大连交通大学信息工程学院2012届本科生毕业设计(论文)实习(调研)报告
调研报告
1 组合机床简介
1.1 组合机床的定义及作用
组合机床是以通用部件为基础,配以按工件特定形状和加工工艺设计的专用部件和夹具,组成的半自动或自动专用机床。现代社会中,人们为了高效、经济地生产各种高质量产品,日益广泛的使用各种机器、仪器和工具等技术设备与装备。为制造这些技术设备与装备,又必须具备各种加工金属零件的设备,诸如铸造、锻造、焊接、冲压和切削加工设备等。由于部分机械零件要求设计制造周期短,加工精度要求高,生产效率高,故往往需要在组合机床上去加工完成。因此,组合机床的设计制造在现代机械制造业具有举足轻重的地位。
1.2组合机床的特点及加工范围
组合机床一般采用多轴、多刀、多工序、多面或多工位同时加工的方式,生产效率比通用机床高几倍至几十倍。由于通用部件已经标准化和系列化,可根据需要灵活配置,能缩短设计和制造周期。因此,组合机床兼有低成本和高效率的优点,在大批、大量生产中得到广泛应用,并可用以组成自动生产线。
组合机床可用于加工箱体类或特殊形状的零件。加工时,工件一般不旋转,由刀具的旋转运动和刀具与工件的相对进给运动,来实现钻孔、扩孔、锪孔、铰孔、镗孔、铣削平面、切削内外螺纹以及加工外圆和端面等。有的组合机床采用车削头夹持工件使之旋转,由刀具作进给运动,也可实现某些回转体类零件(如飞轮、汽车后桥半轴等)的外圆和端面加工。
1.3 组合机床的产生及发展
最早的组合机床是1911年在美国制成的,用于加工汽车零件。初期,各机床制造厂都有各自的通用部件标准。为了提高不同制造厂的通用部件的互换性,便于用户使用和维修,1953年美国福特汽车公司和通用汽车公司与美国机床制造厂协商,确定了组合机床通用部件标准化的原则,即严格规定各部件间的联系尺寸,但对部件结构未作规定。
在我国,组合机床发展已有28年的历史,其科研和生产都具有相当的基础,应用也已深入到很多行业。是当前机械制造业实现产品更新,进行技术改造,提高生产效率和高速发展必不可少的设备之一。
二十世纪70年代以来,随着可转位刀具、密齿铣刀、镗孔尺寸自动检测和刀具自动补偿技术的发展,组合机床的加工精度也有所提高。铣削平面的平面度可达0.05毫 1
米/1000毫米,表面粗糙度可低达2.5~0.63微米;镗孔精度可达IT7~6级,孔距精度可达0.03~0.02微米。
在70年代,数控系统的可靠性有了很大的提高,故到70年代末和80年代初,像Alfing、Hüller-Hille 和Ex-cell-o等公司相继开发出数控加工模块和柔性自动线(FTL),从此数控组合机床和柔性自动线逐年增多。在 1988年至1992年间,日本组合机床和自动线(包括部分其它形式的专用机床)产量的数控化率已达32%~39%,产值数控比率达35%~51%;德国组合机床和自动线产量的数控化率为18%~62%,产值数控化率达45%~66%。这些数字表明,近十年来,组合机床的数控化发展是十分迅速的。
现代组合机床和自动线作为机电一体化产品,它是控制、驱动、测量、监控、刀具和机械组件等技术的综合反映。这些技术有长足进步,同时作为组合机床主要用户的汽车和内燃机等行业也有很大的变化,其产品市场寿命不断缩短,品种日益增多且质量不断提高。这些因素有力地推动和激励了组合机床和自动线技术的不断发展。近20年来,组合机床自动线技术取得了长足进步,自动线在加工精度、生产效率、利用率、柔性化和综合自动化等方面的巨大进步,标志着组合机床自动线技术发展达到的高水平。自动线的技术发展,刀具、控制和其它相关技术的进步以及用户需求变化起着重要的推动作用,其中,特别是CNC控制技术对自动线结构的变革及其柔性化起着决定性作用。
1.4 组合机床的未来发展趋势
目前,在验收组合机床时,已普遍要求设备的工序能力系数要大于1.33,有的甚至要求工序能力系数要大于1.67,以便确保稳定的加工精度。应指出,采用Cp≥1.33来验收设备,这实际上是加严了工件的制造公差,即工件的实际加工公差仅为工件给定公差的1/3~1/2(图13),这无疑是对组合机床提出了更高的要求。组合机床制造厂为了满足用户对工件加工精度的高要求,除了进一步提高主轴部件、镗杆、夹具(包括镗模)的精度,采用新的专用刀具,优化切削工艺过程,采用刀具尺寸测量控制系统和控制机床及工件的热变形等一系列措施外。空心工具锥柄(HSK)和过程统计质量控制(SPC)的应用已成为自动线提高和监控加工精度的新的重要技术手段。
组合机床未来的发展将更多的采用调速电动机和滚珠丝杠等传动,以简化结构、缩短生产节拍;采用数字控制系统和主轴箱、夹具自动更换系统,以提高工艺可调性;以及纳入柔性制造系统等。组合机床的柔性化主要是通过采用数控技术来实现的。开发柔性组合机床和柔性自动线的重要前提是开发数控加工模块,而有着较长发展历史的加工中心技术为开发数控加工模块提供了成熟的经验。由数控加工模块组成的柔性组合机床和柔性自动线,可通过应用和改变数控程序来实现自动换刀,自动更换多轴箱和改变加工行程、工作循环、切削参数以及加工位置等,以适应变型品种的加工。作为组合机床重要用户汽车工业,为迎合人们个性化需求,汽车变型品种日益增多,以多品种展开竞争已成为汽车市场竞争的特点之一,这使组合机床制造业面临着变型多品种生产的挑战。为适应多品种生产,传统以加工单一品种的刚性组合机床和自动线必须提高其柔性。
随着汽车市场竞争更趋激烈,产品市场寿命进一步缩短,新车型的开发周期日益缩短(目前一般为35个月),汽车品种不断增多,因而汽车工业对柔性自动化技术装备的需求量日益增多。如日本丰田汽车公司,在本世纪末的目标是公司下属工厂的柔性化加工系统的普及率达到100%。很显然,组合机床及其自动线在保持其高生产效率的条件下,进一步提高其柔性就愈来愈具有重要意义。
1.5组合机床的设计
组合机床设计需针对被加工零件的特点及工艺要求,按高度集中制的原则设计的一种高效率专用机。设计组合机床时,首先要根据组合机床完成工艺要求的一些限制及组合机床各种工艺方法能达到的加工精度、表面粗糙度及技术要求,解决零件是否可以利用组合机床加工以及采用组合机床加工是否合理的问题。如果确定可以利用组合机床加工,为使加工过程顺利进行,并能达到要求的生产效率,必须在握大量的零件加工工艺资料基础上,通盘考虑影响制定零件加工方案、机床配置形式、结构方案的各种因素及应注意的问题。经过分析比较,以确定零件在组合机床上合理可行的加工方法及组合机床的配置形式等等。
2 组合机床重要传动装置——变速箱
2.1变速箱的定义及组成
机床变速箱是机床中的重要传动装置,机床运行性能的好坏很大程度上决定于机床变速箱的传动性能。机床变速箱主要有变速传动机构和操纵机构组成,他将电动机和主轴联结起来,通过传动轴和齿轮以及其他传动件将电动机动力传递到主轴。可制成单独变速机构或与传动机构合装在同一壳体内。传动机构大多用普通齿轮传动,也有的用行星齿轮传动。普通齿轮传动变速机构一般用滑移齿轮和离合器等。滑移齿轮有多联滑移齿轮和变位滑移齿轮之分。用三联滑移齿轮变速,轴向尺寸大;用变位滑移齿轮变速 ,结构紧凑 ,但传动比变化小。离合器有啮合式和摩擦式之分。用啮合式离合器时,变速应在停车或转速差很小时进行,用摩擦式离合器可在运转中任意转速差时进行变速,但承载能力小,且不能保证两轴严格同步。为克服这一缺点,在啮合式离合器上装以摩擦片,变速时先靠摩擦片把从动轮带到同步转速后再进行接合。行星齿轮传动变速器可用制动器控制变速。
2.2变速箱的发展简介
机床变速箱是机床中极其重要的传动部件,因此在人们开始应用机械时变速箱就已经诞生。早期的机床变速箱主要是简易的换挡变速箱,也就是通过单纯通过齿轮和传动轴以及简单的变速机构来实现传动和变速。随着机械行业的发展,加工技术和金属材料日益先进,使得换挡变速箱结构日趋复杂和先进。但是人们通过长时间的生产和应用,发现换挡变速箱具有其设计原理上的缺陷,其无法实现传动比的均匀变化,造成速度损
失,从而影响加工条件。因此,人们开始研究实现传动比连续变化的方案,也就是无级变速。
无级变速箱是在19世纪90年代出现的,至20世纪30年代以后才开始发展,由于受当时各方面因素如机械发展水平、材质和加工工艺等条件的限制,进展十分缓慢。20世纪50年代,尤其是70年代以后,随着科技的发展,原本无法解决或很难解决的技术难题一一突破,加之实际生产中对无级变速箱的需求越来越多,无级变速箱得到了很大的发展,得到了较为广泛的应用。目前无级变速箱的研究和应用主要包括以下几个方面:液力无级变速、电力无级变速和机械无级变速。近年来以液力和电力无级变速为主要的研究方向,取得了较为较大成果。
在20世纪七十年代,随着机械制造业的发展,人们不再满足于对传统机械的应用,从而提出微机械的概念。到20世纪90年代诞生了对应于加工微型机械零件的微型机床,该机床所应用的传动和变速装置称为微型机床变速箱。微型变速箱的发展是近些年才引起广泛重视的。随着微细加工技术的进步,微小型传动件在生产数量和质量上都已经达到一定得要求,使得微型变速箱在近几年的发展迅速。但由于目前技术仍不够先进,微型变速箱在尺寸和传动精度上都无法达到令人满意的程度。但随着微细加工技术的深入,微型变速箱发展前景将极其可观。
2.3变速箱的分类
机床变速箱按照尺寸大小可划分为传统尺寸机床变速箱和微型机床变速箱。同时传统尺寸变速箱依照变速方式的不同可分为换挡变速箱和无级变速箱。
换挡变速箱是目前在机床上应用最广泛的一种。它采用齿轮传动,具有若干个定值传动比。这种变速箱主要由传动轴、滑移齿轮、离合器、变速机构以及其它传动件组成。变速过程通过箱体内操纵变速机构改变滑移齿轮的相对位置从而改变整体传动比来实现的。它具有传动扭矩大,效率高,功率大以及传动比稳定的优点。这些优点使其广泛应用于普通机床中。但是,其传动比比较固定,无法实现均匀变化,从而造成传动件有较大的冲击载荷,且需要人工调定传动比以保证电机良好运行。
无级变速箱是较换挡变速箱后发展起来并逐渐被广泛应用的变速。装置。它与换挡变速箱最大的区别是其可以实现传动比在一定范围内均匀连续的变化。无级变速的实现方式可分为液力式、电力式和机械式三种。机械无级变速装置有钢球式、宽带式多种结构,它们都利用摩擦力来传递转矩通过连续改变摩擦传动副的工作半径来实现无级变速。其主要应用于小型车床和铣床中。液压无级变速装置利用油液为介质来传动动力,通过连续的改变输入液压机的油液流量来实现无极变速。其主要应用于刨床、拉床等执行件为直线运动的机床中。电气无极变速装置是通过连续改变电动机的转速来实现无级变速,其主要适用于大型机床和数控机床。无级变速箱通过传动比连续均匀的变动能使机床获得最有利的切削速度。
3 研究目的、意义和内容
机床变速箱是机床中的重要组成部分和传动装置,机床运行性能好坏很大程度上决定于机床变速箱的传动性能。机床变速箱主要是由变速传动机构和操纵机构组成。它将电动机和主轴联结起来,通过传动轴和齿轮以及其它传动件将电动机动力传递到主轴。变速箱中的变速机构通过改变传动比从而达到改变电动机运行状态的目的。保持合理的传动比可以使电动机工作在其最佳的动力性能状态下。对于变速箱的研究,目的在于提高我们对机床传动的认识与理解。从设计中学习和总结经验,发现并改进变速箱发展中的不足之处,运用所学知识去解决实际问题,提高自己的动手能力,开拓自己的思维,不断创新。同时,也培养了我做事认真的态度,刻苦钻研的精神。 4进度计划
第1周实习调研并撰写实习调研报告、准备外文翻译资料
第2周查阅参考相关资料
第3周绘制零件加工工序图
第4周选择切削用量、计算相关数据
第5周绘制零件加工示意图
第6周绘制机床联系尺寸图
第7周绘制机床联系尺寸图、编写生产效率卡
第8周熟悉机床主轴箱相关资料
第9周设计主轴箱
第10周设计主轴箱
第11周绘制主轴箱总装图
第12周编写设计说明书提交初稿
第13周修改图纸和说明书并打印
第14周论文评阅和参加答辩
5参考文献
[1] 张耀宗.机械加工实用手册.机械工业出版社
[2] 吴光明.机械加工基础.机械工业出版社
[3] 陈宏钧.机械加工工艺装备设计员手册.机械工业出版社
[4] 王先逵.机械加工工艺手册.机械工业出版社
[5] 陈宏钧.实用机械加工工艺手册.机械工业出版社
[6] 温希忠.王永俊.刘峰善.机械加工基础理论.山东科技
[7] 颜龙.变位齿轮原理和应用.上海科学技术出版社
[8] 组合机床设计手册(大连组合机床研究所编制)
[9] 巩云鹏.机械设计课程设计
[10] 张济川.机械最优化设计及应用实例.新时代出版社
[11] J.P.Den Hartoy,Advanced Strength of Materials,Mc Graw-Hill,New York,1980.
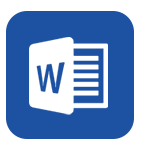