净化车间各单元事故案例汇编
1991年
变换炉爆炸事故
1、事故经过:
1991年8月6日,某化肥厂正常生产时,中变炉突然发生爆炸,炉体拦腰炸断、炉内弊板飞出,落在35m处厂区道路上,砸死1人。爆炸气浪将饱和热水塔掀翻,压坏厂房和设备。
2、事故原因:
经过分析,爆炸的原因是设备运行时长期超温过热,(持续时间在2000小时以上)。引起设备局部氧化、蠕胀、裂缝,产生材料脆性蠕变断裂而爆炸。造成设备局部超温的主要原因是变换炉内保温层局部损坏。
3、事故教训及采取措施:
变换炉内保温层施工时,必须选用耐火质量高的保温器材,施工单位必须选择具有一定资质的建筑队伍,严把质量关。
加强对变换炉炉壁温度的检测,发现温度超高,应及时处理。定期检查炉内壁保温材料完好,发现损坏,及时处理。
严格工艺指标,严禁超温、超压。
1993年
变换炉触媒水淹事故
1、事故经过:
93年11月14日,某厂德士古气化炉投料成功,净化接气开车,煤气入炉后,操作人员发现煤气水分离器报警,立即通知巡检排放,继而发现一变炉温度下降较快,立即作出入工段放空的处理。调度通知气化切气,合成气火炬放空,洗涤塔液位指示稍高但没有高限报警。
净化重新对变换系统升温后,接气生产。15日14:00再次发现煤汽水分离器报警,一变炉温度下降57℃ 。立即进行紧急停车,气化切断了文丘里灰水及洗涤塔塔盘给水,洗涤塔液位仍无下降趋势,判定洗涤塔液位计误指示,后计算机重新组态洗涤塔压差,靠压差值判断塔的液位维持系统运行。 2.事故损失:
造成净化预变和一变催化剂被淹,活性下降,系统阻力增加,被迫停车三天。 3.事故原因:
① 洗涤塔玻璃板液位计被黑水污染,无法现场判断液位高低;
② 气化炉激冷环垢堵严重,激冷水无法加量,造成灰水补充联锁阀打开,洗涤塔循环泵打量很小;
③ 洗涤塔入高压闪蒸罐黑水管线堵,二次疏通后再次被堵,流量计取压管堵后得不到正确判断,造成洗涤塔无法排水;
④ 净化操作人员无处理该类事故的经验,未能及时切气停车,造成大量积水带入预变炉、一变炉,致使炉温较低。
1994年
变换5.20爆炸事故
1、事故经过
1994年5月20日下午3点30分,****化肥厂净化车间变换工段热交换器入口处丁字形立管突然爆炸。一块重约79千克、面积为约0.89立方米的管壁被炸飞水平距离11.3米远。 大量含有混合气体、可燃气体、有毒有害气体高速喷泻,引起空间气体爆炸,殃及正在离爆炸处仅3米远的11名堵漏作业人员,当场造成3人死亡,8人受伤。其中7人重伤。在实施抢救的过程中,先后又有5人死亡。 2.事故损失:
事故共造成8人死亡,2人重伤,1人轻伤。事故造成的经济损失达130万元。
3、事故原因:
事故发生后,厂内组织的工程技术人员对现场进行了勘察。经过对设备材质的金相分析,对管壁测厚及介质等因素方面的分析,认定事故的发生与管内介质对管道的超常不均匀化学腐蚀、气体冲刷、管道局部严重减薄、应力集中,导致其工段热交换器丁字立口处不能承受当时的工艺、压力指标,引起突然爆炸。
事故原因是在系统腐蚀严重的情况下, 对管线严重腐蚀的后果认识不足, 未能及时更换管线所致。
4、采取措施 (1). 严格控制半水煤气中的硫含量; (2). 严格控制变换系统原料气中湿含量和温度, 防止冷凝; (3). 加强压力管道管理, 建立测厚制度, 发现泄漏要检查分析原因, 弄明情况, 及时处理。
1997年
中变炉床层垮温
1、事故经过与紧急处理:
1997年10月11日7:58,某德士古气化的甲醇装置变换入口分离器F7101液位8分钟内从38mm猛涨到636mm,现场可听到管道水击声,虽经排放,液位仍居高不下,引起变换炉进水,催化剂床层温度下跌至其活性温度以下,操作人员通过HV7101阀将合成气放火炬一部分,但炉温仍快速下降。9:30进中变炉气量只有60000m3/h,HV7101开度35%,分离器液位仍未下降。系统生产不能维持,甲醇及CO系统被迫停车。甲醇停车后中变炉氮气循环升温。12日4:00,合成开车。12日18:35,CO压缩机开车。
2、事故原因分析:
从DCS调出的数据来看,当时德士古负荷无大的波动,合成气流量、压力较平稳,无明显变化,合成气带入中变炉的水应为液态水。而德士古1#洗涤塔液位于7:40开始由1110mm下降,8:05降至803mm,说明在这段时间内有带水现象,带水可能是由于洗涤塔顶部除沫器损坏或回水管堵塞。
3、事故后果及损失:
造成甲醇停车18.5小时,CO停车33小时。 2000年
变换气换热器下部膨胀节爆炸
1、事故经过
2000 年9月,某化肥厂变换工段正处于停车检修后的开车阶段。变换炉正常接气后,系统逐渐加量,调整工艺指标。在此过程中,变换系统传来一阵闷响,变换系统压力迅速下降。工艺操作人员立即进行紧急停车处理。处理完毕后发现,变换气换热器 下部膨胀节裂开一道约20cm 的口。该设备进行了约 3 天的检修恢复。运行后为带病设备,监控运行。
2、事故原因分析
(一)变换系统停车时间较长,变换气换热器 管壳程存在温差。在开车接气过程中,因变
换炉内高温气体带入 变换气换热器 内,造成短时间内管壳程温差迅速上涨,热应力过大,引起设备材料产生变化,超过设备的承受能力。造成设备爆炸事故。
(二)变换气换热器 制造存在缺陷,膨胀节没起到相应作用。
3、防范措施
(一)系统长时间停车后应开启变换升温系统,或先接入少量水煤气预热设备,在变换炉前放空,消除变换气换热器 温差后,再逐渐加量。
(二)严格控制操作步骤,接气开车时控制好温度、压力、生产负荷加减应缓和, 不能大开大关,避免因工艺指标波动而引起的设备事故。
(三)加强业务学习,掌握设备的结构、原理,掌握其操作技能、要点。
2006年
一、***车间一段变换炉超温事故经过及原因分析
1、生产波动经过:
2006年9月13日,车间按照检修计划对1#气化炉进行气密,由于此时空分单元尚未生产出合格氮气,为了赶进度,就用氮压机三段出口不合格氮气,作为气密介质对气化炉进行气密;在气化炉充压过程中,不合格氮气窜入一段变换炉,致使一段变换炉内触媒短时间内严重超温,造成了部分耐硫变换触媒损毁。
2、产生原因及危害: 原因:
1)洗涤塔出口去CO变换单元手阀(或副线阀)及快速切断阀HV02121内漏,1#气化炉做气密时氧气进入到变换炉系统内部。
2)耐硫变换催化剂在进行升温操作,催化剂已经达到活性温度。系统有氧气进入后,引起变换催化剂飞温(催化剂在50℃以下与氧气接触不会出现飞温)。
3)200单元与CO变换单元之间阀门均为焊接结构,无法采用加盲板隔绝的措施,仅仅采用关闭两道阀门、打开两道阀门中间导淋放空的方法进行隔离,没有能够做到200单元与CO变换单元的有效隔绝。
4)1#炉开始充压后,现场操作人员在气化炉压力达到1.0Mpa左右时,到现场进行了检查,但是没有发现200单元与CO变换单元两道阀门之间的放空导淋漏气,所以继续对1#气化炉进行充压,气化炉压力继续升高后,没有再次派人去确认该导淋处有无气体,导致高压的不合格氮气窜入到变换系统,造成了一段变换炉的超温。 危害:
一段变换炉催化剂床层温度超温,烧毁部分催化剂。
3、采取措施及处理方法:
在工艺对系统要进行工艺操作时,首先要细致排查操作存在的风险,并针对风险制定相应的应急预案。
在工艺操作出现问题,要针对问题产生的原因进行分析,并对工艺运行工艺条件进行详细检查,发现工艺条件波动要查明原因,并及时联系相关人员进行处理。
4、吸取教训及注意事项:
1) 在工艺对系统要进行工艺操作时,首先要细致排查操作存在的风险,并针对风险制定相应的应急预案和生产操作方案。
2) 再有类似生产操作时,首先保证操作方案和应急预案的落实,保证操作员对方案及应急预案进行充分掌握。 3) 4) 5) 6) 7) 气密实验前,一定要保证系统的有效隔绝或制定安全可靠的防范措施。
气密实验时,一定要保证系统进行氮气置换,并且采用合格的氮气作为气密介质。
在气密过程中,认真执行确认制度,设置合理的确认时间及确认点。 在气密过程中,操作员应该按照方案要求进行操作,不允许违章作业的发生。
在气密期间,操作人员精心操作,监控好各项工艺指标是否正常,每10钟至少浏览一遍画面,并与现场操作指标进行校对。
2007年
一、氨冷冻单元冰机跳车,低温甲醇洗单元甲醇循环温度逐渐升高
1、事故经过:
2007年7月20日,由于氨冷冻单元冰机跳车,导致低温甲醇洗单元甲醇循环温度逐渐升高,系统被迫减负荷。
2、产生原因及危害: 原因:
冰机跳车后,三个氨冷器(E050
2、E050
6、E0515)不能给低温甲醇洗单元提供冷量,造成低温甲醇洗单元甲醇循环温度逐渐升高,T0501塔出口净化气微量逐渐升高,系统被迫减负荷。 危害:
微量超标严重,造成低温甲醇洗单元停车。
3、采取措施及处理方法:
1)引空分单元液氮,送至T0503塔底部,以降低气提氮温度,减缓甲醇温度回升速度。
2)适当关小液氮洗单元去氨合成单元合成气出口阀TV06032,增加液氮洗单元去低温甲醇洗单元合成气的量,为低温甲醇洗单元多提供一些冷量,减缓甲醇温度回升速度。
3)如果液氮洗单元分子筛此时处于加热阶段,高温氮气进入T0503,会加快低温甲醇洗单元甲醇温度回升速度,此时应将分子筛加热再生停止,将氮气切换至经FV0液氮洗1直接入T0503塔,使低温度气提氮进入T0503塔,减缓甲醇温度回升速度。
4)可以根据温度回升情况,逐渐减负荷,维持低温甲醇洗单元操作,一般情况下能维持3-4小时,在这段时间内,冰机基本能恢复正常。
4、吸取教训及注意事项:
1)在正常操作中,注意低温甲醇洗单元温度变化情况,发现异常及时查找原因,及时处理。
2)负荷调整时,氨冷器加、减要缓慢,事先与合成操作工联系,防止因负荷调整过大,造成D1101液位上涨过快,导致高液位联锁动作,冰机跳车。
二、E1303真空度升高
1、事故经过:
2007年8月19日,化工二班发现E1303真空度有上涨趋势,操作人员立刻进行排查,对可能引起真空度上升的原因进行排除,采取了一些措施后,效果比较好,真空度有所下降;基本稳定在40Kpa,但没有降到正常值(27Kpa左右)。直到8月20日白班,在查找真空度上涨原因的过程中,当时循环水温度较高,真空度三点压力再次上涨,几乎快到跳车值(跳车值为80Kpa,为3选2联锁),车间立即采取措施,找仪表对真空度联锁进行强制;同时又采取一些措施降低了真空度,包括打开疏水器旁路对E1309排冷凝液;拆下一段疏水器检修,虽然真空度当时能降低,但不能维持太长时间,而后又快速上涨。
以上这些措施都没有特别明显的效果,经车间研究,初步判断是换热器换热效果不好,可能是循水水质不好,一些列管口被杂质堵塞,然后我们制定了方案,清理杂物,然后制定方案采用反向排水,结果发现循环水水质确实不好,前后排出大小不等的4块塑料布;每次排完以后,真空度大幅度下降,降到28 Kpa左右,循环水投用以后,真空度缓慢上升,基本2小时后达55Kpa,然后排水。而后换热器换热效果较好,循环水温度也比较低,因此真空度一直在工艺控制指标范围内。
2、产生原因及危害: 原因:
1)E1303真空度上涨原因是循环水杂质多,堵塞了换热器的管程,减少了换热器的换热面积,引起了真空度上涨。
2)抽负器J1303A抽负效果不好; 危害:
可能造成氨合成单元联锁停车
3、采取措施及处理方法: 1)、对E1309二段疏水器进行排水; 2)、找仪表对真空度表进行排水; 3)、在E1303表皮用喷淋进行降温 4)、全开循环水进出口阀。 5)、对抽负的IP蒸汽进行排水、排不凝气 6)、先缓慢全关上水阀,然后打开上水管的排污阀进行排污; 7)、停抽负器J1303A
4、吸取教训及注意事项:
1)定期清理换热器杂质;
2)联系调度要求水汽车间保持循环水清洁;
3)对操作人员进行培训,从以下几方面判断真空度升高的原因: ①表冷器液位高; ②循环水温度高; ③循环水量少;
④表冷器内有不凝汽; ⑤IP蒸汽带水;
⑥E1303换热效果不好; ⑦IP蒸汽压力低;
⑧抽负器抽负效果不好; ⑨仪表假指示;
⑩E1309疏水器不好用。
2008年
一、****车间CO变换单元一段变换炉压差高
1、事件经过:
2008年6月11日10时,化肥厂合成氨车间按照检修计划对低温甲醇洗单元进行开车后,发现低温甲醇洗单元与气化单元洗涤塔之间的压差达到1.0Mpa(CO变换单元变换炉压差计堵塞),随后进行排查,发现阻力存在于CO变换单元一段变换炉,经请示工厂、公司领导后,合成氨系统进行停车处理。
2、产生原因及危害: 原因:
合成氨车间一段变换炉按照检修前计划更换10吨催化剂,并且更换的催化剂是变换炉下层的失活催化剂,在对全炉催化剂进行卸出时产生部分粉化,在回装催化剂时,采纳厂家建议没有对利旧的催化剂进行过筛,致使利旧催化剂中大量的粉末又重新填充到变换炉内。 危害:
在CO变换单元开车后由于催化剂间隙内粉末多,使催化剂床层压差上升超出设计范围,为生产的运行埋下了不可预计的安全隐患。
3、采取措施及处理方法:
(1)气化炉及后部系统全面停车,两段变换炉的催化剂进行全部更换。 (2)联系仪表人员处理好两段变换炉的压差计。 (3)制定更换催化剂的方式,尽量不利旧催化剂。
(4)如果有利旧的催化剂回装至系统内时,必须进行过筛处理。
4、吸取教训及注意事项:
(1)联系仪表人员,保证两段变换炉的压差计保持正常好用状态。
(2)加强变换炉系统压差的监控。发现异常,不能掉以轻心,要认真确认及时处理,确保安全。
(3)出现问题时要及时联系车间有关技职人员,防止发生安全事故。
(4)工厂及车间在更换催化剂技术方案的风险识别上要加深认识,不要过于信赖厂家提供的信息。
(5)在催化剂使用前,要进行技术检验,保证催化剂的强度与活性在技术指标范围内。
(6)在更换催化剂的时机及更换催化剂的具体方案制定上要充分考虑清楚,尽量不使用旧的催化剂,如果必须采用旧催化剂,旧催化剂在回装之前,必须经过过筛处理。
二、合成单元开车,E0701反充中压氮气引起锅炉水窜入液氮洗单元冷箱,导致冷箱冻堵。
1、事故经过:
1) 2008年9月6日,在氨从现在氨合成单元开车过程中,为了减少由于压差增大而对E0701的损坏,车间决定E0701充中压氮气,E0701与合成回路同时充压,E0701与合成回路的压差必须小于1MPa,当压力充到7.2 MPa时,保持氮气阀位(氮气阀门不能全关,关闭后锅炉压力会迅速下降),没有留专人看护,待E0701开始产汽,压力开始上升后,及时关闭充中压氮三道阀门,然后打开中压氮气放空阀。发现氮气导淋排出大量的水汽,而后液氮洗单元出现FV0液氮洗7加不上量,导致液氮洗单元、700单元停车。打开中压氮气管网用户低点导淋处排水,结果从氮气导淋处排出大量的水,这充分说明了中压管网已窜入大量的水,水随氮气进入液氮洗单元冷箱,由于冷箱温度低,水冻成冰而堵塞在管道内,因此出现FV0液氮洗7加不上量的现象。
2、产生原因及危害:
原因:
1、E0701开始产汽时,没有及时关闭中压氮气阀门;
2、E0701用氮气充压时,氮气导淋未开,反窜的蒸汽直接进入氮气管网而没有放空;
3、中压氮气管线上的止逆阀坏,不能起到阻止蒸汽反窜的作用。
4、E0701氮气充压线,设计不合理,应从锅炉顶部充入。
5、操作人员责任心不强且经验不足
6、管理技术人员对上次同类事件没有引起足够重视,采取措施不够。
7、反窜水随中压氮气进入液氮洗冷箱,造成冷箱冻堵。 危害:
1、造成液氮洗单元冷箱冻堵,液氮洗单元、700单元停车;
2、中压氮气管网带水,影响用户的正常使用。
3、采取措施及处理方法:
1)在中压氮气管网用户低点导淋处排水,分析氮气露点,直到合格为止; 2) 液氮洗单元发现FV0液氮洗6或FV0液氮洗7加不上量,并且冷箱的阻力突然增大时,马上联系值班长,车间技术人员,并做紧急停车处理。 3) 液氮洗冷箱进行回温复热,各排放点做露点分析合格。
4、吸取教训及注意事项:
1) 重新修订E0701开车方案,进行细化和完善,并组织员工进行学习; 2) 开车时,从E0701充压到产汽的整个过程,应设有专人在E0701处监控运行;
3) 当E0701有产汽迹象时,立即关闭中压氮气阀门,并打开放空; 4) 重新设计充中压流程,更换内漏的阀门和损坏的止逆阀,并增加止逆阀; 5) 不能连续开着氮气来保压,应该间歇保压,当压力平衡时停止充压,打开氮气导淋,当压力低时,再次充压,如此反复。 6) 开车时应有足够的有经验的操作人员把关。
7) 教育操作人员意识到后果的严重性,对此次事故引起足够重视,在以后一定要避免类似事故发生。
8) 液氮洗单元回温复热时一定要全部回温,不可局部回温。
2010年:
一、液氮洗单元安全阀泄漏事件
1、事件经过
2010年7月7日9时左右,施工单位进行消漏,检修人员在消漏过程中,在事先没有联系现场操作工的情况下,擅自拆开安全阀上、下法兰口,造成火炬线管线口往外喷气体,气化炉被迫停车事件。
2、产生原因及危害:
原因:
液氮洗单元在试漏过程中,发现分子筛安全阀下法兰漏,2010年7月7日9时左右,联系施工单位进行消漏,检修人员在消漏过程中,在事先没有联系现场操作工的情况下,擅自拆开安全阀上下法兰口(此时由于气化炉投油点火,火炬线内有压力),沿着火炬线管线口往外喷气体,造成气化炉被迫停车事件,安全阀回装后,气化炉重新投油点火。
危害:
有可燃气体喷出,可能发生火灾,中毒事故。
3、采取措施及处理方法:
1)气化炉停车,卸净火炬压力。 2)联系化验室分析可燃气含量。
3)联系检修人员及时把安全阀回装上。
4、吸取的教训及注意事项:
1)工艺师、班长、现场监护人员监管不到位,检修人员到现场干活没有及时发现。
2)检修人员在消漏过程中,在事先没有联系现场操作工的情况下,擅自进行检修工作。
3)票证书管理有漏洞,检修人员没有找化工确认,擅自进行检修。
二、贫甲醇P0504B泵检修时甲醇外漏事件
1、事件经过:
2010年6月20日9时,合成氨装置进行年度大检修停车处理,低温甲醇洗单元甲醇循环系统,按照停车方案,停止接原料气后,进行甲醇再生和氮气置换工作,于6月21日15时,置换分析合格,系统腿甲醇结束,6月22日8时,按计划交出检修。
贫甲醇P0504B按照工艺处理方案,关闭出入口阀门和回流阀,导通入口管线和泵体去排放罐D0508排液“8”字盲板,将入口管线及泵体内的甲醇排净后,关闭排液阀。在泵拆开后,没有甲醇流出,当将泵轴抽出后,发现泵出口管处往下滴甲醇。
2、产生原因及危害:
原因:
1、挂在管线壁上的甲醇由于时间较长流下来:
2、泵出口止回阀内漏,使泵出口管线内的甲醇流过来(原设计泵出口没有排放管线,所以泵出口至出口阀之间有近三米管线内的甲醇工艺处理时无法排出)。
危害:
1)可能造成人员中毒。 2)可能造成环境污染
3、采取措施及处理方法:
1)在泵出口管线法兰处加盲板。 2)现场临时用胶管接氮气进行置换
4、吸取的教训及注意事项:
1)排放时间有些短,以后检修时排放时间要长一些。 2)以后泵检修时,泵出口法兰处可以加盲板的,一定加盲板进行有效隔绝,防止甲醇外漏造成人员中毒。
3)以后凡是有甲醇的设备检修时,置换工作考虑得不够细致,有死角。 4)要认真吸取经验教训,工作中不怕麻烦,在头脑中树立安全第一思想,不抱有侥幸心理。
三、5月18日E0403工艺气导淋泄漏事件经过
1、事件经过
2010年5月18日7时15分,操作人员于海在现场巡检过程中,突然听到剧烈噪音,操作人员于海顺着噪音发现在E0403工艺气管线弯管下部有大量工艺气泄漏,7时25分1#气化炉停车,11时1#气化炉投油开车,11时50分向CO变换单元导气,12时55分CO变换单元向低温甲醇洗单元导气。
2、产生原因及危害: 原因:
1)E0403工艺气管线弯管下部倒淋阀门存在约1扣的开度,没有全部关闭是造成此次泄漏的直接原因。
2)由于装置大检修期间需要对工艺气系统各排空倒淋进行排放,检查两段变换炉内催化剂是否存在严重粉化出现透催化剂现象,E0403工艺气管线弯管下部倒淋阀门存在约1扣的开度就是在对系统进行吹扫时一段变换炉的催化剂粉末滞留在倒淋阀门口内,致使倒淋无法正常关到位,而操作工将阀门关到关不动的地方,即认为是关严了,经过多次停开车及运行,系统的温度、压力出现大范围的波动,致使卡塞物体出现松动被高压的工艺气体吹出,造成本次事件的发生。
3)此次事件的发生,说明化工在现场实际操作中还存在操作经验还较为欠缺和车间在管理上还有不到位的现象。
危害:合成器大量泄漏已造成着火、爆炸事故,同时高温气体泄漏已造成设备过热或人员伤害事故。
3、采取措施及处理方法:
1)现场操作人员于海发现在E0403工艺气管线倒淋泄漏,立即通报主控。值班长立即通报工厂调度室并下达1#气化炉停车指令,通报全区注意可燃气体防护。
2)车间主任立即下达全区封锁命令,并派专人对下风向区域进行封锁。 3)联系分析车间对泄漏点附近100米范围内空间气体进行可燃气分析,分析结果正常。
4)安排现场操作人员佩戴空气呼吸器到现场进行停车处理,根据装置工艺流程把2CO变换单元中压氮气倒入CO变换单元进行系统正压保护,控制变换单元系统压力保证0.2-0.3Mpa之间,泄漏量减小。
5)现场人员接近泄漏点,关闭E0403工艺气管线弯管下部倒淋阀门,漏点消除。
4、吸取的教训及注意事项:
1)今后在大检修后,在气密过程中,所有的倒淋阀门都要进行通畅确认(即在系统有压力的情况下,打开倒淋阀确认是否有气体排出)及阀门位置确认(检查阀门是否关闭到正常位置)。如有堵塞或阀门关不到位的现象,应处理正常后,方可进行装置开车。
2)严格执行多级确认制度。车间主任、工艺师、值班长、班长、化工对单元的交出、交回应进行详细认真的检查和确认。
3)开车前,应制定检查表对所有的阀门位置进行认真的检查和确认。 4)针对此次事件,在大检修期间对每个工艺气系统倒淋进行排查,确保每个倒淋是处于通畅及开关正常的状态。
四、E0511甲醇冷却器内漏事件
1、事件经过
2010年5月14日,根据工厂计划停车,E0511进行消漏(2010年3月27日系统短停消缺,开车后发现循环水中COD升高较快,循环水换热器取样分析发现E0511内漏)。
2、产生原因及危害:
原因:
由于甲醇冷却器E0511壳程与管程压差较大(9.5-10MPa),在开车过程中由于压力变化较大,导致E0511内漏。
危害:
1、从甲醇消耗量来看,E0511内漏量逐渐增大,从前期的3吨/天增加到6吨/天,甲醇消耗增高。
2、由于甲醇易燃有毒,因此直接排放有一定风险,且对环保构成较大压力,容易造成所排放的地下水管线火灾及爆炸事故及人员中毒事故。
3、突然漏大,由于壳程压力较大(10 MPa),管程耐压较小,容易造成设备损坏。
3、采取措施及处理方法:
为了防止出现以上事故,所以将此换热器循环水全部切出,改由外部喷淋水对甲醇进行冷却,同时将E0511漏出的甲醇进行回收。同时为了保证在E0511漏大的情况下不发生危险及事故,特制定如下工艺处理方案:
1)、循环水切出前需要具备的条件
1.1、将D050
6、E0511喷淋水全部投用。
1.2、将E0511底部1.5"导淋与D0508去P0507泵3"导淋用钢管连接。 1.
3、在E0511顶部导淋管线上安装一1.0MPa(g)量程的压力表。随时监控其排放压力。(要求排放压力小于0.5Mpa)
2)、循环水切出后的操作
2.1、将E0511循环水上水阀缓慢关闭,观察两条导淋排放线排放情况,若其逐渐减小后,取样分析甲醇中水的含量,若水含量小于5%,则逐渐打开E0511底部1.5"导淋与D0508去P0507泵3"导淋连接阀,将甲醇引入D0508中,由于此时甲醇含量还较低,此股甲醇/水需要引入T0503塔进行回收。取样分析甲醇中水的含量,若水含量大于10%时,联系车间相关领导再做决定。
2.2、此甲醇回收到D0508后,应每班对D0508出口甲醇进行取样分析,若甲醇中水含量小于10%,可直接将此甲醇缓慢(要求控制入系统中甲醇流量小于3t/h,即应控制D0508液位下降速度小于20%/h)打回系统中使用。
2.3、在开P0507泵向T0505塔送此甲醇/水过程中,应缓慢开阀并保持小量,即能够保证D0508液位不上涨即可。T0505塔设计最大可处理950.93kg/h,在将D0508中甲醇引入T0505塔前,将E0501前喷射甲醇量减至550 kg/h左右,以确保T0505塔可处理两股甲醇/水的总量。
2.4、在E0511切出后,应加强对入T0501塔甲醇温度的监控,若其逐渐上升,则应将各氨冷器加量,确保其温度在-58℃以下。
3)、E0511漏大的应急处理
3.1、净化外操发现E0511排放甲醇处压力表超压,立即联系值班长,值班长立即联系车间相关技职人员,同时联系调度室,请求低温甲醇洗单元立即紧急停车处理,防止因贫甲醇量过少造成T0501塔出口微量超标,液氮洗冷箱冻堵事故发生或因甲醇大量泄漏造成E0511超压而损坏。
3.2、净化内操发现甲醇循环异常(入T0501塔贫甲醇量掉量较多或压力下降较多),立即联系值班长,值班长立即联系车间相关技职人员,同时联系调度室,请求低温甲醇洗单元立即紧急停车处理,防止因贫甲醇量过少造成T0501塔出口微量超标液氮洗冷箱冻堵事故发生或因甲醇大量泄漏造成E0511超压损坏。
3.3、净化内操发现入T0501塔贫甲醇温度持续上升,无法控制,立即联系值班长,值班长立即联系车间相关技职人员,同时联系调度室,请求低温甲醇洗单元立即紧急停车处理,防止因贫甲醇温度过高造成T0501塔出口微量超标液氮洗冷箱冻堵事故发生。
4、吸取的教训及注意事项:
4.1、日常操作中现场操作人员需要加强对E0511排放甲醇压力的监控,若其排放压力超过0.5MPa(g),则联系调度室,低温甲醇洗单元及后部单元紧急停车。
4.2、如果E0511排放甲醇压力虽然没有上涨,但甲醇消耗量已增加至10t/d,则立即联系车间相关技职人员,车间联系工厂,请求停车进行消漏处理。
4.3、日常操作过程中,总控操作人员加强对D0508液位的监控,若D0508液位上涨过快,则迅速联系现场人员对E0511排甲醇管线上压力表进行检查,确认漏量加大,联系车间相关人员或与调度联系,紧急停车。
4.4、为了加强监控,特在现场及总控设置一个临时记录表,要求30分钟记录一次,总控15分、45分是记录D0508液位。现场整点和半点记录现场压力表压力,要准时,记录要真实。
五、大检修后冰机开车气封损坏事件 事件经过:
2010年7月份大检修后,冰机进入开车阶段,7月8日,冰机开车在加载的过程中,由于冰机振动XI-13631高高联锁跳车,跳车后盘车不能自动启动,手动盘车有卡涩现象,经相关管理人员确认,气封与轴发生摩擦,经检修后,7月12日再次开车,由于仪表程序问题,开车前三次均由于PALL13630、PALL13634低低联锁跳车,第四次开车由于振动XI-13630振动高跳车,跳车后手动盘车有卡涩现象,经检修后,7月18冰机一次开车成功。 原因分析:
1)干气密封安装存在问题;
2)仪表冰机控制系统软件升级安装过程中存在一定问题。 采取措施及处理方法:
1)冰机检修后,经气密、氮气置换、氨气置换合格后方可做开车准备; 2)开车时严格按操作卡执行,冰机系统压力控制在0.1—0.12MPA,D1104液位控制在75—80%。
3) 冰机跳车后,不要急于放压,待E0113出口气氨阀关闭后再卸压。
4) 在开车过程中,控制好D110
1、D110
2、D1103的液位,不能超工艺指标; 吸取教训及注意事项:
1)在检修进度与检修质量发生冲突时,要以检修质量为重; 2)发生跳车后,要认真分析原因,消除故障后再开车;
3)开车时要认真执行操作规程,严禁发生超温、超压、环境污染事件。
五、*****公司变换爆炸事故
1、事故经过
2010年7月22日上午8点半左右,******公司车间工作人员发现变换工段管道有泄漏现象,随后组织公司安全检修人员到现场查看,并制定处理方案。 8点45分左右,变换系统副线管道泄漏气体处发生空间爆炸,造成现场5人死亡、6人受伤,预计经济损失约500万元。
2011年:
一、高压蒸汽压力低手动停冰机事件
1、事件经过:
2011年2月12日23:57分,公用工程主控人员郑晓东发现外来高压蒸汽压力下降较快,立即报告值班长,值班长联系调度室说明情况,同时给二动力打电话说明情况,二动力未发现其生产异常。00:02分,高压蒸汽压力已降到7.8MPa,冰机转数开始掉转,由10350rpm掉到9920rpm;空压机同时也出现掉转现象,由5420rpm掉到5370rpm;00:06分,此时高压蒸汽压力已降到7.47MPa,值班长陆跃忠命令立刻启动应急预案,合成单元主控计冬丽立刻对冰机和合成气压缩机进行手动停车处理。由于冰机停车,高压蒸汽用户减少,空压机转数逐渐恢复到正常转数。
2、产生原因及危害:
原因:
二动力厂炉子跳车,高压蒸汽量减少。 危害:
(1)高压蒸汽压力降低,外来流量减少。
(2)引起冰机跳车,空压机跳车即合成氨装置全面停车。
3、采取措施及处理方法:
(1)立即启动应急预案,手动停下冰机和合成气压缩机,保住空压机。 (2)700单元保温保压。 (3)停F1301炉
(4)1100单元卸压完毕后,待高压蒸汽压力恢复后开冰机。
4、吸取的教训及注意事项:
(1)精心操作,发现高压蒸汽压力有异常,及时采取措施,果断启动应急预案。
(2)加强与调度和二动力的联系与沟通,确保蒸汽平稳。
(3)对于实际操作还需要继续加强,熟练掌握操作要领,并能提前判断运行趋势,操作人员具备快速反应能力。
2012年
一、4.10冰机跳车事件
1、事件经过:
2012年4月10日18:15时,外来高压蒸汽压力瞬间由8.89MPa降到8.64MPa,高压蒸汽消耗量由155t/h达到167t/h,中压蒸汽网消耗不掉,冰机排汽压力高高联锁跳车(联锁值4.55MPa,为三选二联锁),同时手动停C/X0701。
2、产生原因及危害:
原因:
目前合成氨装置已运行到检修周期的末期,特别是空压机、冰机结垢严重,高压蒸汽消耗量较大,导致中压蒸汽过剩、超压放空,高压蒸汽的消耗量受其压力、温度以及循环水温度影响较大,一旦二动力蒸汽控制不好,高压蒸汽消耗量立刻上升,中压蒸汽压力升高,冰机就可能因此联锁跳车(冰机排汽压力高高联锁),这一隐患时刻威胁着冰机的安全稳定运行。本次跳车由于外来高压蒸汽压力瞬间由8.89MPa降到8.64MPa,高压蒸汽消耗量由155t/h达到167t/h,中压蒸汽网消耗不掉,冰机排汽压力高高联锁跳车。 危害:
增加了装置的原料消耗,合成单元不能产量,影响到丙烯腈装置高负荷运行。
3、采取措施及处理方法:
1)加强监控、联系,保证外来蒸汽压力受控。
2)快速适当开PV13006.3降压,避免冰机背压高跳车。
4、吸取的教训及注意事项:
1)精心操作,及时联系保证正常高压蒸汽压力
2)PV13006.3要适当,开度过大会导致外来蒸汽压力更低
二、4.25冰机跳车事件
1、事件经过:
2012年4月25日19:40时,冰机X/C1101出现二次油压和转数波动,转速降低到9884rpm,低于最小控制转速(9951 rpm),冰机X/C1101卸载跳车。
冰机X/C1101跳车后,700单元按正常停车处理,F1301炉停车,工艺气在CO变换单元和CO变换单元放空,低温甲醇洗、液氮洗单元减负荷运行。
在开车过程中出现了I/H转换器输出最大的故障。经过检查发现是由于I/H转换器的信号电缆有短接现象,造成了输出最大。在现场对所有信号线进行了排查,并且全部重新紧固后,I/H转换器恢复正常。
2、产生原因及危害:
原因:
通过查看DCS记录,对二次油曲线,转速曲线和蒸汽量曲线进行对比查看,得出结论,由于外来高压蒸汽压力降低,为了维持转速,通过开大调速阀,进入更多的高压蒸汽,但由于调速阀卡滞,高压蒸汽进不来,就会造成转速降低,只要低于最低转速9951rpm,冰机便卸载停车。 危害:
增加了装置的原料消耗,合成单元不能产量,影响到丙烯腈装置高负荷运行。
3、采取措施及处理方法:
1)冰机跳车,合成气压缩机正常停车 2)对冰机高压阀进行测试,启车
3)启车过程中发现冰机透平I/H转换器出现问题
4)检查更换冰机透平I/H转换器,冰机再次启车正常。
4、吸取的教训及注意事项:
(1)认真监控冰机二次油压指标。
(2)仪表加强I/H转换器定期检测,确保完好。 (3)二次油压异常波动,计划停冰机检查消除
三、5.10冰机跳车事件
1、事件经过:
合成氨岗位人员发现X/P1302A泵跳车,X/P1302A跳车后少用中压蒸汽约16t/h,造成中压蒸汽管网压力迅速升高,中压蒸汽放空阀PV13006.3开到100%,操作人员及时打开PV13005.1阀将中压蒸汽倒入低压蒸汽管网降压,但由于中压蒸汽管网余量过小,中压蒸汽管网压力上涨过快,同时冰机X/C1101因出口蒸汽背压高高联锁跳车(高高联锁跳车值:4.55MPa)。
冰机X/C1101跳车后,700单元按正常停车处理,F1301炉停车,工艺气在CO变换单元和CO变换单元放空,低温甲醇洗、液氮洗单元减负荷运行。
2、产生原因及危害:
原因:
1、P1302A油压低联锁跳车后,中压蒸汽用量突然减少,导致冰机背压高高联锁跳车。
2、空压机工况不佳,中压蒸汽系统压力高,自动放空不能正常调节所致。 危害:
导致冰机跳车,增加了合成单元开停车的原料消耗和产量损失。
3、采取措施及处理方法:
1)X/P1302A泵跳车后,P1302C泵联锁自启。 2)查明原因开启X/P1302A泵,停P1302C泵备用
3)润滑油回流调节阀,加保护盒上锁,防止误操作。
4、吸取的教训及注意事项:
1)更换油过滤网时,必须开启辅助油泵保压。 2)正常生产时,润滑油回流阀上锁,不要乱动。
四、6.28冰机跳车事件
1、事件经过:
2012年6月28日6:22时,UCC发出假信号冰机X/C1101跳车。冰机X/C1101跳车后,700单元按正常停车处理,F1301炉停车。
2、产生原因及危害:
原因:
UCC发出假信号导致冰机X/C1101联锁误动作跳车。 危害:
增加了装置的原料消耗,合成单元不能产量,影响到丙烯腈装置高负荷运行。
3、采取措施及处理方法:
冰机X/C1101跳车,合成气压缩机正常停车;F1301炉正常停车,联系外来蒸汽保压。1100单元系统降压。仪表处理UCC冰机通讯故障。仪表问题处理后,组织开车。
4、吸取的教训及注意事项:
(1)仪表专业要在适当的机会对卡件进行测试,确保其好用。
(2)加强与调度和二动力的联系与沟通,确保蒸汽压力高于8.8MPa。 (3)冰机跳车后,手动停下合成气压缩机,要控制好泄压速度。
五、X/C0701机组因密封气压差高跳车事件
1、事件经过:
2012年8月9日8:22时合成内操发现合成气压缩机C0701干气密封压差三点上涨到283KPa,比较稳定,车间针对干气密封压差升高进行原因分析,并制定了临时方案监控运行。8月10日8:32时,二组合成内操岗位人员计冬丽发现合成气压缩机C0701干气密封压差三点上涨到330KPa,接近跳车值CO变换 KPa,车间及时汇报调度室及相关科室。10:01时,合成气压缩机C0701密封气压差三点瞬间上涨到490 KPa,合成气压缩机C0701密封气压差高高联锁跳车。10:03时冰机透平振动XI13626Y1高高联锁跳车。
X/C1101冰机、X/C0701压缩机跳车后,合成氨装置立即启动装应急预案。 50小时后恢复正常生产。
2、产生原因及危害:
原因:
干气密封存在问题 危害:
(1)导致合成气压缩机停车检修。 (2)引起冰机联锁跳车。
3、采取措施及处理方法:
1)合成气压缩机机封检修后,经气密、氮气置换、合成气置换合格后方可开车。 2)开车阶段工艺密封气压力正常时,及时切换密封气。
3) 冰机跳车后,不要急于放压,待E0113出口气氨阀关闭后再卸压。
4、吸取的教训及注意事项:
1)在检修进度与检修质量发生冲突时,要以检修质量为重; 2)发生跳车后,要认真分析原因,消除故障后再开车;
3)开车时要认真执行操作规程,严禁发生超温、超压、环境污染事件。 2013年
一、低温甲醇洗单元E0503一条甲醇管线发生气阻事件分析
1、起至时间:
2013年5月 9 日 6时 0 分至 5 月 9 日 12时 0 分
2、详细地点:
低温甲醇洗单元换热器E0503
3、事件经过:
2013年5月9日2时,CO变换单元硫化合格,低温甲醇洗单元接原料气,3时30分接完原料气,在循环降温过程中,操作人员发现,T0501塔去E0503有一股管线物料不流动。
4、原因分析及危害:
原因:该管线有气阻现象,导致物料不流动。 危害:低温甲醇洗单元不能正常运行。
5、处理及防范措施:
处理:
6时低温甲醇洗单元停止甲醇循环,T0501塔卸压,9时压力降至0.2Mpa左右,导通该管线盲板,排净此管线物料,10时,T0501塔充压至12时到5.5Mpa,接甲醇循环降温,系统恢复正常。
防范措施:
以后在大检修后开车接甲醇过程中,应时刻注意换热器各点温度,如果发现有异常现象,及时联系相关人员进行处理。
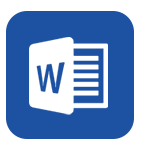