推荐第1篇:SMT近期的工作计划
SMT近期的工作计划
一.SMT车间环境的重新规划(建立一个标准的无尘环保的SMT生产车间、具体布局见附页SMT规划示意图)
1.设备的重新摆放:将现有的A线、B线、C线、F线改成规划后示意图上并排的LINE
1、LINE
2、LINE
3、LINE4等4条2+1的高速生产线;将现有的D线、G线、H线改成示意图上得LINE
5、LINE
6、LINE7线
2.新增SMT办公室、培训室、钢网资料配件房、FEEDER维修房、基本返修房、QA房、SMT工艺宣传栏、品质效率宣传栏、烘烤区、烧录区、BGA返修区和AOI检测区
3.建议SMT车间进行吊顶、所有的电线和气管都从天花板过垂直进入机器接口
4.建议利用假期对SMT车间地板进行重新刷漆。
二.完善SMT的组织结构和合理的人员配置
1.SMT的组织结构和人员的配置见附页
2.将对所有管理人员进行明细的分工和职责范围 3.对所有岗位进行定编定岗和培训
三.SMT 设备的大保养
当设备完成摆放后逐一对每条线进行检修和较为全面的保养
四.完善SMT程序和流程、建立完善的统计数据
1.建立生产效率的日、周、月统计总结;品质的日、周、月统计和总结;物料损耗的统计和结及生产异常的统计和总结
2.建立SMT标准工艺栏和SMT品质、效率栏
五.制定SMT的各项目标
生产效率目标 品质直通率目标 物料损耗目标 生产成本控制目标
以上计划如果在公司的全力支持下将在三个月内完成;三个月后一定会有一个全新、稳定、高效的SMT标准的无尘环保生产车间。
推荐第2篇:SMT近期的工作计划
SMT近期的工作计划
一.SMT车间环境的重新规划(建立一个标准的无尘环保的SMT生产车间、具体布局见附
页SMT规划示意图)
1.设备的重新摆放:将现有的A线、B线、C线、F线改成规划后示意图上并排的LINE
1、
LINE
2、LINE
3、LINE4等4条2+1的高速生产线;将现有的D线、G线、H线改成示意图上得LINE
5、LINE
6、LINE7线
2.新增SMT办公室、培训室、钢网资料配件房、FEEDER维修房、基本返修房、QA房、
SMT工艺宣传栏、品质效率宣传栏、烘烤区、烧录区、BGA返修区和AOI检测区
3.建议SMT车间进行吊顶、所有的电线和气管都从天花板过垂直进入机器接口
4.建议利用假期对SMT车间地板进行重新刷漆。
二.完善SMT的组织结构和合理的人员配置
1.SMT的组织结构和人员的配置见附页
2.将对所有管理人员进行明细的分工和职责范围
3.对所有岗位进行定编定岗和培训
三.SMT 设备的大保养
当设备完成摆放后逐一对每条线进行检修和较为全面的保养
四.完善SMT程序和流程、建立完善的统计数据
1.建立生产效率的日、周、月统计总结;品质的日、周、月统计和总结;物料损耗的
统计和结及生产异常的统计和总结
2.建立SMT标准工艺栏和SMT品质、效率栏
五.制定SMT的各项目标
生产效率目标
品质直通率目标
物料损耗目标
生产成本控制目标
以上计划如果在公司的全力支持下将在三个月内完成;三个月后一定会有一个全新、稳定、高效的SMT标准的无尘环保生产车间。
推荐第3篇:SMT
DIP/SMT分别是什么意思,全称是什么
DIP封装(Dual In-line Package),也叫双列直插式封装技术,如图!
SMT就是表面组装技术(表面贴装技术)(Surface Mounted Technology的缩写),是目前电子组装行业里最流行的一种技术和工艺。
1,SMT作业流程
(SMT)-->进板-->锡膏印刷-->锡膏检查-->贴片作业-->贴片检查-->回焊作业-->终检作业-->(DIP)-->人工插件-->波峰焊接-->补焊作业-->手焊作业-->检查作业-->ICT测试-->组装-->成品(最终)测试(FT:Final Test)-->终检-->包装
2,什么是波峰焊
波峰焊是指将熔化的软钎焊料(铅锡合金),经电动泵或电磁泵喷流成设计要求的焊料波峰,亦可通过向焊料池注入氮气来形成,使预先装有元器件的印制板通过焊料波峰,实现元器件焊端或引脚与印制板焊盘之间机械与电气连接的软钎焊。根据机器所使用不同几何形状的波峰,波峰焊系统可分许多种。
波峰焊流程:将元件插入相应的元件孔中 →预涂助焊剂 → 预烘(温度90-1000C,长度1-1.2m) → 波峰焊(220-2400C) → 切除多余插件脚 → 检查。
回流焊工艺是通过重新熔化预先分配到印制板焊盘上的膏状软钎焊料,实现表面组装元器件焊端或引脚与印制板焊盘之间机械与电气连接的软钎焊
3,SMT与DIP
smt是贴片车间,主要是用贴片机将一些smt元器件贴到pcb板上。
dip是smt的后续工作。pcb板经过smt贴片以后,在经过回流炉,ict以后,就会到dip段。dip就是插件,有人工插件,或是机器插件。
举个简单的例子:我们的电脑主板,南桥北桥sio等芯片就是通过smt贴装上去的,而我们的鼠标键盘接口,usb网卡接口,都是通过dip段插件上去的。
推荐第4篇:SMT
龙源期刊网 http://.cn
SMT车间物料管理系统设计与实现
作者:王凡 毕明路 郭瑞刚
来源:《现代电子技术》2011年第07期
摘要:在SMT车间生产中,物料管理是不可缺少的一部分,传统简单的仓储管理系统已无法保证现代SMT车间生产的需要。为了满足SMT车间多品种变批量的生产需求,根据SMT车间物料管理的要求,分析了SMT车间物料管理的需求,采用Delphi 7和SQL Server 2000设计实现了一种新的物料管理系统,有效地利用仓库空间,满足SMT柔性制造的需要。关键词:SMT;数据库设计;物料管理;数据库查询
推荐第5篇:SMT习题
SMT:将元件装配到印刷电路板或其它基板上的工艺方法称为SMT SMT表面贴装技术 AOI自动光学检查
贴片机將電子元件貼裝到已經印刷了錫膏或膠水的PCB上的設備。
为什么要使用SMT技术?
1.電子產品追求小型化,以前使用的穿孔插件元件已無法縮小 。 (2)无引线或引线很短,减少了寄生电容和寄生电感,从而改善了高频特性,有利于提高使用频率和电路速度。
(3)形状简单、结构牢固,紧贴在印制板表面上,提高了可靠性和抗振性。
(4)组装时没有引线的打弯、剪线,在制造印制板时,减少了插装元器件的通孔,降低了成本。
(5)形状标准化,适合于用自动贴装机进行组装,效率高、质量2.電子產品功能更完整,所採用的積體電路(IC)已無穿孔元件,特別是大規模、高集成IC,不得不採用表面貼片元件 。
3.產品批量化,生產自動化,廠方要以低成本高產量,出產優質產品以迎合顧客需求及加強市場競爭力 。 SMT三大工序
SMT技术的三大工序是锡膏印刷、贴片和回流焊接。 锡膏的基本成分是锡粉和助焊剂。
贴片机按照功能可以分为高速机和泛用机,分别使用贴片头类型为转塔型和拱架型。
回焊炉分为几个区域,功能分别为? 预热区 恒温区 回焊区冷却区
预热区功能:溶剂挥发;均匀加热元件及电路板
恒温区功能:焊剂清除焊件表面的氧化物;使元件和电路板没有温差、受热均匀;焊料完全干燥 回焊区功能:錫膏的熔融、再流动 冷却区功能:焊膏的冷却、凝固
警示灯显示绿灯亮代表机器正在运行中,黄灯闪代表机器待机状况下发出警告讯息,红灯亮代表在生产中机器反正故障停机。 静电防护
静电泄漏和耗散的有效方式为接地。 电子工业静电的4种危害形式。
1、静电吸附
2、静电放电引起的器件击穿
3、静电感应
4、静电放电时产生的电磁脉冲 如何进行静电手环的检测?
1.將靜電手環戴在手上﹐注意要緊貼皮膚。2.將靜電手環的另一端插入測試儀的插孔內。
3﹑上面錄色指示燈亮﹐証明手环是好的﹐其它燈亮則說明手环不符合 ESD 要求。要報告給你的主管﹐要求換手环。 SMT元器件
SMT元器件按照特性一般分为主动元件和被动元件。
零件封装是指实际零件焊接到电路板时所指示的外观和焊点位置。 封裝型半导体器件一般可分为两种,分别是塑封器件和陶瓷封裝器件。
DIP雙列直插式封裝 QFP方形扁平封裝 BGA球形柵格陣列封装 表面贴装元器件的特点?
(1)提高了组装密度,使电子产品小型化、薄型化、轻量化,节省原材料。
好、综合成本低。
在焊接的实际应用中,锡和铅按一定比例搭配的Sn- Pb焊锡被广泛使用,其中Sn63%-Pb37%组成的焊锡一般称为共晶焊锡。 焊接的三要素是清洁、加热和形成合金层。 焊接有润湿﹑扩散﹑合金化三种现象。
助焊剂是是粘結劑(樹脂),溶剂,活性剂,触变剂及其它添加剂組成。
焊接的目的?
1.導通電流﹕將兩種金屬連接在一起,形成電流通路。2.機械連接﹕將兩種金屬接合,使二者穩定、固定。 3.密閉效果﹕通過焊接,防止連接部位進入水、空氣、油等。 4.其他﹕通過焊錫防止金屬表面鍍層氧化(生鏽)。 锡膏的优点。
可以控制錫膏的供給量,只供給需要焊接的部分。 能夠微量供給→對應高精密度貼裝
向基板供給錫膏的方式多種多樣。(鋼板印刷、絲網印刷、點錫等) →具有通用性。
具有粘性,對于貼裝的元件具有臨時固定作用。
供給后,只要加熱到適當的溫度就可以進行焊接。→焊接簡單易行。 锡膏选择的基本原则?
①合金粉末的颗粒大小及形状;②金属粉末的含量;③焊剂类型;④焊膏的稳定性。
叙述一下助焊剂在焊接过程中的作用。
Flux的作用就是將這些臟污和氧化膜去掉,使焊接順利進行,減少表面張力以增加焊錫性,促進潤濕的發生。 (1)溶解被焊母材表面的氧化膜
在大气中,被焊母材表面总是被氧化膜覆盖着,其厚度大约为2×10-9~2×10-8m。在焊接时,氧化膜必然会阻止焊料对母材的润湿,焊接就不能正常进行,因此必须在母材表面涂敷助焊剂,使母材表面的氧化物还原,从而达到消除氧化膜的目的。 (2)形成保護膜,可防止再氧化的發生
焊接中的金屬(基材)及熔化的焊錫,比常溫下氧化的速度更快。在焊接過程中,Flux覆蓋在金屬表面,阻止了它們與空氣的接觸,從而防止了因為加熱焊接引起的再氧化的發生。 (3)降低熔融焊料的表面张力,促进润湿作用
熔融焊料表面具有一定的张力,就像雨水落在荷叶上,由于液体的表面张力会立即聚结成圆珠状的水滴。熔融焊料的表面张力会阻止其向母材表面漫流,影响润湿的正常进行。当助焊剂覆盖在熔融焊料的表面时,可降低液态焊料的表面张力,使润湿性能明显得到提高。
推荐第6篇:smt年终总结
smt年终总结范文3篇
表面组装技术surface mount technology(SMT),是将SMT专用电子零件经由焊接媒介或接着剂焊接于电路板上的技术。本文是小编为大家整理的smt年终的总结范文,仅供参考。
smt年终总结范文篇1:
喜迎新春,首先感谢稚启各位领导对我的关心、指导和帮助,给我一次机会让我得到锻炼、成长,以下是我对xx年的工作总结:
一、SMT工艺方面
1、xx年对物料追踪、管控有较往年进一步提高,生产前有对各个产品之重点物料(如BGA、芯片和PCB) 之生产周期、储存环境等进行查看,确认是否氧化和变形等异常,评估其可焊性,并确认烘烤条件(时间、温度),避免回流发生气泡、分层和断裂等不良;
2、针对我司设备生产要求条件、生产效率和焊接品质方面考量,对客户的PCB Layout 提出改善建议,要求添加标准mark点、5mm工艺边、制作拼版等,且部分客户已采纳建议,品质、效率得到进一步改善;
3、对锡膏进行分类标示,做到先进先出原则,使用状态(解冻、回温、搅拌)标识更加明确,对锡膏出现硬块、及暴露在空气中时间有进一步管控,对有BGA、芯片的PCB,要求做到使用首次回温的锡膏,以确保焊接品质;
4、为确保产品的焊接质量,尽量对每款产品的炉温曲线进行实板测试,对带有BGA的PCBA重点进行制定、优化,并交与袁工、卢工进行审核;
5、学习并掌握了修补PCB镀金层的工艺能力;
6、对试产的产品生产过程进行跟踪,收集生产异常并提出改善建议向客户端进行反馈,下批次生产时进行追踪、确认。
二、SMT设备方面
1、为减少抛料率以及维持设备良好性能,加强了对设备维护、保养频率(吸嘴、过滤芯 一周两次、加油维护 一月一次);
2、因设备使用时间较长,恐其板卡因风扇不工作或灰尘堆积导致其散热性不佳,规定定期对其板卡的清洁度及风扇进行点检,发现异常及时处理,避免出现隐患;
3、增加了冷风干燥机,避免了真空里有水的现象;
4、协助技术员定期检查Europlacer 的塑胶吸嘴头,确认是否有磨损严重、破裂等现象,出现异常立即更换,避免出现抛料现象;
5、培训并指导印刷机、贴片机、AOI、X-RAY的程序制作及异常报警处理,提高技术员及操作员的工作技能,并制作培训作业指导书备份于系统。
三、工作问题及不足
1、部分产品结尾单时,未及时回流,锡膏在空气中放置时间过长,助焊剂挥发后影响焊接质量;
2、部分客户来料生产周期较长或储存条件不当,导致料件异常(如氧化、变形),导致回流后必须手工补锡,影响生产效率及焊接品质;
3、车间地面环境较差,贴片机工作时吸嘴及过滤芯易吸附空气中灰尘,容易堵塞,造成抛料;
4、SMT车间及物料房之温室度达不到要求,湿度较低环境干燥,易产生静电损坏器件;
5、部分客户之PCB器件间距设计较小,Europlacer因使用塑胶头吸嘴,与料件接触面较大,贴装时存在干扰,连续贴装时间长后,会出现吸嘴粘料现象,导致有缺件、抛料等不良;
6、Europlacer贴片机无服务器,产线整体料件优化全靠技术人员,易出现生产瓶颈站,影响稼动率及生产效率;
7、AOI程序制作需较长时间,且软件bug较多,系统不稳定,xx年出现三次程序全部清空现象,影响检验效率和效果;
8、X-RAY 不能正常稳定工作,影响SMT正常工艺检测及分析;
四、xx年工作计划
1、进一步提升SMT工艺能力,完善及优化工艺流程,让作业更加快速、有效、简便;
2、更加详细的对产品的制造过程进行跟踪、记录并存档,后续出现异常,便于追溯、分析和解决;
3、制定详细的设备保养计划,在不影响生产计划的情况下,分批次、逐一对设备关键部位(如贴装头、真空泵、板卡)进行维护、保养,提高设备工作性能;
4、积极协助、配合生产部门,力争第一时间解决工艺异常和设备异常,确保产品的焊接质量和生产效率;
smt年终总结范文篇2:
来到**工作已有大半年了,这段时间里我学会了贴片设备的操作技能及许多实际的工作经验,也体会到公司上级领导的随和及对员工的关心。从已习惯严厉苛刻的民营企业转换到人性化管理国企里,两种截然不同的管理方式和环境,使我有许多学习的机会,因此我自身的专业技能得到了很大的提升。
xx年5月份我从东莞民营的工厂辞职来到公司的SMT工作,刚来时,面对新的工作环境新的工作方式很不习惯,在这里,公司主张一人多岗,要懂很多SMT方面的知识才能把工作做好,到现在我才发现我以前在民营企业里学到的东西太少了,根本无法安时安量完成组长安排给我的工作,还好公司常会找相关的资料来培训我们新员工,组长和老员工也很热心把各岗位的知识教给我们。
刚来的第一个月,组长常安排我到仓库领物料,这个岗位的工作我做起是得心应手 因为我本身对SMT的物料有较深的认识,所以做起来感觉很轻松,但当上级领导给机会我学习JUKI贴片机的操作和编程时我才感觉到自己很吃力,因为我对贴片机认识不深,也从未动过手去编程,所以一切学起来觉得很难,还好上级领导及老员工很认真地把贴片机的操作和编程的步骤一点一点地教会我,现在我已能自已独立来完成JUKI贴片机的操作和编程,对贴片机也有了一定的认识。
时间过得真快,不知不不觉在公司工作已有大半年,从中学到了很多实际生产经验及对设备操作的技能,但这只是一小部份,这里还有很多东西值得我认真去学习,在即将到来的新一年里,我计划在明年五月份前学会MPM印刷机和YAMAHA贴片机的编程与操作,同时我也会更加努力把各岗位的工作做好,争取做一个优秀的员工,为公司尽一份心出一份力.
smt年终总结范文篇3:
xx年悄然离去,这一年里,在公司的领导及各位班组成员的帮助与支持下,按照公司与车间要求,通过不断的努力,文成了自己的本质工作,并在现有的工作模式上有了新的突破,工作效率方面都有了较大的提升,先将xx年的工作情况总结如下:
1.狠抓生产效率:
相当于公司其他车间而言,SMT车间是自动化程度较高的车间,
2.保证产品质量,提高产品品质
随着SMT这个行业的竞争越来越大,各公司对于如何......我深知作为车间班组长,自己的工作直接影响车间的工作质量,出于对公司的负责任的想法,在质量方面我一直不敢有所松懈,积极发现并控制可能会出现的问题,对于严重的品质隐患,及时的配合各部门以及相关人员有效的处理,杜绝类似问题的再次发生,同事加强员工对质量的重要性认识,要求大家认真做好自检互检工作,确保不让不良品流入下一道工序;
3.加强班组建设,提高班组管理力度
考核制度
4.加强自身学习,提高管理水平
由于感到自己身上的打字很重,而自己的学识,能力和阅历与一名优秀称职的班组张都有一定的距离。所以一直不敢掉以轻心,一直在学习,积极提高自身各项管理知识,女里提升工作效率和工作质量,争取工作的主动性通过这一年的学习感觉自己还是有一点进步,能够独立,从容的处理日常工作中的各项问题......
二.工作中出现的问题
。。。。。。。。
1.班组管理方面:
2.质量控制方面
3.生产效率方面
4.节约方面
三.xx年的工作计划:
,,,,,,,,,,,,,
推荐第7篇:SMT检讨书
篇一:smt 检讨书 检讨书
尊敬的领导: 您好!感谢您在百忙之中抽空看我写的检讨书!我在此为我在11月25日上错料做如下检讨: 我不想再为自己的错误找任何借口,那只能让我更加惭愧。这份检讨书,向您表示我对这种错误行为的深痛恶绝,我下定决心,不再 犯类似错误。其时,领导反复教导言犹在耳,严肃认真的表情犹在眼前,我深为震撼,也已经深刻认识到此事的重要性,于是我一再告诉自己要把此事当成头等大事来抓,不能辜负领导和同事对我的一片苦心。 自己并没有好好的去考虑我现在的责任,造成了工作的失误。 通过这件事,我感到虽然是一件偶然发生的事情,但同时也是长期以来对自己放松了要求,工作做风涣散的必然结果,也是与我们时代要求-----树新风,讲文明,背道而行。经过几天的反思,我对自己这些年的工作成长经历进行了详细回忆和分析。记得刚上班的时候,我对自己的要求还是比较高的,时时处处也都能遵守相关规章制度,从而努力完成各项工作。但近期,由于工作逐渐走上了轨道,而自己对公司的一切也比较熟悉了,尤其是领导对我的关怀和帮助使我感到温暖的同时,也慢慢开始放松了对自己的要求,反而认为自己已经做得很好了。因此,这次发生的事使我不仅感到是自己的耻辱,更为重要的是我感到对不起领导对我的信任,愧对领导的关心。 如今,大错既成,我深深懊悔不已,深刻检讨。本人思想中的致命错误有以下几点:思想觉悟不高,对重要事项认识严重不足。就算是有认识,也没能在行动上真正实行起来。
思想觉悟不高的根本原因是因为本人对待工作的思想观念不够深刻、不够负责。我决定做出如下整改:
1、对自己思想上的错误根源进行深挖细找,并认清其可能造成的严重后果。
2、认真克服生活懒散、粗心大意的缺点,努力将工作做好,以优秀的表现来弥补我的过错。
3、经常和同事加强沟通,保证不再出现类似错误。此外,我也看到了这件事的恶劣影响,如果在工作中,大家都像我一样自由散漫,漫不经心,那怎么能及时把工作落实好、做好呢?同时,如果在我们这个集体中形成了这种目无组织纪律观念,不良风气、不文明表现,我们工作的提高将无从谈起,服务也只是纸上谈兵。因此,这件事的后果是严重的,影响是恶劣的。
短短几百字,不能表述我对自己的谴责;更多的责骂,深藏在我的心理。盼望领导能给我改过自新的机会。如果公司能给我改过的机会,我会化悔恨为力量,我绝不在同一地方摔倒,以后我要努力工作,认真负责,争取为公司的发展做出更大的贡献。
在这件事中,我还感到,自己在工作责任心上仍就非常欠缺。这充分说明,我从思想上没有把工作的方式方法重视起来,这也说明,我对自己的工作没有足够的责任心,也没有把自己的工作做得更好,也没给自己注入走上新台阶的思想动力。在自己的思想中,仍就存在得过且过,混日子的应付思想。现在,我深深感到,这是一个非常危险的倾向,也是一个极其不好的苗头,如果而放任自己继续放纵和发展,那么,后果是极其严重的,甚至都无法想象会发生怎样的工作失误。因此,通过这件事,在深感痛心的同时,我也感到了幸运,感到了自己觉醒的及时,这在我今后的人生成长道路上,无疑是一次关键的转折。在此,我向领导做出深刻的检讨。 检讨人:易晓安
时间:2012年12月14篇二:smt炉后目视检查作业指导书 smt炉后目视检查作业指导书
一、作业流程: 1.全数将传送台或套板ok的pcb取下,仔细检查固化后的是否有假焊、偏移、多件、
少料、浮高、短路、零件破损、侧立、误配、反向、反面、少锡等不良,检验标准(依ipc-a-610dcla 2客户另有要求除外)如下: a.假焊:部品焊接端与pcb未有锡连接或未完全连接, b.偏移:零件偏移量不超过焊盘尺寸的1/3或角度偏移不能超过35度.c.组件破损:电极上的裂痕或缺口玻璃组件上的裂缝刻度及电阻的缺口损伤等不良.d.反面:有上下面之分的元器件出现反面现象.e.侧立:部品与pcb的接触部分不在同一平面而形成一个夹角.f.误配:pcb上贴装的部品与设计所需的部品p/n不相符.g.反向:有极性的组件贴片方向与实计贴片的方向相反.h.短路:组件与组件、pin与pin之间不在同条线路有锡连接.i浮高:部品与焊盘之间空隙超过0.1mm.j.少锡:锡量不足爬上组件焊接端高度之1/3 2.针对所检查出的不良做出标示并区分放置在红色“不良品”拖盘内,不良现象及时记录 报表.(终检处可自行维修,可使用无铅烙铁,但须具有相当水准能力才可作业,且须自检维修此位及周边组件有否破损、连锡、假焊).3.如当班时间内同种不良发生3次以上须向拉长报告,针对严重缺陷需及时反馈相关工程人员.4.全数检查pcb外观,是否残有异物,ic点检记号是否用其它颜色点检,记号不可有划到文字丝印.5.检查ok之pcb用黑色蜡笔在指定的板边固定作上自已的代号区分放置标示,放可流入下一工位(客户要求除外).
二、使用工具: 1.静电手套2.静电环3.rohs油性笔4.报表5.不良标签
三、注意事项: 1.作业前佩戴ok防静电手环和手套.2.pcb轻拿轻放,板边有组件须朝外放置.3.所有机种严禁在板内作记号.4.物料须核对正确,须全部为无铅.5.拿取pcb须拿pcb板板边,勿触摸组件
6.ic点检记号不可划到本体丝印篇三:smt车间检查表 smt车间检查表
推荐第8篇:SMT生产工艺
SMT就是表面组装技术(表面贴装技术)(Surface Mounted Technology的缩写),是目前电子组装行业里最流行的一种技术和工艺。
SMT有何特点:
组装密度高、电子产品体积小、重量轻,贴片元件的体积和重量只有传统插装元件的1/10左右,一般采用SMT之后,电子产品体积缩小40%~60%,重量减轻60%~80%。
可靠性高、抗振能力强。焊点缺陷率低。
高频特性好。减少了电磁和射频干扰。
易于实现自动化,提高生产效率。降低成本达30%~50%。 节省材料、能源、设备、人力、时间等。 电脑贴片机,如图
为什么要用SMT:
电子产品追求小型化,以前使用的穿孔插件元件已无法缩小
电子产品功能更完整,所采用的集成电路(IC)已无穿孔元件,特别是大规模、高集成IC,不得不采用表面贴片元件
产品批量化,生产自动化,厂方要以低成本高产量,出产优质产品以迎合顾客需求及加强市场竞争力
电子元件的发展,集成电路(IC)的开发,半导体材料的多元应用
电子科技革命势在必行,追逐国际潮流
SMT 基本工艺构成要素:
丝印(或点胶)-->贴装 -->(固化) -->回流焊接 -->清洗 -->检测 -->返修
丝印:其作用是将焊膏或贴片胶漏印到PCB的焊盘上,为元器件的焊接做准备。所用设备为丝印机(丝网印刷机),位于SMT生产线的最前端。
点胶:它是将胶水滴到PCB的的固定位置上,其主要作用是将元器件固定到PCB板上。所用设备为点胶机,位于SMT生产线的最前端或检测设备的后
面。
贴装:其作用是将表面组装元器件准确安装到PCB的固定位置上。所用设备为贴片机,位于SMT生产线中丝印机的后面。
固化:其作用是将贴片胶融化,从而使表面组装元器件与PCB板牢固粘接在一起。所用设备为固化炉,位于SMT生产线中贴片机的后面。
回流焊接:其作用是将焊膏融化,使表面组装元器件与PCB板牢固粘接在一起。所用设备为回流焊炉,位于SMT生产线中贴片机的后面。
清洗:其作用是将组装好的PCB板上面的对人体有害的焊接残留物如助焊剂等除去。所用设备为清洗机,位置可以不固定,可以在线,也可不在线。
检测:其作用是对组装好的PCB板进行焊接质量和装配质量的检测。所用设备有放大镜、显微镜、在线测试仪(ICT)、飞针测试仪、自动光学检测
(AOI)、X-RAY检测系统、功能测试仪等。位置根据检测的需要,可以配置在生产线合适的地方。
返修:其作用是对检测出现故障的PCB板进行返工。所用工具为烙铁、返修工作站等。配置在生产线中任意位置。
SMT常用知识简介
一般来说,SMT车间规定的温度为25±3℃。
2.锡膏印刷时,所需准备的材料及工具锡膏、钢板、刮刀、擦拭纸、无尘纸、清洗剂、搅拌刀。
3.一般常用的锡膏合金成份为Sn/Pb合金,且合金比例为63/37。
4.锡膏中主要成份分为两大部分锡粉和助焊剂。
5.助焊剂在焊接中的主要作用是去除氧化物、破坏融锡表面张力、防止再度氧化。
6.锡膏中锡粉颗粒与Flux(助焊剂)的体积之比约为1:1, 重量之比约为9:1。
7.锡膏的取用原则是先进先出。
8.锡膏在开封使用时,须经过两个重要的过程回温、搅拌。
9.钢板常见的制作方法为:蚀刻、激光、电铸。
10.SMT的全称是Surface mount(或mounting) technology,中文意思为表面粘着(或贴装)技术。
11.ESD的全称是Electro-static discharge, 中文意思为静电放电。
12.制作SMT设备程序时, 程序中包括五大部分, 此五部分为CB data; Mark data; Feeder data; Nozzle data; Part data。
13.无铅焊锡Sn/Ag/Cu 96.5/3.0/0.5的熔点为 217C。
14.零件干燥箱的管制相对温湿度为
15.常用的被动元器件(Paive Devices)有:电阻、电容、点感(或二极体)等;主动元器件(Active Devices)有:电晶体、IC等。
16.常用的SMT钢板的材质为不锈钢。
17.常用的SMT钢板的厚度为0.15mm(或0.12mm)。
18.静电电荷产生的种类有摩擦、分离、感应、静电传导等;静电电荷对电子工业的影响为:ESD失效、静电污染;静电消除的三种原理为静电中和、接地、屏蔽。
19.英制尺寸长x宽0603=0.06inch*0.03inch,公制尺寸长x宽3216=3.2mm*1.6mm。
20.排阻ERB-05604-J81第8码“4”表示为4个回路,阻值为56欧姆。电容ECA-0105Y-M31容值为C=106PF=1NF =1X10-6F。
21.ECN中文全称为:工程变更通知单;SWR中文全称为:特殊需求工作单,必须由各相关部门会签, 文件中心分发, 方为有效。
22.5S的具体内容为整理、整顿、清扫、清洁、素养。
23.PCB真空包装的目的是防尘及防潮。
24.品质政策为:全面品管、贯彻制度、提供客户需求的品质;全员参与、及时处理、以达成零缺点的目标。
25.品质三不政策为:不接受不良品、不制造不良品、不流出不良品。
26.QC七大手法中鱼骨查原因中4M1H分别是指(中文): 人、机器、物料、方法、环境。
27.锡膏的成份包含:金属粉末、溶济、助焊剂、抗垂流剂、活性剂;按重量分,金属粉末占85-92%,按体积分金属粉末占50%;其中金属粉末主要成份为锡和铅, 比例为63/37,熔点为183℃。
28.锡膏使用时必须从冰箱中取出回温, 目的是:让冷藏的锡膏温度回复常温,以利印刷。如果不回温则在PCBA进Reflow后易产生的不良为锡珠。
29.机器之文件供给模式有:准备模式、优先交换模式、交换模式和速接模式。
30.SMT的PCB定位方式有:真空定位、机械孔定位、双边夹定位及板边定位。
31.丝印(符号)为272的电阻,阻值为 2700Ω,阻值为4.8MΩ的电阻的符号(丝印)为485。
32.BGA本体上的丝印包含厂商、厂商料号、规格和Datecode/(Lot No)等信息。
33.208pinQFP的pitch为0.5mm。
34.QC七大手法中, 鱼骨图强调寻找因果关系;
35.CPK指: 目前实际状况下的制程能力;
36.助焊剂在恒温区开始挥发进行化学清洗动作;
37.理想的冷却区曲线和回流区曲线镜像关系;
38.Sn62Pb36Ag2之焊锡膏主要试用于陶瓷板;
39.以松香为主的助焊剂可分四种: R、RA、RSA、RMA;
40.RSS曲线为升温→恒温→回流→冷却曲线;
41.我们现使用的PCB材质为FR-4;
42.PCB翘曲规格不超过其对角线的0.7%;
43.STENCIL制作激光切割是可以再重工的方法;
44.目前计算机主板上常用的BGA球径为0.76mm;
45.ABS系统为绝对坐标;
46.陶瓷芯片电容ECA-0105Y-K31误差为±10%;
47.目前使用的计算机的PCB, 其材质为: 玻纤板;
48.SMT零件包装其卷带式盘直径为13寸、7寸;
49.SMT一般钢板开孔要比PCB PAD小4um可以防止锡球不良之现象;
50.按照《PCBA检验规范》当二面角>90度时表示锡膏与波焊体无附着性;
51.IC拆包后湿度显示卡上湿度在大于30%的情况下表示IC受潮且吸湿;
52.锡膏成份中锡粉与助焊剂的重量比和体积比正确的是90%:10% ,50%:50%;
53.早期之表面粘装技术源自于20世纪60年代中期之军用及航空电子领域;
54.目前SMT最常使用的焊锡膏Sn和Pb的含量各为: 63Sn+37Pb;
55.常见的带宽为8mm的纸带料盘送料间距为4mm;
56.在20世纪70年代早期,业界中新出现一种SMD, 为“密封式无脚芯片载体”, 常以HCC简代之;
57.符号为272之组件的阻值应为2.7K欧姆;
58.100NF组件的容值与0.10uf相同;
59.63Sn+37Pb之共晶点为183℃;
60.SMT使用量最大的电子零件材质是陶瓷;
61.回焊炉温度曲线其曲线最高温度215C最适宜;
62.锡炉检验时,锡炉的温度245℃较合适;
63.钢板的开孔型式方形、三角形、圆形,星形,本磊形;
64.SMT段排阻有无方向性无;
65.目前市面上售之锡膏,实际只有4小时的粘性时间;
66.SMT设备一般使用之额定气压为5KG/cm2;
67.SMT零件维修的工具有:烙铁、热风拔取器、吸锡枪、镊子;
68.QC分为:IQC、IPQC、.FQC、OQC;
69.高速贴片机可贴装电阻、电容、IC、晶体管;
70.静电的特点:小电流、受湿度影响较大;
71.正面PTH, 反面SMT过锡炉时使用何种焊接方式扰流双波焊;
72.SMT常见之检验方法: 目视检验、X光检验、机器视觉检验
73.铬铁修理零件热传导方式为传导+对流;
74.目前BGA材料其锡球的主要成Sn90 Pb10;
75.钢板的制作方法雷射切割、电铸法、化学蚀刻;
76.迥焊炉的温度按: 利用测温器量出适用之温度;
77.迥焊炉之SMT半成品于出口时其焊接状况是零件固定于PCB上;
78.现代质量管理发展的历程TQC-TQA-TQM;
79.ICT测试是针床测试;
80.ICT之测试能测电子零件采用静态测试;
81.焊锡特性是融点比其它金属低、物理性能满足焊接条件、低温时流动性比其它金属好;
82.迥焊炉零件更换制程条件变更要重新测量测度曲线;
83.西门子80F/S属于较电子式控制传动;
84.锡膏测厚仪是利用Laser光测: 锡膏度、锡膏厚度、锡膏印出之宽度;
85.SMT零件供料方式有振动式供料器、盘状供料器、卷带式供料器;
86.SMT设备运用哪些机构: 凸轮机构、边杆机构、螺杆机构、滑动机构;
87.目检段若无法确认则需依照何项作业BOM、厂商确认、样品板;
88.若零件包装方式为12w8P, 则计数器Pinth尺寸须调整每次进8mm;
89.迥焊机的种类: 热风式迥焊炉、氮气迥焊炉、laser迥焊炉、红外线迥焊炉;
90.SMT零件样品试作可采用的方法:流线式生产、手印机器贴装、手印手贴装;
91.常用的MARK形状有:圆形,“十”字形、正方形,菱形,三角形,万字形;
92.SMT段因Reflow Profile设置不当, 可能造成零件微裂的是预热区、冷却区;
93.SMT段零件两端受热不均匀易造成:空焊、偏位、墓碑;
94.高速机与泛用机的Cycle time应尽量均衡;
95.品质的真意就是第一次就做好;
96.贴片机应先贴小零件,后贴大零件;
97.BIOS是一种基本输入输出系统,全英文为:Base Input/Output System;
98.SMT零件依据零件脚有无可分为LEAD与LEADLESS两种;
99.常见的自动放置机有三种基本型态, 接续式放置型, 连续式放置型和大量移送式放置机;
100.SMT制程中没有LOADER也可以生产;
101.SMT流程是送板系统-锡膏印刷机-高速机-泛用机-迥流焊-收板机;
102.温湿度敏感零件开封时, 湿度卡圆圈内显示颜色为蓝色,零件方可使用;
103.尺寸规格20mm不是料带的宽度;
104.制程中因印刷不良造成短路的原因:a.锡膏金属含量不够,造成塌陷b.钢板开孔过大,造成锡量过多c.钢板品质不佳,下锡不良,换激光切割模板d.Stencil背面残有锡膏,降低刮刀压力,采用适当的VACCUM和SOLVENT
105.一般回焊炉Profile各区的主要工程目的:a.预热区;工程目的:锡膏中容剂挥发。b.均温区;工程目的:助焊剂活化,去除氧化物;蒸发多余水份。c.回焊区;工程目的:焊锡熔融。d.冷却区;工程目的:合金焊点形成,零件脚与焊盘接为一体;
106.SMT制程中,锡珠产生的主要原因:PCB
PAD设计不良、钢板开孔设计不良、置件深度或置件压力过大、Profile曲线上升斜率过大,锡膏坍塌、锡膏粘度过低。
推荐第9篇:smt基本知识
1.一般来说,SMT车间规定的温度为25±3℃。
2.锡膏印刷时,所需准备的材料及工具锡膏、钢板﹑刮刀﹑擦拭纸、无尘纸﹑清洗剂﹑搅拌刀。
3.一般常用的锡膏合金成份为Sn/Pb合金,且合金比例为63/37。
4.锡膏中主要成份分为两大部分锡粉和助焊剂。
5.助焊剂在焊接中的主要作用是去除氧化物﹑破坏融锡表面张力﹑防止再度氧化。
6.锡膏中锡粉颗粒与Flux(助焊剂)的体积之比约为1:1, 重量之比约为9:1。
7.锡膏的取用原则是先进先出。
8.锡膏在开封使用时,须经过两个重要的过程回温﹑搅拌。
9.钢板常见的制作方法为﹕蚀刻﹑激光﹑电铸。
10.SMT的全称是Surface mount(或mounting) technology,中文意思为表面粘着(或贴装)技术。
11.ESD的全称是Electro-static discharge, 中文意思为静电放电。
12.制作SMT设备程序时, 程序中包括五大部分, 此五部分为PCB data; Mark data; Feeder data; Nozzle data; Part data。
13.无铅焊锡Sn/Ag/Cu 96.5/3.0/0.5的熔点为 217C。
14.零件干燥箱的管制相对温湿度为
15.常用的被动元器件(Paive Devices)有:电阻、电容、点感(或二极体)等;主动元器件(Active Devices)有:电晶体、IC等。
16.常用的SMT钢板的材质为不锈钢。
17.常用的SMT钢板的厚度为0.15mm(或0.12mm)。
18.静电电荷产生的种类有摩擦﹑分离﹑感应﹑静电传导等﹔静电电荷对电子工业的影响为﹕ESD失效﹑静电污染﹔静电消除的三种原理为静电中和﹑接地﹑屏蔽。
19.英制尺寸长x宽0603= 0.06inch*0.03inch﹐公制尺寸长x宽3216=3.2mm*1.6mm。
20.排阻ERB-05604-J81第8码“4”表示为4 个回路,阻值为56欧姆。电容ECA-0105Y-M31容值为C=106PF=1NF =1X10-6F。
21.ECN中文全称为﹕工程变更通知单﹔SWR中文全称为﹕特殊需求工作单﹐必须由各相关部门会签, 文件中心分发, 方为有效。
22.5S的具体内容为整理﹑整顿﹑清扫﹑清洁﹑素养。
23.PCB真空包装的目的是防尘及防潮。
24.品质政策为﹕全面品管﹑贯彻制度﹑提供客户需求的品质﹔全员参与﹑及时处理﹑以达成零缺点的目标。
25.品质三不政策为﹕不接受不良品﹑不制造不良品﹑不流出不良品。
26.QC七大手法中鱼骨查原因中4M1H分别是指(中文): 人﹑机器﹑物料﹑方法﹑环境。
27.锡膏的成份包含﹕金属粉末﹑溶济﹑助焊剂﹑抗垂流剂﹑活性剂﹔按重量分﹐金属粉末占85-92%﹐按体积分金属粉末占50%﹔其中金属粉末主要成份为锡和铅, 比例为63/37﹐熔点为183℃。
28.锡膏使用时必须从冰箱中取出回温, 目的是﹕让冷藏的锡膏温度回复常温﹐以利印刷。如果不回温则在PCBA进Reflow后易产生的不良为锡珠。
29.机器之文件供给模式有﹕准备模式﹑优先交换模式﹑交换模式和速接模式。
30.SMT的PCB定位方式有﹕真空定位﹑机械孔定位﹑双边夹定位及板边定位。
31.丝印(符号)为272的电阻,阻值为 2700Ω,阻值为4.8MΩ的电阻的符号(丝印)为485。
32.BGA本体上的丝印包含厂商﹑厂商料号﹑规格和Datecode/(Lot No)等信息。
33.20834.QC七大手法中, 鱼骨图强调寻找因果关系; 35.CPK指: 目前实际状况下的制程能力; 36.助焊剂在恒温区开始挥发进行化学清洗动作; 37.理想的冷却区曲线和回流区曲线镜像关系; 38.Sn62Pb36Ag2之焊锡膏主要试用于陶瓷板; 39.以松香为主的助焊剂可分四种: R﹑RA﹑RSA﹑RMA; 40.RSS曲线为升温→恒温→回流→冷却曲线; 41.我们现使用的PCB材质为FR-4; 42.PCB翘曲规格不超过其对角线的0.7%; 43.STENCIL制作激光切割是可以再重工的方法; 44.目前计算机主板上常用的BGA球径为0.76mm; 45.ABS系统为绝对坐标; 46.陶瓷芯片电容ECA-0105Y-K31误差为±10%; 47.目前使用的计算机的PCB, 其材质为: 玻纤板; 48.SMT零件包装其卷带式盘直径为13寸、7寸; 49.SMT一般钢板开孔要比PCB PAD小4um可以防止锡球不良之现象; 50.按照《PCBA检验规范》当二面角>90度时表示锡膏与波焊体无附着性; 51.IC拆包后湿度显示卡上湿度在大于30%的情况下表示IC受潮且吸湿; 52.锡膏成份中锡粉与助焊剂的重量比和体积比正确的是90%:10% ,50%:50%; 53.早期之表面粘装技术源自于20世纪60年代中期之军用及航空电子领域; 54.目前SMT最常使用的焊锡膏Sn和Pb的含量各为: 63Sn+37Pb; 55.常见的带宽为8mm的纸带料盘送料间距为4mm; 56.在20世纪70年代早期,业界中新出现一种SMD, 为“密封式无脚芯片载体”, 常以HCC简代之; 57.符号为272之组件的阻值应为2.7K欧姆; 58.100NF组件的容值与0.10uf相同; 59.63Sn+37Pb之共晶点为183℃; 60.SMT使用量最大的电子零件材质是陶瓷; 61.回焊炉温度曲线其曲线最高温度215C最适宜; 62.锡炉检验时,锡炉的温度245℃较合适; 63.钢板的开孔型式方形﹑三角形﹑圆形,星形,本磊形; 64.SMT段排阻有无方向性无; 65.目前市面上售之锡膏,实际只有4小时的粘性时间; 66.SMT设备一般使用之额定气压为5KG/c67.SMT零件维修的工具有﹕烙铁﹑热风拔取器﹑吸锡枪、镊子; 68.QC分为﹕IQC﹑IPQC﹑.FQC﹑OQC; 69.高速贴片机可贴装电阻﹑电容﹑ IC﹑晶体管; 70.静电的特点﹕小电流﹑受湿度影响较大; 71.正面PTH, 反面SMT过锡炉时使用何种焊接方式扰流双波焊; 72.SMT常见之检验方法: 目视检验﹑X光检验﹑机器视觉检验
73.铬铁修理零件热传导方式为传导+对流; 74.目前BGA材料其锡球的主要成Sn90 Pb10; 75.钢板的制作方法雷射切割﹑电铸法﹑化学蚀刻; 76.迥焊炉的温度按: 利用测温器量出适用之温度; 77.迥焊炉之SMT半成品于出口时其焊接状况是零件固定于PCB上; 78.现代质量管理发展的历程TQC-TQA-TQM; 79.ICT测试是针床测试; 80.ICT之测试能测电子零件采用静态测试; 81.焊锡特性是融点比其它金属低﹑物理性能满足焊接条件﹑低温时流动性比其它金属好; 82.迥焊炉零件更换制程条件变更要重新测量测度曲线; 83.西门子80F/S属于较电子式控制传动; 84.锡膏测厚仪是利用Laser光测: 锡膏度﹑锡膏厚度﹑锡膏印出之宽度; 85.SMT零件供料方式有振动式供料器﹑盘状供料器﹑卷带式供料器; 86.SMT设备运用哪些机构: 凸轮机构﹑边杆机构﹑螺杆机构﹑滑动机构; 87.目检段若无法确认则需依照何项作业BOM﹑厂商确认﹑样品板; 88.若零件包装方式为12w8P, 则计数器Pinth尺寸须调整每次进8mm; 89.迥焊机的种类: 热风式迥焊炉﹑氮气迥焊炉﹑laser迥焊炉﹑红外线迥焊炉; 90.SMT零件样品试作可采用的方法﹕流线式生产﹑手印机器贴装﹑手印手贴装; 91.常用的MARK形状有﹕圆形,“十”字形﹑正方形,菱形,三角形,万字形; 92.SMT段因Reflow Profile设置不当, 可能造成零件微裂的是预热区﹑冷却区; 93.SMT段零件两端受热不均匀易造成﹕空焊﹑偏位﹑墓碑; 94.高速机与泛用机的Cycle time应尽量均衡; 95.品质的真意就是第一次就做好; 96.贴片机应先贴小零件,后贴大零件; 97.BIOS是一种基本输入输出系统,全英文为:Base Input/Output System; 98.SMT零件依据零件脚有无可分为LEAD与LEADLESS两种; 99.常见的自动放置机有三种基本型态, 接续式放置型, 连续式放置型和大量移送式放置机; 100.SMT制程中没有LOADER也可以生产; 101.SMT流程是送板系统-锡膏印刷机-高速机-泛用机-迥流焊-收板机; 102.温湿度敏感零件开封时, 湿度卡圆圈内显示颜色为蓝色,零件方可使用; 103.尺寸规格20mm不是料带的宽度; 104.制程中因印刷不良造成短路的原因﹕a.锡膏金属含量不够,造成塌陷b.钢板开孔过大,造成锡量过多c.钢板品质不佳,下锡不良,换激光切割模板d.Stencil背面残有锡膏,降低刮刀压力,采用适当的VACCUM和SOLVENT 105.一般回焊炉Profile各区的主要工程目的:a.预热区;工程目的:锡膏中容剂挥发。b.均温区;工程目的:助焊剂活化,去除氧化物;蒸发多余水份。c.回焊区;工程目的:焊锡熔融。d.冷却区;工程目的:合金焊点形成,零件脚与焊盘接为一体; 106.SMT制程中,锡珠产生的主要原因﹕PCB PAD设计不良、钢板开孔设计不良、置件深度或置件压力过大、Profile曲线上升斜率过大,锡膏坍5S : 5S管理
ABC : 作业制成本制度 (Activity-Based Costing) ABB : 实施作业制预算制度 (Activity-Based Budgeting) ABM : 作业制成本管理 (Activity-Base Management) APS : 先进规画与排程系统 (Advanced Planning and Scheduling) ASP : 应用程式服务供应商(Application Service Provider) ATP : 可承诺量 (Available To Promise) AVL : 认可的供应商清单(Approved Vendor List) BOM : 物料清单 (Bill Of Material) BPR : 企业流程再造 (Busine Proce Reengineering) BSC :平衡记分卡 (Balanced ScoreCard) BTF : 计划生产 (Build To Forecast) BTO : 订单生产 (Build To Order) CPM : 要径法 (Critical Path Method) CPM : 每一百万个使用者会有几次抱怨(Complaint per Million) CRM : 客户关系管理 (Customer Relationship Management) CRP : 产能需求规划 (Capacity Requirements Planning) CTO : 客制化生产 (Configuration To Order) DBR : 限制驱导式排程法 (Drum-Buffer-Rope) DMT : 成熟度验证(Design Maturing Testing) DVT : 设计验证(Design Verification Testing) DRP : 运销资源计划 (Distribution Resource Planning) DSS : 决策支援系统 (Decision Support System) EC : 设计变更/工程变更 (Engineer Change) EC : 电子商务 (Electronic Commerce) ECRN : 原件规格更改通知(Engineer Change Request Notice) EDI : 电子资料交换 (Electronic Data Interchange) EIS : 主管决策系统 (Executive Information System) EMC : 电磁相容(Electric Magnetic Capability) EOQ : 基本经济订购量 (Economic Order Quantity) ERP : 企业资源规划 (Enterprise Resource Planning) FAE : 应用工程师(Field Application Engineer) FCST : 预估(Forecast) FMS : 弹性制造系统 (Flexible Manufacture System) FQC : 成品品质管制 (Finish or Final Quality Control) IPQC : 制程品质管制 (In-Proce Quality Control) IQC : 进料品质管制 (Incoming Quality Control) ISO : 国际标准组织 (International Organization for Standardization) ISAR : 首批样品认可(Initial Sample Approval Request) JIT : 即时管理 (Just In Time) KM : 知识管理 (Knowledge Management) L4L : 逐批订购法 (Lot-for-Lot) LTC : 最小总成本法 (Least Total Cost) LUC : 最小单位成本 (Least Unit Cost) MES : 制造执行系统 (Manufacturing Execution System) MO : 制令(Manufacture Order) MPS : 主生产排程 (Master Production Schedule) MRO : 请修(购)单(Maintenance Repair Operation) MRP : 物料需求规划 (Material Requirement Planning) MRPII : 制造资源计划 (Manufacturing Resource Planning) NFCF : 更改预估量的通知Notice for Changing Forecast OEM : 委托代工 (Original Equipment Manufacture) ODM : 委托设计与制造 (Original Design & Manufacture) OLAP : 线上分析处理 (On-Line Analytical Proceing) OLTP : 线上交易处理 (On-Line Transaction Proceing) OPT : 最佳生产技术 (Optimized Production Technology) OQC : 出货品质管制 (Out-going Quality Control) PDCA : PDCA管理循环 (Plan-Do-Check-Action) PDM : 产品资料管理系统 (Product Data Management) PERT : 计画评核术 (Program Evaluation and Review Technique) PO : 订单(Purchase Order) POH : 预估在手量 (Product on Hand) PR : 采购申请Purchase Request QA : 品质保证(Quality Aurance) QC : 品质管制(Quality Control) QCC : 品管圈 (Quality Control Circle) QE : 品质工程(Quality Engineering) RCCP : 粗略产能规划 (Rough Cut Capacity Planning) RMA : 退货验收Returned Material Approval ROP : 再订购点 (Re-Order Point) SCM : 供应链管理 (Supply Chain Management) SFC : 现场控制 (Shop Floor Control) SIS : 策略资讯系统 (Strategic Information System) SO : 订单(Sales Order) SOR : 特殊订单需求(Special Order Request) SPC : 统计制程管制 (Statistic Proce Control) TOC : 限制理论 (Theory of Constraints) TPM : 全面生产管理Total Production Management TQC : 全面品质管制 (Total Quality Control) TQM : 全面品质管理 (Total Quality Management) WIP : 在制品 (Work In Proce)塌、锡膏粘度过低。 m2;pinQFP的pitch为0.5mm。
推荐第10篇:SMT基础知识
SMT岗位职责、基础知识培训
一、印刷工位
作业内容:
1、负责冰箱内温度及锡膏红胶期限的管控;
2、负责生产前、生产中锡膏、红胶的解冻 搅拌以及相应机型钢网、刮刀等辅料的准备及表格填写。
3、对全自动印刷机/半自动印刷机的清洁 日常保养点检工作以及转线时印刷机调试工作;
4、严格控制 连锡 少锡 不良品的制造;每10pcs抽检1pcs
5、PCB的领料及数量核对,印刷PCB时,应对PCB首件进行检查确认、PCB日期填写(写于无元件空白处或背面)
6、保证印刷区域的5S工作。
7、调整合适的印刷速度,以保证贴片机正常生产.
8、将印好焊膏(贴片胶)的板正确地送入贴片机,保证贴片机能够正常生产;
9、检查焊膏(贴片胶)有无印准确,并挑出不良品;保证做到少量多次锡膏的添加
10、将焊膏准确地印在印制板上.并且保证焊膏无严重塌落,边缘整齐.无短路等不良现象. 发现则洗板重新印刷(清洗过的板必须用放大镜检查,PCB上无残留物).
11、印刷中注意锡膏的性能(流动性)
12、机器简单故障的处理
13、转线后钢网的清洗、检查、记录,表格填写、锡膏回收
14、
交接工作、相互沟通
15、
上班纪律
二、高速贴片机工位 作业内容:
1、工作交接,上班物料的确认,以及日常的点检保养工作及表格填写。
2、首件的确认,生产中进行备料以及下个计划物料的准备。
3、生产中用完物料的及时更换,并且填写换料记录表(换料时需二者确认,OK后记录于换料记录表,対料时以物料编号为准),贴出第一块板时必须在首件上标识出来(特别是有极性元件)通知检验员认真核对;
4、处理机器设备在生产时出现的异常情况或简单故障;
5、及时查看机器的抛料状况及时调整与反馈工作,并记录抛料表格中。
6、生产换线时,物料的提前准备以及对生产中的物料确认,发现缺料状况反应物料员领取,退料时做好标识,特别是散料
7、生产换线时负责机器设备的调试及上料工作
8、每两个小时进行一次物料核对.
9、保证贴片机区域的5S工作以及废料盒的清理。
10、上班纪律
二、炉前目检/泛用机操作工位
作业内容:
1、工作交接,上班物料的确认,以及日常的点检保养工作及表格填写。
2、首件的确认,生产中进行备料以及下个计划物料的准备。
3、生产中用完物料的及时更换,并且填写换料记录表(换料时需二者确认,OK后记录于换料记录表,対料时以物料编号为准),贴出第一块板时必须在首件上标识出来(特别是有极性元件)通知检验员认真核对;
4、处理机器设备在生产时出现的异常情况或简单故障;
5、及时查看机器的抛料状况及时调整与反馈工作,并记录抛料表格中。
6、生产换线时,物料的提前准备以及对生产中的物料确认,发现缺料状况反应物料员领取,退料时做好标识,特别是散料
7、生产换线时负责机器设备的调试及上料工作
8、每两个小时及上下班进行一次物料核对.
9、保证贴片机区域的5S工作以及废料盒的清理。
9、检查是否漏贴或元件歪并校正 反馈(漏贴的PCB必须做标识);
10、补件时对于无标识元件要从料盘上取用.并标明补件的位号。告知检验员认真检查,对于取下贴片不良元件后更换或修正,必须确认锡膏量和红胶量,不足可适量添加。
11、每两个小时进行一次物料核对及有极性元件的核对.
12、IC空盘、空管状料等材料包装丢弃前必须认真目检后才可丢弃。
13、上班纪律
三、炉后检验工位
作业内容:
1、工作交接,当班数量的核对确认。
2、日常的点检及保养工作,烙铁温度测量,表格的填写。
3、上线前确认资料是否齐全(首末件表等)异常反馈。
4、首件的核对并填写首末件表。
5、转线时或交班是确认回流焊炉温设定,是否与设定指引相符合及炉温曲线确认。
6、对流出回流焊的板进行检验,机检20pcs目视抽检1pcs,发现不良检不出时及时汇报,良品与不良品的认识与判定,三个相同的不良点及时反馈。AOI误报时必须确认清楚才可流入下一工位。
7、拿取板时防止揰板,无对叠摆放,良品与不良品的区分。
8、生产日报表的填写,数量核对
9、对不良品进行修理、补件时对于无标识元件必须从料盘上取用或使用仪器测量其值。修理时不可造成其他地方不良如(堵孔、连锡),修理OK必须重新检验。.
10、检验区域5S的工作。
11、周转车的调试。
12、不良项认识
五、班长作业内容
1、工作交接、早会
2、车间巡检(相关表格的确认,生产线物料的确认,印刷、贴片状态、炉后质量抽检、抛料率查看与汇报、5S检查等等)。
3、生产线的工作指导及监督。
4、生产日报表的填写,生产看板定如时填写、生产线工作安排
5、支持生产线(装料、换料、备料、修理等等)
6、公司会议的参加
7、新员工入职培训
8、品质、产量监督及原因对策
SMT基础知识问答
1、胶水使用前要回温,请述主要原因?
A 使它在封闭环境里逐渐升至室温,不会因打开使用造成骤热吸水。 B 粘度达到使用要求。
2、操作员在准备PCB板时,为何要判定放板的方向?
因为印刷机、贴片机程序对放板方向有严格的要求
3、操作员在准备PCB板时,放板的方向错误会造成什么不良?
造成识别通不过、降低效率或元器件贴错位
4、为什么装板时应预先戴好干净布手套?
避免徒手污染PCB表面。
5、当SMT车间实际环境参数超过文件要求时,你怎么办?
反馈给工艺工程师处理。
6、锡膏使用前,必须先从冰箱中取出放在室温下回温几4小时以上?
4小时
7、为什么用过的锡膏回收待下次用时,不能与未用过的锡膏混装?
破坏未用过锡膏的质量
8 用过的锡膏回收待下次用时,怎么办?
用一个空瓶单独装。
9 为什么瓶中剩余的锡膏要盖上内盖,内盖下推接触到锡膏面?
挤出内盖和锡膏间空气。 10 如果不拧紧外盖有何坏处?
空气容易进入瓶内,使锡膏氧化严重。 11 清洁纸各用多次较污浊,为何要换?
因为污浊的纸不仅不能擦干净钢网,还使钢网更脏。 12 印胶或点胶后,操作员对前三块板要认真检查什么?
胶点是否完整,胶量是否合适,位置是否正确。 13 为什么生产中每天上午做一次炉温曲线测试?
确认回流炉的稳定性
14 为什么每次转线时操作员对回流炉的轨道宽度进行检查?
宽度调整不合适容易卡板。
15、潮湿敏感器件常见的是哪一类?
IC类
16、印刷了锡膏的板,超过时间将板用怎么清洗?
先用白布沾酒精抹干净,再超声波清洗
17、印刷了锡膏的板从开始贴片到完成该面回流焊接,要求几小时内完成?
2小时
18、PCB板印刷焊膏后,发现某些焊盘少锡或无锡(钢网无问题),可能是因为?
A、网板少锡膏 B、网孔堵住
19、PCB板印刷焊膏时,印刷压力过大将会有什么不好
A、引起连锡 或锡珠 B、磨损刮刀
20、贴片料常见的包装方式有哪三种?
A、盘式 B、卷带式 C、管式
21、自动化设备紧急开关的作用有 ?
A、保护人身安全 B、保护设备安全 C、减少生产损失
22、在向钢网上添加锡膏时,添加量如何控制?
保证钢网上滚动的锡膏柱径在1厘米左右/少量多次
23、印有锡膏的板子要求在多长时间内过炉?
半小时
24、PCB开封多长时间未生产需进行烘烤?
48小时。
25、PCB 的全称?
PRINTED CIRCUIT BOARD
26、回流炉指示灯在什么状态可以过板?
绿色灯亮
27、胶水为何不能污染焊盘?
过波峰焊后引起虚焊。
28、搅拌锡膏时为何戴手套?
防止污染人的皮肤。
29、锡膏有毒吗?
有
30、生产前为何要测试防静电腕带?
检测防静电腕带是否失效,带得正确与否。
31、锡膏从冰箱拿出解冻时可以撕开瓶口的密封胶吗?
不能。
32、如果生产线急用锡膏,而恰好要用的锡膏的解冻时间只有2小时,可以破例使用,这种说法对吗?
不对。
33、怎样清洗钢网?
网板用过后,先用抹布沾酒精清洗干净表面,再用牙刷沾酒精清洗钢网开口(清洗时用牙刷的毛刷顺着开口方向刷洗,严禁用牙刷的杆体部分接触钢网,特别是IC开口部分),以彻底清除钢网开口内壁残留锡膏(重点是IC引脚开口内壁),最后用无纤维纸或无纤维布对钢网两面同时擦洗,擦洗完检查无误后立即放回对应的钢网位中。
SMT设备转线操作步骤(现场培训)
印刷机
一、钢网、锡膏、红胶的提前准备。
二、调整机器的轨道及相应宽度,使其与PCB宽度相符--------调整项目包括:转送轨道的宽度/ PCB板固定夹具的宽度/ PCB居中调整/ PCB平度调整
三、读取程序(设备或磁盘)--------1.设备调出操作:按F8返回菜单画面;按F1(PROGRAM.SELECT)读出所需要程序。 2.磁盘调出操作:按F8返回菜单画面;按F2(DATA INPUT/OUT PUT);按F1(NC PROGRAM);按F1 (LOAD CFD—PA、、、)读出所需要程序。
四、MAKE 确认
1.全自动或半自动模式下,插入手动盘打起钢网固定器,放入钢网,再关闭钢网固定器。2.按操作菜单画面REQUEST键转至生产画面。 3.按下操作版面(自动AUOT和连续CONT)键,后按F1校正钢网MAKE,OK后封住钢网MAKE孔。 4.选择刮刀—钢刮刀和胶刮刀。5.加锡膏或红胶试印刷,OK 后批量生产。
高速贴片机:
一、使用手动操作盘,按下PCB定位夹具将台面打下。
二、取下台面下所以顶针。
三、按操作菜单画面REQUEST键进入画面。四.按F8返回服务功能菜单(F1---F7)画面。
五.按F1(PROGRAM SELECT)读取相应生产程序,读取后按F8退出,退出是询问是否调整轨道宽度?
第11篇:smt规章
贴片车间规章制度
为了进一步强化贴片车间现场管理,创造一个良好的工作氛围,不断提高产品质量,降低生产成本,提高公司经济效益。同时保障公司和员工的利益。经上级领导研究决定特制定本>,SMT车间所有员工必须遵守,具体规定如下
1. SMT车间所有人员进入车间必须穿防静电衣服进入车间,出入SMT生产车间必须随手关门
2.工作调配由组长统一根据工作的需要来确定人员位置,任何人员不可有挑剔工作的行为,一切均服从安排。
3.员工对管理人员,管理制度,任何其他的人有意见或者见意,可以当面或书面的形式对相关人员或相关人员的上司提出。由管理人员协调解决,不得背后议论或煽动事非。员工对管理人员不服时可以投诉,但不得顶撞报复,否则将给予严重处分。
4.车间员工上班必须提前五分钟进入车间,工作交接时应尽量保持小声,严禁大声喧哗,说笑,和争吵,如发生争执由组长进行处理。
5.所有员工应按时上下班,做到不迟到,不早退,不旷工(如遇赶货,上下班时间按照车间安排执行),有事需请假,请假需提前一天填写当班组长批准后生效.紧急情况下可随时处理.病假需提供病假证明.请假未经同意,私自不上班以旷工处理,旷工一天将扣除当月全勤奖。
6.上班迟到/早退每1分钟罚款1元,上班时间开始后5分钟至30分钟内才上班者,按迟到论处;超过30分钟以上者,按旷工半天论处。提前30分钟以内下班者,按早退论处;超过30分钟者,按旷工半天论处。
7.各岗位人员必须每天对自己5S责任区进行打扫,包括地面的清扫,机台表面,灰尘的擦拭,主管将不定时对车间现场5S进行检查
8.车间设备都是贵重物品,应确保公司财产安全。必须做到安全生产,严禁在车间内跑动,机台上严禁放置任何物品(如印刷工位的工具及清洁剂等)使用设备时必须小心谨慎。
9.车间所有作业员在上班期间严禁玩手机或接听电话,如有急事处理可出车间短时间处理(时间在两分钟左右),同时需要知会当班组长
10.所有在贴片车间上班的员工,必须严格遵守车间的生产秩序,严禁吃零食、闲聊天、玩手机上网、看杂志、打瞌睡、睡觉等,做与工作不相干的事。不得将私人用品放在生产线上.如有违反将按车间奖罚制度处理
11.员工有责任维护工作之环境卫生,严禁随地吐痰,乱扔垃圾。在生产过程中要注意节约用料,不得随意乱扔物料、工具。 二.员工奖罚制度
全勤奖:根据员工考勤,工作一个月无迟到,早退,请假,旷工,可获取全月勤奖100元,如有一次迟到,早退,请假当月月勤奖减50元,两次以上者均无月勤奖
处罚项:违反公司车间制度或不按作业流程作业导致不良发生者,第一次将给予警告,第二次给予十元罚款,屡犯或未按作业流程操作造成严重问题者将给予小过30元或大过60元罚款,视情节轻重及对问题认识程度处理。如对公司造成重大损失者,视情节轻重,由公司研究决定处理。 三.物料损耗控制
为了减少物料损耗,减少公司生产成本,增强SMT所有员工的责任心,使其能够爱护公司财物,做到人人监管。现要求生产过程中做到以下监控措施
1.生产线在领取物料时应点清数量需点实数,保证上线物料数量足够
2.生产线不存放整套物料或散料,所有多余物料存放在货架。减少物料丢失机会
3.生产线操作员杜绝上料时物料浪费,生产转线时需将机器抛料倒出,放在指定袋中,如多则需手工贴掉。
批准:
执行时间:
第12篇:SMT物料
SMT物料管理
班级:
学号:
姓名
SMT物料管理
表面组装技术是一门包括电子元器件、装配设备、焊接方法和装配辅助材料等内容的系统性综合技术。为了保证电子产品的质量,做好工艺质量管理的同时,对SMT物料的管理也是相当重要的。下面我将对SMT生产中的焊膏、焊剂、点胶用的胶、PCB板等物料的特性,储存条件及管理做一下介绍。
焊锡膏是将焊料粉末与具有助焊功能的糊状焊剂混合而成的一种浆料,通常焊料粉末占90%左右,其余是化学成分。焊锡膏是一种假塑性流体(非牛顿流体)。其特点是在较高切变率下,切变率随切应力以大于正比的关系增加。应力下的这种“稀释”作用对于丝网印刷非常重要,它可以使钎料膏在印刷操作时粘性降低,流动性增强,易于流入丝印孔内并印刷到PCB的焊盘上。而在印刷之后,钎料膏粘度又增加,保持其填充形状而不向下塌陷。当印刷焊锡膏时,由于重力和张力的原因,好焊锡膏要求有良好的抗坍塌性能,不仅常温印刷、贴片时有这种要求,高温150℃时都要求有这种良好的性能,否则,再流焊预热时就会产生坍塌。
焊锡膏是一种比较敏感的SMT贴片加工焊接材料,污染、氧化或吸潮都会使其产生不同程度的变质,而焊锡膏变质后不仅会使流动性改变而影响印刷效果,更严重的是会造成焊接不良,降低成品一次合格率,因此需要在制造过程上加以注意,以提高焊锡膏的使用效果。 (一)、焊锡膏的保存要求
焊膏的保存应该以密封形态存放在恒温、恒湿的冷柜内,保存温度为0℃~10℃,如温度过高,焊膏中的合金粉未和焊剂起化学反应后,使粘度、活性降低影响其性能;如温度过低,焊剂中的树脂会产生结晶现象,使焊膏形态变坏。在保管过程中,更重要的一点是应注意保持“恒温”这样一个问题,如果在较短的时间内,使锡膏不断地从各种环境下反复出现不同的温度变化,同样会使焊锡膏中焊剂性能产生变化,从而影响焊锡膏的焊接品质。最大的库存时间为六个月,室温下的储存时间为四周(20.5℃~25℃),最佳运输方式为筒装。
(二)、使用前的要求 焊膏从冷柜(或冰箱)中取出时,应在其密封状态下,待其回到室温后再开封,约为2-3小时;如果刚从冷柜中取出就开封,存在的温差会使焊膏结露、凝成水份,这样会导致在回流焊时产生焊锡珠;但也不可用加热的方法使焊锡膏回到室温,急速的升温会使焊膏中焊剂的性能变坏,从而影响焊接效果。这也是锡膏使用厂商在使用过程中应该注意的一个问题。
(三)、使用时的注意事项
1、刮刀压力:保证印出焊点边缘清晰、表面平整、厚度适宜;
2、刮刀速度:保证焊膏相对于刮刀子为滚动而非滑动,一般情况下,10-20mm/s为宜;
3、印刷方式:以接触式印刷为宜;
另外,在使用时要对焊膏充分搅拌,再按印刷设定量加到印刷网板上,采用点注工艺的,还须调整好点注量。
在长时间的印刷情况下,因焊膏中溶剂的挥发,会影响到印刷时锡膏的脱模性能,因此对存放焊锡膏的容器不可重复使用(只可一次性使用),印刷后网板上所剩的焊锡膏,应用其它清洁容器装存保管,下次再用时,应先检查所剩锡膏中有无结块或凝固状况,如果过分干燥,应添加供应商提供的锡膏稀释剂调稀后再用。
操作人员作业时,要注意避免焊膏与皮肤直接接触。另外,印刷完成的基板,应当天完成焊接。焊膏已经回温到室温后,不能再放回冰箱
(四)、工作环境要求
焊锡膏工作场所最佳状况为:温度20~25℃,相对湿度50~70%,洁净、无尘、防静电。
助焊剂作业安全事项
1.助焊剂为易燃之化学材料,在通风良好的环境作业,并远离火种。 2.助焊剂应储存于阴凉通风处,远离火种,避免阳光直射。 3.开封后的助焊剂应先密封后储存,已使用之助焊剂请勿再倒入原包装以确保原液的清洁。
4.已报废之助焊剂需请专人处理,不可随意倾倒污染环境。
5.不慎沾染手脚时,立即用肥皂、清水冲洗。沾染五官时,立即用肥皂、清水冲洗。勿用手揉搓,要送医院治疗。 点胶用的胶水的运输及储存条件
最长的运输时间:供货商发货后,4天之内必须到生产线 。储存的条件:不同型号的胶水存储条件不同,Loctite3593型号胶用冰箱冷藏在-20°C~+8°C ,Emerson and Cuming E1216型号胶,冷藏在-20 °C, 最大储存时间:Loctite3593型号胶在 -20 °C ~ +8 °C的条件下储存6个月 ,Emerson and Cuming E1216型号胶在-20°C条件下储存6个月。 使用前稳定时间:Loctite3593型号胶使用前须达到室温,Emerson and Cuming E1216型号胶需3小时,罐装的储存时间:Loctite3593型号胶要5周,Emerson and Cuming E1216型号胶要5天,均在+20°C的条件下。
印刷电路板(PCB)的储存、管理作业条件
运输包装要用真空,防潮袋包装(参照EIA583 CLASS 2, 50PANEL/BAG,HIC湿度标示卡) 加干燥剂,并且在每个包装的两侧面用PWB STACK板放置弯曲。 进料要检验,检查真空包装有没有破损,HIC卡片是否是
1、领料与入库都要数清楚: 在仓库领料与产品入库时都要与对口人员当面点清数量,无误后双方签名。
2、先来先用不能乱: 按材料的制造时期,先生产的先使用,后生产的后使用,有以下优点: ⑴、确保在保质期内使用; ⑵、确定不良对策线索时需用; ⑶、品质改善时需用;
3、材料去向要清楚: 不是所有的材料都能组装出成品,中途分流的材料要有合理的理由,分流的数量要补回,否则生产计划就无法达成。
材料管理时需注意:
⑴、非正常生产所需的材料,尽量从仓库领取,而不是从制造现场取得; ⑵、作《材料去向清单》,实施现场材料管理追踪; ⑶、当日不良当日清理;
⑷、及时记录和销去不同生产单位之间转用材料的数目; ⑸、制定相应奖惩制度,防止人为遗失、损毁材料; ⑹、改善材料保管和作业环境,防止盗窃和天灾的发生;
4、副料管理要清楚: 缺少副料,生产一样无法进行,副料的好坏不仅直接影响着品质,它在成本中也占据着一定比例。管理时需注意:
⑴、指定专职管理人员,负责申请、领取、保管、派发、统计等工作; ⑵、额定单位用量⑶分门别类保管好; ⑷、定期统计台帐,寻找规律; ⑸、简化领取手序; ⑹、励行节约为本的原则; ⑺、完备报废手序。
5、不良品退回要确认: 现场不良品退回时一定要请品管人员确认OK,并签名后,方可退回。
6、搬运方式要讲究: 搬运作业需要遵循以下一些基本原则:
⑴、机动性原则,既保持随时可以搬动的状态; ⑵、自动化原则; ⑶、避免等待和空搬的原则。 ⑷、缩短移动途径的原则;
7、材料摆放要整齐、清楚。
8、盘点时候要仔细。
9、不用的时候保存好。
10、报废大笔挥不得。
11、追加工、选别要有品管签核的样品。
12、当天下班时材料要归位。
13、算准在线库存量。
14、特殊材料,特别管理。
15、特采不慎是自杀。
16、申领手续要齐全。
17、早早反馈不良情报。
SMT工厂的物料周转很快,很多工厂大部分的物料保存期间都不会超过1个星期。这样不仅仅是出于资金周转的考虑,还有一个原因是很多电子元件物料也有其保值期,如果保存时间过长,某些电气特性会有可能发生改变。正因为这样管理严格的工厂会要求先进先出管理,避免某些进货较早的物料一直未被使用最后过了“保质期”,最后造成不必要的浪费。 那么怎样做到先进先出管理呢。具体有如下几种做法:
方法一 位置管理
例如进料都从料架的左侧放入,而取料都从料架的右侧取出,好比一个队列,先取出的都是先进的物料。如果有退库的料原则上也应该放在最右边,也就是说下次用到该物料时应该先用这个料。
方法二 位置管理+记号管理
在上述位置管理的基础上,在每个进料上盖一个日期戳,比方说 2008/09 表示9月份进的料,这样即使由于盘点等原因,造成料盘摆放次序不正确,仍然可以找到最早进来到料。 方法三 位置管理+条码标签管理
在上述位置管理的基础上,为每个进料贴附一个条码标签,标签中包含了进料日期的信息,这样在出库的时候,只要扫描这个条码,通过在库管理系统查找是否有比这个料更早的料,如果有的话提示出库操作人员应该使用另一个更早进的料。如果结合在库管理系统,甚至可以提示出库操作人员应该取用的料在仓库中的料架位置。
在经费受限制的情况下,通过加强管理,使用方法二可以满足基本的先入先出管理。如果有导入系统的计划,不妨在考虑在库管理系统的同时要求系统供应商提供先入先出的功能,这样在最大限度上保证了先入先出管理,还可以避免人为疏忽造成的失误。
物料损耗严重控制措施,无外乎在人\\机\\料\\法
人:主要指产线的操作员,平时他们在上料时,下线时,到底有没有真正的视每一颗物料为\"金子\".掉在地上的料有没有放起来,并手摆.机器频繁报警时是否及时反映工程等.机:平时机器是否切实执行保养作业,吸嘴是否经常清洁检测,料架是否经常保养校正,程式编写是否正确等.料:物料是否有来料异常,如来料包装太紧,取不到料抛了;来料破损,更换损耗等.法:如作业员操作机器的熟练程度,分辨及合理使用料架的能力等.控制人为的浪费的办法:
1、拆装料不当:对设备操作人员进行培训,对应的包装形式使用对应的料架
2、用错料,重工浪费:每班有3次查料,换料时对应料盘以一换一的方式进行,由专门人员确认,并测试数值
3、物料领取及退库数每天都有点实数的
4、机器设备不良导致异常消耗,有时候没有办法及时发现,还没有办法及时避免
5、有发现有时候操作人员为了追求产量,提前换料,没有做完的物料就消耗掉了,现在也没有办法控制。
6、对于线上正常生产时候所产生的不良品的返修消耗,暂时也没有好的办法控制 总之一句话,有效的控制抛料率,并非只从机器方面进行考虑,应该从各个方面进行分析
原因,给出对策,进行改善.
第13篇:SMT技术发展
SMT技术发展
一.概述
SMT是电子电路表面组装技术(Surface Mount Technology),称为表面贴装或表面安装技术。它是一种将无引脚或短引线表面组装元器件(简称SMC/SMD,中文称片状元器件)安装在印制电路板(Printed Circuit Board,PCB)的表面或其它基板的表面上,通过再流焊或浸焊等方法加以焊接组装的电路装连技术
二.SMT设备
(一)上板机
上板机是贴片生产线上全自动上料(PCB)机,摆放在贴片线首位,即贴片机前。主要功能是接收到下位机要板信号后,从PCB料架上一件一件推出PCB板。料架结构:进出轨道分别放一个料架(一上一下),升降里一个料架,共三个。
(二)印刷机
1、手动印刷机
手动印刷机是通过人手动给PCB板上锡的机器,手动印刷机价格便宜,操作简单但其定位精度差,只适用于印刷要求较低的场合和科研。
2、半自动印刷机
SMT半自动印刷机,用于取代手印台,实现半自动锡膏印刷 ,钢网自动上升下降,PCB需要手工载入和取出。半自动印刷机特点是: (1)PLC控制系统,工作稳定可靠,触控式操作,简单方便。
(2)高精密架构,采用进口线形导轨、调速马达传动,确保印刷之稳定性和精密度。
(3)根据红胶和锡膏的各种不同的特性,自动设定运行参数,可适合不同的产品以达到良好效果。
(4)伸缩自如的手臂座,机台手臂可分别左右调整,适合于不同基板尺寸。
3、全自动印刷机
全自动印刷机是利用模板被印刷刮刀向下压,这样一来模板的底 部就可以充分的接触到电路板的顶面,从而进行印刷作业的。全自动印刷机优点:PCB尺寸兼容范围广,高精度印刷分辨率’全自动锡膏印刷机控制可以提高生产效率,控制品质,节省成本
(三)点胶机
1、手工点胶机
手工点胶机,就是由手动来控制点胶控制器的开关,属于半自动化点胶机的范畴,自动化程度不高,一般常用于点胶产品种类多,规格多的设备上,不适宜批量生产的物品的点胶。
2、全自动点胶机 全自动点胶机是通过压缩空气将胶压进与活塞相连的进给管中,当活塞处于上冲时,活塞室中填满胶,当活塞下推时胶从点胶头压出。全自动点胶机适用于流体点胶,在自动化程度上远远高于手动点胶机,从点胶的效果来看,产品的品质级别会更高。自动化的操作,简单可控。点胶机应用的行业在不断的扩大,生产技术也在不断的创新。
(四)贴片机
1、动臂式贴片机
动臂式贴片机运动机构、贴装头机构和控制系统,贴装头机构安装于运动机构上,控制系统通过线路控制运动机构和贴装头机构的工作,运动机构包括安装由贴装头机构的横梁、平行并列的两个运动轴和一对丝杠机构,横梁安装于运动轴上,且与运动轴垂直,其上设有导轨和用于贴装头横向移动的两个电机,运动轴上设有同步驱动横梁纵向移动的电机,一对丝杠机构分别安装于运动轴上。
2、转塔式贴片机
转塔式贴片机是元件送料器放于一个单坐标移动的料车上,基板(PCB)放于一个X/Y坐标系统移动的工作台上,贴片头安装在一个转塔上,工作时,料车将元件送料器移动到取料位置,贴片头上的真空吸料嘴在取料位置取元件,经转塔转动到贴片位置(与取料位置成180度),在转动过程中经过对元件位置与方向的调整,将元件贴放于基板上。
3、模组式贴片机
元件送料器、基板(PCB)是固定的,贴片头(安装多个真空吸料嘴)在送料器与基板之间来回移动,将元件从送料器取出,经过对元件位置与方向的调整,然后贴放于基板上。由于贴片头是安装于拱架型的X/Y坐标移动横梁上,所以得名。
(五)焊接设备
1、电烙铁
电烙铁是电子制作和电器维修的必备工具,主要用途是焊接元件及导线,按机械结构可分为内热式电烙铁和外热式电烙铁,按功能可分为无吸锡电烙铁和吸锡式电烙铁,根据用途不同又分为大功率电烙铁和小功率电烙铁。
2、回流焊炉
回流焊炉在电子制造领域并不陌生,我们电脑内使用的各种板卡上的元件都是通过这种焊炉焊接到线路板上的,这种设备的内部有一个加热电路,将空气或氮气加热到足够高的温度后吹向已经贴好元件的线路板,让元件两侧的焊料融化后与主板粘结。这种工艺的优势是温度易于控制,焊接过程中还能避免氧化,制造成本也更容易控制。
3、波峰焊炉
波峰焊是让插件板的焊接面直接与高温液态锡接触达到焊接目的,其高温液态锡保持一个斜面,并由特殊装置使液态锡形成一道道类似波浪的现象,所以叫波峰焊,完成波峰焊的机器就是波峰焊炉。
(六)清洗设备
1、超声波清洗机
超声波在液体中传播,使液体与清洗槽在超声波频率下一起振动,液体与清洗槽振动时有自己固有频率,这种振动频率是声波频率,所以人们就听到嗡嗡声。超声波清洗机的优点是:超声波清洗效果好,操作简单。
三.电子制造工艺
(一)技术文件
技术文件是指公司的产品设计图纸,各种技术标准、技术档案和技术资料以及未打印出图的尚在计算机里的图纸资料、技术文档等。
(二)工艺文件
指导工人操作和用于生产、工艺管理等的各种技术文件。
一、品质管理
(一)ISO9000:2015 ISO9000质量管理体系是国际标准化组织(ISO)制定的国际标准之一,在1994年提出的概念,是指\"由ISO/TC176(国际标准化组织质量管理和质量保证技术委员会)制定的所有国际标准\"。该标准可帮助组织实施并有效运行质量管理体系,是质量管理体系通用的要求和指南。
(二)QC七手法 QC七手法又称品管七大手法,它是常用的统计管理方法,又称为初级统计管理方法。它主要包括控制图、因果图、直方图、排列图、检查表、层别法、散布图等所谓的QC七工具。
(三)5S 5S起源于日本,是指在生产现场中对人员、机器、材料、方法等生产要素进行有效的管理,这是日本企业一种独特的管理办法。因为这5个词日语中罗马拼音的第一个字母都是“S”,所以简称为“5S”,开展以整理、整顿、清扫、清洁和素养为内容的活动,称为“5S”活动。
四,工艺流程。
六,发展趋势。
未来SMT装备技术发展趋势:
新技术革命和成本压力催生了自动化、智能化和柔性化生产制造,组装、物流装连、封装、测试一体化系统MES。SMT设备通过技术进步提高电子业自动化水平实现少人作业,降低人工成本增加个人产出,保持竞争力,是SMT制造业的主旋律。高性能、易用性、灵活性和环保是SMT设备的主要发展必然趋势: 1).高精度、柔性化:行业竞争加剧、新品上市周期日益缩短、对环保要求更加苛刻;顺应更低成本、更微型化趋势,对电子制造设备提出了更高的要求。电子设备正在向高精度、高速易用、更环保以及更柔性的方向发展。贴片头功能头实现任意自动切换;贴片头实现点胶、印刷、检测反馈,贴装精度的稳定性将更高,部品和基板窗口大兼容柔性能力将更强。
2).高速化、小型化:带来实现高效率、低功率、占空间少、低成本。贴片效率与多功能双优的高速多功能贴片机的需求逐渐增多,多轨道、多工作台贴装的生产模式生产率可达到100000CPH左右。
3.半导体封装与SMT融合趋势:电子产品体积日趋小型化、功能日趋多样化、元件日趋精密化,半导体封装与表面贴装技术的融合已成大势所趋。半导体厂商已开始应用高速表面贴装技术,而表面贴装生产线也综合了半导体的一些应用,传统的技术区域界限日趋模糊。技术的融合发展也带来了众多已被市场认可的产品。POP技术已经在高端智能产品上广泛使用,多数品牌贴片机公司提供倒装芯片设备(直接应用晶圆供料器),即为表面贴装与半导体装配融合提供了良好的解决方案。
七.总结。
目前,封装技术的定位已从连接、组装等一般性生产技术逐步演变为实现高度多样化电子信息设备的一个关键技术。更高密度、更小凸点、无铅工艺等需要全新的封装技术,更能适应消费电子产品市场快速变化的需求。 封装技术的推陈出新,也已成为半导体及电子制造技术继续发展的有力推手,并对半导体前道工艺和表面贴装技术的改进产生着重大影响。如果说倒装芯片凸点生成是半导体前道工艺向后道封装的延伸,那么,基于引线键合的硅片凸点生成则是封装技术向前道工艺的扩展。
在整个电子行业中,新型封装技术正推动制造业发生变化,市场上出现了将传统分离功能混合起来的技术手段,正使后端组件封装和前端装配融合变成一种趋势。不难观察到,面向部件、系统或整机的多芯片组件封装技术的出现,彻底改变了只是面向器件的概念,并很有可能会引发SMT产生一次工艺革新。
元器件是SMT技术的推动力,而SMT的进步也推动着芯片封装技术不断提升。片式元件是应用最早、产量最大的表面贴装元件,自打SMT形成后,相应的IC封装则开发出了适用于SMT短引线或无引线的LCCC、PLCC、SOP等结构。四侧引脚扁平封装(QFP)实现了使用SMT在PCB或其他基板上的表面贴装,BGA解决了QFP引脚间距极限问题,CSP取代QFP则已是大势所趋,而倒装焊接的底层填料工艺现也被大量应用于CSP器件中。
随着01005元件、高密度CSP封装的广泛使用,元件的安装间距将从目前的0.15mm向0.1mm发展,这势必决定着SMT从设备到工艺都将向着满足精细化组装的应用需求发展。但SiP、MCM、3D等新型封装形式的出现,使得当今电子制造领域的生产过程中遇到的问题日益增多。
由于MCM技术是集混合电路、SMT及半导体技术于一身的集合体,所以我们可称之为保留器件物理原型的系统。多芯片模组等复杂封装的物理设计、尺寸或引脚输出没有一定的标准,这就导致了虽然新型封装可满足市场对新产品的上市时间和功能需求,但其技术的创新性却使SMT变得复杂并增加了相应的组装成本。
可以预见,随着无源器件以及IC等全部埋置在基板内部的3D封装最终实现,引线键合、CSP超声焊接、PoP(堆叠装配技术)等也将进入板级组装工艺范围。所以,SMT如果不能快速适应新的封装技术则将难以持续发展。
第14篇:SMT knowledge
SMT 磁场电场的区别、联系
在2005-02-26 21:35:15 aiwenti新手说: 问题补充:电场和磁场的本质联系和本质区别? spirit学弟:2005年3月21日 答: 您的答案我看了以后觉得匪夷所思!如果从经典电磁学角度来看,磁场和电场是对带电粒子在场中运动所受力的一种分解所产生的结果。一种与运动速度无关,叫电场。另一种叫磁场。它们的联系在于: 1 电流产生磁场。(毕奥萨法尔定律) 2 变化的磁场产生电场。 (法拉第电磁感应定律) 3 变化的电场产生磁场。 (经过修正的安培环路定则) 若从相对论角度来看,磁场不过是运动电荷所产生的相对论效应的一种非常良好的等效。电场与磁场实际上是一回事。 /浏览284
什么是理想无源元件?理想无源元件是什么意思?
电路中常用的理想电路元件有电阻、电感、电容、理想电压源和理想电流源。理想电
路元件分无源元件和有源元件。
能向电路网络提供能量的元件为有源元件;吸收电源能量,并将这些能量转化为其它形式或将它储存在电场或磁场中的元件为无源元件。从功率角度考虑前者发出功率,后者吸
收功率。
3, 点胶—波峰焊工艺中常见的缺陷与解决方法 1. 拉丝/拖尾
现象:拉丝/拖尾是点胶中常见的缺陷。
产生的原因:胶嘴内径太小,点胶压力太高,胶嘴离PCB的时间距太大,黏胶剂过期或品质不好,贴片胶黏度太高,从冰箱中取出后未能恢复到室温,点胶量太多。
解决方法:改换内径较大的胶嘴,降低点胶压力,调节“止动”高度,换胶,选择适合黏度的胶种,从冰箱中取出后恢复到室温(约4小时),调整点胶量。 2. 胶嘴堵塞
现象:胶嘴出量偏少或没有胶点出来。
产生原因:针孔内未完全清洗干净,贴片胶中混入杂质,有堵孔现象,不相容的胶水相混合。 解决方法:换清洁的针头,换质量好的贴片胶,贴片胶牌号不应搞错。 3. 空打
现象:只有点胶动作,却无出胶量。 产生原因:混入气泡,胶嘴堵塞。
解决方法:注射筒中的胶应进行脱气泡处理(特别是自己装的胶),按胶嘴堵塞方法处理。 4. 元器件移位
现象:固化后元器件移位,严重时元器件引脚不在焊盘上。
产生原因:贴片胶出胶量不均匀(例如片式元件两点胶水中一个多一个少),贴片时元件移位,贴片胶初黏力低,点胶后PCB放置时间太长,胶水半固化。
解决方法:检查胶嘴是否有堵塞,排除出胶不均匀现象,调整贴片机工作状态,换胶水,点胶后PCB放置时间不应太长(小于4小时)。 5. 固化后,元器件黏结强度不够,波峰焊后会掉件
现象:固化后,元器件黏结强度不够,低于规定值,有时用手触摸会出现掉片。
产生原因:固化工艺参数不到位,特别是温度不够,元件尺寸过大,吸热量大,光固化灯老化,胶水量不够,元件/PCB有污染。
解决方法:调整固化曲线,特别是提高固化温度,通常热固化胶的峰值固化温度很关键,达到峰值温度易引起掉片,对光固胶来说,应观察光固化灯是否老化,灯管是否有发黑现象;胶水的数量,元件/PCB是否有污染都是应该考虑的问题。 6. 固化后元件引脚上浮/移位 固化后正确的形态如图27所示。
现象:固化后元件引脚浮起来或移位,波峰焊后锡料会进入焊盘,严重时会出现短路和开路,如图28所示。
产生原因:贴片胶不均匀,贴片胶量过多,贴片进元件偏移。 解决方法:调整点胶工艺参数,控制点胶量,调整贴片工艺参数。
什么是SMT:
SMT就是表面组装技术(Surface Mounted Technology的缩写),是目前电子组装行业里最流行的一种技术和工艺。
SMT有何特点:
组装密度高、电子产品体积小、重量轻,贴片元件的体积和重量只有传统插装元件的1/10左右,一般采用SMT之后,电子产品体积缩小40%~60%,重量减轻60%~80%。
可靠性高、抗振能力强。焊点缺陷率低。
高频特性好。减少了电磁和射频干扰。
易于实现自动化,提高生产效率。降低成本达30%~50%。 节省材料、能源、设备、人力、时间等。 电脑贴片机,如图
为什么要用SMT:
电子产品追求小型化,以前使用的穿孔插件元件已无法缩小
电子产品功能更完整,所采用的集成电路(IC)已无穿孔元件,特别是大规模、高集成IC,不得不采用表面贴片元件
产品批量化,生产自动化,厂方要以低成本高产量,出产优质产品以迎合顾客需求及加强市场竞争力
电子元件的发展,集成电路(IC)的开发,半导体材料的多元应用
电子科技革命势在必行,追逐国际潮流
SMT 基本工艺构成要素:
丝印(或点胶)-->贴装 -->(固化) -->回流焊接 -->清洗 -->检测 -->返修
丝印:其作用是将焊膏或贴片胶漏印到PCB的焊盘上,为元器件的焊接做准备。所用设备为丝印机(丝网印刷机),位于SMT生产线的最前端。
点胶:它是将胶水滴到PCB的的固定位置上,其主要作用是将元器件固定到PCB板上。所用设备为点胶机,位于SMT生产线的最前端或检测设备的后
面。
贴装:其作用是将表面组装元器件准确安装到PCB的固定位置上。所用设备为贴片机,位于SMT生产线中丝印机的后面。
固化:其作用是将贴片胶融化,从而使表面组装元器件与PCB板牢固粘接在一起。所用设备为固化炉,位于SMT生产线中贴片机的后面。
回流焊接:其作用是将焊膏融化,使表面组装元器件与PCB板牢固粘接在一起。所用设备为回流焊炉,位于SMT生产线中贴片机的后面。
清洗:其作用是将组装好的PCB板上面的对人体有害的焊接残留物如助焊剂等除去。所用设备为清洗机,位置可以不固定,可以在线,也可不在线。
检测:其作用是对组装好的PCB板进行焊接质量和装配质量的检测。所用设备有放大镜、显微镜、在线测试仪(ICT)、飞针测试仪、自动光学检测
(AOI)、X-RAY检测系统、功能测试仪等。位置根据检测的需要,可以配置在生产线合适的地方。
返修:其作用是对检测出现故障的PCB板进行返工。所用工具为烙铁、返修工作站等。配置在生产线中任意位置。
SMT常用知识简介
一般来说,SMT车间规定的温度为25±3℃。
2.锡膏印刷时,所需准备的材料及工具锡膏、钢板、刮刀、擦拭纸、无尘纸、清洗剂、搅拌刀。
3.一般常用的锡膏合金成份为Sn/Pb合金,且合金比例为63/37。
4.锡膏中主要成份分为两大部分锡粉和助焊剂。 5.助焊剂在焊接中的主要作用是去除氧化物、破坏融锡表面张力、防止再度氧化。
6.锡膏中锡粉颗粒与Flux(助焊剂)的体积之比约为1:1, 重量之比约为9:1。
7.锡膏的取用原则是先进先出。
8.锡膏在开封使用时,须经过两个重要的过程回温、搅拌。
9.钢板常见的制作方法为:蚀刻、激光、电铸。
10.SMT的全称是Surface mount(或mounting) technology,中文意思为表面粘着(或贴装)技术。
11.ESD的全称是Electro-static discharge, 中文意思为静电放电。
12.制作SMT设备程序时, 程序中包括五大部分, 此五部分为PCB data; Mark data; Feeder data; Nozzle data; Part data。
13.无铅焊锡Sn/Ag/Cu 96.5/3.0/0.5的熔点为 217C。
14.零件干燥箱的管制相对温湿度为
15.常用的被动元器件(Paive
Devices)有:电阻、电容、点感(或二极体)等;主动元器件(Active Devices)有:电晶体、IC等。
16.常用的SMT钢板的材质为不锈钢。
17.常用的SMT钢板的厚度为0.15mm(或0.12mm)。
18.
静电电荷产生的种类有摩擦、分离、感应、静电传导等;静电电荷对电子工业的影响为:ESD失效、静电污染;静电消除的三种原理为静电中和、接地、屏蔽。
19.英制尺寸长x宽0603=
0.06inch*0.03inch,公制尺寸长x宽3216=3.2mm*1.6mm。
20.排阻ERB-05604-J81第8码“4”表示为4
个回路,阻值为56欧姆。电容ECA-0105Y-M31容值为C=106PF=1NF =1X10-6F。
21.ECN中文全称为:工程变更通知单;SWR中文全称为:特殊需求工作单,必须由各相关部门会签, 文件中心分发, 方为有效。
22.5S的具体内容为整理、整顿、清扫、清洁、素养。
23.PCB真空包装的目的是防尘及防潮。
24.品质政策为:全面品管、贯彻制度、提供客户需求的品质;全员参与、及时处理、以达成零缺点的目标。
25.品质三不政策为:不接受不良品、不制造不良品、不流出不良品。
26.QC七大手法中鱼骨查原因中4M1H分别是指(中文): 人、机器、物料、方法、环境。
27.
锡膏的成份包含:金属粉末、溶济、助焊剂、抗垂流剂、活性剂;按重量分,金属粉末占85-92%,按体积分金属粉末占50%;其中金属粉末主要成份为锡和铅, 比例为63/37,熔点为183℃。
28.锡膏使用时必须从冰箱中取出回温,
目的是:让冷藏的锡膏温度回复常温,以利印刷。如果不回温则在PCBA进Reflow后易产生的不良为锡珠。
29.机器之文件供给模式有:准备模式、优先交换模式、交换模式和速接模式。
30.SMT的PCB定位方式有:真空定位、机械孔定位、双边夹定位及板边定位。
31.丝印(符号)为272的电阻,阻值为 2700Ω,阻值为4.8MΩ的电阻的符号(丝印)为485。 32.BGA本体上的丝印包含厂商、厂商料号、规格和Datecode/(Lot No)等信息。
33.208pinQFP的pitch为0.5mm。
34.QC七大手法中, 鱼骨图强调寻找因果关系; 35.CPK指: 目前实际状况下的制程能力; 36.助焊剂在恒温区开始挥发进行化学清洗动作; 37.理想的冷却区曲线和回流区曲线镜像关系; 38.Sn62Pb36Ag2之焊锡膏主要试用于陶瓷板;
39.以松香为主的助焊剂可分四种: R、RA、RSA、RMA; 40.RSS曲线为升温→恒温→回流→冷却曲线; 41.我们现使用的PCB材质为FR-4; 42.PCB翘曲规格不超过其对角线的0.7%; 43.STENCIL制作激光切割是可以再重工的方法; 44.目前计算机主板上常用的BGA球径为0.76mm; 45.ABS系统为绝对坐标;
46.陶瓷芯片电容ECA-0105Y-K31误差为±10%; 47.目前使用的计算机的PCB, 其材质为: 玻纤板; 48.SMT零件包装其卷带式盘直径为13寸、7寸;
49.SMT一般钢板开孔要比PCB PAD小4um可以防止锡球不良之现象; 50.按照《PCBA检验规范》当二面角>90度时表示锡膏与波焊体无附着性; 51.IC拆包后湿度显示卡上湿度在大于30%的情况下表示IC受潮且吸湿; 52.锡膏成份中锡粉与助焊剂的重量比和体积比正确的是90%:10% ,50%:50%; 53.早期之表面粘装技术源自于20世纪60年代中期之军用及航空电子领域; 54.目前SMT最常使用的焊锡膏Sn和Pb的含量各为: 63Sn+37Pb; 55.常见的带宽为8mm的纸带料盘送料间距为4mm;
56.在20世纪70年代早期,业界中新出现一种SMD, 为“密封式无脚芯片载体”, 常以HCC简代之; 57.符号为272之组件的阻值应为2.7K欧姆; 58.100NF组件的容值与0.10uf相同; 59.63Sn+37Pb之共晶点为183℃; 60.SMT使用量最大的电子零件材质是陶瓷; 61.回焊炉温度曲线其曲线最高温度215C最适宜; 62.锡炉检验时,锡炉的温度245℃较合适;
63.钢板的开孔型式方形、三角形、圆形,星形,本磊形; 64.SMT段排阻有无方向性无;
65.目前市面上售之锡膏,实际只有4小时的粘性时间; 66.SMT设备一般使用之额定气压为5KG/cm2;
67.SMT零件维修的工具有:烙铁、热风拔取器、吸锡枪、镊子; 68.QC分为:IQC、IPQC、.FQC、OQC; 69.高速贴片机可贴装电阻、电容、IC、晶体管; 70.静电的特点:小电流、受湿度影响较大;
71.正面PTH, 反面SMT过锡炉时使用何种焊接方式扰流双波焊; 72.SMT常见之检验方法: 目视检验、X光检验、机器视觉检验
73.铬铁修理零件热传导方式为传导+对流; 74.目前BGA材料其锡球的主要成Sn90 Pb10; 75.钢板的制作方法雷射切割、电铸法、化学蚀刻; 76.迥焊炉的温度按: 利用测温器量出适用之温度;
77.迥焊炉之SMT半成品于出口时其焊接状况是零件固定于PCB上; 78.现代质量管理发展的历程TQC-TQA-TQM; 79.ICT测试是针床测试;
80.ICT之测试能测电子零件采用静态测试;
81.焊锡特性是融点比其它金属低、物理性能满足焊接条件、低温时流动性比其它金属好; 82.迥焊炉零件更换制程条件变更要重新测量测度曲线; 83.西门子80F/S属于较电子式控制传动;
84.锡膏测厚仪是利用Laser光测: 锡膏度、锡膏厚度、锡膏印出之宽度; 85.SMT零件供料方式有振动式供料器、盘状供料器、卷带式供料器; 86.SMT设备运用哪些机构: 凸轮机构、边杆机构、螺杆机构、滑动机构; 87.目检段若无法确认则需依照何项作业BOM、厂商确认、样品板; 88.若零件包装方式为12w8P, 则计数器Pinth尺寸须调整每次进8mm; 89.迥焊机的种类: 热风式迥焊炉、氮气迥焊炉、laser迥焊炉、红外线迥焊炉; 90.SMT零件样品试作可采用的方法:流线式生产、手印机器贴装、手印手贴装; 91.常用的MARK形状有:圆形,“十”字形、正方形,菱形,三角形,万字形; 92.SMT段因Reflow Profile设置不当, 可能造成零件微裂的是预热区、冷却区; 93.SMT段零件两端受热不均匀易造成:空焊、偏位、墓碑; 94.高速机与泛用机的Cycle time应尽量均衡; 95.品质的真意就是第一次就做好; 96.贴片机应先贴小零件,后贴大零件;
97.BIOS是一种基本输入输出系统,全英文为:Base Input/Output System; 98.SMT零件依据零件脚有无可分为LEAD与LEADLESS两种;
99.常见的自动放置机有三种基本型态, 接续式放置型, 连续式放置型和大量移送式放置机; 100.SMT制程中没有LOADER也可以生产;
101.SMT流程是送板系统-锡膏印刷机-高速机-泛用机-迥流焊-收板机; 102.温湿度敏感零件开封时, 湿度卡圆圈内显示颜色为蓝色,零件方可使用; 103.尺寸规格20mm不是料带的宽度;
104.制程中因印刷不良造成短路的原因:a.锡膏金属含量不够,造成塌陷b. 钢板开孔过大,造成锡量过多c.钢板品质不佳,下锡不良,换激光切割模板d. Stencil背面残有锡膏,降低刮刀压力,采用适当的VACCUM和SOLVENT 105.
一般回焊炉Profile各区的主要工程目的:a.预热区;工程目的:锡膏中容剂挥发。b.均温区;工程目的:助焊剂活化,去除氧化物;蒸发多余水份。c.回焊区;工程目的:焊锡熔融。d.冷却区;工程目的:合金焊点形成,零件脚与焊盘接为一体;
106.SMT制程中,锡珠产生的主要原因:PCB
PAD设计不良、钢板开孔设计不良、置件深度或置件压力过大、Profile曲线上升斜率过大,锡膏坍塌、锡膏粘度过低。
第15篇:SMT岗位职责
SMT岗位职责
1.职位:拉长直属上司:生产主管直接下属:物料员
a.每天早会(生产情况,状态、注意事项)
b.车间纪律及“5S”执行。
c.产量及质量跟踪。
d.炉后品质管控。
e.员工培训及物料管控。
f.对员工报表完成情况进行监督。
2.职位:物料员直属上司:拉长
a.对出货产品数量核对,并送至仓库或相关区域摆放。
b.有接到仓库通知收料应拿BOM单和发料单核对用量,单量,收取物料,对物料的数量核对清楚,尤其贵重物料,(如二极管,三极管,IC等)
c.生产清尾时要提前帮操作员备好埋拉所用物料以便缩短清尾时间。 d.协助拉长搞好车间“5S”工作。
3.职位:技术员直属上司:工程主管直接下属:操作员
a.对机器设备各种保养作好记录。
b.对品质进行控制,有品质异常的及时向上级反映情况。
c.对新产品编程,转拉,协助IPQC核对物料。
d.对员工纪律管理和对其作业要求进行监督。
e.对员工技能不间断的进行培训。
4.职位:IPQC
a.对车间各报表监督完成情况(温湿度,静电手环测试记录,锡膏解冻时间,换料报表等)
b.对新转机产品首板确认,做好记录,每三小时核对一次样板。
c.对换料进行核对,有散料进行确认并在料带上签名确认。
d.车间“5S”和工艺流程进行监督。
e.对QC看好的板进行抽检(10/25),搞好自己工作周围的“5S”,抽检好的板放到相关区域标示清楚。
5.丝印员
a.对新上线产品提前将钢网安装在丝印台上。
b.按照锡膏,胶水作业指导书作业,拿出使用应给IPQC确认签名。(锡膏,胶水应解冻四小时)以上
c.对印刷出来的板自检,并往接驳台上放板。
d.对板数进行交接,搞好自己工作周围的“5S”,下班前将丝印钢网清洗干净。
6.操作员
a.每天四遍全检物料,上换物料应叫IPQC、拉长、技术员签名确认并在报表上作好记录。
b.保证机器工作正常,有故障及时排除或向技术员反映。
c.上料要使用接料的方法。
d.及时做好产量报表,并填写白板上。
e.清尾埋拉提前备好物料,以缩短埋拉所用时间。
f.搞好自己工作周围“5S”,尤其是机器上的灰尘,机器内部没有散料现象,对IC要进行交接。
g.严格控制物料,视物料如自已钱财。有抛料严重应及时叫技术员调机。对任何浪费物料的行为进行阻止,配合好物料员的工作。
7.炉前QC
a.对机器或手贴好的板进行检查有没有漏料少件、偏位、反向等不良现象。
b.若需手贴物料应依照样板手贴,注意方向,丝印是否符合要求,若有IC不可有短路移位等不良现象。
c.搞好自己工作周围的“5S”,注意防静电手环是否合格佩带是否正确。
d.对贵重物料做好交接记录,自己看好的板要做好记号以便区分。
8.过炉
a.首先要确认炉温是否是按要求调试的炉温,温度不清楚应叫技术员确认。
b.对炉前QC看好的板再进行检查主要检查有极性元件有没有反向,大元件是否有少件,移位等不良,放板过炉时按照作业指导书操作。
c.搞好自己工作周围的“5S”,保持炉面干净,整洁。
9.炉后QC
a.将炉子里面出来的板拿下来,不可让板直接落下来或撞到别的板上。
b.注意高温烫伤带好手套,静电环,将板插到卡板上,不可多块叠在一起。
c.按照从左到右或从右到左的顺序检查从炉里出来的板有没有假焊,短路,少件,立片等不良,若能自己修好则修,不敢确定或少料的贴上红色箭头纸送到修理处,看好的板做好记号。
d.按照标示或状态将看好的板放到相应位置待IPQC抽检。
e.注意工作周围的“5S”。
10.修理
a.将QC用箭头纸标示出来的坏机根据《修理作业指导书》作业,修好后做好自检确认QK后送到QC处重新检查,有需要洗板的用棉签蘸洗板水将要清洗的地方清洗干净。
b.修板时认真作业,注意工作周围的“5S”执行和防静电措施。
第16篇:SMT管理方式
SMT管理方式
作者:薛竞成文章来源:网络点击数:2482更新时间:2004-4-1
5SMT厂家不可忽视的管理方式
技术管理顾问薛竞成
我对国外SMT厂家的多年,发现在SMT应用上,他们有多项工作做得不足够,其中一项是制造过程的管理工作。早前,[电子工业]的主编和我谈到我以往系列文间提及的制程管理应用概念,相信国内厂家也会用得着。因而我特写本篇来谈谈这方面的概念。
制程管理,译自英文中的ProceManagement一词。由于我们把焦点放在SMT的制造技术上所以我把Proce译成(即制造过程)。其实ProceManage-ment所涵盖的范围更广。本广只就SMT制造有关的范围加以探讨。
从THT到SMT的管理需求变化
制程管理,并不是专为SMT而同设的。但要较成功的应用SMT这门技术,正确的推行有必要的。制程管理虽不是门新的管理技术,但它得人们认识、重视、有效应用并比SMT这门技术来早。也正为这原因,许多由THT(插件技术)提升SMT的厂家并没有意识到在管理上需要做改革的工作。在THT制造环境下,忽略制程管理并不会为制造商带来太大的问题;但对於SMT制造工作而言,尤其是进入微间距和采用现今BGA和倒装片(Flip-Chip)之类技术的情况下,制程管理是不可或缺的管理工具。
制程管理为何对SMT应用那么重要?回答这问题,们得了解THT和SMT之间存在许多不同的地方,尤以下下旬 几项最为显著:
1、微型化-SMT发展的动力,主要是突破旧有组装技术对产品微型化的限制。由于THT本身的技术局限,不断提升微型化的程度。
2、质量因素-THT和SMT两者的组装技术不大相同,影响质量的因素也大分别。虽然在许多方面,SMT组装质量已证实比THT更及更可靠,但SMT保证中工作比THT较为复杂。
3、自动化-SMT的发明变带来了高度的自动化,此亦是SMT生产效率比THT更高的原因。
以上三点所带出的信息是:SMT成品检查不易进行;成品寿命或可靠性的变化幅度大;制程工艺对成品的质量影响日益深刻;返修成本和代价高;即时诊断和改正生产误差的重要性提高等等。而这些对制造商不利的因素正是需要制造管理来解决。
在THT制造管理的环境下,人们并不注重制程功能(Proce Capability)、制程整合(Proce Integration)等的应用和管理。一般做法是在试产时把设备调校到配合绝大部分的组装工作,当达到相当的合格率后就接入正式生产。及后,在生产线上设立了因定的检查站,把发现的不良品抽出返修 。本文为了方便解说,把以往这种简单的制造-检查-返修或淘汰的-贯做法
称为‘制造管理’,有以区别本文提倡的’制程管理’,用以区别本文提倡的‘制程管理’。’制造管理’注重防止不良产品离厂,而‘制程管理’则把重点放在把制造方法加以合理化和优化(防止 不良产品出现是随这方法自然而来的)。‘制造管理’,在SMT生产中有以下几点不理想的地方:
1.不能照顾到成品寿命保证的问题;
2.生产效率难以达到最优化的状态,成本遂难以降低廉;
3.生产稳定性较差;
4.难以进行长期的改进;
5.由於组装基本变更和微型化,即使是同样的工作在SMT应用上也不易进行。
在市场对质量要求日益增高,对产品价格要求低,以及同行竞争日益增高,对产品价格要求低,以及同行竞争日益激烈的今天,如果厂商对上述问题仍坐视不理,继续沿习THT一贯的做法,不对生产管理加以改革,实在不是明智之举。
制程管理对SMT应用的帮助
制程管理方法如何避免或减低制造管理中如上述提到的那些问题呢?
首先制程管理在观念上有彻底而重要的改变、那就是不提倡检查,更不容忍错误发生。以往,制造管理相当大量的检查工序、检查活动,不论对成品的质量,或对生产的效率都有不良的影响。我们不难发现在许多工厂中,除非成品的不良率很高,否则一般如只有几个百份比的,在交货的压力下,都因检查-返修工作能应付而不加以追究。其实这方面的浪费,详细的计算也是相当可观的,在成本上一般绝非可以忽略的;而在质量学的观念上,任何返修工作都可能给成品质量添加了不稳定的因素。
但这可能还是其次,对SMT成品寿命或可靠进行研究都会了解到,成品寿命和可靠性是不能从一般的生产检查中得到任何住处,加以分析就能获得。视程度而定,不良品的出现,很有可能是产能或制程能力(Proce Capability)不足的一种表现。如果生产线的制程界限(Proce Window)不能配合成品的设计要求,头号题就不是只出现不良品和浪费资源那么简单了。在不良(或不够好)的制程下生产的成品,具有寿命代名词危险性,但不是所有的缺陷都能在生产线上的检查工序中被发现的。这就解释了一些成品在用户使用不久后便失效的原因。我想大家都能想象这类情况对公司或品牌的影响,这才是真正的危机所在。虽然目前仍没有十全十美的寿命保证生产方法,但制程管理在这方面的处理,通过其设计、调制、监控、改进四大步骤,在效益上较制造管理方法大大的提高了。
由于较缺乏制程管理中的调制管理以及灵活而深入的监控 工作、制造管理下的生产能力的稳定性一般都较差。而这也是对优化和改进发展的一大事故,和在好些方面都处于难以突破的局面。制程管理中对制程能力的制定和应用有较严格的管制,而稳定性是制定制程必须考虑到的因素,并且是首要的工作之一。对生产能力有了实在的了解和稳定的控制后,改进和
优化工作才能接着进行。
在了解制程管理和制程管理的过程中,也带来了设备的配置、改进设计的学问和全面改进的好处。由于制程管理中重要的一节是制程整合(Proce Inetegration),而在处理制程整合的工作中必须对设备技术和产品的生产设计有很好的了解和配合,这就要求技术人员在这些方面进行学习、研究、了解和应用。而此做法也正好迎合SMT对技术整合的依赖性。也只有通过对这些全面的学习应用,才能达到长期的改进,才能作出最优化、最低成本的生产作业。
另一个制造管理日益难以应付的问题是SMTR 快速微型化。微间距IC、0402和0201矩形件、微型BGA、Flip-Chip等的出现已对检查工作造成不便,甚至带来了不实用的压力。但如果我们在这问题上作根本的考虑,问题其实也不怎么存在。检查作业是项没有附加价值的工作,为会么我们在生产过程中需要检查?这便是因为生产能力 稳定性不足面不能有足够信心确保成品质量的。其实如上面所提到的,检查作业并不能最有效的确保寿命和质量(甚至误导而使我们相信成品具备足够的寿命)。既然检查作业是花费而又不完整的工作,那是否有更好的做法呢?制程管理就是个可能的代替方法。在成熟的技术上、良好的制程管是有可能废除某些检查作业的。虽然我们知道不会有十全十美,但如果通过制程管理而在某一工序上能达到制程能力掼标(ProceCapability)为2以上时,你是否还需要检查作业?我们一直沿用的检查作业,很多时候是因为没有学习和使用制程管理法,而不是毫无选择的做法。
制程管理,是一门先质后量的管理。在未能保证品质的情况下提高产量,只会造成浪费和损失(材料、时间、设备使用、能源的浪费和公司名誉上的损失)。乍看之下,采用制程管理似乎会带来生产投入较慢、交货期较不理想的问题。其实这情况只有在学习的阶段会出现。一个成熟的制程管理系统,在生产接入的时间上是能很快速的。而当投入生产后,其在免除浪费上所回收的利益,却是制造管理所望尘莫及。所以真正的制程管理是项质、量兼收,稳定优化的管理方式。
什么是制程管理
制程管理,好些工厂把它当作只是工序的制定和执行。此所以许多工厂管理都以为本身有采用这方面的管理;其实真正有用的市 程管理远较此复杂。它包括了四大主要部分:制程设计、制程调制设定、制程监控、制程改进。其中制程监控又可细分为监督和控制两部分。以上这些都必须完整的包含在整个制程管理的活动中,缺乏任何一项都不能算是推行制程管理。此外,制程管理并不是独立运作的一门管理技术。它也必须配合产品设计、设备技术和质量水平要求来进行。让我们来看看它们之间的关系。制程设计,这里所指的不只是制造过程的工序(如锡膏印刷),还包括工序中所需的工艺参数(如刮刀压力、速度、模板分离参数、印刷间隔等等)的订立。这工作在新的管理应用中是和产品设计同步进行的、通过使用并行工程(ConcurrentEngineering)概念和做法来实现。制程设计受限于现有设备的特性、功能以及厂内对品质的要求,所以必须制定设备在这方面的极限值,而后加以配合来设计。如果一家工厂拥有好些不同档次的设备,则管理上须牺牲某些较好的制程能力,或采用较复杂的生产管理安排。制程设计是整个制程管理中至关重要而相当复杂 的一步。要求技术人员对工艺、设备、设计有很好的认识,以及部门间良好的沟通。由于制程设计受限于设备,对初次使用SMT的用户来说在处理上就有和现有SMT设备的用户不同的地方。这点读者须留意。
制程调制设定,是如何将制程设计的结果应用在生产线上的工作。这要求技术人员对设备的特性、功能以及如何操作有很好的了解。设计未必能一次完整无缺的把所有制程参数都定得最优最完善,这阶段工作也具微调改正的责任。同时,这阶段工作也对调制后的制程能力做计量,并初步检讨制程设计时定下的监控方法。以作为全面生产时开始的制程监控参照。也是设备保养维修部门日后技术目标的参照。
制程监控,是确保生产效益的和质量的重要活动。由于生产线上的变数很多,设备、人员、材料等等都有其各自许多变数,每天在不同程度上的互相影响,互相牵制着。如何能采取有效足够的监控又不会影响生产以及提高生产成本,是一项不易做得好的工作。另一和制造管理很不同之处,是真正制程管理注重于不良品的预防,而制造管理则流于对不良品进行返修改正。在制程管理方面,要求员工具备良好的测量知识、统计学知识、因果分析能力、以及对设备性功能的深入了解等等。
制程改进,也是制程管理技术优于制造管理技术的重要之一。制造管理,在生产演化的路程上进展太慢,甚至相对工发展来说是在退步。制程管理。由于通过较科学性的管理,由於不断的在收集生产资料、分析生产资料,以及注重包括设计在内的全程整合处理,对生产和选题的改进提供了十分有利的条件。有了这方面的活动、制程管理不单给工厂带来生产效率和质量,也同时带来不断往前改进的工具。
制程管理的应用,不应只停留在厂内。很多时候SMT工厂所处理的工作,只是限于电路板的组装(如组装加工厂),或由电路板的组装开始,到完整产品如电脑、VCD等。在这情况下,工厂所能控制的,也只是由原材料如元件的进货处理开始。但我们都知道,成品的寿命和质量包括了各元件的质量,厂内进行的组装质量也受元件质量的影响。其实在我的工作中就发现元件如基板等常是影响生产质量的主要问题之一。所以,在步向零缺陷的目标路程中,我们必须通过交流合作把制程管理推广到元件供应商处。这方面的工作当然自己厂内的更难执行,但却是应该努力的。
你还需要什么?
在制程管理中有一关键性环节,就是组织上应采或混合采用矩阵组织结构(MatrixOrganization),这是制程有效与否相当依赖整体制程的关联性处理能力的缘帮。因此在厂内的组织上必须要有一个或一组能应付这类需求的人员(请参考上几期‘中国SMT厂家最解决的是什么问题?’的系列文章)。制程管理是一种管理方法,它并不会自动生效,所以你必须在执行时同时借助技术方法如工艺技术、设备技术等知识的支援,方能见效。没有这些方面的知识,低温 不可能的把制程管理应用得好的。
结语
在今天SMT市场中要确保竞争中,采用制程管理法是不可或缺的。国内许多SMT用户还未了解这门管理,遑论加以应用。这对眼光正确和行动迅速管理者是一个领先竞争对手的大好机会。
由于采用制程管理的优点,加以业内已存在拥有这方面知识经验者,尚欠的只是SMT用
户是否意识其重要性,因此SMT业界采用制造管理只是时间的问题而已。但有一点可以肯定的,今日不行动就不能把握同伴的机会,他日可还落得为了不被淘汰而挣扎求存的境况。希望本文能让读者认识到为什么制程管理对SMT是那么重要,并把握国内目前正处发展情况的机会,立即开始进行改革工作。
第17篇:SMT报告
报 告
一、技能方面
我主要负责SMT品质,从刚开始接触贴片换料时的经常出错,到现在能够熟练操作并且错误发生率明显下降,从对产品的一知半解,到熟悉作业流程和客户需求的品质,这期间让我学习到了不少知识,但同时也感受到伴随而来的压力,当然,有压力才有动力。
二、质量方面
经过一年多的时间,技能的熟悉。起初,对生产质量的控制不到位,也导致较多不良品的产生,但我知道,产品品质就是公司的命脉,针对品质出现的问题,进行原因分析,对质量薄弱环节进行改善.跟踪.验证,不良率不断下降,产品品质呈上升趋势。
三、人员方面
新老员工不断交替,人员流动性比较大,这给品质工作带来较大的困难,如何控制不良品的产生,成了车间的最大困难。包括新员工的入职培训、物料员如何配料、操作员在转线应注意哪些问题……慢慢地,随着人员技能的熟练,操作手法的规范,生产质量才能得到稳步的提升。
四、工作计划 随着旺季的到来,新的希望与挑战翻开崭新的一页,如何在以后的工作中取得更好的成绩是今年最大的目标,
1、培训工作。加强作业员与物料员之间的沟通,培养每个员工应有的责任感和良好的行为习惯,提升作业员的工作技能。
2、提升执行力。坚持工作原则,凡是公司要求指定的任务、事项,就一定要不折不扣地执行下去,并且随时进行跟进、检查。
3、物料管理。严格要求物料员做到卡 料一致,应当每个月最少对仓库物料盘点一次,以便对物料、产品进行追溯。
最后,祝愿公司明天更加美好、辉煌!
报告人:罗靖
2012年02月21日
第18篇:SMT工艺
钢网:用来把锡膏印刷到PCB上。
锡膏:用来焊接元器件到PCB上,锡膏分分有种类,不同的公司做在板的时候,要求使用的锡膏是不同的。锡膏上面有条形码,在使用锡膏的时候,扫描条形码,就可以记录这条生产线使用的是哪种类型的锡膏,方便以后做调查。
贴片机:根据PCB板的横纵坐标,找到每个元器件所需要放置的位置,通过吸嘴吸取元件,粘贴到正确位置的锡膏上。
流程:
PCB装框——自动进板——自动印刷——检测印刷锡膏是否符合规格——PCB贴片——检测贴片是否符合规格——过炉固化——检查焊接效果——拆板
注意事项
1、印刷员在PCB拆包前,需要先检查PCB 是否过期,数量是多少,是否受潮,是否变形等。
2、钢网在印刷一定数量PCB后,需要清洗,防止网口堵塞。
3、在印刷完成之后,必须有印刷检测点,专门用于检查锡膏印刷是否符合要求。根据影像投射的原理,横纵坐标逐步扫描对比每个点锡膏印刷情况,把扫描的情况和正确的印刷板做对比,通过计算相似度得出印刷是否符合规格。
4、贴片机在贴片的时候,需要先贴小的元器件,再贴大的元器件。因为这样可以防止大的元器件阻碍吸嘴贴小的元器件。
5、贴完所有体积小的元器件之后,需要对整个板子做影像分析,把现在正在加工的板子和已经正确加工的板子作对比,通过图像处理,分析出两张图片的相似度,进一步判断贴片是否准确。
6、做完贴片后的影像分析后,再贴大个元器件,大个的元器件贴片完毕,我们只需要通过员工观察板子贴片情况是否合格就可以过炉固化了。因为贴大哥元器件体积较大,员工肉眼就可以判断他们是否粘贴合格。
7、印刷锡膏不合格的板子,需要重新清洗板子,然后进行再次印刷。
8、贴片不合格的板子,需要取下元器件,清洗锡膏,再重新印刷贴片。
9、印刷和贴片合格率过低的时候,应及时向工程师汇报,让工程师重新设定参数。
第19篇:SMT 检讨书
检讨书
尊敬的领导:
您好!感谢您在百忙之中抽空看我写的检讨书!我在此为我在11月25日上错料做如下检讨:
我不想再为自己的错误找任何借口,那只能让我更加惭愧。这份检讨书,向您表示我对这种错误行为的深痛恶绝,我下定决心,不再 犯类似错误。其时,领导反复教导言犹在耳,严肃认真的表情犹在眼前,我深为震撼,也已经深刻认识到此事的重要性,于是我一再告诉自己要把此事当成头等大事来抓,不能辜负领导和同事对我的一片苦心。 自己并没有好好的去考虑我现在的责任,造成了工作的失误。
通过这件事,我感到虽然是一件偶然发生的事情,但同时也是长期以来对自己放松了要求,工作做风涣散的必然结果,也是与我们时代要求-----树新风,讲文明,背道而行。经过几天的反思,我对自己这些年的工作成长经历进行了详细回忆和分析。记得刚上班的时候,我对自己的要求还是比较高的,时时处处也都能遵守相关规章制度,从而努力完成各项工作。但近期,由于工作逐渐走上了轨道,而自己对公司的一切也比较熟悉了,尤其是领导对我的关怀和帮助使我感到温暖的同时,也慢慢开始放松了对自己的要求,反而认为自己已经做得很好了。因此,这次发生的事使我不仅感到是自己的耻辱,更为重要的是我感到对不起领导对我的信任,愧对领导的关心。
如今,大错既成,我深深懊悔不已,深刻检讨。本人思想中的致命错误有以下几点:
思想觉悟不高,对重要事项认识严重不足。就算是有认识,也没能在行动上真正实行起来。
思想觉悟不高的根本原因是因为本人对待工作的思想观念不够深刻、不够负责。
我决定做出如下整改:
1、对自己思想上的错误根源进行深挖细找,并认清其可能造成的严重后果。
2、认真克服生活懒散、粗心大意的缺点,努力将工作做好,以优秀的表现来弥补我的过错。
3、经常和同事加强沟通,保证不再出现类似错误。
此外,我也看到了这件事的恶劣影响,如果在工作中,大家都像我一样自由散漫,漫不经心,那怎么能及时把工作落实好、做好呢?同时,如果在我们这个集体中形成了这种目无组织纪律观念,不良风气、不文明表现,我们工作的提高将无从谈起,服务也只是纸上谈兵。因此,这件事的后果是严重的,影响是恶劣的。
短短几百字,不能表述我对自己的谴责;更多的责骂,深藏在我的心理。盼望领导能给我改过自新的机会。如果公司能给我改过的机会,我会化悔恨为力量,我绝不在同一地方摔倒,以后我要努力工作,认真负责,争取为公司的发展做出更大的贡献。
在这件事中,我还感到,自己在工作责任心上仍就非常欠缺。这充分说明,我从思想上没有把工作的方式方法重视起来,这也说明,我对自己的工作没有足够的责任心,也没有把自己的工作做得更好,也没给自己注入走上新台阶的思想动力。在自己的思想中,仍就存在得过且过,混日子的应付思想。现在,我深深感到,这是一个非常危险的倾向,也是一个极其不好的苗头,如果而放任自己继续放纵和发展,那么,后果是极其严重的,甚至都无法想象会发生怎样的工作失误。因此,通过这件事,在深感痛心的同时,我也感到了幸运,感到了自己觉醒的及时,这在我今后的人生成长道路上,无疑是一次关键的转折。在此,我向领导做出深刻的检讨。
发生这件事后,我知道无论怎样都不足以弥补自己的过错。因此,无论领导怎样从严从重处分我,我都不会有任何意见。在此次错误中损失的物料我愿意由我个人承担。同时,我请求领导再给我一次机会,使我可以通过自己的行动来表示自己的觉醒,以加倍努力的工作来为公司做出积极的贡献,请领导相信我。
检讨人:易晓安
时间:2012年12月14
第20篇:smt返修
SMT成功返修的关键工艺
再流之前适当预热PCB板;再流之后迅速冷却焊点。对于成功返修SMT起帮助作用的两个最关键工艺,也是两个最容易引起忽视的问题:
由于这两个根本工艺经常为返修技术人员所忽视,事实上,有时返修后比返修之前的状况更糟糕。尽管有些“返修”缺陷有时能被后道工序检验员所发现,但多数情况下总是看不出来,但在以后电路试验中马上会暴露出来。
预热——成功返修的前提
诚然,PCB长时间地在高温(315-426℃)下加工会带来很多潜在的问题。热损坏,如焊盘和引线翘曲,基板脱层,生白斑或起泡,变色。板翘和被烧通常都会引起检验员注意。但是,正是因为不会“烧坏板”并不等于说“板未受损坏”。高温对PCB的“无形”损害甚至比上述所列问题更加严重。几十年来,无数次试验反复证明PCB及其元件能“通过”返工后的检验和试验,其衰减速度比正常PCB板高。这种基板内部翘曲和其电路元件衰减等“隐形”问题来自于不同材料不同的膨胀系数。显然,这些问题不会自我暴露,甚至在开始电路试验时也未被发现,但仍潜伏在PCB组件中。
尽管“返修”后看上去很好,但就象人们常说的一句话:“手术成功了,可病人不幸死去”。 巨大热应力的产生原因,常温下(21℃)的PCB组件突然接触热源为约370℃的烙铁、去焊工具或热风头进行局部加热时,对电路板及其元器件有约349℃的温差变化, 产生”爆米花”现象。
“爆米花”现象是指存在于一块集成电路或SMD在器件内部的湿气在返修过程中迅速受热, 使湿气膨胀, 出现微型爆裂或破裂的现象。因此,半导体工业和电路板制造业要求生产人员在再流之前, 尽量缩短预热时间, 迅速升到再流温度。事实上PCB组件再流工艺中已经包括再流前的预热阶段。无论PCB装配厂是采用波峰焊,红外汽相或对流再流焊,每种方法一般均要进行预热或保温处理,温度一般在140-160℃。在实施再流焊之前,利用简单的短期预热PCB就能解决返修时的许多问题。这在再流焊工艺中已有数年成功的历史了。因此, PCB组件在再流前进行预热的好处是多方面的。
由于板的预热会降低再流温度, 所以波峰焊、IR/汽相焊和对流再流焊均可以在大约260℃左右下进行焊接的。
预热的好处是多方面的和综合的
首先,在开始再流之前预热或“保温处理”组件有助于活化焊剂,去除待焊接金属表面的氧化物和表面膜,以及焊剂本身的挥发物。相应地,就在再流之前活化焊剂的这种清洗会增强润湿效果。预热是将整个组件加热到低于焊料的熔点和再流焊的温度。这样可大大地降低对基板及其元器件的热冲击的危险性。否则快速加热将增加组件内温度梯度而产生热冲击。组件内部所产生的大的温度梯度将形成热机械应力,引起这些低热膨胀率的材料脆化,产生破裂和损坏。SMT片式电阻器和电容器特别容易受到热冲击的伤害。
此外,如果整个组件进行预热,可降低再流温度和缩短再流时间。如果没有预热,唯一办法只能进一步升高再流温度,或延长再流时间,无论哪一个办法都不太合适,应该避免。
减少返修使电路板更可靠
作为焊接温度的一个基准,采用的焊接方式不同, 焊接温度也不一样, 譬如: 多数波峰焊温度约在240-260℃,汽相焊温度约在215℃,再流焊温度约为230℃。正确地讲,返工温度不高于再流焊温度。尽管温度接近,但决不可能达到一样的温度。这是因为:即所有返修过程只需要对一个局部元器件采取加温,而再流需要对整个PCB组件进行加温,无论是波峰焊IR和汽相再流焊均如此。
同样限制返工中降低再流温度的另一个因素是工业标准的要求,即要返修点周围的元器件所处温度决不能超过170℃。所以,返修中再流温度应与PCB组件本身和要再流的元器件尺寸的大小相适应,由于本质上是PCB板的局部返修,所以返修工艺限制了PCB板的维修温度。局部化返修的加热范围比生产工艺中的温度更高一些,以抵消整个电路板组件的吸热。
这么说来,仍没有充分理由说明整块板的返修温度不能高于生产工艺中的再流焊温度,从而接近半导体制造厂所推荐的目标温度。
返修前或返修中PCB组件预热的三个方法:
如今,预热PCB组件方法分为三类:烘箱、热板和热风槽。在返修和进行再流焊拆卸元器件之前使用烘箱来预热基板,是行之有效的。而且,预热烘箱在烘烤掉某些集成电路中内部湿气和防止爆米花现象上,采用烘烤是一个有利方法。所谓爆米花现象是指返修的SMD器件在湿度上高于正常器件的湿度在突然受到快速升温时会发生的微崩裂。PCB在预热烘箱中的烘烤时间较长, 一般长达8小时左右。
预热烘箱的一个缺陷是不同于热板和热风槽,预热时由一个技术员进行预热和兼同时返修是行不通的。而且,对烘箱来讲做到迅速冷却焊点是不可能的。
热板是预热PCB板最无效的办法。因为要维修的PCB组件不全是单面的, 当今是混合技术的世界,一面全部是平整或平面的PCB组件的确是少见的。PCB在基板两边一般都要安装元器件。这些不平整的表面采用热板预热是不可能的。
热板的第二个缺陷是一旦实现焊料再流,热板仍会持续对PCB组件释放热量。这是因为,即使拔掉电源之后,热板内仍会有储存的残余热量继续传导给PCB阻碍了焊点的冷却速度。这种阻碍焊点冷却会引起不必要的铅的析出形成铅液池,使焊点强度降低和变差。
采用热风槽预热的优点是: 热风槽完全不考虑PCB组件的外形(和底部结构),热风能直接迅速地进入PCB组件的所有角落和裂缝中。使整个PCB组件加热均匀, 且缩短了加热时间。 PCB组件中焊点的二次冷却
如前所述,SMT对PCBA(印制板组件)返修的挑战在于返修工艺应该模仿生产的工艺。事实证明: 第一,在再流前预热PCB组件是成功生产PCBA所必需的;第二,再流之后立即迅速冷却组件也是很重要的。而这两个简单工艺一直被人们所忽视。但是,在通孔技术以及敏感元件的微型焊接中,预热和二次冷却更显得重要。
常见的再流设备如链式炉,PCB组件通过再流区后立即进入冷却区。随着PCB组件进入冷却区,为达到快速冷却, 对PCB组件通风是很重要的,一般返修与生产设备本身是结为一体的。
PCB组件再流之后放慢冷却会使液体焊料中的不需要的富铅液池产生会使焊点强度降低。然而,利用快速冷却能阻止铅的析出,使晶粒结构更紧,焊点更牢固。
此外,更快地冷却焊点会减少PCB组件在再流时由于意外移动或振动而产生一系列的质量问题。对于生产和返修,减少小型SMD可能存在的错位和墓碑现象是二次冷却PCB组件的另一优点。
总结
正确预热和再流时的二次冷却PCB组件的好处有很多,需要把这两种简单程序纳入技术人员的返修工作中。事实上,预热PCB时,技术员可以同时做其它准备工作,如在PCB板上涂焊膏和焊剂。
当然,需要解决新返修的PCB组件工艺问题,因为它还未通过电路试验,这也是一种真正的节约时间。显然,不必将在返修中造成PCB报废而节约了成本,一分预防抵得十二分治疗。
相应地,可减少因基板脱层,生斑点或气泡,翘曲,褪色和过早硫化而消除过多的废品。正确使用预热和二次冷却是PCB组件两个最简单,且最必要的返修工艺。
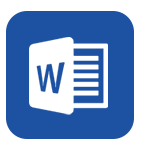