第一章
仪器主要由实验装置、测量部件、数据处理、分析和输出设备,以及针对具体对象的控制设备等几部分构成。 仪器设计与工艺制造的关系:优质仪器既是设计出来的,也是制造出来的。
虚拟仪器是以计算机为核心,充分利用计算机的软件和硬件资源,将各种仪器功能卡应用于微型计算机,使之成为计算机与仪器兼容的微型计算机。
第二章
功能材料:具有特殊的电、磁、光、热、声、化学性能和生物学性能及互相转换的功能,用以实现对信息和能量的感受、计测、显示、控制和转换的材料。
电接点是指专门用以建立和消除点接触的导电构件。 弱接点材料,主要有Ag系、Au系、Pt系和Pd系等四类。 导电高分子材料:结构型和复合型
超导材料:有些物质在一定的温度Tc(超导温度)以下时,电阻为零,同时完全排斥磁场,即磁力线不能进入其内部,这就是超导现象。具有这种现象的材料叫超导材料。 永磁材料:磁性材料在磁场中被充磁,当磁场去除后,材料的磁性仍长时保留。
永磁材料性能的指标是最大磁能积(BH)max。160高,32~80中。
稀土永磁材料,目前磁能积最大、矫顽力特高的一类永磁材料。
形状记忆材料:具有形状记忆效应的材料。通常是两种以上的金属元素构成,所以也称形状记忆合金。
形状记忆效应:将材料在一定条件下进行一定限度以内的变形后,在对材料施加适当的外界条件,材料的变形随之消失而恢复变形前的形状的现象。 按形状恢复形式可分为:
单程记忆——在低温下塑性变形,加热时恢复高温时形状,再次冷却时不恢复低温形状。
双程记忆——加热时恢复高温形状,冷却时回复低温形状,即随温度升降,高、低温形状反复出现。
全程记忆——在实现双程记忆的同时,冷却到更低温时出现与高温形状完全相反的形状。
光功能材料按用途可以分为光学材料、固体激光器材料、信息显示材料(如液晶显示器)、光纤、隐形材料等。 通信光纤的纤芯和包层构成:纤芯用高透明固体材料或低损耗透明液体制成,包层由石英玻璃、塑料等有损耗的材料制成。
吸波材料是用来对抗雷达探测和激光测距的隐形材料,所依据的原理是吸波材料能够将雷达或激光发射出的信号吸收,从而使雷达、激光探测接收不到反射信号。
红外隐形材料是用来对抗热成像仪的隐形材料,它要求材料的比辐射率低。
智能材料是指对环境具有可感知、可响应,并具有功能发现能力的材料。
金属及其合金分为两类: 黑色金属——铁和以铁为基的合金
有色金属——包括黑色金属以外的所有金属及其合金
钢中S、P是有害杂质,Si、Mn是有益杂质。 优质碳素结构钢必须同时保证化学成分和力学性能 调质钢多用中碳和中碳合金,主加合金元素Cr、Mn、Ni、Si、B等,该类钢经调制处理后具有高强度与韧性的配合,综合力学性能优秀。制作轴类、齿轮、连杆、螺栓。 高分子是指分子质量大于500的有机化合物,可分为天然高分子化合物和合成高分子化合物。
高分子材料的共同缺点是易老化。
工程塑料的特性:密度小。比强度高。良好的抗腐蚀性。优良的电绝缘性。耐磨、减摩、自润滑性好。工艺性好,一热压成形。
陶瓷弹性模量很大,比金属高若干倍。Al2O3(刚玉)陶瓷广泛用于制造高速切削工具、量规、拉丝模、高温炉零件等。 复合材料: 将两种或两种以上物理/化学性质或是组织结构不同的材料组合起来而制成的一种多相固体材料。 1纤维增强复合材料
2金属陶瓷材料(由陶瓷颗粒与金属结合的颗粒增强金属复合材料称为金属陶瓷)
电子元件引脚材料基本要求:导电性和导热性好。热膨胀系数小。机械强度高。拉伸和冲裁等加工性能好。 材料Fe-Ni基合金(如42合金)、铜基合金
选材的一般原则:1使用性能原则 2工艺性能原则 3经济性原则
第三章
工艺规程:按照一定的条件选择产品最合理的工艺过程,将实现这个工艺过程的程序、内容、方法、工具、设备、材料以及每一个环节应该遵守的技术规程,用文字和图表的形式表示出来。
作用: 1.是指导生产的主要技术文件2.是组织生产及管理工作的主要依据3.是新建、扩建工厂或车间的主要依据。 工艺规程是用于指导生产的,因此要做到正确、完整、统
一、清晰。 工艺过程:在机械产品生产过程中,直接改变生产对象形状、尺寸、性能及位置的过程。
插装元件时,主要遵循原则:先小后大,先远后近。
工序:一个或一组工人在一个工作地点,对一个工作连续完成的那部分工艺过程
安装:如果在一个工序中需要对工件进行几次装夹,则每次装夹下完成的那部分工序内内容
工位:在一次安装过程中,通过分度装置,使工件相对于机床床身变换加工位置,则把每个加工位置上的安装内容 工步:加工表面,切削刀具,切削速度和进给量都不变的情况下所完成的加工内容
走刀:切削刀具在加工表面上切削一次所完成的工步内容称为一次走刀。
制定加工工艺规程的原则和步骤:
原则:1.应满足生产纲领的要求,要与生产类型相适应。2.应保证零件的加工质量,达到图样上提到的各项技术要求3.在保证加工质量的基础上,应使工艺工程具有较高的生产率和较好的经济性。4.要尽量减轻工人的劳动强度,保证安全生产,创造良好的文明劳动条件。 步骤:1研究产品图样,进行工艺分析。2.计算零件生产纲领,明确生产类型。3.确定毛坯种类,设计毛坯图。4.拟定工艺路线5.确定机械加工余量,计算工序尺寸及公差,并制工序草图。6.研究企业现有的设备和条件,选择各工序所用设备、工艺装备、参数和工时定额。7.研究产品验收和质量标准,制定产品检验方法。 什么是基准?基准分为哪几类?
基准就是用以确定零件上点线面的位置所依据的点线面。 设计基准:设计零件时,根据零件在装配结构中的装配关系和零件本身结构要素之间的相互位置关系
工艺基准:工序基准,定位基准,测量基准,装配基准。
定位基准的选择中,粗基准和精基准的选择原则: 粗基准:1.保证互相位置要求的原则2.保证加工表面余量合理分配的原则3.便于工件装夹的原则4.粗基准一般不重复使用的原则。
精基准:基准重合原则,统一基准原则,互为基准原则,自为基准原则,便于装夹原则
什么是机械加工余量,影响工序余量的因素有哪些? 加工余量是指为使加工表面达到所需要的精度和表面,而应切除的金属表面厚度。 影响工序余量:1.上道工序的尺寸公差Ta。2.上道工序产生的表面粗糙度Ry和表面缺陷层深度Hy。3.上道工序的下空间误差ea。4.本道工序的装夹误差εb。
什么是尺寸链?说明尺寸链中组成环和封闭环的含义。 在零件的加工或产品的装配过程中。经常遇到一些相互联系且按一定顺序排列着的,封闭的尺寸组合,这些互相联系。又按一定顺序排列着,封闭的尺寸组合。被称为尺寸链。 组成环:直接影响封闭环精度的各环,称为组成环。 封闭环:在零件的加工或产品的装配过程中,间接形成的,其精度是被间接保证的各环,称为封闭环。
工件装夹的含义是什么?在机械加工中有哪几种装夹工件的方法?简述每种装夹方法的特点和应用场合。 装夹有两种含义,即定位和夹紧。定位是指使工件在机床或夹具中获得正确位置的过程;夹紧是指工件定位后将其固定,使工件在加工过程中保持定位位置不变的操作。 装夹有三种方法:1.直接找正装夹:工件装到机床后,用百分表(或千分尺)或划线盘上的划针目测校正工件位置,以保证被加工表面的位置精度,然后夹紧工件
2.划线找正装夹:这种装夹方式所需设备比较简单、适应性强,但生产效率均较低,因此多适用于单件、小批生产中的复杂铸件或铸件精度较低的粗加工工序
3.夹具装夹:在夹具上装夹工件时,由工件上的定位基准与夹具定位元件的工作表面保持接触来实现工件的定位。
定位误差:由于工件在夹具或者机床上定位不准确而引起的加工误差。
来源:一是由于工件的定位表面或夹具上的定位元件制作不准确引起的定位误差,称为基准位置误差。二是由于工件的工序基准定位基准不重合而引起的定位误差,称为基准不重合误差。
工件以外圆定位,以工件下母线为工序基准时,定位误差较小。
常用夹紧机构: 1斜楔夹紧机构,有增力作用 2螺旋夹紧机构,自锁性能好 3偏心夹紧机构 4定心夹紧机构 5联动夹紧机构
第四章
表面贴装SMT和通孔组装THT技术的根本区别: 一是所用元器件外形不相同;二是PCB焊盘表面,前者焊盘上没有孔、而后者焊盘上有通孔;三是前者是“贴装”,即将元器件贴装在PCB焊盘表面,而后者则是“插装”,即将长引脚元器件插入PCB通孔内;四是前者是预先将焊料锡膏涂放在焊盘上,贴装元器件后一次加热而完成焊接过程,而后者是通过波峰焊机利用熔融的焊料流,实现升温与焊接。
电子组装中常用的焊接技术有哪些? 1.手工焊接:在企业中,焊接SMT元器件主要依靠自动焊接设备,但在维修电子产品或者研究单位制作样机时,检测,焊接SMT元件常用手工焊接。
2.浸悍:是最早应用在电子产品批量生产中的焊接方法,现在还在一些小型企业中使用。
3.波峰焊:分为两种:单波峰焊和双波峰焊电子产品THT批量生产中的焊接方法是单波峰焊;SMT批量生产中的焊接方法是双波峰焊。
4.再流焊:再流焊目前主要用于表面组装技术中片状元件的焊接。
塑料零件的成形方式:
1.注射成形 2.压塑成形 3.挤出成形 4.压延成形
设计塑料零件时,在结构工艺性上应注意问题: 1.形状 2.壁厚塑件的壁厚应适当和均匀 3.脱模斜度 4.加强筋 5.薄壁件的底部和边缘 6.圆角 7.孔 8.螺纹 9.镶嵌件
精密冲压的基本工序可分为分离工序和成形工序
第五章
仪器参数与特性:
1示指与示指范围 2刻度与分辨力 3测量范围 4灵敏度与鉴别阀 5仪器的稳定性与漂移 6滞差 7零值误差和基值误差
影响仪器精度的主要因素:
1.仪器原理误差(在仪器制造过程中,由于采用了近似的理论、近似的数学模型、近似的机构和近似的测量控制电路等近似方案,所以产生了原理误差)2.形状特性 (措施:合理的分配误差和确定制造公差、正确应用仪器设计原理和设计原则、合理的确定仪器的结构参数、合理的结构工艺性、设置适当的调整和补偿环节 ) 3.运动特性 4.外部干扰特性 加工精度是指零件加工后的实际几何参数(尺寸、几何形状、表面相互位置)与理想几何参数相符合的程度。 加工精度包括:尺寸精度、形状精度、位置精度
影响加工精度的工艺因素:
1.方法误差2.机床误差(主轴回转误差、机床导轨误差、机床传动链误差)3.夹具误差和磨损 4.刀具误差和磨损5.工艺系统的受力变形6.工艺系统的受热变形(热源种类、刀具的热变形、工件热变形对加工精度影响、机床热变形对加工精度影响、减少工艺系统热变形的措施)7.工件安装误差调整误差和测量误差(工件安装误差、调整误差、测量误差)8.工件残余应力引起的变形(毛坯制造和热处理过程中产生的残余应力、冷校直产生的残余应力、切削加工产生的残余应力)
主轴回转误差又分为轴向窜动误差、径向圆跳动误差和角度偏摆。
机床主轴系统的回转精度对加工件表面的形状精度有直接影响。
误差敏感方向是指加工中刀具接触处工件法线的方向。
在具有丝杠-螺母副传动的机床中,传动链中最后一个与丝杠同步旋转的齿轮对加工精度影响最大,因为它的传动误差将以1:1传给丝杠。
由机床、夹具、刀具、工件所组成的工艺系统是一个弹性系统。
工艺系统的刚度在沿工件轴向的各个位置是不同的,所以加工后工件各个横截面上的直径尺寸也不相同,造成了加工后工件轴向的形状误差。
加工误差分类 举例:
1.系统误差 刀具的的磨损误差也是与时间相关的变值系统误差2.随机误差 毛坯误差的复映
工艺系统的受热变形:工件热变形、机床热变形、刀具热变形
热源种类:1切削热 对工件加工精度的影响最直接 2摩擦热 导致机床产生热变形的主要原因,因而破坏了工艺系统原有的精度 3辐射热及环境温度
Cp>1,只能说明工艺足够,不代表全部合格。
第六章
研磨过程中磨粒的滚轧和微切削作用
特种加工有别于传统切削加工的特点:
1.加工中工具不与工件接触,没有切削力的影响,工具硬度可以低于工件材料的硬度。 2.加工能量容易控制。
3.便于实现特殊形状零件加工即微细加工。 4.机床运动简单。
电火花加工又称放电加工或电蚀加工。
电火花成形加工的原理是基于工具和工件之间脉冲性火花放电时的电腐蚀现象来腐蚀多余的金属,以达到对零件的尺寸、形状及表面质量预定的加工要求。 电火花切割加工与电火花成型加工相比不同点( 或线切割特点):1.以细金属丝作为电极,不需要制作特定形状的电极,降低成本。 2.通过计算机控制,很容易加工出形状复杂的零件。 3.轮廓加工所需加工余量少,能有效节约材料,特别是对贵金属材料,能加工微细异型孔,窄缝的工件。 4.加工中电极丝往复移动,损耗小,对加工精度的影响可以忽略,特别是用低速走丝线切割的工件。 5.电火花线切割不能加工型腔,盲孔类零件。
电解磨削与机械磨削有何区别?
电解磨削即是电化学机械复合加工的另一种,电解磨削是利用电解腐蚀和机械磨削作用相结合的方法对零件进行加工。 影响材料放电腐蚀的主要因素:
1极性效应:材料相同的两个电极电蚀量不一样的现象 2脉冲参数3金属材料的热学常数
4工作液:电火花加工一般在液体介质中进行,液体介质通称工作液。5其他因素
电解加工的特点:
可以加工高硬度高强度的各种金属材料,并且可以形状复杂的型面。生产率高。对于型孔、型面、型腔可以一次进给成形。
电解加工的基本原理:
利用金属在电解液中发生电化学阳极溶解而去除金属材料的一种加工方法。
电解磨削是利用电解腐蚀和机械磨削作用相结合的方法对零件进行加工,是电化学机械复合加工的一种,另外还有电解珩磨和电解研磨。 超声波加工原理:
超声波加工是利用工具端面做超声品振动,通过磨料悬浮液加工脆性材料的一种成形加工方法。
超声波加工设备:
1超声波发生器 2超声振动系统(换能器、变幅杆、工具) 3超声波加工机床本体 4研磨悬浮液冷却及循环系统 超声波加工特点:
1加工范围广 2切削力小、切削功率消耗低 3工件加工精度高、表面粗糙度低 4易于加工各种复杂形状的型孔、型腔和成型表面等 5工具可用较软的材料做成较复杂的形状 6设备结构一般比较简单,操作维修方便。
第七章
数控机床控制方式分类:
1开环控制系统 2半闭环控制系统 3闭环数控系统 什么是柔性制造系统(FMS)及其主要特征
指一种主要用于多品种中、小批量或批量生产的制造自动化技术。 特征: 指制造系统对系统内部及外部环境的一种适应能力,也是指制造系统能够适应产品变化能力。 柔性制造系统由哪几部分组成?它们的主要作用是什么?
组成:多位数控加工系统、自动化的物料储存系统和计算机控制的信息系统。作用:主要包括生产调度理论与算法的研究;计算机通信及数据库技术的研究。 FMS(柔性制造系统)的特点:
1具有很强的柔性制造能力 2提高设备利用率 3减少在制品数量 4产品质量提高,加工成本降低。 5减少直接生产工人,提高劳动生产率。6FMS可以逐步的实现实施计划。 工业机器人的基本形成和结构特点:
工业机器人一般由机械系统、控制系统、驱动系统、智能系统组成。
特点:1.工业机器人的操作可以简化成各连杆首尾相连、末端开放的一个开式连杆系,结构刚度差。2.在组成操作机的开式连杆系中,每根连杆都具有独立驱动器,不同连杆之间运动没有依从关系,操作机的运动灵活但复杂。3.连杆驱动转矩在运动过程中的变化规律比较复杂,连杆的驱动属于伺服控制型,对系统刚度、间隙和精度有高要求。4.连杆的受力状态,刚度条件和动态性能都随位置改变而改变,容易发生振动或不稳定。 工业机器人分类:
1按自动化功能层次分类:专用机器人、通用机器人、示教再现机器人、智能机器人
2按结构形式分类:直角坐标型机器人、圆柱坐标型机器人、球坐标型机器人、关节型机器人
3按控制类型分类:伺服控制(固定程序控制)机器人、非伺服控制(可编程控制)机器人
4按自由度数目分类:无亢余度机器人、有亢余度机器人 5按驱动方式分类:电力驱动机器人、液压驱动机器人、气压驱动机器人、复合驱动机器人 什么是快速原型制造技术及特征:
快速原型制造技术借助于计算机、激光、精密传动和数控技术等现代手段,将CAD和CAM集成于一体,根据计算机上构建的三维模型,在短的时间内直接制造出产品样品,无须传统刀具、夹具和模具,整个过程中无人干预。 特征:1.高柔性 2.成形的快速性 3.全数字化的制造技术 4.无切割、噪声和振动等,有利于环保。
快速原型制造工艺主要有哪几类型?举例说明主要应用领域。
1.光固化成形工艺 2.叠层实体制造工艺 3.选择性激光烧结工艺 4.熔融、沉积制造工艺 5三维印刷工艺 6弹道微粒制造工艺 7三维焊接工艺 应用领域:1.RPM技术在新产品开发的应用 2.基于RPM技术的快速模具制造 3.RPM技术在医学领域中的应用 4.RPM技术在铸造领域中的应用 快速原型制造工艺主要有哪几类型及主要应用领域: 1.光固化成形工艺 2.叠层实体制造工艺 3.选择性激光烧结工艺 4.熔融、沉积制造工艺 5三维印刷工艺 6弹道微粒制造工艺 7三维焊接工艺
应用领域:1.RPM技术在新产品开发的应用 2.基于RPM技术的快速模具制造 3.RPM技术在医学领域中的应用 4.RPM技术在铸造领域中的应用
第八章
微机电系统(MEMS)也称为微系统或微机械,是利用集成电路制造技术微细加工技术,把电路、微结构、微传感器、微执行器等制造在一个芯片上的微型集成系统。 微细加工可分为微米级、亚微米级和纳米级微细加工 按基本加工类型可大致分四类:1分离加工。如分解,蒸发,溅射,破碎等。 2接合加工。如蒸镀,淀积,掺入,生长,黏结等。 3变形加工,如塑性变形加工,流体变形加工。 4材料处理或改性,如一些热处理或表面改性等。 光刻技术: 1匀胶 2前烘 3曝光 4显影 5后烘 6刻蚀 体微细加工技术指通过刻蚀等方法去除部分基体或衬底材料,从而得到所需元件的体构形
表面微细加工技术指那些能够制造微小尺寸元器件或薄膜图形的方法 LIGA加工技术 基本工艺过程 :
1深层同步辐射X射线光刻: 利用同步辐射X射线透过掩膜,对固定于金属基底上的厚度高达几百微米的X射线抗蚀剂层进行曝光,然后将显影制成初级模板。
2电铸成形:电铸成形是根据电镀原理,在胎膜上沉积一定厚度金属以形成零件的方法。
3注塑:将电铸制成的金属微结构作为二级模板的模腔,形成微结构塑性件,从金属模中提出,也可用已形成的塑性件作为模板再进行电铸。
微细加工技术中的刻蚀工艺可分为:干法和湿法刻蚀 硅体刻蚀和面刻蚀加工区别:体刻蚀加工对基体材料进行加工,面刻蚀加工不对衬体材料进行加工
第九章
装配精度,装配精度与零件的精度有何区别与关系
相互位置精度,相对运动精度,相互配合精度
零件的精度特别是关键零件的精度会直接影响相应的装配精度,但完全由零件的制造精度会给加工带来困难,降低加工效率所以要采取一定的保证装配精度的方法。 保证装配精度的方法 各适用于场合:
一、互换装配法:1.完全互换装配法:常用于高精度的少环尺寸链或低精度的多环尺寸链,只要满足零件经济精度要求就优先考虑2.大数互换装配法:使零件加工容易,降低成本
二、选择装配法 1.直接选配法:方法简单,装配精度高但无法阻止大批量流水装配2.分组选配法:在大批大量生产中,对于组成环数少而装配精度又高的部件,常采用分组装配法3.复合选配法:装配速度快、质量高、能满足一定生产节拍的要求。
三、修配法:用在单件小批量中,尺寸链环数较多、封闭环精度要求又很高的场合,广泛应用于精密仪器装配。
四、调整法:适用于尺寸链长,封闭环精度较高的机构装配,在精密仪器中广泛应用。
装配尺寸链如何构成?装配尺寸链封闭环是如何确定的?它与工艺尺寸链的封闭环有何区
与装配技术要求有关的零部件因素(尺寸)与装配技术要求构成的。
在加工、检测和装配中,最后得到或间接形成的尺寸称装配封闭环。
在工艺工程中,由同一零件上的工艺相关的尺寸所形成的尺寸链称为工艺尺寸链。工艺封闭环一定是工艺过程中间接保证的尺寸;封闭环的公差值最大,等于各组成环公差之和。
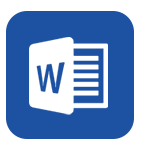