AC发泡剂的分解速率和提高分解温度。一般选用硬脂酸钡为AC发泡剂的阻滞剂。
⑦润滑剂。在回收配方中,选择硬脂酸和石蜡作内外润滑剂。
硬脂酸另一作用是对填充剂碳酸钙表面进行活化处理、其工艺是预先将碳酸钙在ll0℃干燥后,在50℃上加入20%硬脂酸进行搅拌。
⑧填充剂。选用轻质碳酸钙作为填充剂。用硬脂酸进行活化处理,增加碳酸钙与聚氯乙烯树脂表面亲和力。
⑨着色剂。尽量不用易变色的着色剂。并掌握拼色技术。
(3)加工工艺:将已洗净、分类的边角料和废膜先切碎,再依照配方要求加入各种助剂,通过捏和工序,使各组分变为均匀的混合料。如能造粒则更理想。捏合后经塑炼进—步混合和预塑化,再按产品要求进行称量,组成色层胶片,然后加压塑化。热处理后定型、冲裁,最后装配成产品。
①捏和。捏和操作和加料顺序因原料不同而有所不同。
用聚氯乙烯微孔拖鞋边角料的捏和操作是先将边料粉与色浆、硬脂酸钡一起投入卧式捏和机冷拌5min,然后使用0.2一0.3MPa蒸汽加热,温度控制在80℃以下,搅拌10一15min,再投入AC发泡剂浆料,搅拌15min转入适当的冷却搅拌。在搅拌过程中需严格控制温度。
用聚氯乙烯废膜破碎料的捏和操作与用聚氯乙烯树脂料基本相同。将辅助料(包括稳定剂、AC发泡剂、润滑剂、色浆等)、氯化石蜡、一部分邻苯二甲酸二辛酯、一部分聚氯乙烯树脂或破碎膜,先打桨使其分散,经15min后,加邻苯二甲酸二丁酯和余下的邻苯二甲酸二辛酯以及聚氯乙烯树脂或破碎膜在Z型捏和机中,蒸汽压力控制在0.3MPa左右,捏和时间约40min。
在选用聚氯乙烯树脂巾加碳酸钙填充剂时,先将聚氯乙烯树脂相增塑剂混合,使树脂完全溶胀,然后再借助机械搅拌使聚氯乙烯树脂与碳酸钙充分混合。
②塑炼。采用二辊机塑炼,前辊温度控制比后辊高。操作过程调节至最小辊距,薄通2—3遍,使聚氯乙烯边料粉形通均细。在高弹态的温度下再经过三道粗炼与精炼可获得最佳混合状态的预塑均勺片坯。顶塑化好的片坯,还必须及时冷却以防堆放散热不良。
③加压塑化成型。用0.65一0.7MPa的蒸汽加热20一25min,在热的作用下,增塑剂渗入聚氯乙烯聚合物,膨胀、扩散,AC发泡剂分解产生的气体,形成许多大小均匀的微孔。在规定的模塑压力范围内产生均勺微细的气孔结构。在塑化完全后冷却15min左右至室温,以提高塑料流体的粘度,防止泡孔壁进一步减薄,稳定发泡体。
④热处理。将油压塑化冷却后的片坯,在80—l00℃温度范围内的蒸汽箱中及时进行热处理,获得均匀孔径的发泡体。
〔4〕性能测试:按SG77—73标准进行试验,其结果见表5—11。
二、填充改性
[例]用泥炭填充废旧聚氯乙烯生产防水卷材。 (1)原料与配方:
①采用废旧聚氯乙烯大棚膜、水稻育秧薄膜或其他软质废旧聚氯乙烯薄膜,经粉碎后使用。
②泥炭在自然条件下呈黑色或黑褐色,含有未完全分解的植物残体和分解物形成的黑色腐殖质等物质。使用前泥炭要过0.25mm筛。
③其他添加剂有增塑剂、稳定剂、软化剂、改性剂。软化剂采用一种不易挥发的石油馏分,兼起润滑作用。
④配方见表5—12。
表5-12 用泥炭填充生产防水卷材的配方
(2)工艺流程:见图5—11。
图5—11 用炭岩填充生产防水卷材的工艺流程 (3)设备:高速捏合机、炼塑机、三辊压延机。 (4)产品性能:见表5-13。
表5—13 用泥炭填充生产防水卷材的产品性能
[例2]用粉煤灰填充废旧聚氯乙烯生产防水卷材。 (1)配方:见表5-14。
表5—14 用粉煤灰填充生产防水卷材的配方
(2)生产工艺:
①聚氯乙烯废旧料先经两辊炼塑机压成碎片或丝状。
②将粉煤灰和聚氯乙烯树脂加入高速搅拌机,加入碱性填料和其他助剂进行混合,温度110℃左右,20min后加入聚氯乙烯废料,继续搅拌3mm。
③混合好的料进入密炼机加入抗老剂、补充剂等,3min左右出料。 ④经两辊炼塑机初步塑化,温度170-200℃,约5-7min出片。 ⑤送入三辊(或四辊)压延机,强制压料,塑化成片。 ⑥片材经冷却定型后卷取包装。 (3)产品性能及用途: ①经测试,产品经336h 110℃静态老化试验未出现严重老化。 ②拉伸强度可达6.8MPa;断裂伸长率达82.5%:
③该产品可作为交通、建筑和民用铺地、屋顶防水材料。
三、共混改性
[例1]聚氯乙烯废膜与丁腈橡胶共混生产鞋料。
用聚氯乙烯薄膜和丁腈橡胶进行机械共混,制成颗粒,生产的材料耐油性、耐酸性好,低温耐曲挠性和抗滑性好。有橡胶手感,粘合牢度和抗撕性能优良,可在绝大多数注塑机上加工。可用作运动鞋、劳保鞋的鞋底和其他制品。
(1)配力:见表5—15。
表5—15 PVC废膜与丁腈与橡胶共混生产鞋料的配方
(2)设备;250L捏合机,XK—40混炼机,Φ90造粒机。
(3)生产工艺:
①聚氯乙烯废膜捏合塑化。按配比将聚氯乙烯废膜在捏合机中捏合塑化,蒸汽压0.3一0.5MPa,时间l一1.7h。
②塑炼。速比1:1.5,辊温45±5℃,辊距0.5一1mm,丁腈橡胶塑炼在小辊距低温下进行,采取—段直接填料法共混,塑炼时间视丁腈橡胶中丙烯脂含量而定。将丁腈橡胶炼至包辊,调距3—4mm,填加聚氯乙烯捏合料进行共混,翻动均匀。再以1mm辊距薄通3次。
③挤出造粒。挤出机供料区的温区为80℃,压缩段为150—l60℃,计量段为140℃,机头为90一100℃。
〔例2〕废旧聚氯乙烯鞋底料共混改性制作泡沫鞋。 [1]原料与配方:见表5—16。
表5—16 废旧聚氯乙烯鞋底料共混改性制泡沫鞋的配方
(2)工艺流程:见图5—12。
图5—12 废旧聚氯乙烯鞋底料共混改性制泡沫鞋的工艺流程 (3)生产工艺:
①丁腈橡胶与氯化聚乙烯共混胶的生产。将丁腈橡胶于38℃低温辊上分三阶段塑炼、每阶段塑炼时间为25min,其间应停放l2h以上。后将丁腈橡胶与氯化聚乙烯按配比于150℃下的高温辊上混炼成均匀的共混胶片待用。
②碳酸钙的表面处理。将碳酸钙、硬脂酸加入混合机,混合3min后加增塑剂,再混合5min。
第三节
聚苯乙烯废弃物
聚苯乙烯是苯乙烯的均聚物,是一种热塑性近用塑料,产量仅次于聚乙烯、聚丙烯、聚氯乙烯。聚苯乙烯的应用范围很广,可大致分为以下四个方面。
通用聚苯乙烯:为无定型高透明度塑料、一般用注射或挤出成型,产品大量应用于日用制品以及家电、计算机、医疗等透明制品上。通用聚苯乙烯的最大缺点是脆性,冲击强度较低,约为11—27J/m2(缺口);
高抗冲聚苯乙烯:大大提高B 其冲击强度和断裂伸长率,产品广泛用于电气配件、家电外壳、食品容器等。
挤出发泡聚苯乙烯片材及其热成型制品:密度一般为48—160Kg/m3。厚的板材主要用作绝热、隔音、防振材料。热成型制品则大量用于食品包装以及快餐食品容器。
可发性聚苯乙烯泡沫制品:密度一般在l6—60kg/m3,产品用于电器的防震包装,建筑、冷冻等行业的绝热材料。
前二类聚苯乙烯制品使用寿命长,废弃后可用常规的回收方法回收,故对环境的压力也较小。而后二类聚笨乙烯制品则多属于一次性包装,体积大,消耗量大,如不处理而直接废弃,会对环境造成极大的压力。人们常说的“白色污染”中很大一部分内容即是泡沫聚苯乙烯。由于处理能力的限制,我国的很多大城市包括杭州和北京,已禁用聚苯乙烯泡沫快餐盒,而采用价格较贵,强度较差的纸质快餐盒。仅从废弃后对环境的影响程度来说,易于腐烂的纸制品无疑比聚苯乙烯泡沫要小得多,但考虑得再深一点,我们知道制造纸快餐盒的优质纸浆需要消耗大量的树木,而且造纸厂对环境的污染也远比塑料厂要大。
所以说回收聚苯乙烯泡沫塑料还有着极为重要的社会意义,本节也就主要介绍其回收与再生的力法。
泡沫聚苯乙烯回收与再生的方法概括起来有以下三种:物理回收法、裂解回收法以及用于制造涂料、油漆和胶粘剂等。
一、物理回改法
物理回收法即用物理的方法回收聚苯乙烯泡沫,常用、最经济的方法。
典型的回收过程见图5-13。原料通过输送带时用人工方法先去除明显的杂物,然后将原料粉碎并用带清洁剂的水清洗,进人一振动筛以去除清洗水,再用干净的漂洗水喷射漂洗,同时也去除了一些固体杂物和纸浆。漂洗后输送到离心干燥机以去除表面水分。这时原料中还有相当数量的水分必须除去。除去这些水分可以通过挤压、加热、真空排气挤出等几种方法来实现,比较常用的是真空排气挤出机和脱水机组,配以熔体过滤系统。
脱水过程是由挤出机来完成的,挤出机可以是单螺杆或双螺杆,单螺杆挤出机脱水时需要先进行预干燥,预干燥时可能会有些污染物带入。而双螺杆挤出机脱水无需预干燥,可直接在压缩段将水汽排出,所以其产品更干净。另外由于食物包装中的油脂有可能不能完全清洗掉,这样会使产品留有明显的气味,而用双螺杆挤出机脱水就可以消除异味。此外,如果需要还可以在造粒前加入另外的材料,如橡胶进行改性。
这时的物料还含有一定的水分,需再进入强力热空气干燥器,使含水量降到2%以下。 聚苯乙烯泡沫回收的关键工艺就是增密减容,也即消泡(或称脱泡):将其泡沫结构部分或全部破坏,去除其中的空气从而使容积减小。脱泡最常用的方法是用热(可由外部热源或由摩擦产生)软化并破坏泡孔结构,此外还有溶解法和凝胶法。
选择用何种方法脱泡,要根据加工量、聚苯乙烯泡沫的清洁程度等因素来定,一般来说,脱泡前原料必须是干净的,没有其他杂物,如原料受污染程度较大,如快餐食品盒,则必须先进行清洗和干燥。
(1)热收缩法;热收缩法(图5—14)使用如下几种典型设备。
①振动加热炉。振动加热炉主要由阶梯式空心振动板及加热装置组成。振动板由减速机带动,按一定的频率振动。板内充以100℃的热水,使板面均匀加热。加热装置采用电热丝加热,并可调压控温。
聚苯乙烯泡沫废料首先经粉碎机粉碎成10一15mm的颗粒,分散进入振动加热炉,穿过炉膛,受热收缩,在炉内大约滞留10s左右,出炉后由金属辊挤压,进一步压缩,静置冷却后粉碎造粒即为再生粒料。炉口温度控制为125℃,出口为110℃,振动频率为2.5Hz。
①红外加热炉。图5-l5是由日本5ekisui公司生产的红外加热回收炉,聚苯乙烯泡沫废料从输送带进入炉内,炉内装有特殊的陶瓷加热器,以产生红外线,聚苯乙烯泡沫料很容易吸收这种波长的红外线。因而迅速加热熔化,出炉后经风冷粉碎即可。
②熔融回收炉。熔融回收炉的结构如图5—l6所示。
聚笨乙烯泡沫废料从投料口投入,进入己加热至一定温度的小料筒,随着小螺杆的转动,一部分废料被软化和压缩,不断地被送往熔融炉中,炉壁外部有热空气加热,内部又有从中空螺杆与炉壁上设置的小孔送出的高温高压气体对废料进行直接加热,使之熔融,排出气体,废料进一步被压缩、变软、熔融,成为高密度物料,从喷嘴处挤出棒状再生料。然后可根据需要破碎,再加工成粒料。这种熔融回收炉可适用于多种废旧塑料的回收再生。
④双料筒小型回收设备。设备结构如图5-17所示。先将废聚苯乙烯泡沫块破碎成20mm见方的碎块,然后投入料斗,此料斗附近还设有一个小料斗,用于添加防熔融剂。防熔融剂一般为滑石粉、碳酸钙、粘土等无机物,或高级脂肪酸盐(如硬脂酸钙等),添加量为树脂量的0.5%一4%。防熔融剂由小料斗底部的螺杆输送进入大料斗,粘附于泡沫碎块的表面一同进入大料筒。大料筒的温度在200℃左右,泡沫碎块体积压缩后被送入小料筒。小料筒的温度只有100℃左右,温度不得过高,以防止树脂熔融。最后从小料筒中排出,粒子为0.2—2mn:见方,发泡倍数只有1—4倍,可作为低发泡挤出制品的原料。
(2)溶解法:溶解法设备投资大,工艺复杂,溶剂回收操作难度大,易对环境造成二次污染,故目前还不常用。
我国的溶解回收工艺如图5—18所示。将聚苯乙烯泡沫废料经净化处理后,在常温下溶于某种溶剂,得到一定浓度的聚苯乙烯溶液或溶胀体,然后蒸发出溶剂,回收聚苯乙烯。回收工艺条件见表5—17。
②英国的溶解回收工艺如图5-19所示。将废聚苯乙烯泡沫块投入料斗,同时加入少量溶剂,即苯乙烯单体,加热至145℃,使废料溶解脱泡流到下部,经冷却凝固后压出。添加的苯乙烯单体受热并在催化剂的作用下聚合,回收再生料块,再经粉碎造粒即成。
〔例〕废旧聚苯乙烯泡沫塑料再制聚苯乙烯树脂。
本例采用电视机厂废弃的聚苯乙烯泡沫包装材料,聚苯乙烯泡沫塑料厂的边角废料、悬浮法聚合生产聚苯乙烯树脂厂粒径不合格的产品等为原料。其工艺流程见图5—20。
①消泡与除杂。用溶剂对废旧聚苯乙烯泡沫塑料进行消泡处理(液固比例为3:1)。泡沫中包容的气体逸出后,体积大大缩小;搅拌、加热,调成聚苯乙烯溶液;静置5天,将其中的泥土,粉尘和机械杂质沉降分离出来,由于废旧聚苯乙烯泡沫塑料可能沾有油污等物质,所以需在消泡前用60℃碱性皂水进行洗涤,然后用清水洗净。再配制成溶液,以保证最终产品外观为无色透明物。
②造粒。造粒过程见图5-2l。当介质温度升至62℃时。将储于聚苯乙烯溶液计量罐中的预先配制的聚苯乙烯溶液计量后放入造粒罐中,搅拌,20min内升温至85℃,接着在30min内升温至85℃〔注意添加软水,保持介质体积〕,并存90℃下保温4b(此时介质中悬浮的液滴由于溶剂被蒸发而形成球形的聚苯乙烯颗粒),然后使其降温至50℃可出料,再降至室温,过滤,洗涤后即得到半透明的球形聚苯乙烯珠体。从造粒罐蒸发出的溶剂进入全凝器,回收的溶剂放入溶剂储罐,然同送回消泡工序循环使用。
在造粒过程中,以水为分散介质,聚氯乙烯—1799和聚氯乙烯-1788作为分散稳定剂,并加入氯化钠等辅助剂,以调整介质的密度、粘度和表面张力,使聚苯乙烯溶液在介质中呈球形颗粒悬浮、分散。
加料温度需选择在由溶剂与水所形成共沸混合物的沸点以下,以52—65℃为宜。
加料量由造粒罐的容积来定,容积为1m3的造粒罐每次的加料量以125一150kg为宜。 按要求,产品的粒径应为3.35一0.69mm。影响产品粒径除加料温度相加料量外,还有搅拌器的形式、转速以及介质的组成等因素。我们采用螺旋桨式搅拌器,在转速不变的条件下调配介质溶液的组成,可使聚苯乙烯溶液始终呈珠体稳定地悬浮在介质中。
另外,应严格控制其回收条件:一是造粒罐内需呈微负压,水蒸气和溶剂蒸气能克服管道阻力进入全凝器,以尽量减少泄漏,二是全凝器的热交换需充分,使水蒸气和溶剂蒸气全部得到冷却。通常,溶剂回收率可达到85%一90%。
③后处理。造粒所得聚苯乙烯珠体,尚含部分溶剂需除去。用水将其洗涤后,再用3.35mm和0.69mm筛进行筛分(筛余物可重新溶解、造粒)。
筛分所得聚苯乙烯珠体,含有水分,需经干燥。为防止聚苯乙烯珠体在干燥过程中发生粘连,每100kg聚苯乙烯珠体中加入1.5kg细粉状磷酸三钙(作分散介质),将其置于转筒烘干机中,控制转速150r/min,于1h内升温至115℃并维持7h,放出后冷却到30℃,用10%盐酸溶液除去其中的磷酸三钙,再用冷水淋洗,于50℃下烘干,得无色透明珠体,即聚苯乙烯树脂成品,
(3)凝胶化脱泡法;以可发性凝胶液或高沸点混合溶剂使废弃聚苯乙烯泡沫塑料凝胶化脱泡,再挤出造粒。
①回收步骤。将废弃的聚苯乙烯泡沫在80一100℃下加压,软化泡壁,受压后体积缩小8—10倍,随后投入装有可发性凝胶的容器之中,收缩为凝胶料团,此时含湿量为30%一50%。再将料团捏合或挤压排出残余气泡,经剪切造粒得到表面光滑且内部结构密实的粒料,粒径为0.25—2mm。
②可发性凝胶液。可发性凝胶液由发泡剂石油醚和溶剂组成。溶剂有醋酸酯类、卤代烷烃类、芳香类、丙酮及乙醚等。溶剂含量为5%一70%(体积比)。其典型配方:石油醚(沸程30一60℃,相对密度0.69)50,乙醚〔相对密度0.71〕50。
[例]聚苯乙烯废泡沫再生可发性聚苯乙烯。
将聚苯乙烯泡沫废料加入高沸点凝胶化混合溶剂中,即可迅速脱泡成为凝胶料;将其通过排气式挤出机,在回收混合溶剂的同时,热塑造粒得到聚苯乙烯粒料,粉碎后筛分。筛分按常规方法进行,以水作分散介质,在热压釜中再加入分散剂、匀泡剂、液体发泡剂等助剂,搅拌升温至130—140℃,使粒料软化变成小球状,并渗入发泡剂。然后降温出料,淋洗,沥干,得再生可发性聚苯乙烯珠状粒料。此种粒料可按常规方法须发泡及成型加工。
用于聚苯乙烯泡沫废料凝胶化的混合剂由聚苯乙烯的良溶剂和非溶剂组成,混合溶剂的沸点高于100℃。其适宜的良溶剂有:芳烃(如甲苯、二甲苯、二乙苯等),卤代芳烃(如氯苯、邻二氯苯等),酯类(如醋酸丁酯、醋酸戊酯以及焦油溶剂等),适宜的非溶剂包括烷烃类(如C8以下的石油馏分,各种溶剂汽油、煤油、柴油等)及醇类(如异丙醇、正丁醇、戊醇等)。凝胶化混合溶剂中良溶剂的体积数以30%一60%为佳。凝胶热塑造粒回收溶剂的操作温度为150一300℃,压力为101—1000Pa。再生可发性聚苯乙烯用的液体发泡剂为C3—C8的烷烃或沸点<60℃的卤代烷烃,用量为3%一15%。此外,根据不同的要求可加入其他助剂,如着色剂、阻燃剂等,用量一般<35%。
根据回收废料质量的不同,本例制得的可发性聚苯乙烯可用于不同要求的泡沫塑料产品,如作夹芯板,浮标,救生器材,保温、隔热材料或包装材料等,密度大的还可作冷库的地面材料。
二、化学裂解法
化学裂解法得到的苯乙烯单体经聚合后可得到与塑料一致的原料,但设备装置、工艺路线复杂,能耗大,效率低。目前的经济效益较差。废旧聚苯乙烯泡沫用化学裂解回收苯乙烯单体有4种方法。
1.溶剂裂解法
首先将聚笨乙烯溶解于烷基荼溶剂中制成聚苯乙烯含量大约为20%的溶液,然后将此溶液用泵送到管式分解炉中,在400一500℃分解10一20min。将冷凝后的流出物送到蒸馏塔内蒸馏可以得到纯度为95.52%的苯乙烯,产率为65%一70%。将此产品经精馏塔分离后可以得到更高纯度的苯乙烯。蒸馏残液可作为溶解聚苯乙烯的溶剂重复使用。
2.催化裂解法
将95%一99%的聚苯乙烯和1%一5%的硅铝微球催化剂投入反应釜中,在常压、350一450℃条件下裂解。反应物经冷凝器液化成粗苯乙烯,经100℃左右的预热室,把粗产品打人压力为5333Pa的分馏塔,分馏后得到高纯度的苯乙烯产品。
3.铅室裂解法
在反应釜中先装上10—15kg的铅,再投入30一40kg的废旧聚苯乙烯,密封后升温加热。裂解产物经过冷凝器液化成粗产品,粗产品经精馏后即得产品苯乙烯。加入铅的目的一方面是为了提高釜的导热效率;另一方面能使聚苯乙烯降解后的残渣不致于坚固地附着于裂解反应釜釜底和釜壁,而是悬浮在熔融铅液中;第三.反应釜内有熔铅存在可避免温度过高而引起聚苯乙烯进一步分解。
4.情性气体裂解法
以氯气为载体,在带孔板的管式反应器内聚苯乙烯的裂解速度上升,同时单体苯乙烯的产率增加,氮气的最佳流速为0.8—1.1m3/s,温度升高裂解速率也增加,苯乙烯单体的收率可达98%。
〔例〕用废旧聚苯乙烯塑料回收苯乙烯。
(1)原料:废快餐饭盒,废聚苯乙烯泡沫包装材料等。 (2)设备:裂解炉,冷凝器,真空泵,储罐,蒸馏塔等; (3)回收步骤:
①原料顶处理,废料中杂质较多,需经粉碎后风选,除去泥沙、米粒等杂质,得到小颗粒状原料。
②消泡。原料除杂后仍是泡沫状,内含大量气体,用液体消泡剂消泡,排出气体,使体积大幅度减小。一般控制固液比1:1,使物料呈糊状。
(3热裂解反应。反应在裂解炉内进行,每炉装料约200一300kg,装料后密封、升温。低于145℃时,从炉内导出消泡剂气体,经冷凝器冷凝回收再用,正常裂解反应温度在350一500℃、压力在一0.01MPa下进行,导出裂解气经冷凝器进入储罐,大约5—6h即可完成裂解,然后,清除残渣(残渣量为装料量的1%以下),再进行下一次裂解。
①蒸馏。裂解产品是黄棕色液体,主要成分为苯乙烯、乙苯、甲苯和多聚苯乙烯。采用蒸馏方法分离出苯乙烯,为防止热敏性的苯乙烯再聚合,除加入阻聚剂外,还要用减压蒸馏方法,降低蒸馏温度,控制塔顶真空度为0.06MPa,截取初馏分,得到混合苯溶剂,主要成分是甲苯、乙苯、二甲苯等。蒸馏采用恒回流比操作,当塔顶冷凝液中不饱和键物质的含量为80%时分馏,最终得到含量不小于90%的苯乙烯产品。塔釜残液为棕黑色油状物,主要成分为二聚体、三聚体、四聚体及多聚体,应及时由塔釜内放出,可重新裂解或用于制造防水涂料。
裂解炉内残渣为黑色粉末,主要是积炭和泥沙,不含其他有机物,可混入燃煤中烧掉。蒸馏釜底残液回裂解炉重新裂解、不外排。工艺过程中不产生废料,对环境无二次污染。但本工艺冷凝水用量较大,因此拟采用部分冷却后循环使用。
三、综合利用
1.油漆和涂料
废旧聚苯乙烯泡沫塑料经改性后可制得多种油漆和涂料。
(1)溶剂型涂料生产工艺(同济大学化学系):废聚苯乙烯泡沫经清洗去污、干燥后投入带搅拌器的反应釜中,加入适当配比的酚醛树脂、甲基纤维素、松香和混合溶剂(氯仿、香蕉水、二甲苯),浸泡之后,高速搅拌3h以上,使之溶解并改性成均匀的胶状溶液,用玻璃棒蘸液提起,呈线状下滴即可。用0.18mm铜筛网过滤胶状液,得到合格的改性塑料胶,然后加入色浆,高速搅拌lh得到粗色漆、经球磨后用0.15一0.125mm铜筛网过滤,即得到合格的漆。色浆是用颜料加溶剂经研磨和0.15一0.125mm铜筛网过滤后制成,色浆用量为2—4份(改性塑料胶为10份)。
(2)瓦楞纸箱用防潮涂料:
①原料主要有废聚苯乙烯泡沫,此外过有增塑剂、溶剂、水、表面活性剂、增粘剂、消泡剂。其中溶剂以二甲苯为主溶剂,配以适量的醋酸乙酯或丙酮;增粘剂选用聚醋酸乙烯乳液;乳化剂采用烷基酚聚氧乙烯醚。
②生产方法。将净化后的废弃聚苯乙烯泡沫塑料粉碎为一定粒径的碎料,然后加入盛有溶剂的反应釜,充分搅拌溶解制成油相液。在另一反应釜中将增粘剂和乳化剂加入水中制成水相液。利用分散设备将油相液同水相液混合制成水乳涂料。
(3)防水涂料:配方见表5-15。
表5-18 防水涂料的配方
工艺流程见图5—22。
本涂料粘度较低,适合手工刷涂和机械喷涂,可用于纸箱的防水防潮,提高纸箱的强度和改善表面粗糙度,并降低其生产成本。
(4)用废聚苯乙烯泡沫制成建筑防水涂料:原料为废聚苯乙烯泡沫、二甲苯、松香、煤焦油。
工艺流程见图5—23。
该涂料的耐温性为一35—85℃,粘结强度大于0.2Mpa,在10%的硫酸、盐酸或氢氧化钠溶液中浸泡4天无变化。涂后2h表干,100h实干,防水性很好。
(5)耐酸碱防腐蚀涂料:配方见表5—19。
表5-19 耐酸碱防腐蚀涂料的配方
工艺流程见图5—24。
该涂料在常温下刷涂,15min后基本干透,优于普通油漆和涂料;在水中浸泡10天以上不起泡,不脱落;在浓酸或浓碱液中浸泡10h,不起泡,不脱落;经过1年多的实用表明,耐老化性良好。
(6)可剥性涂料:配方见表5-20。
表5—20 可剥性涂料的配方
生产方法:聚苯乙烯泡沫与溶剂混溶后,再加增塑剂、稳定剂,搅拌均匀后,即成可剥性涂料,可用于防锈防腐。
(7)快干漆:
原料:废聚苯乙烯泡沫、乙酸乙酯、乙醇、二丁酯、环氧树脂、丁腈胶、填料、着色剂。
生产力法:把废聚苯乙烯和一些配料在反应釜中搅拌,使聚苯乙烯泡沫溶解,经研磨过滤,加入填料和着色剂,在一定温度下继续搅拌,过滤得到高分子快干膝。
(8)上光漆:配方见表5-21。
生产方法:上述原料经搅拌、溶合、共聚、过滤后,即得上光清漆。
(9)几种涂料配方:见表5-22。
表5-22 几种涂料的配方
2.胶粘剂
(1)改性胶;配方见表5—23。
生产方法:将净化处理后的聚苯乙烯废料与苯乙烯—丁二烯-苯乙烯嵌段共聚物及松香置于混合溶剂中,25℃下搅拌混合溶解6h即制得改性胶粘剂。
胶粘剂的性能见表5—24。
表5-24 改性胶粘剂的性能
(2)不干胶:配方见表5—25。
表5—25 不干胶的配方
生产方法:将聚苯乙烯泡沫完全溶化在溶剂中,再加入邻苯二甲酸二丁酯和乙酸乙酯,搅拌均匀即可。该胶适用于将纸类物品(如商标、标签等)粘贴于玻璃、金属、木材、塑料等物体表面。
(3)白乳胶替代胶:利用废PS制的白乳胶替代胶可改善其成膜性能和粘度。加入适量增塑剂和聚乙烯醇,可提高胶粘剂的韧性。
配方见表5-26。
表5-26
白乳胶替代胶的配方
生产方法:在耐有机溶剂的容器中。用炼油厂的重芳烃作溶剂,将废聚苯乙烯溶解,制成固含量为30%一40%的粘胶液;在另一容器中,用水作溶剂,将聚乙烯醇(1788)加热溶解,制成12%一13%的水溶液,然后将其冷却至50℃以下,加入增塑剂、防老剂、表面活性剂和填料,搅拌均匀;将上述生产的聚苯乙烯粘胶液缓慢地加入到聚乙烯醇水溶液中,并不停地搅拌,使其乳化。在活性剂的作用下,溶液愈搅愈白,约40min后,观察其乳化状况,若无油滴状物存在,或取样静置12h无离析和分层现象,则均认为乳化合格。
使用性能:该胶为乳液型胶,干燥较快,白干成膜,坚固、耐冻、耐老化、耐酸碱和潮湿,是较经济实月的粘结剂,经无纺布、木制家具粘结试用的结果表明,它完全可以替代目前市场上销售的白乳胶,并且成本比白乳胶低,也适用于重芳烃不溶解的塑料、陶瓷等制品的装修粘结。
(4)无毒粘合剂:配方见表5—27。
生产方法:制取粘合剂时,先将废聚苯乙烯泡沫塑料粉碎(若太脏,还需洗净、晾干)置烧杯内。在常混下,边搅拌边慢慢加入已计量后的各种溶剂混合液,待聚苯乙烯溶完后。再加邻苯二甲酸二丁酯及酚醛树脂或萜烯树脂,充分搅匀,放置一段时间后即成,产品需加盖密封保存,
用途:这种粘合剂可用于聚苯乙烯塑料、瓷砖、木材和日用器皿等的粘结,还可用于图书馆小塑料封皮书上贴标签纸等。
(5)其他胶粘剂:
①建筑胶:先将皮聚苯乙烯泡沫溶于二甲苯(或乙酸乙酯)中,加入改性剂(如酚醛树指)、活性剂(如氧化锌)及填充剂(如滑石粉),充分搅拌均匀,得金黄色粘胶刘。可代替415建筑胶,用于木材、地板块以及马赛克的粘结。
②密封胶:以废聚苯乙烯泡沫、甲苯、邻苯二甲峻二丁酯等为主料,加上其他辅料,经过加热、溶解、搅拌,可制得密封胶。
②通用胶:先将废聚苯乙烯泡沫溶于乙酸乙酯中,再加入松香(或酚醛树脂)改性,加入适量的交联剂和防老剂以及填料,搅拌均匀后即得通用胶。该胶可在24h内完全固化,粘结力>3×105N/m2,并在45℃下,保持2年有效。
第四节
聚对苯二甲酸乙二醇配废弃物
聚对苯二甲酸乙二醇酯(PET)是对苯二甲酸或二甲基对苯二甲酸与乙二醇酯的缩聚物,是一种线型热塑性塑料。PET通常是一种结晶型塑料、但在瓶、薄膜产品中,为了其高透朗度,可用特殊的工艺条件使之成为无定型塑料。
PET由于性能优良,成本低,用途非常广泛。根据其制品形式,可分为四类:聚酯纤维、薄膜、工程注塑件、瓶类。前三类,特别是聚酯纤维,使用量很大,使用寿命长,目前的回收利用率不高,不是本节研究的重点。PET瓶由于质轻不碎、能耗低等优势,替代了一些传统的包装材料,大量应用在食品、饮料、化妆品等领域,特别是饮料瓶,PET已占绝对优势。饮料瓶都是一次性使用,所以废弃量极大。
PET瓶的回收技术在国外已达到相当高的水平,美国、德国等国家的回收率现已达80%以上。不仅如此,为方便回收,这些国家还专门制订了一些地方性法规,对PET瓶的废弃、收集、使用、设计制造作强制性的规定。如日本在1997年颁布了一套PET瓶设计的“管理指导准则”。“准则”规定不允许使用染色的PET瓶,除非所盛产品有避光保存要求,可将瓶制成绿色或蓝色,禁止聚氯乙烯标签,不允许在瓶面上直接印刷,禁用底座或独立把手,禁用铝制瓶盖,标签必须用物理手段能去掉等等。
目前PE丁瓶的回收方法主要有机械回收、共混改性和化学回收等几种。
一、机械回收
机械回收是目前最普遍的方法,一般过程是:粉碎、分选、清洗、干燥、造粒。也有工厂是先用手工将PET瓶体与盖、标签、底托等分离,然后再粉碎。
PET瓶回收时,首先要注意以下几个问题:
①废旧PET瓶中一般都带有瓶盖、标签,有的还带有高密度聚乙烯的底托。瓶盖材料有铝、聚两烯和乙烯—醋酸乙烯共聚物,标签一般是塑料或纸。这些材料的不同会影响回收时工艺路线的选择,也会影响PtT回收料的质量。
②PET在加工温度时极易发生水解,水解会导致PET变色和降解。所以PET回收时,除要严格控制含水量外,还要控制催化水解物的产生:如在清洗过程中避免使用苏打或其他碱性清洁剂,因为碱性物质会催化PET的水解。
③要控制其他水解催化物的含量:如瓶盖中的铝、乙烯-醋酸乙烯共聚物,标签中的
-聚氯乙烯,PET中只要有1x106的聚氯乙烯即可使其变色和降解。
④很多废旧PET瓶中都带有胶粘剂,如底托和纸质标签都需用胶粘剂。胶粘剂存在于回收料中,会使PET呈雾状,降低透明度,同时PET在加工时易变色、降解,严重影响其质量。
FET瓶机械回收的方法很多,比较成熟且已工厂化操作的有以下几种。 1.水浮选器或水力旋流器分离回收技术
这种技术的原理是根据PET瓶上各种组分的密度和物理性能不同,利用气流分选器、水浮选器或水力旋流器、静电分离器等分离出标签、胶、高密度聚乙烯、铝等物,最后得到纯PET。工艺流程如图5—25:
在人工分选时,将其他颜色的PET瓶,或者PVC瓶、高密度聚乙烯瓶挑出。因为杂色的PET,特别是PVC会严重影响回收料的质量。
粉碎成较小的碎粒后,标签就从PET中脱开,这时用气流分选器就很容易将标签和疏松的脏物分离出去。
清洗时,要使用热的无泡清洁剂,避免使用苏打等碱性清洁剂,因为碱性物质的存在,会催化PFT的水解而导致其相对分子质量的降低以及固有粘度的降低。当然也有例外,如果回收料是用于PET纺丝的,对固有粘度的要求不是很高,则可以使用苏打作清洁剂,以减少胶粘剂的残留量。
清洗后的混合料还要用清水漂洗,并通过一过滤网过滤,这样残留的清洁剂、固体杂物、少量的标签及胶粘剂都在这一过程除去。
利用密度的不同,水浮选器或水力旋流器就可将高密度聚乙烯从较重的PET和铝中分离出去。如果瓶盖的密封用乙烯—醋酸乙烯共聚物,则乙烯—醋酸乙烯共聚物也随高密度聚乙烯一起被分离。
PET、铝混合物经脱水干燥后送入一静电分离器(见图5—26)将铝片分离出去,得到纯PET。用这种方法可得到纯度很高的PET,同时还可得到中等纯度的高密度聚乙烯(含有乙烯—醋酸乙烯共聚物,聚丙烯等)。
图5—26 静电分离器
这种工艺因为不能使用苏打等碱性清洁剂,除去胶粘剂就比较困难,所以有些工厂就增加了一道低温粉碎工序。由于胶粘剂低温呈脆性,易粉碎成粉末料,而FET仍然是碎片,这样用筛网就很容易将胶粘别除去。用这种方法可以得到胶粘剂含量极少的PET回收料。
2.水浴或水力旋流器分离技术
该工艺是由荷兰DSM公司开发的,与水浮选器或水力旋流器分离回收技术基本相同,不同的是它的前期处理工艺。
该工艺适用的废旧PET是无盖或塑料盖,不能带有铝盖。粉碎前,先将瓶子的各组成部分分开,方法是将颜色一样的废旧瓶连续通过一个温度为70一100℃的热水浴,经过l—1.5min后,因为PET是经双向拉伸吹塑制成的,受热后即收缩,而高密度聚乙烯底托、标签、瓶盖并不收缩。这样PET瓶体就可以与其他组分脱开。各组分脱离后就进入一振动筛,就可清除已剥离的标签,剩下的PET瓶体和高密度聚乙烯底托经过另一个振动筛分离。分离后的PET瓶体和高密度聚乙烯底托分别进行破碎、清洗、漂洗。PET碎片通过一水力旋流器将较轻的残留聚乙烯和胶粘剂去除,经脱水、干燥、金属探测器处理后即可得到纯度较高的PET回收料。
3.溶液/清洗工艺回收
这种回收工艺是由美国Pure Tech公司开发的,最早是用在塑料瓶的油墨去除工艺。后改为PET瓶的回收工艺。该工艺与连续水浴/水力旋流器分离工艺相似,但只能批量生产,不能连续生产。废旧PET瓶最好不要带铝盖,如有铝盖,则在回收生产线的末端必须安装金属探测器或静电分离器。工艺过程如下:先将经手工分选后的PET瓶压碎,然后在工业清洗机中用非碱性溶液清洗,漂洗约30min。清洗过程中标签和底托与瓶体间连接变松,用机械方法去掉底托,再用过滤装置去除标签,同时胶粘剂也与瓶体分离,随过滤液一起去除。
这种工艺回收的PET和高密度聚乙烯料纯度较高,但均含有少量的胶粘剂。
4.溶剂/浮选工艺回收
该工艺是由美国Dow化学公司开发的,能得到纯度很高的PET回收料。
该工艺与水浮选器/水力旋流器分离工艺基本相同,不同的是该工艺采用氯化烷烃作溶剂,能较彻底地去除其他组分,尤其是胶粘剂。工艺流程如图5—27:
图5—27 溶剂/浮选工艺回收流程
二、共混改性回收
对PET废料进行共混改性时,共混组分的选择十分重要,主要有改性树脂和增容剂,此外,还有起结晶中心作用的成核剂,降低玻璃化温度的结晶促进剂以及改善制品物理性能的防老剂等。
在共混组分中改性树脂的重要作用就是大大提高PET回收料的加工性能以及制品性能,通过共混,回收料可以直接用于注射成型。作为PET废料的改性组分通常选用聚对苯二甲酸丁二醇酯〔PBT〕和聚乙烯、聚丙烯。鉴于后二者与PET的相容性不好,有必要添加增容剂,以提高不同种树脂的相容性,消除共混后的分层现象。
用PBT、聚丙烯作为改性树脂所制得共混料的性能见表5-28。
表5-28 PBT、聚丙烯作改性树脂制得的共混料的性能
[例1]PET/HDPE/SEBS 1.25L以上的PET饮料瓶过去常用瓶体(PET)和底托(高密度聚乙烯)组成,为简化回收工艺,降低回收成本,最佳的共混方案是将PET与高密度聚乙烯共混。这一回收工艺的流程见图5—28。
由于PET与高密度聚乙烯的高度不相容性,PET/高密度聚乙烯共混料表现出极差的机械性能,因此加入热塑性弹性体作为增容剂来改善共混料的性能。实验表明,在PET:高密度聚乙烯=3.5:1(这与饮料瓶的PET/高密度聚乙烯的质量比相当)的共混料中加入13%的SEBS,其缺口冲击强度可高达5.7J/mm2,这种高抗冲材料可用来生产各种仪表外壳、汽车零部件,还可用来取代部分工程塑料,用途十分广泛。
[例2]PET/PC。将PET废料与10%一60%的聚碳酸酯共混而制得热塑性共混料,这种共混料具有优异的耐热性、韧性和耐化学品性,其拉伸强度可达40MPa,工艺流程见图5—29。
三、化学回收
大家知道PET有两种合成方法,即对苯二甲酸与乙二醇酯的缩聚反应和酯交换反应,反应是可逆的,因此,在一定条件下,水和醇过量就会发生逆反应。利用这—特点就可以将废旧PET解聚成单体或齐聚物,再将单体或齐聚物合成PET树脂,真正实现原料循环利用。
PET在进行化学回收时,对废旧PET原料有—定的质量要求,一般都是用机械回收得到的PET碎片,因为其中的杂质会对解聚反应产生如下不利的影响:
①金属杂质合成为PET料降解和变色的催化剂; ②聚烯烃会使PET料变脆,降低其使用性能;
③聚氯乙烯的分解产物氯化氢会引起PET水解,使PET变脆、脱色; ④乙烯—醋酸乙烯共聚物、胶粘剂等会使PET变色。 化学回收对PET原料的质量要求见表5—29。
表5-29 PET瓶化学回收时对原料的质量要求
现阶段PET化学回收的几种主要工艺如下。
1.水解/甲醇醇解工艺
将机械法回收的PET碎片加热到150一250℃,在过量水中用醋酸钠作催化剂,在4h内PET就可以水解成对苯二甲酸和乙二醇酯。水解的催化剂还可以用酸(如硫酸)或碱(如氨水)。酸性催化剂在60一95℃时在10-30min内加快水解反应速度。
另外,还可以用甲醇醇解,得到对苯二甲酸甲酯和乙二醇,配方为PET/甲醇=1;4,反应式为:
在典型的甲醇醇解反应中,将熔融的PET和甲醇混合,在催化剂的作用下,于2—7MPa下,将混合物加热到160一240℃,lh后得到的解聚产物99%为单体。这种单体聚合得到的PET料可用于食品包装。
2.二醇醇解回收工艺
如果PET不是在过量水或甲醇作用下而是在过量二醇作用下,就会发生酯交换反应。在催化剂作用下,用二醇如丙二醇加热PET,将长链PET变成短链。典型的催化剂有胺、烃氧化物或全属醋酸盐。在聚酯分子链上,通过链断裂过程和二醇交换,自由的丙二醇代替了乙二醇,最后PET被裂解为以烃基为端基的短链组分。在二醇醇解过程中,用丙二醇作为自由的二醇,最终产物主要是双羟乙基对苯二甲酸酯和双羟丙基对苯二甲酸酯、乙二醇、丙二醇。对苯二甲酸甲酯和一些自由的乙二醇和丙二醇。反应式如下:
典型的二醇醇解反应温度为200℃,时间为8h,丙二醇/PET的比例为1.5:1,反应过程中连续注入氮气,以防止得到的多元醇裂解。
另外也可以采用乙二醇醇解PET。乙二醇/PET的比例为1:3,反应的催化剂为醋酸锰,温度为205-220℃,时间为3.5h,反应过程中通氮气以防止热氧化。
3.水解的反应挤出技术
以上介绍的二种工艺都是在反应釜中进行的,不能连续生产。而反应挤出是在双螺杆挤出机上通过连续混合一步完成,可以连续生产,而且克服了反应过程中反应产物性能易变化等难题。
PET水解反应所需设备为一台直径为25mm,长径比为28:l的同向旋转双螺杆挤出机。挤出机分为加料段、熔融段、反应挤出段、排气段和计量段。螺杆上有输送、捏合和混合盘等元件,其中输送元件和捏合元件共同完成PET的熔融;捏合盘、混合盘及输送元件共同完成PET的水解反应,在注水点前,采用反向元件提高PET熔融后的压力,在加料段的末端形成一密封环,防止反应物的泄漏。熔融段的长度约为螺杆直径的10倍,反应段紧靠排风口反向元件处或者置于挤出机末端机头节流阀处。用一冷凝器收集由于膨胀而排出的热挥发性物质和过量的水蒸气。反应产物通过一3mm双层线材挤出机头挤出。
4.醇解和水解的设备和工艺
设备都较复杂,各公司处理的方法也不尽相同,以下是几种较有代表性的工艺。
(1)Du Pont工艺:Du Pont公司的PET解聚工艺是醇解与酯解的结合,首先使PET碎片在醋酸锌催化剂的作用下与二甘醇和甲醇反应60min,然后在磷酸螯合剂的作用下反应20min,反应压力为2.7—3.4MPa。
(2)Goodyear法:Goodyear公司利用甲醇将回收的PET瓶解聚为对苯二甲酸乙二醇酯和乙二醇,将其聚合后,再用以生产各种新的PET瓶。这种技术使塑料瓶“闭环”回收利用的愿望得以实现。
(3)Freeman法:Freeeman化学公司利用酯基转移作用的原理,把长链的PET在加热的情况下与二甘醇溶液混合,二甘醇破坏PET链使其分解为乙二醇和对苯二甲酸,这些单体又生成液态芳香族聚酯多元醇,这种多元醇通常用作硬质聚异氰脲酸酯泡沫的材料,制成屋顶材料和墙壁隔热层,还可用于热固性树脂。
(4)West Footscray法:奥地利West Footscray公司开发的工艺过程为:先把废弃瓶切成碎片,然后用一种分离器分离出纸和聚烯烃,再将碎片送至194℃的乙二醇溶浸50min,使PET脆化,分离得到的FET小碎粒进一步压碎,在200℃下水解,从水解液中回收对苯二甲酸,通过精馏得到乙二醇。用这两种单体合成的PET,符合美国与食品接触的联邦法规要求。
(5)酸解法:日本东北大学开发出分离回收废PET容器为附加价值高的化学原料的再资源化技术。这种技术首先是将废PET容器粉碎为0.1mm左右粉末,然后溶于50%一60%的硝酸中分解,溶液温度为100℃以上,反应时间约15一16h。反应后可分解为对苯二甲酸和乙二醇。对苯二甲酸不溶于硝酸而浮在溶液上面,在高温下过滤回收。然后将溶液降至室温,溶液中的乙二醇用硝酸氧化为乙二酸结晶。其结果,对苯二甲酸回收率100%,乙二酸回收率35%。
[例1]用PET废料生产不饱和聚酯树脂 原料与配方:见表5—30。
生产工艺:采用通用的不饱和聚酯生产装置,按配方将干净的PET废料、乙二醇和催化剂一起加热,至接近乙二醇沸点,回流使PET废料醇解。醇解结束后加入丙二醇并使温度降至140℃,加入邻苯二甲酸酐,使之完全熔化,当温度降至100℃时加入顺丁烯二酸酐,升温至160℃时回流半小时,随后再升温至190一210℃脱水酯化,直至酸值合格。反应在二氧化碳或氮气保护气氛中进行,反应结束后,降温至150℃时加稳定剂,至80℃时加苯乙烯,最后得到浅黄色钻稠状液体不饱和聚酯。
常用催化剂为锌盐、锰盐、钴盐和铁盐,最佳用量为PET总重的0.4%一0.5%。 交联剂可用苯乙烯、甲基丙烯酸甲酯、乙烯基甲苯、邻苯二甲酸二烯丙酯及丙烯腈等。用量为醇酸树脂量的30%一40%。
所得不饱和聚酯的性能如表5—31所列。
[例2]PET废料化学再生成聚酯切片。 1)原料及配方;列于表5-32。
表5-32 PET废料再生成聚酯切片的配方
(2)工艺条件:以生产纤维级聚酯切片为例,各阶段工艺参数列于表5—33。
(3)设备:按年产300t聚酯切片生产能力,其主要设备为: 醇解釜:1000L,不锈钢,带搅拌器。 聚合釜:700L,不锈钢,带搅拌器。 真空泵:W—3型及H—150型。 冷凝器:传热面积10m2。 切粒机:200kg/h。
锅炉:0.5t/h。若用电加热,此设备可省。 再生工艺流程见图5—30。 (4)反应过程:在醇解釜内分别加入废料、乙二醇(质量比为1:0.9),在加热(约200℃)、搅拌(200r/min)条件下,吏废料分子裂解,经过一定的时间加入催化剂(乙酸锌)和稳定剂(亚磷酸三苯酯、三氧化二锑),继续加热(280℃)进行酯化反应。待酯化结束后冷却(约122℃),把釜内物料进行过滤并进入聚合釜内,这时釜内升温至275—280℃,在强力搅拌下(330r/min),并用真空泵保持一定的真空度。真空度随着反应进行逐步提高,用粘度法确定反应进行的程度,并根据再生料的用途,确定反应终止的特性粘度(如纤维级为0.64cm3/g、注塑级为0.85cm3/g)。这时釜内物料的粘度较高,出料时必须借助于充入氮气加压,料流经多孔板呈线状,经冷水槽冷却,由切粒机切粒成聚酯切片。
(5)操作注意事项:
①备料。废料应洗净、晾干,块大的料应适当粉碎,以减轻下道工序中的过滤负担,降低醇解时间及减少副反应。
②醇解。升温要慢,并要维持200℃左右(因乙二醇的沸点0.1MPa下为197.6℃),这时乙二醇处于沸腾状态,有利于醇解。若温度过低,醇解速度太慢;相反,乙二醇大量气化,不但加重了回流塔负担,而且易产生副反应,使乙二醇消耗增多。
③酯交换。加入催化剂和稳定剂后,升高温度至280℃,温度过低或过高均对酯化不利。 ④过滤。滤网要完好无损,在过滤时滤液要冷却至l20℃左右,防止因过滤时间长而造成过早聚合。滤液先精滤后粗滤。发现过滤速度不正常要查明原因。若因网破而使过滤质量不好,则必须重新过滤,以保证质量。
⑤聚合。为加快聚合,用真空泵及时抽出产生的乙二醇。但真空度及抽气量的变化一定要随着反应进程逐渐改变。聚合初期,反应物浓度高,粘度低,反应速度快,宜用低真空、高抽气量的泵,但到后期则相反,必须用抽气量小的高真空度泵,使聚合反应顺利进行。
⑥出料切粒。料流暴露在空气中的时间尽量要短,以防止氧化。必须协调好出料速度、冷却速度和切粒速度。
四、用聚酯废料生产涂料和油漆 1.地面涂料
(1)原树及配方见表5—34。
表5—34 地面涂料的配方
(2)反应温度:80一85℃,反应时间4—5h。
(3)特点:该涂料具有良好的附着力,耐磨、耐水、耐酸碱。 2.1730聚酯绝缘漆
(1)工艺流程:见图5-31。
反应温度:220—250℃。
特点:该漆耐热,耐电压,优良的绝缘性。
第五节
聚氨酯废弃物
聚氨酯由多元异氰酸酯与聚酯多元醇防或聚醚多元醇逐步聚合反应而得。根据所用原料的不同可得到热塑性或热固性聚氨酯。用聚氨酯可制得的产品有泡沫塑料、胶粘剂、涂料、弹性体等,其中以泡沫塑料产量最大,应用最广。因此,其废弃物的数量也大。这类废弃物的主要来源是聚氯酯泡沫塑料生产过程中的残次品、边角料及消费后废弃的泡沫制品。聚氨酯泡沫双双塑料又有软硬泡、软泡之分,在其生产过程中硬泡产生20%左右的废料,而软泡产生l2%左右的废料。
一般说来,软泡的密度在0.02一0.03g/cm3硬泡的密度在0.05一0.04g/cm3,正因为如此,其占地面积大,治理问题尤为突出。
聚氨酯泡沫塑料废弃物的回收利用有物理法和化学法两种。物理回收是指废旧泡沫制品自身并未发生化学结构与组成上的变化而获得再生利用。化学回收是将废旧泡沫制品经化学处理,使泡沫体分解生成多元醇、胺类化合物和液化燃料等化工原料。这是一种行之有效而又经济合理的回收方法。
物理回收的方法:将软泡破碎后,再用胶粘剂固化成块加以利用;将硬泡同热塑性塑料混炼,或与水溶性粘合剂混合加以利用,或者制成复合泡沫塑料,作人工土壤。在此就不一一介绍了。下面主要介绍聚氨酯泡沫塑料的化学回收。
一、热解法
废旧聚氯酯泡沫制品直接置于燃烧炉中在氧气氛围下部分燃烧,释放出热能,使尚未燃烧的泡沫体分解,从而得到聚醚多元醇等原料。它纯度高,可以二次利用再制泡沫塑料。
1.技术条件
热裂解温度为400℃左右; 氧气浓度为21%以上;
聚醚多元醇回收率为50%一55%。 2.操作步骤
将废旧聚氨酯泡沫体破碎后备用,调节好空气中的氧浓度,然后以400L/min的速度导入氧化燃烧炉(容积为30L)。将15g的破碎泡沫于lmin内添加进燃烧炉,使燃烧后溶出的液化物迅速冷却回收。
3.再生泡沫体的性能比较(以聚醚多元醇为例) 新料聚醚多元醇与回收聚醚多元醇以同样配方所制得泡沫体,其发泡性能相同,物理性能稍有下降,参见表5—35。
表5—35 用新料与回收料聚醚多元醇所制泡沫体的性能对比
二、水解法
水解法处理聚氨酯废泡沫可回收较多的化学原料,温度要求低,比热解法优越。 1.工艺流程
如图5—32所示。
2.工艺条件
见表5-36。
3.操作步骤
将聚氨酯泡沫连同金属支架置入裂解炉反应区内,于100kPa、260℃的蒸汽流中持续20min;泡沫开始转化,水解产物中二胺类化合物(气体部分)与蒸汽一起从上部排气口排出,经冷凝回收。液体产物以滴液形式从泡沫下面的捕集器收集,回收的液体生成物为聚氧化丙烯多元醇,将其真空蒸馏,得到聚醚多元醇,其含水量低于0.2%,含甲苯二胺低于0.1%。
三、碱解法
聚氨酯废弃泡沫的碱解工艺是以苛性碱为分解剂,由分解反应、甲苯二胺的分离回收和聚醚的精制三部分组成。
1.工艺流程
碱解法的工艺流程如图5-33所示。
2.分解反应:将20份苛性碱同40份废泡沫的溶剂聚醚混合,升温至160℃时缓慢地加入100份碎泡沫,搅拌溶解。保温约4h.反应结束。
3.甲苯二胺的分离回收
所得液化物经减压蒸馏、在160一175℃,133Pa时回收馏出的甲苯二胺。甲苯二胺的纯度为98.5%以上,凝固点为82—84.5℃。这种回收的甲苯二胺可应用于光气化反应合成甲苯二异氰酸酯(TDI)。
4.聚醚的精制
馏出甲苯二胺后的残留物含有粗聚醚、碳酸钠及其他不纯物。用非亲水性有机溶剂萃取、过滤、再水洗脱出溶剂,经脱水脱色处理后制得精制聚醚。
5.质量对比
回收的精制聚醚可直接应用于制造软质聚氨酯泡沫塑料,这种再生泡沫塑料的物性与制成的软泡很接近,表5—37中列出新旧料两者的质量对比。
表5-37 碱解法回收聚醚与新聚醚质量比较
四、醇解法
以醇类化合物为分解剂,使聚氨酯泡沫加热分解回收聚醚多元醇的方法均称为醇解法。在聚氨酯泡沫塑料废弃物的回收技术中以醇解法最为常用,并已工业化。醇解法工艺条件不高,操作简单,流程短,所得产品可直接重新合成泡沫塑料。 1.工艺条件
硬质聚氨配泡沫塑料的交联密度比较高,要求醇解温度等工艺条件也较苛刻,而软泡和半硬泡废料的醇解条件就比较低,它们使用的热分解剂也各不相同,硬泡通常使用乙二醇或一缩乙二醇等与二乙醇胺相配作醇解剂;半硬泡则以使用一缩丙二醇为佳,泡沫与—缩丙二醇之比为(1一1.5):1;而软泡以使用丙二醇,1.2—丁二醇为佳,其用量为泡沫的50%。
2.分解剂与助分解剂
醇解法中使用的分解剂(又称醇解剂)有:二元醇、二醇、多元醇(或与胺类化合物并用)、聚丙二醇等。助分解剂有叔胺、二烷醇胺、碱金属氢氧化物、卤代磷酸酯。
选用的分解剂和助分解剂不同,其醇解条件和二醇回收条件也不相同。
若以低相对分子质量二醇为热分解剂,如乙二醇、丙二醇、1,4-丁二醇、一缩乙二醇、一缩乙二醇等,则降解温度最好在170—180℃之间,时间为4—8h。分解物分层,上层为聚醚多元醇,下层为含二醇的氨基化合物。前者可二次利用,制造泡沫塑料,后者可作为聚氨酯泡沫塑料的增强剂,环氧树脂或聚氨酯橡胶的交联剂。
3.实例
[例1]将450g—缩乙二醇,25g乙醇胺混合,加热至195土5℃,再逐步添加500g硬质聚氨酯废泡沫碎粉至完全溶解,混合持续30min得到聚醚醇、然后冷却。这种再生聚醚醇需与新聚醚醇混合,方可重新发泡制取硬泡沫。
(1)配方:见表5-38。
(2)再生泡沫制品的性能:见表5—39。
表5-39 再生泡沫制品的性能
[例2]将400g聚醚醇钾分解剂与100g二胺混合,加热到140℃时添加500g硬质聚氨酯废泡沫和236g氢氧化钾,大约5h后完全溶解;约在100℃时析出无机盐碳酸钾,过滤后取700g滤液放入高压釜,于100—l10℃导入230g氧化丙烯单体,使之聚合,生成粗聚醚;用
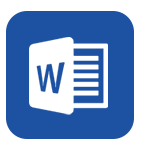