推荐第1篇:制程检验作业指导书
制程检验作业指导书
过程指导
首检检验
● 车间主任及班组长按工艺规范制作首检样品,并自检
● 制程质量检验专员按照产品生产工艺、工序规定,全面检查首检样品 ● 召开产前会,提出质量问题,协商对策
首三件检验
● 前期生产出的三件成品,全面检验,并填写记录表
● 主管审核后,班组长根据首三件审核意见,督导生产
● 生产首三件时,做好自检和互检工作
巡回检验
● 对各班组执行巡回检验,根据生产工艺规定、产品制程检验规定进行判定 ● 将检验结果记录于日报表上,及时反馈给制程检验主管
● 每日分上午、下午、加班时段进行巡回检验
● 在制的半成品经成品检验专员查验合格后,方可转入下一道工序或流程 ● 返工由制程检验专员重检合格方可放行
制程不良品的处理
● 检验过程中,发现不良率超过5%且无法直接加工改造成良品者,按不合格品控制程序处理
● 对不良品加以明确表示和控制
注意事项
⊙自检过程中,将良品、不合格品分开放置
⊙对不易测量及需要特殊检验技能的产品特性予以特别注意
⊙以适当频次对制程参数进行监控和验证
⊙认为可能会发生重大质量事故时,立即上报上级主管处理,不得延误
推荐第2篇:制程检验作业指导书
制程检验作业指导书
过程指导
首检检验
● 车间主任及班组长按工艺规范制作首检样品,并自检
● 制程质量检验专员按照产品生产工艺、工序规定,全面检查首检样品 ● 召开产前会,提出质量问题,协商对策
首三件检验
● 前期生产出的三件成品,全面检验,并填写记录表
● 主管审核后,班组长根据首三件审核意见,督导生产
● 生产首三件时,做好自检和互检工作
巡回检验
● 对各班组执行巡回检验,根据生产工艺规定、产品制程检验规定进行判定 ● 将检验结果记录于日报表上,及时反馈给制程检验主管
● 每日分上午、下午、加班时段进行巡回检验
● 在制的半成品经成品检验专员查验合格后,方可转入下一道工序或流程 ● 返工由制程检验专员重检合格方可放行
制程不良品的处理
● 检验过程中,发现不良率超过5%且无法直接加工改造成良品者,按不合格品控制程序处理
● 对不良品加以明确表示和控制
注意事项
⊙自检过程中,将良品、不合格品分开放置
⊙对不易测量及需要特殊检验技能的产品特性予以特别注意
⊙以适当频次对制程参数进行监控和验证
⊙认为可能会发生重大质量事故时,立即上报上级主管处理,不得延误
推荐第3篇:制程检验求职简历
制程检验求职简历
个人资料
姓名:性别: 年龄:
籍贯:国籍: 婚否:
民族:身高: 体重:
电子邮箱:手机号码:
简历求职意向
求职职位:
IpQC(制程检验)
工作类型:
工作经验/年:
工作性质:
全职
期望薪资:
2000--3500
求职地区:
广东省
工作履历
xx保安制品有限公司 起止年月:
公司性质:
国营企业
担任职位:
产品检验员
工作描述:
1、按照相关标准、要求和检验方法、检验程序,对锁具的物料和锁具的产品进行质量检验。
2、负责公司的产品质量,做到出厂产品质量合格率≥99%。
3、做好质量记录,对所检物品的质量情况进行统计、分析上报。
离职原因:
寻找更好的发展
语言能力
外 语:
英语一般
粤语水平:
良好
第二外语:
无
国语水平:
良好
教育背景:
毕业院校:
专业:
主修课程:
机械制图、计算机绘图(cad)、电子电工、工程力学、工程材料、机械设计原理、三维造型(ug)、冲压模具设计与制造、塑料模具设计 数控加工工艺与编程,现代制造(cam)、现代企业管理、精密与特种加工、模具制造工艺学。
简历自我评价
工作中,能够同过与各部门的工作沟通,很好地完成各布置的工作任务;从问题的出现,提出解决方案,到验证方案可行性,落实最终执行方案;有针对地进行零件的修改或者重新设计,跟进新样件试制-试装-落实全过程;并能够熟练地绘制零件图纸,且熟练使用AutoCAD、pro/E、CAXA等绘图软件;同时,也能够熟练使用办公软件Office对日常办公文件进行编辑。在校期间,对机械设计制造,模具设计制造,电子电工,力学,控制原理等等多方面都有系统学习,所以有扎实的理论基础。毕业学期,运用所学知识,结合AutoCAD、pro/E、有限元分析软件Dynaform等相关软件,完成课题为《镁合金手机外壳冲压模具设计及成形过程研究-第一工序》的毕业设计。
求职自我介绍
有较强的组织协调能力;能客观的处理各种问题;具备高度的责任心和敬业精神、有良好的团队协作精神和工作热情; 对计算机的基础知识掌握较好;为人友善,性格稳重,有清晰的思路和很强的自学能力,能较快融入集体。
推荐第4篇:节能灯制程检验规范
一,制程检验分类:首件检查;巡回检查;最终抽检;测试全检.
首件检查:以下生产工序开始生产产品或半成品需进行首件检查; 插件,装配.(生产完成首件的制作,IPQC检查)
巡回检查:在每个组生产的产品或半成品或加工半成品每二个小时需进行巡回检查一次;(IPQC每人每工位每工序从前往后或从后往前全部巡检检查)
测试全检:指调试,装配,包装巳生产好的成品或半成品进行全检全部点亮测试.(由生产作业员或生产QC完成) 最终抽检:指一个组对于一个产品或一个半成品批量生产完成的(并巳经生产QC全检点亮测试的)产品的抽检,每二个小时抽检30--50PCS以上.
扩大抽检:在巡回检查和最终抽检时发现有不良品:≥1PCS的一律需要扩大抽检以验证此问题. 二,检验工位设置:
1,
首件检查:每一个制单的某一款产品在插件和装配生产的开始都需要做首件检查,首件确认OK后后续产品才可以开始批量进行量产.(如果NG,需要重新做首件检查才可以.)
2,
巡回检查:每款产品首件检查OK后,进行批量生产过程中要进行不停的每二个小时一次的巡回检查,IPQC要从生产线最前的第一个工位开始,每个工位一个一个的往后进行检查;对照产品规格书/作业指导书等相关资料标准对每个工序每个工位的生产产品的品质情况进行检查.每工位至少抽检5-10PCS;重要的工位必须抽检10PCS以上; 3,
测试全检:调试,装配,包装所有生产的产品或半成品在完成的最后必须由生产QC进行全检点亮测试;
4,
最终抽检:每一个组每一种产品或每一种半成品生产完成的最后要进行抽检(检查的是生产QC巳经全检点亮测试过的产品);
5,
扩大抽检:=巡回抽检和最终抽检;照巡回抽检和最终抽检数量再检验一次. 三,检验标准:检验标准资料和检验标准内容
A:检验标准资料:
1,
作业指导书;2,产品规格书;3,流程图;4,包装资料;5,钢板资料;6,制程检验规范;7,承认书;8样品;9,制造单;10,合约评审及客户资料;11,工程变更及相关联络函;
(A:处内容最多只能合并为三项,否则就会乱,这么多的资料就是神仙也理会不过来,看了这里忘了那里,还有一些需要联系起来的更是会理不清,斩不断,搞不清所以原;因为在生产过程中有很多部门和人员都需要来查证这些资料,必定会因人的原因和资料多的原因,弄出杂乱的问题来.只有坏处没有什么好处.最好只有产品规格书/包装资料/作业指导书就可以了,但这三项一定要清楚明白包括所有需要显示的资料内容,否则就没有意义.) B:检验标准内容在没有客户和地区标准要求时以国标要求为准)
1,
基本内容:低压/额压/极压开关三次以上正常;可以正常起动;正常点亮;无闪烁;变暗; 2,
电性参数:照客户的要求和所使用地区的要求;
3,
功率要求:A, D, B 档产品功率要求在±10%; C1 C2档产品功率要求在+10%/-15%; G, 档产品功率要求在+10%/-30%(正常点亮15分钟以后测);
4,
光效/光通量:满足客户规定的要求(点亮15分钟以后测); 5,
耐压:高压测试1500V3秒10mA可以通过无击穿;
6,
漏电流:以正常使用电压的1.11倍,照耐压方法接线测试,漏电流小于等于1.0mA. 7,
扭力:灯头扭力可以满足国外客户产品≥3N.M;国内客户产品≥2.5N.M;
8,
爬电距离:交流与直流部分的走线布线路径和焊点间距,在有绿油或绝缘漆掩盖时应为≥1.5mm;在没有绿油和绝缘漆掩盖时应为≥2.5mm; 7,功率因素:在客户要求的范围内; 8,额定电压:在客户要求的范围内; 9,额定电流:在客户要求的范围内;
四,检验项目:巡回检查——分工位工序抽检(或者单个的作业人员) 最终抽检——和最终产品的抽检(生产QC巳全检测试OK的产品);
五,判定标准:1,每工位工序不设固定的判定标准,当发现不良品和不良情形立刻改善并对巳生产好的产品进行隔离返工处理;
2,
最终抽检的不良的判定标准是(所有不良品除掉属于零配件来料不良的内容) A:电性≤2%判OK;≥2%的判NG;
(其中单个电子元件(来料不良除外)引起的不良情形的比率:≤1%判OK;≥1%的判NG;) B:外观:严重的≤1%判OK;≥1%的判NG; 轻微的≤3%判OK;≥3%的判NG;
C:整体的判定:严重的≤3%判OK;≥3%的判NG;(含外观和电性) 轻微的≤5%判OK;≥5%的判NG;(含外观和电性) 六,检验流程;检验产品流程和不良品情形处理流程. A:检验产品流程:
1,
生产开始生产某一种产品前在插件和装配必须照工程样品和产品规格书等内容制作4-10PCS的产品,自行照作业要求检验OK后送品管部IPQC进行首件确认检查;品管部确认首件检验OK后生产组别才可以开始批量生产后续产品;
2,
在每处组的IPQC必须照工艺和工位按排一个作业员一个作业员的进行检查;确认符合规定的操作要求; 3,
每组重点工位控制:a,准备:印字;灯管漏气;打胶粘灯管; b,电感:电感绕制;电感测试;
c,插件:每种零件的工艺要求;浸锡;切脚;过波锋;检焊; d,调试:测试;刷绝缘漆;
e,装配:绕灯丝;装面壳吻合;装(灯头)输入线;焊(灯头)输入线;锁压灯头;点亮测试;装输出线; f,老化:上下灯;
h,包装:点亮测试;清洁;外观检查;漏气控测;印字及标贴检查;装盒及装箱检查;
4,
生产场所任何人从事的任何工作和动作,品管部IPQC都有责任和义务自动的进行检查,以发现巳产生了的问题或者隐含的将要产生的问题,予以改善纠正和预防. B:不良品情形处理的流程:
1,
当超过第五项允收水平被判定为批量不合格的产品;IPQC首先开具《制程不良状况联络单》通知到生产部,工程部,品管部上司,副总经理
2,
是电性不良严重且超出允收水平的一律通知生产部门先停止生产;
3,
由生产部把不良的产品分开隔离开来,由品管部IPQC贴上拒收标签与良品进行区分;
4,
由工程和生产部门确认更改方案措施出来,由副总经理签名批准以后才可以开始后续产品的生产. 5,
发现的单个和少量的不良品挑选出来隔离;放置在红色的不良品筐中,由维修人员返修处理; 6,
不良品和未经整改的不良品绝不可以流入下一个工序. 七,检验产品内容:
1,
外观:与订货单,产品的要求,样品等一致;
2,
规格型号尺寸:与订货单和产品规格书中的要求一致,国标标准,承认书等一致; 3,
材质:与订货单和产品要求,产品规格书,承认书,样品等一致; 4,
组装性能牢固度:实际组装无异常;与样品等一致;松紧适中;
5,
电性参数:实测与订货单和产品要求,产品规格书,承认书,样品等一致; 6,
电性协配:组装和与相关的其它配件组合进行功能测试无异常;
7,
包装印字及标示:照包装资料内容,字体,图案,尺寸,颜色,排版等检验一致; 8,安全性的要求:此产品物料不会伤及接触它的人和物(如锋利的边缘) 9,其它:依产品和客户的要求检验一致.
八,报表的记录方法内容照报表格式的相应内容进行检测和记录;
九,标示:照最后的处理结果和判定结果进行相应的标示.OK品由生产自行作产品标示;NG不良品由品管部IPQC作拒收标签贴在生产部的产品标示上.
推荐第5篇:注塑成型制程检验规范
成型制程检验规范
一.目的
规范制程检验,正确监控制程以预防品质异常,确保产出品质及满足客户要求。
二.适用范围
本规范使用于塑件成型所有产品。 三.定 义
无
四.权 责
4.1 工程部: 4.1.1.负责提供生产作业标准,技朮支持; 4.1.2.负责提供标准生产工时。
4.1.3.制程中生产重点参数的提供与变更。
4.1.4.与制程相应的文件、规范、条件及标准的编制。4.1.5.协助分析检讨改善制程异常。 4.2 企划部: 4.2.1.负责提供生产计划表,跟进提供成型生产所需原料及零件给产线生产。 4.2.2.负责代工客户的订单处理,物料跟进及制定《出货通知单》及出货明细。 4.3 塑件品质部: 4.3.1.负责制定各产品品质检验规范。
4.3.2.制程中各项重要参数的稽核与确认,确保产品满足检验规范/规格及客户需求。4.3.3.制程中的首件检验,巡回检验,最终检验。 4.3.4.制程异常初步确认,不良品的确认。 4.3.5.产品质量数据之统计,分析,并传达相关单位。 4.3.6.矫正与预防措施效果的跟踪与效果确认。 4.4 其它单位:
4.6.1 协助生产过程中相关事项处理,保证生产顺利进行。 五.作业流程
企划成型单位品管生产计划物料投入成型模具等周边设备安装/成型条件设定NG自主检查OK初件检查OK按SOP作业OKNG自主检查NGNG记录/分析/调试/停机/加工OK制程巡检OK包装作业最终检验不合格品处理/预防与矫正措施入库NGOK出货
六.作业内容
6.1 获取产品制作所需信息
6.1.1.产品在生产前,生产各相关人员必需获得以下工程资料方可生产:产品工程图、BOM表、作业指导书、作业流程及包装规范。6.1.2.品管检验人员在产品生产前必需获得该产品的SIP、蓝图、评估报告、样品等资料,以作为检验该产品的依据。
6.1.3.以上工程资料及检验资料必需为文控中心正式发行的资料。
6.1.4.生产必需依各相关产品的工程资料要求进行产品制造。若生产条件或生产流程需要任何变更时, 由工程填写工程变更通知单,经相关部门签核同意后,由文控中心统一变更受控发行,具体操作参照《文件资料管理程序》。
6.2 生产计划管制
6.2.1.企划部生管员依客户或各厂区需求制订每周生产计划。
6.2.2.企划部生管员需依生产计划跟进采购或供应商按时供给成型原料,并由生管员开出《发料单》,通知货仓备料发料,生产领料。
6.2.3.生产接到企划课的每周生产计划后,由生产课长或组长对每周生产计划审核并作生产排配,当不能达成时,应及时反馈企划课,由企划课协调解决。
6.3 原料投入
6.3.1.生产单位依据发料单和生产计划表到仓库领料,原料生产前需先对原料进行烘烤,烘烤温度和烘烤时间参照《标准成型条件表》进行。
6.3.2.生产塑胶料次料添加比例参照《BOM表》或《塑件产品次料添加标准》进行。每次加料/拌料前需记录在上,并通知品管签名确认。
6.3.3.成型在加料或拌料前,需先清理干净之前料筒内余料,预防余料和加入原料颜色、成型温度等特性不一致混用,造成产品混色、料花、粘模等异常。
6.4 成型模具等周边设备连接/成型条件设定。
6.4.1.成型周边设备安装:
A、上模安装:查找产品对应之成型模具,依《标准成型条件表》规定将模具安装在合适吨位之机台上。
B、依《标准成型条件表》连接模具所需用的标准模温(常温水、冷冻水、模温水)。 6.4.2.依照《标准成型条件表》调试自检OK后,由成型课技术员开出《成型首/终件记录表》,品管检验OK后再开机生产。
6.5 初件检验
6.5.1.IPQC接收到成型技术员送检的《成型初/终件记录表》和首件样品后,应在2小时内给出判定结果。
6.5.2.初件检验过程当发现成型条件记录超出《标准成型条件表》时,应通知生产&工程检讨标准成型条件是否合理,。如工程评估可进行变更,则跟进工程对此标准成型条件发出工程变更通知单,并跟进产品外观和尺寸是否符合产品标准。
6.6 制程作业员作业
6.6.1.生产前IPQC及现场人员应事先确认相关工程数据(蓝图、承认书、包规、作业指导书、检验规范等)是齐全及版次是否正确,确认OK后方可生产,并且各个工站应悬挂生产该机种的作业指导书(如果有太多相同工序,最多可两人共享一份作业指导书)。6.6.2.初件检验OK后机台操作员开始生产同时进行自主检查,并将结果记录于成型生产日报表上,挑出不良品集中放置并交线/组长处理,制程IPQC巡回检查各机台并将检验结果记录于《成型制程产品巡回检查记录表》和《成型制程尺寸巡回检查记录表》上。 6.6.3.各工序作业人员应严格按作业指导书内容的要求执行作业。
6.6.4.制程出现异常时IPQC应将不良现象填写制程质量异常追踪单,由品管组长及生产线/组长确认是否调机或修模,生产制程中若有发生重大质量异常时均需记录于《成型产品制程质量履历表》内以供后续作业参考。
6.6.5.为保证生产现场物料摆放合理及生产机台清洁,作业员应做好“5S”工作。6.7 包装作业
6.7.1.机台操作员依据包装规范核对自检OK的产品进行包装作业,包装前需确认包材无误后才可进行,以免误用:逐层摆放产品需重点确认每层摆放数量、层数、一箱总数量等不可错误;散装产品自检合格后,用电子称根据标准重量100%称重,并将称得重量书写在外箱标签上,确保重量100%准确,预防多装、少装不良情况。
6.7.2.一台机生产两种以上产品,包装过程要注意区分隔离,避免混装/标签错误等不良产生。
6.8 制程检查
按规定的时间间隔或当生产条件发生变化时(如材料,设施,人员的变化等),应对制程进行检查,确保对影响制程能力的变化作出及时的反应。
1.初件检查
制造单位作业人员、主管或品检人员,依据检验规范,于每日或每批开机、修模、设备维修、调机、换料等情况, 进行首件检验,并将检查结果记录于《成型首/终件检查记录表》、成型日报表。当生产条件、参数设定发生变更时,应重新记录超出规格的要重新评估相关部门同意后在文件中心统一变更发行。 2.制程自主检查
制造单位依据制造作业规范或检验规范要求作业人员针对制程所使用的设备与治具、在制品及作业条件、外观、结构、参数......等管制项目, 作好自主检查,并将检查结果记录于《成型生产日报表》、《成型条件记录表》, 直接主管应不定期查核作业人员是否依作业规范要求确实执行。 3.生产互检
每一作业工站作业人员对本工站作业手法,产出半成品均要进行自检,下一工站人员除对本工站要求检验事项做好自检外,还应对上一工站流下之部品均要进行仔细检验,发现不良知会前工序改善,防止不良流出。 4.制程巡回检查
制程检验人员依据检验规范和规格要求,针对重要制程之在制品检验其质量是否符合规格, 并将检验结果记录于《成型制程产品巡回检查记录表》、《成型制程尺寸巡回记录表》等管制表。 5.禁用物质管控
协创成型产品对ROHS规定之六项元素管控标准为:Cd≤50、Pb≤50、Hg≤50、Cr6+≤50、PBB ≤800、PBDE ≤800。每款产品1月送测1次,由IPQC填写《化学测试申请单》送环境检测机构测试,客户有特殊要求,要满足客户特殊要求。 6.入库检验
针对各制程之部品必须依据检验规范、抽样计划、相应质量缺点判定基准或检验样品实施检验,确定符合产品规格后方可进行下一制程或入库,详细参照《抽样检验计划》。
6.9 入库作业
生产单位填写入库验收单并把IPQC检验合格产品统一摆放在OQC待验区,待入库检验,OQC检验合格则入库,不合格则退回生产处理,并由OQC开出品质异常处理单分析原因、制定有效对策改善。 6.10 成品出货:
成品出货注意事项如下:
6.10.1.企划生管员每日下午18:30前资讯客户段出货需求,打印第二天出货通知单送交品管、成型、仓库等单位知悉,并打送货单交企划仓管员备料。
6.10.2.成型课依据《出货通知单》之先后顺序,了解货仓库存情况,紧急物料优先安排生产。出货前不能完成要通知生管员协调处理。
6.10.3.出货1小时前仓管员依送货单备货,并通知品管确认,品管课依出货通知单上不同客户之需求,附相关出货检验报告、SGS化学物质测试等报告。
6.11、不合格品、制程异常之处理: 6.11.1.异常品及异常嫌疑品处理:
1.异常发生后,应立即通知制程检验人员或线组长确认处理,属于来料问题交品管IQC处理,属制程设备问题则由成型管理通知设备管理员、技术员、模具或工务进行处理。2.异常发生后,需检查相关时间段产品(现场、库存、客户段)等是否有类似异常,如有对产出品按照6.11.1.中
3、
4、
5、6项规定办理。
3.产品制造过程中之不合格品若属于外观不良则由QE签限度品进行挑选作业。4.对于结构性问题,需要加工处理的,需由工程部门门制作重工流程,成型课进行加工处理,品管跟进成型加工,确保产品品质。
5.产出异常品虽不符合公司验收标准,但经验证或客户同意的状况下予以允收入库,如需特采时由责任单位提出特采申请单,经品管、制工及相关单位一致同意并经事业处最高主管或其授权主管核准后方可特采。
6.报废处理:当产品测试环境管理物质超标,必须进行报废处理;当不合格品在质量特性上有影响其主要功能或不合格品不适用于重加工或特采时,得办理报废:产品或物料报废由责任单位填写报废单,经责任部门主管确认,品管/工程单位确认不良无法修复或重工时,再经事业处最高主管或其授权主管核准后方可报废。 6.11.2.制程异常定义
A、制程重要工站之不良率超出设定管制界限(单项不良超过1%,总体不良超过3%)。 B、制程发生突发性变异,导致产品质量不良。
C、品管人员制程稽核发现管制项目超出已明确订定之条件/参数。 D、制程中发现的潜在性质量隐患。
6.11.3.首件检验异常,则在首件单上写清楚不符合项,将首件单和首件样品一起退给成型课技术员分析原因改善。改善后自检产品OK再送检IPQC进行重新确认,IPQC确认合格后通知成型开机生产。
6.11.4.制程自主检查异常,成型包装或全检挑选的异常品,需记录在《成型生产日报表》上,单项不良超过1%或总体不良超过3%时,需通知技术员/全技员分析原因改善,对不能及时解决的(2H内),由IPQC开出品质异常处理单,由成型单位书面分析异常原因,相关单位协助改善。6.11.5.设备及模(治)具异常处理
1.制程中生产设备发生损坏造成质量不良或生产停顿时,作业人员应立即通知工程或工务/生技等责任人员进行故障排除,或请制造厂商派人前来维修。
2.设备修理完毕后,应将设备维修记录填写在\"设备维修记录表\"中,如维修项目涉及产品质量时,应执行初件检查确认合格后,并将结果记录于维修记录表中,方可继续生产。3.在模(治)具生产作业过程中, 发生模(治)具不良导致零件、产品质量不符规格时,应立即进行故障排除或停机换模或下模修理。
4.模(治)具修复或更换完毕后, 应将模(治)具发生不良事项填入模(治)具维修记录表或成型生产日报表。
5.品保或制造单位须对修模后之生产质量实施初件检查及生产条件确认, 经确认符合标准要求后才可继续开机生产。
6.模(治)具如无法修复时, 应立刻提出报告请部门主管裁决。 6.11.6.IPQC制程巡回检查异常:
1.制程抽检产品异常:制程IPQC依据检验规范、抽样计划、相应质量缺点判定基准或检验样品每两小时对产出品抽样检验一次,合格则在标签上加盖IPQC合格章;有不符合项,且不良数超出AQL值时,开出重工记录表,通知成型重工,并将其不良项记录在《制程巡回检验记录表》上追踪结果。对于持续的不能彻底改善的异常,汇报上级主管依6.10.2项异常处理方法办理。
2.标准指导文件不符(作业指导书、包装规范悬挂位置不正确,作业员作业与指导书不相符,成型设备参数与标准不符等),需知会成型单位分析改善,提供正确之指导文件,指导作业员正确作业,当成型单位不能即时纠正时,需经过工程、品保等相关部门签核同意后,由工程部填写《工程变更通知单》在文控中心统一变更受控发行(特急时临时作业指导书致文控中心盖临时发行章发行)。
6.11.7.OQC在入库检验时不合格,需开出《品质异常单》由成型单位分析异常原因,制定改善和预防对策(当OQC检验不良超过3%,且生产时间超过4H时,责任品管需检讨漏失原因,协助成型及时发现潜在异常,预防批量问题)。
七.参考文件
7.1 不合格品管制程序 7.2 抽样检验计划 7.3 文件资料管理程序 7.4 标准成型条件表 7.5 塑件产品次料添加标准 八.相关记录
8.1 生产日报表
8.2 成型首/终件检查记录 8.3 成型制程产品巡回检查记录 8.4 成型制程尺寸巡回检查记录 8.5 化学测试申请单 8.6 制程异常处理单 8.7 重工记录表 8.8 生产计划表 8.9 出货通知单 九.实施与修订:
以上呈核准后实施,修订亦同。
推荐第6篇:制程检验作业管理办法(推荐)
1.0 目的
为更好完善公司的品质管理,明确各部门的工作分工职责,提升产品品质,减少制程过程中不良的产生,特制订此作业管理办法。 2.0 范围
适用于本公司半成品及制程各工序环节产品的检验。 3.0 职责
3.1 通机部/机车部:首件检查与过程自主检查、制程异常原因的分析与纠正预防措施的落实执行; 3.2 品质部:过程首件检验、过程巡检及记录,异常的跟进和改善效果追踪确认;
3.3 技术中心:协助生产对工艺方法的改进,相关文件修订,必要对异常原因的分析和责任单位的判定。 3.4 相关部门:与品质有关连责任,协助品质改善。 4.0 作业内容 4.1开机前检查
4.1.1.开机前品质巡检人员须对来料品质进行检查,相关作业SOP是否与生产订单相符,机台参数和模具编号是否与工艺卡上要求相符。4.1.2.必要时或客户有特殊要求时,须要求生产人员将工艺实际参数写在首检记录表中。 4.2 开机首件检查 4.2.1首检定义:
4.2.1.1按生产计划订单,生产部开机后稳定生产的第一件产品;白班和夜班接班时,每个班的第一模/件产品,需进行检验确认OK后方可开始批量生产。 4.2.1.2在每次上模、换模、更换材料、设备维修、模具维修后及停机4小时以后开机生产时。需送样品进行首件检查。
4.2.2 首检的操作流程:
4.2.2.1制造部门依生产订单安排生产,开机后产品稳定后,经自检外观和结构与标准相符,再填写首检申请记录表,给负责当班品质巡检人员做首件检查确认。 4.2.2.2品质人员接到首检申请记录表后,在15分钟内完成首件检查,如有测试项目,以测试要求时间为准。在规定时间完成后,将结果通知生产部门主管。 4.2.2.3品质人员首件判定合格后,填写首件检查记录,并将首检样品放在指定区域。
4.2.2.4首件检查经品质人员确认OK后,方可批量生产。
4.3 制程巡回检查
4.3.1首件判定OK后,生产人员依据作业SOP、工艺卡和样品进行自主检查作业。
4.3.2 品质人员依据工艺卡,图纸及其它标准要求,每两小时一次对制程品质状况进行巡回检查,每次抽查的产品数不少于5PCS,依工艺卡要求,将检查结果记录包括外观、尺寸及其它项目内容写在检查记录上;在各工序检查表或产品流转卡上,并签名和注明日期。
4.3.3 生产人员按时间段,依据产品流转卡记录上判定OK标示,将良品周转到下一工序进行生产。 4.4 制程品质异常单作业内容
4.4.1 当生产在开机前,品质人员发现工艺卡,作业SOP与生产订单要求产品不相符时,口头通知生产主管/组/班长即时改善;品质人员对生产的来料,辅治具进行确认,若发现有异常时,通知
生产负责人即时处理,必要时开立书面《制程品质异常单》或《纠正措施处理单》,通知相关单位改善,当确认可接受或让步接受后,方可批量生产。
4.4.2 制程品质异常单开立时机
4.4.2.1 生产送首件给品质人员做检查,送检3次以上仍未判定合格时,品质人员可视具体情况开立《制程品质异常单》,要求其改善。 4.4.2.2 生产部门未送首检或首检判定不合格时,擅自批量生产时,品质人员可开立《制程品质异常单》处理作业,要求生产部门进行回复预防改善措施。 4.4.2.3品质人员在制程中,抽检不良率达到3%以上(含)时,或存在重大功能性品质隐患不良,不间断的产生,又未从根本上改善时。
4.4.2.4制程中出现不良时,品质人员口头通知其改善,但在超过半小时未完全改善OK,仍一直在生产的前提下。4.4.2.5 生产作业中,人、机、料、环、法、环境与工艺卡或作业指导书不相符时。 4.4.2.6 当接到客户投诉时,在制品或生产过程存在同样或类似不良时。
4.4.3 制程品质异常处理流程
4.4.3.1 制程中如出现品质异常,品质人员先以口头方式通知生产班/组/主管人员,依4.4.2项原则开立制程品质异常单。 4.4.3.2 品质巡检人员发现异常后,在15分钟内开立制程异常通知单,异常单需品质经理审核。交给生产或责任单位主管签收,品质巡检人员做好登记明细。 4.4.3.3 生产单位或责任单位接收到制程品质异常单后,针对异常状况加以处理,改善OK后方可批量正常生产。在三个工作日内回复异常处理报告,特殊情况(如长期改善方案需验证测试),不超过七个工作日;完成回复后,生产部门将异常单交给对应开立异常单品质人员。品质主管主导、制程巡检人员跟进,对改善效果追踪,确认改善方案有效和落实后,方可结案处理。 4.4.3.4 责任单位对异常单上的原因分析、改善预防措施需及时回复,否则作为异常报告回复不及时处理;品质异常单需妥善保管,《制程品质异常单》一式两份,一份由责任单位保管,一份由品质部门留底存档,作为品质追溯和部门评核依据。 4.4.3.5 当异常属专业性或属工艺缺陷时,由技术人员对原因进行分析,回复相应改善措施;如责任单位存在争议或分歧,必要时提请副总经理裁定责任归属单位。 4.4.3.6 同一种或类似不良发生超过3次时,品质未完全改善OK,品质部门主管有责任和权利,召集相关责任单位召开品质专题会议进行检讨改善。
4.4.4不合格品处理
4.4.4.1 开机前检查发现的来料不合格品,依《产品标识与追溯管理程序》规定,标示隔离放在指定的不合格品区域。 4.4.4.2 制程中品质人员依2小时巡回检查1次,巡检中发现不良,及时将此段的不良品隔离标示,并要求生产将不良品放在指定的区域,品质人员并追溯前一时间段是否有不良产生,若存在不良,按《不合格品管理程序》加以处理,填写不合品处理记录。 4.4.4.3 制程出现不良按以下方式加以处理:特采使用、返工/返修、挑选、报废,品质人员对生产制程的不良品,原则上要求生产部门在3个工作日内加以处理,特殊情况除外。
4.4.4.4 生产或其他部门返工/返修、挑选及报废的产品,需给品质人员确认;报废产品须填写报废申请单给品质人员签名,并交生产经理和品质经理审核后才能生效。
5.0 相关文件
5.1 记录控制程序 5.2 标识与可追溯性管理程序 5.3 生产过程控制程序 5.4 产品的监视和测量管理程序 5.5 不合格品控制程序 5.6 控制计划管理程序 5.7 改进策划管理程序 5.8 进料检验规范 5.9 工序检验规范 5.10 成品检验规范 6.0 使用表单
6.1 特采申请单 6.2 进货检验单 6.3 工序检验表 6.4 制程品质异常通知单 6.5 成品检验报告 6.6 纠正措施处理单 6.7 不合格品记录表 6.8 全检记录表
推荐第7篇:IPQC制程检验及制程稽核
IPQC如何做好制程检验及制程稽核
一、制程检验与测试之规划
1.1 对新产品、新制程或新合约而牵涉及制程的新设定或变更时,研发部门、工程部门、质量部门 等相关单位应共同考虑产品特性、物料或环境的状况,于制程中的重要点验证其质量状况。每一阶段的检验与测试作业均应直接与成品规格或作业要求相关。
1.2 应在制程中适当定点实施检验与测试作业,设置的位置与检验频率,应依据产品的重要特性与验证的难易而规划。
1.3 制程中检验与测试应依产品之特性、制程之型态规划于特定产品制程检验与测试作业中,并采用下列之一种或数种方法;
a) 自主检查-作业人员本身所作的检验与测试,依据QC工程图与各作业指导书执行之。 b) 自动化检验与测试-使用自动量测减少人为失误,为现代化工厂大量使用。 c) 检验站检验与测试-依据IPQC制程检验标准执行100%检验或抽样检验。
d) 巡回稽核-由品管员巡回稽核以监测特定之制程,巡回稽核之作业应定于制程检验与测试作业程序中。
e) 首件检验-依据各作业指导书与IPQC制程检验标准执行每工令正式生产前之第一件检验。(首件定义为每日生产前或换线,异常停止后重开或每工令的第一件) 1.4 应规划在重要制程点使用管制图表,并规定于「QC工程图」中。 1.5 各作业指导书应说明圆满达成工作、符合良好工艺标准与规格之准则。 1.6 各作业指导书应以书面标准、图面或实体样品说明必要的程度。 二 .检验与测试作业的实施 2.1 完成制程检验作业流程。
2.2 新机种及产品初次生产、制程初次设立或间隔一段时间再生产时,应依产品试产之规定实施验证。
2.3 首件检验: 每批首件产品须经制程品管人员检验合格后,始可继续生产,检验结果记录于首件检查表。 若首件不合格﹐应立即通知制造现场主管重新设定与调整。 2.4 制程检验
a) 每工段作业完后, 现场人员将在制品放置待验区待制程品管人员检验﹐检验前应确认半成品追踪单基本数据填写是否详实。
b) 制程品管人员使用最新版本的相关质量文件,如图样、QC工程图、IPQC制程检验标准或各作业指导书﹐并确认检测仪器均经校正合格﹐始可执行制程检验与测试作业并作记录。
c) 检验完成后﹐如为质量合格产品﹐需于检验合格批上贴上”IPQC PASSED“标签与盖章﹐移至特定标示区域以便入库或作下一制程加工。 d) 检验完成后﹐如为质量不合格产品﹐需于检验合格批上贴上”REJ“标签与盖章并加一退货单﹐移至退货区域﹐作不合格品之重工或维修处理﹐参考第三项作业。 e) 各种IPQC标示均需注明日期﹐且经由检验人员签章后﹐始为生效。 2.5 制程稽核
a) 品管员每天至少一次至各作业站、测试站稽核作业者所使用的材料、作业方式及仪器设定是否正确?同时依据IPQC制程检验标准抽验在制品、以随时了解质量状况,适时发掘问题,做好防治不良作业;巡回稽核的结果填于制程稽核巡检表。
b) 各制程稽核质量记录﹐包含制程设定条件﹐以符合各作业指导书。
2.6 依据QC工程图与各作业指导书的规定,于制程之重要点使用管制图,以点线的变动监视产品及制程状况,并提供查问题与解决对策之有用信息。 三 .不合格品之处理
3.1 作业人员或测试员于发现产品不合格时,应依各作业指导书的规定予以标示或移离生产线,并放置于红色容器内待处理。
3.2 当发现属制程不良,亦即有重复产品(如连续三次)不良发生时,应向主管报告,并经主管确认后,立即进行改善措施。 3.3 制程检验发现不合格品时
a) 制程检验发现不合格品时,而须采取矫正措施以防止事件之再发时,制程品管人员应发行产品质量异常单,给相关责任单位并要求在期限之内处理完毕。 b) 如因情形特殊拟予特采时﹐应按照特采作业程序作业。 c) 良品/不良品应作明显之区分与标示﹐以免混杂一起。 3.4 制程稽核发现不符合事项时 a) 当有下列情形时﹐应实施改善: 1) 当制程统计管制图超过管制线时。 2) 当制造流程与工作指导书之规定不一致时。 3) 当严重失误发生时。
4) 当制造流程不当可能对产品质量造成影响或导致严重失误时。
b) 当制程在稽核中要求改善时﹐制程品管人员提出异常通知单﹐生产线负责人或制程主管必须立即反应﹐改善行动须在同一天采取行动﹐并尽速完成。
c) 制程品管人员在改善行动后必须追踪是否全然遵守规定实施﹐并提出评估成果。
3.5 制程变异对产品质量有严重不良影响时,经制造单位主管确认后,立即停止生产。待问题解决,并经制程品管人员确认后,始得继续生产。
3.6 停线若有争议时,应由副总仲裁;如有涉及技术问题,必要时通知研发部门或制造工程部门处理。
3.7 制程品管人员于发行异常通知单后,应主动跟催处理情形与结果,并将处理结果记录与归档,作为质量回馈与分析改善之资料。
3.8 产品若经制程检验不合格而批量退回时,应依不合格品管制程序之规定处理之。
3.9 如决定重工时,应依据重工之规定办理;重工后之产品应再行检验与测试合格后,始可放行。 3.10 制程中如因紧急用料或特采时,应将产品予以鉴别与记录其方式可于相关文件予以记录,便于发生间题时,得收回或追溯。
3.11 如作制程变更时,制程品管人员应验证变更后应符合原规格要求,并做成记录。 四.制程质量数据分析
4.1 制程品管人员每日应将各IPQC质量报表键入计算机﹐每月提报月报表。
4.2 制程品管人员每月应依上述数据制作IPQC不良项目统计,计算月不良率并绘制图表,同时将主要不良项目作要因分析图,研拟改善对策并作成不良检讨报告。
推荐第8篇:制程工程师岗位职责
1.负责QC工程表、作业标准书、纳入式样书、包装式样书等标准文件的制定。2.生产所需治工具的设计。3.组立治工具的维护、维修与保养。4.外来文件、图面的审核。5.标准工时的降低与测定。6.新产品的试做。7.生产技术创新。
推荐第9篇:制程QC职责06
1.IPQC職責:
a.負責初件檢驗(開線,換線,調机后),前加工加測保持力(每台機每2H一次),并作搖擺測試; b.產線開線前/收線后,對備料進行抽樣檢查,.c.產線巡迴抽樣檢查,對來料,半成品及成品進行品質確認,并在”制程巡迴檢驗日報表”上作記錄.d.巡查各工站的作業是否與SOP的標準一致.e.巡查產線是否按正常的流程走,并督促其正常運作.f.檢查檢測治具的性能.g.巡查物料擺放是否合理,確認報廢品的報廢.h.對不良品的處理按”不良品處理流程”作業,并在不良品流程上進行簽認.i.接受FQC的反饋信息,對異常迅速進行跟蹤處理,并呈報主管.j.執行本區域的5S.k.資料的整理,歸檔.2.FQC職責:
a.完成當日成品/重工品的入庫工作.b.在檢驗成品發現的重大異常時,向前追溯,并把信息反饋給IPQC,并進行跟蹤處理,同時呈報主管.c.檢查檢測治具的性能.d.接受OQC的信息反饋,對異常進行跟蹤.e.填寫FQC日報表,品質經歷表.f.執行本區域的5S工作.g.分析本次成績與目標達成的差距,采取改善對策.h.相關資料整理及歸檔.
推荐第10篇:SMT车间品管制程
SMT车间品管制程
一般说来,工厂生产行为都是批量性流水作业,最怕的就是现场产生变异,产生变异的原因一般
有五大因素:人员、物料、机器、方法、环境,简称4M1E,做品管只要适时适地把这几个大因素盯紧
,尽量在第一时间发现变异并将变异现象呈报、解决,那么工作就做好了一大半了。然后发挥积极的
处世态度和良好的品质意识,不断地推动品质改善,以达到趋于完美的境界。DTL科技有限公司品保
部的《IPQC检验规范》明确了四点要求,在这里结合规范及实际经验,把它们整合起来,总的来说有 以下几点:
第一、上线物料的稽核 http://blog.sina.com.cn/pbfree0
1要求对物料非常熟悉,对准备上线的原材料要看IQC检验PASS单和原材料供应商的标识,是否与
所要领取的PO单号及工单BOM一致。一般情况下,进料检验是对应工单号进行检验,出错率较小,以
此来初步判断是有必要的。另外还要注意几点,
1.工单号不一致。(要查两单是否为同单,后单是否作了更改)
2.无IQC标识。(要查为什么没有标识,往往出错的地方就在这儿)
3.散料。(要特别注意有否混料以及容易被混料)
4.物料不匹配(比如胶壳上、下盖)等。(生产前.生产中要留意)
5.特采物料。(注意是否有批量异常及产生一些新的异常)
6代用物料。(同上)
7.试产物料。(同上)
8.加工物料。(同上)
而对像DTL这样的中小型企业,对物料的管制有两个方面,在量(数量)的方面是由生产线助拉管
制,在质(在这里指的是物料的正确性)的方面就要要求随线的IPQC担负全责了。如果物料用错未能及
时发现而造成制程大批量不良,此为IPQC工作失职(物料发放错误/物料领取领错不在此攒笔),所以
在工作中绝不能粗心大意。(这里涉及到一个品质管理成本的问题,DTL公司这种IPQC模式和其它公司
如深圳泰丰是没有办法比的,当然这有其历史原因的,如果要改革的话那是后话。)
1.时间性:检验核对物料时,要在生产线领好物料至投产前这一段时间内完成。如果遇到生产线
急转单,核对来不及就把工单文件拿到生产线上,对照BOM一件一件地核对。
2.方法性:
A.在核对物料时,务必要求以工单BOM表为准,且工单BOM表、IQC PASS单标注、实际物料三者要 一致。
B.在核对物料时要仔细全面,大到外箱小到螺丝钉,千万不能落下哪一项不去稽核。实际稽核中
要注意:各物料的供应商是否与工单规定的一致、IQC PASS上标注的单号与在生产之工单号是否一致
,同种物料外箱上标注的进料日期是否一致(或接近),如不一致要看是新进的还是库存物料,如是货
仓库存物料,则要特别注意制程中的情况有无异常发生。(这是因为:通常情况下,货仓发料有“先
进先出”的原则,例如某订单数为1K,采购也订了物料1K,但此物料已有库存200PCS,仓库发料的时 候他就要先发库存的200PCS及1K里面的800PCS,而将新到料的物料重新作库存了)这时就要特别注意
库存物料在制程中是否有异常。例如库存胶壳上下盖是否为配套一致(模号、材质、颜色等)、在超声
及跌落时有无异常、CASE有无改模、材质是否与工单相符,有无更换供应商。稽核时既要细心又要注
意“首检”和“尾检”,避免因物料的变异而造成在制品产生变异。(线索:要关注每箱物料上的IQC 标识卡的日期是否为同一时期)
例如塑胶类物料稽核:
1)、胶壳材质,一般有三种:PC料,ABS料。尼龙料。胶壳内面一般都有标示材质,如没有,则
按培训方法来识别,熟练的话用眼睛看、用手感或加以燃烧就能初步判断。
2)、PC料能做成透明体,其它两种则不能做到。
3)、安规要求胶壳防火94V0级,达不到94V0级要求的是不能使用的,检验方法:把胶壳放在本生
灯外焰燃烧8-10秒钟,移开火焰,胶壳燃烧火焰5秒内能自动熄灭,则为防火94V0级,反之为不符合 94V0级防火要求。
4)、胶壳卡口与输出线S/R要实装。
5)、CASE外形、内部档位及PIN脚尺寸必须用卡尺进行测量。
6)、CASE色号等。http://blog.sina.com.cn/pbfree01
例如线材类物料稽核:除外观、尺寸外,特别注意:1)、安规线印字,如UL246
8、UL2464等。2)、线材规格,18#、20#、22#、24#、26#等,线芯数量及横截面积大小必须能明确判断。3)、五金头
外形“H”头、“L”头以及特殊荣绩头、仍合头等是否与要求相符。
包装材料要对照图面、尺寸、印字要求与工单一致,例如纸箱、白盒、环保胶袋、铭牌,在此要
特别强调铭牌,铭牌在本厂有两种:PVC和铝制,PVC材质又有耐高温不防火和普通的但防火。铝质铭
牌外表面有一层保护膜,一般情况是不用撕掉保护膜的(但我厂生产泰丰41BSI白色胶壳这一款机型客
户要求要撕掉保护膜,所以在制程中此外观较难控制,要特别注意划伤不良。检验铭牌的粘性,铭牌
贴后用封箱胶带贴在其表面,然后拉扯封箱胶带,循环三次如果铭牌不随胶带一起被拉起则为合格。
对于上线物料检验和判断在此不一一细说,具体可参阅>,多掌握不同物料
的判断和要求。我们要在第一时间发现异常情况,防止大批不良的发生,对特殊的物料,我们要多次
检验,在中途还要反复核对。核对物料过程中不可偷懒,不可怕麻烦不去看,但上线物料稽核毕竟不
是进料检验,要合理利用时间,在生产前及生产过程中不定时核实。做到先知先觉,将问题点控制在 源头,即生产前。
案例:2005年3月份,生产一款直充Hi777,工单要求包装材料用印有警告语的胶袋,而生产线用
的是没有警告语的普通胶袋,后在线IPQC发现了此不良,将此批产品贴“红单”隔离管制。
这里,重点说明这个例子,货仓发料员、生产物料员责任心不强,发的敢发,领的敢领。往往,
与工单要求不符的物料上线生产,别的人都不着急,而品管在着急,联系厂部看要不要放行。这就是
一种品质意识的落后。也是管理上的失败。说白了,在中国人的团队里,面对这种情况,什么可以什
么不可以,不是你一句话就可以的,而是要走正常的程序,不然“对后工序负责”就是一句空话了。 这种局面如何扭转,也是摆在我们管理者面前的一个问号了。
制程中涉及到物料用错的几个方面:
1.同一订单中类似物料放置在相近的地方,往往造成第三人无意中拿错。*****
2.不同工单物料没有及时进行隔离,往往造成第三人无意中拿错。*****
3.http://blog.sina.com.cn/pbfree0
1第二、制程工艺稽核及思考 物料检验合格后,开始生产,我们要对制程中的工艺去进行稽核,
生产线有无挂工艺流程图、作业指导书,工序排位和作业员操作是否与流程图及作业指导书上相符。
说了不等于做了,做了不等于做到位了。要做好每一件事都要不折不扣地去做,而没有其它的捷径了
。这一点,在DTL公司就不用多说了,毕竟------
为改善制程中的不良品,有时对现有的工艺进行变通也能起到控制不良的作用, 这就要对现场
非常熟悉及善于思考问题了。
案例:本厂的直充电源产品生产线,在电脑综合测试仪位置的不良率非常高,一般可达到5%-- 10% 。
现象:在加工组只配电阻但不测试电性,在电源板生产线第一站有测试OVP电压但不测试其它电
性,对后工序没有一点控制作用。
如果将此控制点前移到加工组对所有参数进行全检,不就避免了做不良品的无用功吗?经笔者多
次建议后,工程部才采纳了(2004年10月份)。在加工组配电阻工位后增加一站电性测试工位,即将控 制点前移,现在已将不良率控制在1%--3%之间,提高了生产线的效率。经实践证明是正确的。这一点 应记入>以示后人。
从公司实际情况来看,作业工序能力还比较低,按照IE制定工艺来执行生产时,以IE排线的角
度认为工位自检能保证产品质量,实际生产时无法做到,这就要在制程中加一个检查点来控制品质了
。这一点以焊点目检工位为代表在运作,以前低频焊点检查只有十多个焊点,而现在高频有100-300 个焊点,如果还按以前的方式堆到装配线肯定行不通,必须在加工半成品源头把关。
制程中,我们发现,DTL直充产品存在一些致命缺陷,三直三现原则要求我们现场、现物、现象 ,经分析得出如下结论:
一、缺陷等级
致命缺陷
二、耐压不良的位置分布
1:元器件不良:Y电容、光耦、变压器、PCB高压隔离带
2:工艺不良:
① R10与变压器胶芯相碰
② Y电容、光耦、变压器下面有导电体异物
③ PCB板初、次级隔离带表面有锡渣、脏污
④ 盖子内有导电体异物
三、具体原因判定(运用排除法)
1:外观初步检查:http://blog.sina.com.cn/pbfree01
参照工艺不良4点逐一检查,找出不良,如果工艺没有问题,则进行下一步;
2:测试时检查有无打火现象:
如有跳火现象,则重点检查跳火部位元器件与周围元件的绝缘距离,是否有:
①引脚长②绝缘层(皮)破损③有导电物质(水、锡渣、受潮、松香等)
3:元器件逐一排除法:
① 假设是Y电容不良:将Y 电容取下来,再来打高压,看高压机的反应,是否是一启动开关就鸣
叫,如果是一启动开关继续报警的话,则说明是其它元件的原因了;(因为Y 电容已取下来了)
② 再假设是“光耦”不良,将“光耦”取下来后再打高压,此时如果不报警则是光耦的问题了
;如果报警则说明前面两个元件应没有问题,可能是变压器或其它的问题,
4:结合以上几点,再加上经验,可以很快地找到原因。
四、以上方法可以快速判定耐压不良问题点在哪里,可以给IPQC控制致命缺陷争取到主动,对后 续的预防和改善起到作用。
五.耐压不良的解决方案:(省略1K字)
拉线越长,越容易产生一些因仪表、治具误差而造成的不良品。在生产实践中。笔者发现并总结
出了一个“前紧后松”的原则。例如直充板的电性参数。(仅举例配电流一项,加工组为527-532mA, 装配线为515-535mA,包装线为510-540mA,此原则遵循在源头控制不良品的方针。)
第三、在制品检查 按每个工位抽检5个/2H的比例来检查
对制程中的产品,要求定格、定向摆放,以及轻拿轻放。产品要求定格定向摆放,但每个工位 的摆放与其它工位摆放方向是不一致的,其目的是使未作业的产品容易识别而不至于流入下一工序造
成不良。在线上经常发现有作业员乱扔产品现象,但是一部分中层管理干部并不重视这个问题。在品
管的角度是不能接受这种作法的,但是从实际现场来看相当一部分人不能理解轻拿轻放的意义。
让我们用一个因果关系来说明乱扔产品是如何影响质量的,影响质量是果(结果),乱扔产品就是 因(原因)。
举例说明:我们厂的支柱产品低频变压器,所用的桥式整流电路PCB板,上面有四个二极管一个
电解电容的那种,最常见的了,在DTL科技有限公司有一道独特的风景那就是在电解电容引脚上要套
PVC套管,这种作法在珠三角可以说无厂能出DTL左右了。
这种原因有两点:一是PCB板插孔间距与电解电容脚间距不一致。二是作业堆积或作业过程中使 电解电容受太大外力。
这种方案的目的就是为了控制因电解电容引脚松造成的输出电压低问题而采取的一项措施,我们
看这种措施也确实有效,但从另一个角度暴露了DTL的一个质量管理的“懦弱性”,因为管理的容忍
或者是漠视而允许存在“构件不匹配”、“扔产品”,管理的职能退其次而变通为:将电解电容引脚
上加两个套管来控制这种不良。走曲线运动,不把“根本”当回事了。试问这种只忙于“救火”的管 理模式能有前途吗?
还有另一道风景线那就是“全检线”的存在,这种派生出来的模式其实也有它合理存在的一面,
这在当时应对泰丰客户也确实立下了汗马功劳。不过时代的发展,这种模式已越来越遭人质疑,现在 终于痛下决心将其拆掉,但我们有没有心理准备呢,用一句不恰当的话来形容:“扶你的人已走了,
你再次跌倒后能自己爬起来吗?”在这种恶劣的条件下,也是给品管一个压力,如何才能发挥“军师
”的作用,既要自己清醒也要让更多的人清醒,从一开始就要把产品做好,这就要拥有丰富的经验来
辅导其它的干部了,并将“不做不良品”的口号落到实处。(此处就不在阐述工业工程方面的知识了 。)
让我们看一看“扔产品”和“堆机”的成本:案例:2004年12月1日某线做某某客户ADAPTOR产品
因制程中发现有输出电压低不良品,原因为电解电容引脚松脱造成,其引脚也有套PVC套管,但在制
程中无法控制这种不良,且因其客户对此产品的品质要求较严,故厂内品质保守派意见为此批产品进
行全检处理,经全检3200PCS发现有2PCS电压低,虽然此次全检弥补了一次客户投诉,但其代价是不
能让人忽视的。每次都这样忙于救火,火只会越烧越大。品质的管理也只能疲于奔命。
生产能力究竟有多高、管理深度有多高,值得我们去思考(此处省略1K字) !
每条线开拉时,先从第一道工序跟到最后一道工序,产品流到哪里,IPQC就要跟到哪里,不要前
面在换单生产你人还在拉尾,或在其它地方停滞,就算前头出现问题你也不知道,等你知道了也做出
来大堆不良品,那时就算问题你反馈或发出了品质异常单。但结果总给人的感觉不好,没有在第一时
间发现,做IPQC也失职,所以做工作要注重方式去做,不能顾头不顾尾,一条拉排顺后,那就依照
5PCS/2H的频率对制程产品进行巡回抽检,虽然检验规范是这样要求的,但我们可以活用,对某些关 键工位要重点稽核,像装配线的焊锡工位是比较重要的,为什么这样说呢?有些问题具有隐患性,装
了盒超了声,电性测试也发现不了,而在QA抽检或客户验货时出现不良,想一想,你就明白。前面控
制好了到超声后,就是一个外观问题,只要超音波不出现异常,一般可以及时控制的。所以装配线
IPQC控制重点在超音前段。
在制程中,对发品质异常单而言,你要明白在什么样的情况要发品质异常单,发单的目的 :制
程中有异常情况,要及时提交工程及相关责任部门分析,从而提出改善方案控制制程中的不良,以保
证品质,发异常单不是非要等到2H或规定数量就发单,如果你认为某种情况具有隐患性,也是可以发
单的,发单出去之后,别的部门回复改善方案还要跟踪有无效果,如无效果则要继续追踪,在此要说
明,发异常单我们有个不好的习惯:1.不良情况描述不清楚2.有异常情况一打单交与领班就完事,也
不去查不良原因及想办法解决3.久而久之,制程有什么不良、是什么原因造成,应该怎样解决也不知
道,想一想,你做一名IPQC认为该怎么做呢!http://blog.sina.com.cn/pbfree01
对产品的判定要参照IPQC检验规范及QA成品检验规范去做,在结合自己平时积累的经验知识去做
,专业水平要强,判定要准确,做事不能拖泥带水,犹豫不决,要胆大心细,电性方面不用作太多的
讲解、在此对外观不良的判定、外观方面的东西范围很广、而且弹性较大,且每个人对一个事物的理
解和判定标准不一样,在实际工作中大家也遇到过,IPQC认为可以,但QA判不可以接受,同样有检验
标准,为什么会存在这样的情况,检验规范上所写的为上级领导平时经验或客户标准揉合在一起,在 实际应用中有些不适应,如果是量度的东西,就比较好掌握,如:错位不大于0.35mm壳缝不大于
0.35mm,这就是量度,用塞尺一量就知道结果,是行还是不行,非量度就不好把握,如AC PIN脚松动
,歪斜成什么样可以,什么样不可以,这样就会形成争议,怎样来处理呢?(此处省略500字)
平时工作的积累,之前此不良问题怎样处理,现在就怎样处理,如把握不住可以请示上级,按照
上级要求,事后追踪客户有无不良反馈,就可把它拿来为自己的判定依据,针对之前对不同客户的不
同要求而对外观进行调整,如客户对外观要求比较高,对内部标准上要加严,如客户对某些外观不良
有反馈,后续生产就要控制,对标准重新调整,参照上级领导封的样办放行。
执行标准的统一及集中制,此点在中小型企业中,有非常重要的作用。
总之,我们对产品的判定要准确,一般要依照和考虑,加严对内部影响极大,放宽影响用户的品
质,不能把良品判成不良品,反之,把不良品判成良品。
第四、关键工位检查 关键工位:对产品质量特性影响严重的工位,在工艺上有特殊(别)要求,
对下一环节有较大影响的工位,工艺要求程度高,标准要求高,客户的质量信息反馈表明质量不稳定
及不良品较多的项目。无法在后续的检验和实践中确认的工序,我们对关键工位的控制,设立控制点
,例如:焊点检查工位,电性测试工位等,重点审核关键工位,对关键工位工序具体熟练人员,可靠
的设备详细的作业指导书,控制点有明确的标示,关键工位的人员变动和更换应经过工程部IE审核,
IPQC人员重点巡检工位,关键工位不能随意取消。
所以,针对以上所说的,我们应该明白关键工位的重要性,对关键工位,我们多花点时间去稽核
,对他们挑出的不良品,要尽快分析不良原因,并采取相应的措施去改善,我们要定点,定时去巡检
,把这些关键工位控制得好了,那大部分问题就可以解决了,在制程中巡检就比较轻松了。
生产使用的仪器设备是否正常,是否在保养期内,对有异常的仪器、设备要求生产停止使用,交 与设备组维修,
采取前紧后松的控制手法,将更利于后工序的操作,如前站的参数收紧,后站的不良品就少。案
例:低频、高频变压器含浸前的测试范围就比含浸后的测试范围收紧了,以此来避免因含浸而产生的
变异来控制后工序的不良。然而,在两种产品上,品管提出了具体的要求但是得不到及时解决,而是
拖很久才解决。一是高频变压器浸油前后的参数,二是直充电源加工组与装配生产线前后的电性参数
。可是这本来在实践中是不争的事实,但在我们的工程、开发等部门各有道理,抱旧的一套不放。( 此处过程省略1.5K字)
第五、制程中的异常情况反馈及不良控制 由于DTL运作模式决定,在制程中拉长主导产品产量而
不怎么注重质量,使得在线IPQC要对线上的质量进行管制,但由于部门不同,我们提的要求他们有时
候不听,这就要求IPQC既要熟悉各种标准也要站稳立场。
只有建议权而没有行使权,所以一般情况下,如果在线出现不良及不良率较高时,我们有好的建
议要及时向拉长提出,他们如果不接受的话则我们就要将异常情况及时向自己的直接上司反映了。有 的时候在线IPQC对制程中的异常处理得不够理想,如线上出现了大批不良,心里就发慌,不知道该怎
样去处理,做质量就是替后工序负责,“后工序就是客户”的理念要落到实处,但由于生产线工序能
力及品管等的经验有限,往往达不到理想状况,这时就要将后工序的情况及时反馈到前工序,及时纠
正改善,使相同问题不再重复发生,以达到最终控制不良的目的。
例如:有些IPQC在装配线跌落发现有壳开或者松动时,不知道叫生产线采取措施而跑来对上级说
现在发现不良了,想一想是否比较气人,有不良就要叫生产不要现超声了,但我们的人中途跑来问,
生产还在继续超声,自己想一想此方法合理吗?不用说就知道怎样处理了,电性测试站或外观站有一
大堆不良品,自己还不去看、不分析原因、不打单反映,这种情况在IPQC之中是一种通病,生产做出
一大堆坏品,IPQC一点都不着急,有时叫他们打单才发单,这种就缺乏主动性了,生产线员工或拉长
向你反映问题漠不关心,等到出现大批不良,问你时,你说已经知道,为什么知道而不反映呢,此种
对工作不热情、冷漠,制程中出现已发单,相关单位已回复改善措施并交与生产执行,但我们不跟踪
效果,方案不行也不继续反馈,继续让生产做,到时有一大堆坏机或生产做不出成品,一了解,方案
没有用,但品管没有反映,此种跟踪效果不彻底,有头无尾的工作态度,生产拉长非正常操作,IPQC 向拉长提出不行,但生产不改善也不反馈,继续让生产做,到时一出问题,了解,你说已经向拉长反
映了,但不改善,为什么不向你自己的上级反映呢,继续让生产做,此种对工作极不负责,生产部收
尾或补单但未知会我们,但我们也知道生产在做,但不去看和跟踪,物料或其它做错,一了解,知道 这回事,但生产未通知,故未去看,此种工作也缺乏工作责任感和主动性,不管生产做什么单,知道
和不知道我们都有责任,我们做工作要学会独挡一面的能力,
制程中还有一些异常情况,分析起来可能较为复杂,此时要积极寻求PIE的帮助。此时有两点最
怕:一怕自己不积极了解异常现象,二怕PIE不作为。
第六、建立标准化 这一点非常重要,有很多问题我们有发现又知道怎么去控制,但没有完成标
准化,随着时间推移而淡忘了,到再一次生产中又出了异常的时候才发现,这个问题早就知道了,就 是没有改,再一次面对尴尬.
案例 “关于电阻更改事宜”:
一封邮件:[品管部发文] **(客户)订单AM-AX/BX/DX工艺要求R40、R
28、R32为卧插,但元件规
格工单要求为立式(立式元件引脚有绝缘处理),给在线生产(引脚不上锡)造成极大的困扰,现知悉工
程要求知会**(客户。笔者注,下同)立即作出更改。TKS!!!(2004.10.15)
(以下为11.22再次出现异常时各部发回的邮件)
[开发BOM工程师] 你部是\"现知悉工程要求知会**立即作出更改\",因**没书面指令我司开发更改,
[开发部经理] 没业务和上级的通知开发部是不会更改资料的。
[PMC经理] 都本着这样的态度那等着更多的库存吧。
[厂长办公室] 请采购查实,何时订料?何时来料?料来之前,工程有无提醒采购和开发暂停进
料?且有无追跟客户或反馈给业务追跟客户更改?以上,必须明天之内如实回复我结果!!!
[品管部经理] 此文当时品管(10/15发文邮件)已要求的非常明确,到现在既然说不知道更改哪
个零件,请仔细查阅你的收件箱。而且工程在产品总结会议上已有明确要求更改。品管10/28也发有
异常单,开发也有签名请查阅。TKS!
[厂长办公室] 通过上述事件很显然说明一点,就是各部做工作都是有欠主动而上升不到境界。 体现在:
1、工程有在会议上提出,但并无事先通知到采购等相关责任人,即光提出问题,但问题缺欠被 落实;
2、品管10/28号有发异常单,但中途有无跟踪?否则为何到11/22日还未更改结案。即问题有发 现、有发单,而缺欠主动跟踪;
3、开发既然有在异常单上签名,就也应有责任和义务向业务索取客户之ECN,实际上并非如此, 可见工作很是欠积极主动。
以上,特在此提出,希各部尤各部经理级干部能引起足够重视并做出积极检讨,在后续的工作中
务必改进。否则,就正像[PMC经理]所说的“如果大家都是这种做事态度,则只有等着库存”!
个人评论:如此的管理模式太让人悲哀了(允许扯皮、喜欢摊派)(明眼人一看就知道谁对谁错),
但现在每个人都有自己的理由,那事情又等到什么时候才能做好呢!?!分工协作的工厂没有务实的精
神是不能搞成事情的!!!在这种环境之下更要一线的品质管理人员有务实的精神和追求完美的态度去
推动质量的改善! (建议一切事情都由品管做完,那就一了百了了。面对这种情况,有两座山压在品 管身上,那就是有没有发现问题、发现了问题有没有能力将它实行标准化。特别是第二步需要很大的
勇气。这也是制约DTL发展的一个因素。需要思考的不仅仅是我们一线的人员,也是高层领导要思考 的。笔者注。)
第七、提升整体品质意识与员工的培训 医生查病因时有“望、闻、问、切、诊”五大手法,做
品管也要借用这种方法,使得检验手段更加完善:“望”就是看、检查的意思。要求品管员脚踏实地
的一一去落实,问题一般都能发现。“闻”就是听的意思。就是要增强对事物的敏感性,以及善于接
受别人的意见,加以推敲,得以发现或预防问题。“问”就是了解、询问的意思。要多问一问生产线
上的作业员生产情况,因为他们在亲自操作,有一些感受,但是他们不太知道后工序的情况而不能清
楚的判断质量的好与坏以及有什么影响。 “切”就是自己动手做和动手找原因。而不是像现在我们
的IPQC在等问题,脑袋里面要带着疑问去看事情。一些结构性及隐含性的东西必须动手去做,要经常
从符合性和适用性的角度来判定事物。这几点要结合起来综合运用,做事就会事半功倍。
对生产作业员都有要求自检和互检,但实际运作与理想的还有很大的落差,一般来说作业员都有
个误解以为上线物料是合格的为什么还要他们自检呢?他们以为IQC判定合格的物料作了全检才上线
的,其实不然,这一点就要我们的IPQC去改变这种员工观念了(这里是谈的品管这一边的控制点,当
然大头要生产去落实)。要多看作业员挑出来的不良品,有的时候我们没有发现的问题,但作业员有 发现,我们就要把不良信息及时收集起来再作出相应的对策。
综上所述,IPQC在工作中,要善于从不同角度发现问题,同时要胆大心细,不能犹豫不决,对产
品的判定要干脆利落,不要拖拖拉拉,因为拖拉给人感觉不好且耽误时机,有些问题当断不断,反受 其乱。
第八、人与人之间沟通及观念的提升 第一至第五点为我们工作中的注意事项,如把这些工作搞
好,我们就成功了一大半了。现行有句话叫“沟通创造财富”。人与人之间好比有一层隔膜,而沟通
就是刺破隔膜的利剑。在一个企业,部门与部门之间,上级与下级之间都缺少不了沟通,为什么有人
会天天闹矛盾,感觉到这里不“顺”那里也不“畅”。就是因为没做好沟通。品管与生产之间,一个
管质量一个管效率,意见不统一是很正常的,但不能一个说不行一个说行就去闹矛盾,不行是那里不
行,行又是行在那里,冷静下来双方探讨达成共识才是关键。“天下事非一人之所能独力,事事欲有
所为,必与其类同心共济。”现在社会的人际关系非常重要,工作上也一样,搞好品质不是靠一个人
或几个人就可把事情做得好的,是靠全体同仁共同努力才能做好的,是观念的提升。别人对我们工作
不良指责或提出改善建议,以为对我们不利而不但不采纳,而且怒目相向,其实我们要虚心的接受,
对自己不足的地方要分析改进,对不同的建议要“吸其精华,去除糟粕”不断地充实自己,不断地提 升自己的业务水平及观念。
一切社会活动都是分工协作的过程,搞质量也是这个道理,部门与部门的不一样,每个人的立场、看问题的角度不一样,对事物的认识也就不一样,因此,在工作中就会因标准问题而产生不同意见
,我们一线的IPQC如果意见与生产线意见不一致,首先向生产线提出,如果他们不接受,则要及时向
自己的直接上司提出来取得本部门上级的支持,以便更好地去开展工作。
在工作中,要把事情做好,不管用什么方法均可,但要讲道理、讲原则。在生产线上做事,拉长
或员工不配合,你就觉得没方法或做得比较辛苦,就打消了积极性。自己总找别人身上的毛病,说别
人不配合,自己有没有静下心来想一想,现有的阻力、我们的态度是进或退都在自己的手中,你要选
择哪一种呢?是把这个困难摆平还是退缩呢?我不希望你们都退缩,人生一辈子,什么困难都会遇到
,难道你什么都退,要退到什么时候呢?
附《IPQC制程巡查项目表》
01.确定工单号及档案,确定检验规范
02.是否悬挂作业指导书,排拉是否按工序流程安排
03.上线物料是否符合工单BOM要求,小到螺丝大到纸箱,每换一箱(袋)物料是否及时确认
04.认真按时填写巡检报表,检测、记录静电环佩带,检测、记录电批扭力1次/2H
05.测量、记录烙铁/锡炉温度1次/4H,烙铁是否有接地防漏电措施
06.确定有开发/工程确认合格的首件、样板
07.用首件、样板校对仪器、治具是否正常;确定在仪校有效期内;确认设置的参数与工单一致
08.用首件核对插件方式,内部点胶工艺,结构等与样版一致
09.员工操作是否与作业指导书一致,下拉前5个产品是否从前跟到后,再次抽检5个/2H/工位, 进行确认
10.新产品、新员工是否重点巡查,特采、代用、试产、让步放行的必须重点稽核、记录情况及 结果反馈
11.作业定格定位摆放,无堆积,轻拿轻放,员工是否自检、互检合格品才下拉
12.不合格品是否有标识,且用红胶箱盛装进行隔离,不合格品是否准时记录
13.任何来料及作业不良造成物料无法正常使用、影响订单完成的,要及时发>反馈
14.不良比例超过品质目标要填写>并要追踪处理结果
15.物料、半成品、产成品摆放是否有落实状态标识及签名
16.老化报表记录是否完整,确认输入电压、负载电阻是否符合要求,死机要及时反馈
17.有客诉及退货情况是否了解及跟进。返工情况必须跟进、统计不良及结果反馈
18.易磨损型测试用插座、电池、触片等及时更换及记录
19.任何操作、包装、储存不能有潜在影响品质
如何做好制程品质管制
(一)
表3-1 四大环节对产品品质不良的影响 2 制程品质不良的原因分析与对策
仅从制程的角度分析品质不良的原因,可以从下列四个方面来总结: ①员工不能正确理解和执行作业标准——不会 ②干部对制程的管制能力不足——不能。 ③制程品质稽核、检验不当——不当。 ④缺乏品质意识与品质责任——不愿。 表 3-2 制程品质不良分析与对策
(二)强化人员的管理以提升品质 1 人员品质观念强化
灌输现场人员良好的品质观念: ①品质是制造出来的,不是检验出来。 ②第一次就把事情做好。 ③品质是最好的推销员。 ④没有品质就没有明天。
⑤客户是上帝,而且是不懂得宽恕的上帝。 2 员工技能培训 ①岗前训练
产品特点与基本知识; 品质标准与不良辨识; 作业流程与品质要求。 ②岗位训练
如何正确操作设备、工具; 如何自检、互检; 品质不良种类与限度; 基本的不良修复技巧; 如何求救。 3 操作者自主管理
①操作者的“三按”、“三自”、“一控”要求。 三按,即:按图纸、按工艺、按标准生产。 三自,即:对自己的产品进行检查。 自己区分合格与不合格的产品。
自己做好加工者、日期、品质状况等标记。 一控,即:控制自检合格率。 ②开展“三不”、“三分析”活动。
三不,即:不接受不良品、不制造不良品、不传递不良品。
三分析,即:当出了品质问题,应及时组织相关人员召开品质分析会,分析品质问题的危害性,分析
产生品质问题的原因,及分析应采取的措施。 表3-3 人为操作不良常用对策
(三)制度化、标准化、简单化、愚巧化 1 流程制度化
任何作业流程都应该予以规范化、制度化,使员工有据可循,使每一次作业可以预先得以教导、安排
,事中得到控制,事后便于追查。 2 工作标准化
将工作方法、步骤、注意事项予以标准化,易于操作,不易出错,便于查核,对品质稳定有关键作用 。
3 作业简单化
基层员工的素质,能力、意识在企业中处于较低水准,尽量让其工作内容更简单,有利于学会、方便
作业,自然降低出错的概率。
4 愚巧化(Fool Proof),俗称防呆。其目的是防止作业人员因不熟练或不会做,以及疏忽或不小心 而造成制程不良,必要时也可防止过剩生产或产量不足。如国内电器的电源线插头依CCEE规定应为三
扁插,且仅能从一个方向插入插座,此即防呆功能。 愚巧化的作用: ①防止过剩的生产量
②防止错误或不良的原料投入。
③防止作业标准、作业条件的变化超限。 ④防止多装、少将的发生。
⑤防止因“定位失误”而造成的品质不良。 ⑥防止作业不安全事故的发生。
流程制度化,工作标准化,作业简单化,工具愚巧化,既可以提升品质,也可以提升效率,是现场干 部工作的法宝之一。
如何做好制程品质管制
(二)
(四)建立品质与历史档案
由于品质问题的发生有其特殊性与历史原因,在许多企业中,重复发生的品质问题令管理者十分头痛
。现介绍一种既简单又实用的方法,即建立品质历史档案。
将发生的重大品质问题,逐一记录在每一个产品专用的品质历史档案表,详细记载问题发生的时间、
情形、原因、责任及对策等内容。在下次生产该产品时,只要调出该档案,即可以清楚其自“出生”
以来的历史问题,不必再依赖老员工、老干部、老品管的传帮带了。 表3-4 品质历史档案表
(六)全员参与活动 1 开展QCC活动
图3-1 品管圈活动推行步骤 2 推进TQM 全面品管(TQM,Total Quality Management)的推行要点: ①教育及训练 ②要转动PDCA管制圈 ③要设置全公司的推进组织。 ④要引进品管图 ⑤推动方针式管理 ⑥实行上级诊断的方法 ⑦充实品质保证体系 3 推行5S活动 4 推行TPM活动 5 推行改善提案活动
(四)品质做得好 ,顾客留住不会跑
(一) 品质工程与品质保证 1 品质工程
如何将“检验的品质管制”推向“管制品质的品质管制”呢?许多企业中的品管人员只是在做检验的
工作,尚不能发现所存之不良,更不用谈协助现场品质改善,因相品管部门与制造部门常常成为一对
“冤家”。品管要真正树立权威,除了发现问题外,还要能解决问题,改善品质的需要而建立的。
①品质工程人员职责 制定品质计划; 制定检验规范 设计检验量具; 制程解析,改善实验; 处理品质事故。 ②品质改善信息来源 品管报表或品质状况推移图
管制图;
品质成本分析表。 2 品质保证
品质保证,是为了保证产品品质能够充分地满足顾客的要求,进行有组织、系统化的品质推进活动。
品质保证(QA、Quality Aurance)正是因应预防问题、保证品质的需要而建立的(有些企业称为 品质稽核Quality Audit)。 品质保证人员的职责:
①公司品管体系运作系统、规范的查核
②客户抱怨(退货)的统计、分析、调查和处理。
③长期性的试验工作。 ④外协厂商辅导。 ⑤公司内的品质教育 ⑦全员品管活动的推动。
(二)没有品质就没有明天 1 对品质保证的认识误区
由于ISO 9000是一种品质保证体系,很多企业以为通过ISO 9000就是有了品质保证,甚至在产品包装
上大力宣扬,以标榜产品品质达到“国际水平”。
且不论企业是否确实依照ISO 9000的规定执行了各项制度,就是完全实施了, 也只能保证产品品质具有一致性,即属受控状态,但并不表明没有不良品,或者品质已有了保证。扎
扎实实地分析现场品质问题,逐一予以改善和提高,采取有力的预防措施,方可保证品质良好。
有的企业认为做好以下的工作就是保证: ①允许顾客退、换不良商品
②在某一期间内免费为顾客维修、保养商品。 ③加强了内部的检验工作。 ④对客诉积极处理、回复和赔偿。
以上只是表明企业有诚意提供好产品,愿意负责任,但同时也说明了品质还有瑕疵,还需改进。 2 品质是最好的推销员
好的品质,就是企业最好的推销员,众多世界名牌之所以能百年不衰,靠的是过硬的品质,而近年来
国内不少民营企业一夜成名,往往是靠广告和盲目的扩张,而很快又轰然倒下,却大多是因为品质出 了问题!
营销学上常说,留住一个老顾客,比开发五个新顾客强,而留住顾客的最佳方法正是提供良好品质的 产品与服务!
品质,是企业的价值与尊严! 品质,是企业未来的决战场! 品质,是最好的推销员! 没有品质,就没有明天! 品质做得好,顾客留住不会跑!
(三)品质管理的方法
(三)品质管理的方法 1 掌握4M1E的品质变异要素 3 运用QC—STORY解决品质问题 4 SQC统计技术的应用
常见的统计技术被称为QC七大手法,其简要说明如表1-1 5 QC七大手法
近年来,所谓新QC七大手法(New Seven Tools for TQM),也被广泛运用,如 表1-2 新QC七大手法简要说明 6 其他常用品质管理方法 ①实验计划 ②抽样计划
最常用的方法,普扁沿用美国军方标准MIL-STD-105D(即中国国家标准GB 2828)。 ③SPC统计制程管制(Statistical Proce Control)。通过对制程能力指数Cp、Ca、Cpk 的计算分
析,来判断制程能力,找出不足,予以改进。 ④FMEA
即失效模式及后果分析(Failure Mode and Effects Analysis),尤其是QS 9000 :认证企业,强制要求实施FMEA。 ⑤6 手法 由于摩托罗拉、GE等公司的成功应用,6 手法已引起企业界,尤其大中型企业的关注。
-=-=-=-===========================
(四)品质管理的方法 4 效果确认
进行效果确认时,应注意下列事项: ①确认对策是否有效果 ②分段确认、层别确认 ③确认时数据不可太少 ④确认时不可只比较平均值
⑤可以用推移图、直方图、柏拉图等 方法确认。
⑥确认效果的特性、标准须前后一致。 ⑦判定对策是否有效,考虑有无其他 因素加入。
⑧考虑其他方面有无反效果。
(七)采取巩固措施 :标准化
品质问题的改善效果要加以维持,需要标准化的推动,只有将改进的方案列入作业标准,或重要制定
作业标准,才能使执行长期有效。同时也可能要修必或重订检验规范与标准。 1 标准化的作用
①作业合理化、效率化,减少浪费。 ②问题容易显化,原因追查较易。 ③减少个人差异,变异缩小。 ④技术储蓄、经验传承。 ⑤权责明确,使授权得以进行。 ⑥可作为教育训练之依据。 ⑦有利于自主管理。 2 制定作业标准的来源 ①上级指示
②维持改善后有效的对策 ③需系列化者
④下一工序或客户经常抱怨的项目 ⑤工作上不明确,尚未整合者。 ⑥影响作业的有关因素改变时
⑦同样的手续、方法、流程,由许多人重复在进行的例行性工作。 3 制定标准的要领 ①内容要符合作业项目 ②内容要合符实际,配合实情。 ③要有具体的作业方法,操作性强。 ④追求简单化、步骤化、图表式和 限度样本。
⑤明确协同关系及作业权限责任。 ⑥以作业的重点为主,特别注意事 项、不能遗漏事项、必须遵守事项 和容易出错事项等亦须明确说明。 ⑦说明自检及异常处置的方式。 ⑧不与相关标准或规范相矛盾。 4 制定检验规范(标准)的作用
①明确检验作业的各项内容与需求,使繁杂的的检验工作不易产生疏漏。 ②规范品质检验的作业,有利于保持产品品质的一致性。 ③不易因检验人员的好恶影响品质判定的客观、公正。 ④减少送检单位与检验人员的工作争议。 ⑤有利于供应商、制造单位遵守品质原则。 ⑥易于人员的品质训练。
(八)找出遗留问题 1 指认潜在问题
改善之后,应该寻求下一个主题,可以从以下方面着手思考: ①原问题是否已彻底解决。
②原问题解决后,依优先顺序解决其他问题。 ③原已潜在问题是否凸现。 ④是否产生新问题。 2 指认可能原因
重新进入调查原因、把握现状步骤: ①现状调查 ②原因分析 ③要因确认 3 采取因应对策 ①采取预防措施 ②拟定紧急应变措施
③重新进入QC-STORY的循环步骤。 --------------- 品质检验服务 工厂评估
根据标准要求的具体方法对工厂工作环境、设备、机器、原材料、技术能力、质量控制体系及环境控
制体系进行检查。我们的现场检查员将给制造商和客户提供有关 不符事项的评估报告.生产能力评估
现场检查工厂的厂房、生产线、机器设备、人员技艺、原材料、工艺技术、品质控制情况等,提供现 场评估报告.行为规范评估
根据客户或国际通用准则(如OHSA18000,SA8000)的要求,现场检查工厂遵守所在地的环境、职业
健康、安全、社会责任等法律法规情况,提供评价报告.质量体系审核
根据客户或ISO9000标准的要求对工厂的质量管理体系进行审核,对其质量保证能力作出评价,出具
评价报告,并对不符合事项提供改善建议.环境体系审核
根据客户或ISO14000标准的要求对工厂的环境管理体系进行审核,对生产过程及产品对环境可能造成
的影响作出评价,出具评价报告并提供改善建议.生产初期检查
通过随机抽样对产品的原材料和配件进行检查,预见将会发生的问题。根据实际情况,调整质量控制 环节,确保其符合规格或参照样品.生产中期检查
对生产期间制造出的产品进行全面质量检查,并对生产进度进行了解,如有问题或不合格情况,我们
将提供有关改善建议,并及时反馈,确保产品质量符合标准,调节生产工艺过程.交货前检查
当产品全部包装完毕,准备出货时,我们的验货员将按抽样标准ANSI/ASQCZ1.4、MIL-STD-105E、
BS600
1、DIN40080、ISO2859或NFX06-22等随机从成品中抽取样品,确保产品数量、外观、作工、功
能、安全、颜色、尺寸和包装符合规格或购货单信用书或客户要求,并对货物的总体质量进行评定 装货监察
在产品装货时,我们的验货员抵达工厂、仓库或装货地点核对产品信息、数量和包装状况,并对货物
装柜过程进行监察,协助制造商确保所有的装货在正确明了的工作条件和工作程序中完成.运用 QC STORY 解决品质问题
(一)明确把握问题,调查现状 1 问题叙述
①发生品质问题,应事先了解“问题是什么”,才能迅速有效地解决问题.②对问题从“多个角度”进行分析,以“事实”说明清楚,使之真相大白.2 问题把握的步骤 ①收集数据
可以利用查检表来记录数据的状况.②数据的整理 利用查检表、层别法、柏拉图、直方图、管制图或推移图,将数据统计、整理,寻求规律,发现问题 。
3数据配合观察与意见
现状把握不能只着重于数据整理分析,应注重“三现”(现场、现人、现物)原则,实地了解问题发
生的状况,避免被虚假数据迷惑,或者陷入理想化之境地。
(二)原因分析
重点要因再作特性要因图分析,如图2-2 2 确认真正原因 ①指认可能的原因 根据经验或历史事件判断。 用层别法或柏拉图判断。 用特性要因图脑力激荡法分析。 ②评估可能的原因 相关专业人员讨论、表决。 收集相关数据,加以层别比较。 模拟试验以确定。 ③确认真正的原因 通过实践来验证。 通过事实调查分析。
(三)要因确认 1 对圈选要因进行检讨 ①有无标准? ②是否依标准? ③标准是否合理?
2 以柏拉图确认重要原因的影响度 ①必要时柏拉图可连续展开.②应用不同的层别角度追查焦点.③模拟实验.3 要因明确且可采取对策者,立刻进行 ①经验、专业判断。 ②历史事件启示。 ③及时总结调整。
4 影响度大的要因尚无法确定对策时 ①再作特性要因分析,并确认重要因影响度。 ②用问题阻力因素和助力因素分析影响问题的 各种要素,并选出其中的重点。
(四)制定对策 2 提出对策的注意要点 ①对策要具体可行。
②尽量是自己能力可解决的对策方案 ③活用创造性思考原则,运用改善技 巧与方法。 ④治本而非治标。 ⑤经济效益大的对策。 ⑥考虑风险。
⑦符合公司经营理念、企业文化。
(五)实施对策 1 教育训练
对策实施前,应充分进行说明、训练。其内容应包括: ①应达成的目标 ②实施的方式 ③注意事项 2 实施执行
对策要确实有效,应该注意以下事项: ①制定执行办法 ②分段实施
③容易做、效果大的先做 ④实施过程要做点检 ⑤让部属看得到实施状况 3 问题的回馈
①问题点查核,并回馈
②当对策无效或有反(副)作用时,应讨论,并调整。
(六)检查效果 1 检查标准的设定
对策实施后应及时检讨其效果,并注意设定相关的标准,如: ①检查项目 ②时间点 ③检查方法 ④负责人 2 检查的重点 检查的重点包括 ①方法、规范遵守难易度 ②实施人员的了解程度 ③方法的合理性 ④操作的便捷性 3 查核时机 ①实施过程的查核
实施过程的查核至关重要,其目的是确保实施者依既定之方案执行,给予必要的指导,纠正错误,并
对实施中的问题及时排除解决。
②实施完成后,应该将实施后的结果与实施前比较。查核方法可采用查检表、层别法、柏拉图、直方 图或管制图等。
第11篇:制程质量管理作业办法
制程质量管理作业办法
第一条 目的
确保制程质量稳定,并求质量改善,提高生产效率,降低成本。
第二条 范围
原料投入经加工至装配成品上。
第三条 制程质量管理作业流程。
第四条 实施单位
生产部检查站人员、质量管理部制程科及有关单位。
第五条 实施要点
(一)操作人员确依操作标准操作,且于每一批的第一件加工完成后,必需经过有关人员实施首件检查,等检查合格后,才能继续加工,各组组长并应实施随机检查。
(二)检查站人员确依检查标准检查,不合格品检修后需再经检查合格后才能继续加工。
(三)质量管理部制程科派员巡回抽验,并做好制程管理与分析,以及将资料回馈有关单位。
(四)发现质量异常应立即处理,追查原因,并矫正及作成记录防止再发。
(五)检查仪器量规的管理与校正。
第六条 本办法经质量管理委员会核定后实施,修正时亦同。
第12篇:DIP制程基础知识培训教材
DIP制程基础知识培训教材
DIP培训项目:
一、手插件的原则与标准
二、电子元件的单位及换算关系
三、电子元件的识别
四、电子元件的插件标准
五、插装零件成型作业要求
六、插件/补焊/后焊的作业要求
七、无铅/恒温烙铁使用与管理 名次解释: DIP:dual in-line package 双内线包装(泛指手插件)
一、DIP Manual Aembly Rule 1.双手并用:需左右手交替作业.如预备动作:当左手插件,右手要做好插件准备(极性识别),可以 随时将零件插入,反之亦然,尽量缩短等待的间.2.插件顺序原则: A、零件由小至大插件(可防止大零件挡手).B、水平方向由右至左插件(输送带由左至右流线).C、垂直方向由上至下插件(可避免手碰到下方零件) 3.外观相同但规格不同之零件,不排在同一站或相邻站.4.含固定脚之零件,需于前3站插件完毕(防止引起跳件).5.有方向性零件之插件原则: A、方向相同之零件排于同一站.B、不同方向之零件不排在同一站.6.PCB 板上无印刷及标识、防呆孔时,将正确插件及零件位置图片作标识.7.同一站内零件种类(盒)以不超过五种为原则(可保持零件盒在正常作业范围内).8.零件盒摆放位置顺序需与双手动作顺序相符.9.分开作业:左右手的零件要分开,不可右手抓左边零件槽的零件、左手抓右边的零件.10.排站时,以一人插 6-8 颗零件时,效率最佳.最大工作区域 装配点
最佳工作区域
作业员插件标准作业范围: 最佳工作范围:以肩算起水平180 度 47.4CM.正常工作范围:以肩算起水平180 度 57.0CM.最大工作范围:以肩算起水平180 度 72.9CM.
二、生产中所用电子元件的单位及换算关系 电阻:1Mohm=103Kohm=106oh 电容:1F=106μF=109nF=1012PF 电感:1H=103mH=106μH 电压:1KV=103V=106mV 电流:1A=103mA=106μA 频率:1MHz=103KHz=106Hz
三、色环电阻中颜色与数值的对应关系 黑 0 100 棕 1 101 ±1% 红 2 102 ±2% 橙 3 103 黄 4 104 绿 5 105 兰 6 106 紫 7 107 灰 8 108 白 9 109 金 银 有效值 倍率 误差 10-1 ±5% 10-2 ±10% ±0.5% ±0.2% ±0.1% 1.当为四环电阻时前二环为有效数字,第三环为倍乘数,第四环为误差,且误差只有金银两种。 2.当为五环电阻时,前三环为有效数字,第四环为倍乘数,第五环为误差,且误差有棕、红、绿、兰、紫、金、银。
四、常用电阻、电容误差经常采用字母来表示: F:±1% J:±5% K:±10% M:±20% Z:+80%-20%
五、常用元件的符号表示方法: 电阻:R 电容:C 电感:L 二极管:D 三极管:Q 集成电路:IC(U) 晶振:Y 或 X 继电器:K 变压器:T
六、SMD 元件规格 0603、0805、1206 等均以英制表示,如:0805 表示长为 0.08 英寸,宽为 0.05 英寸。
七、生产中常用有极性元件:
1、电解电容
2、钽电容
3、集成电路
4、二极管
5、三极管
6、继电器
7、变压器
8、排阻(DIP)
1、电容(Capacitor)元件符号为 C。 电容单位为法:PF、MF、UF、NF、F 电容的容量换算关系:1F=103MF=106UF=109NF=1012PF
2、分类: 电解电容 (有极性) 钽电容 (有极性) 瓷片电容 (无极性) 独石电容 (无极性) 聚脂电容 (无极性)
3、电感(Inductor)元件符号为 L。 电感的单位为亨:H、UH、MH 电感量换算关系:1H=103MH=106UH=109NH 分类:色环电感 图标符号: 磁珠电感 绕线电感元——单股绕线电感无方向性,多股绕线电感则有方向性磁芯电感
4、二极管(Diode)元件符号为 D 图形符号: 分类:稳压二极管用干电池的两极接触发光二极管的两极、若发光,则干电池 发光二极管 正极一端接的二极管的一端为正级,双导向二极管无方向性。 双导向二极管 普通二极管
5、三极管(Triode) 元件符号为 Q 图形符号:三极管极性无件 电路原理分类: 1.PNP b 表示三极管的基极 2.NPN c 表示三极管的集电极
e 表示三极管的发射极 封装形成分类:
2、金属屏散式封装 塑料封装 功率三极管
6、集成电路(IC) 集成电路上方向标志:圆点、一条竖线、一个缺口等表示第一脚位置,对应 PCB 丝印缺口位 置插入(PCB 方型焊盘表示 IC 的第 1 脚) 注意集成电路的脚序排列:从第 1 脚数起,逆时针排 列
7、晶振(Crystal) 晶振元件符号为 Y 或 X 图形符号为, 为无极性元件。 晶振的外壳需 接地,起屏蔽作用。 晶振的引脚不得与外壳短接。
四、电子元件插件标准 1.二极管插件标准 正确 错 误
2.发光二极管 3.电解电容 4.钽电容
5.保险丝座&蜂鸣器 6.三极管&稳压管
7.桥式整流二极管(桥堆) 正确 错 误 8.I C 正确 错 误 9.插 座 正确 错 误
10.变压器 正确 错 误
五、插装零件成型作业要求 1.功率小于 1W 的二极管、电阻、色环电感、保险管、磁珠、色环电容等元器件的成型(卧式)。 说明: A.共进 3.2±0.1mm 外协 6.0±0.2mm B.90°±5° C 随不同产品进行调整 要求: a.组件成型后,组件应平贴 PCB 板,组件的外表不能损伤,组件脚成型印痕(损伤)深度不超 过组件脚直径的 10%。 b.组件脚跨距与 PCB 板的焊孔间距应一致。 2.功率大于 1W 的二极管、电阻等元器件的成型(卧式)。 说明: A.共进 (D+3.2)±0.1mm 外协 (D+6.0)±0.2mm B.90°±5° C.随不同产品进行调整 D 浮高 3~6mm 要求: a.组件成型后组件体浮高 PCB 板面高度(PCB 板距组件体下缘高度)为 1.5-3mm,功率越大,浮 高的高度相对越高。
b.组件脚成型印痕(损伤)深度不得超过组件脚直径的 10%.c.组件脚跨距 C 与 PCB 板焊孔间距应一致。 d.同一种规格组件浮高高度应一致。 e.组件插装到位后, 组件体不平行于 PCB, 其倾斜范围为: L2-L1≤1.3mm
3 独石电容、瓷片电容、钽电容、金膜(绦沦)电容等元器件的成型。BA 5.3.1 图示说明: A 共进 3.2±0.1mm 外协 6.0±0.2mm B 随不同产品进行调整 B 要求: 元件成型后元器件的包漆部分不能插入 PCB 板(成型时,从引脚非包漆部分算起) ; b.元件脚跨距 B 与 PCB 板焊孔间距应一致。 c.元件脚成型印痕(损伤)深度不得超过元件脚直径的 10%。 d.元件脚包漆部分允许有轻微裂缝或碎裂, 破裂处不得延至元件体本身漆皮部分, 下列允许接收的图示: A 4.电解电容、晶振(立插)、发光二极管、大功率立插电感等元器件成 型。 图示说明: A 共进 3.2±0.1mm 外协 6.0±0.2mm B 随不同产品进行调整 要求: a.元件成型后元件体(以最突点算起)应平贴 PCB 板;元件外表不能损伤,正、负极标示应清晰; b.元件脚跨距与 PCB 板焊孔间距应一致(若不一致,元件脚长度须作相应的调整) ; c.元件脚成型印痕(损伤)深度不得超过元件脚的直径的 10%。 5.小功率的三极管、三极管封装形成的 IC 等元器件成型。 图示说明: A 共进 3.2±0.1mm 外协 6.0±0.2mm B 若需锁附于散热片上,则 A 应从散热片底部开始计要求: a.元件成型后, 元件体浮高 (本体下缘与 PCB 板) 高度为 4-6mm。 b.元件脚成型印痕(损伤)深度不得超过元件脚的直径的 10%。 6.集成电路、集成电路封装形式的电阻排、光藕等元器件的整型。 图示说明: B 随不同产品进行调整 要求: a.元件成型后,元件体要能平贴 PCB 板.b.元件脚距 B 与 PCB 板焊孔间距应一致。 c.元件插入 PCB 板时应轻松自如, 元件脚不得有变形、弯曲等不良现象。
7.卧装的电解电容、功放管、大功率三极管、大功率二极管,发光二极管等元器件的成型。图示说明:3.2±0.1mm 3.2±0.1mm 要求: a.元件成型后,元件应平贴 PCB 板面(电解电容类) ; b.元件散热面(根据工艺要求或实物丝印面)应平贴 PCB 板面(大功率三极管类) ; c.元件安装孔与 PCB 板安装孔同心或元件在丝印框内; d.成型时避免触及元件脚根部; e.元件脚伸出 PCB 板面长度 L 为 1.0-1.5mm。 8.跨接线(跳线)的成型: 图示说明: A.5±0.2mmB90°±5°C 随不同产品进行调整
要求: a.元件成型后,元件体应平贴 PCB 板; b.元件脚跨距与 PCB 板焊孔间距应一致; c.元件脚成型印痕(损伤)深度不得超过元件脚直径的 10%。 9.立插的色环电感、二极管、电阻的成型: 图示说明: A.共进 3.2±0.1mm 外协 6.0±0.2mm B2~3mm C 随不同产品进行调整
要求: a.元件成型后,元件体应平贴 PCB 板; b.元件脚跨距与 PCB 板焊孔间距应一致; c.元件脚成型印痕(损伤)深度不得超过元件脚直径的 10%。 10.成型电脑主板或双面板上跨距与 PCB 孔距相符的元件时,脚长剪为 3.2±0.1mm。 11.特殊元件成型,需按照特殊成型工艺或样品。
六、插件/补焊/后焊的作业要求 1.切板工位注意切板边的 SMT 零件,以免切板时撞伤或损坏电子零件。
2.切板工位每周要求做好切板机器表面周边的卫生,及时去除尘灰。3.插件工段物料员发料时,应特别检查该物料是否为无铅电子料(物料编号不同) ,各物料代码 最后一位为(L)的代码均为环保电子材料。 4.物料员注意将有铅与无铅物料区分放置,并做好标示牌。无铅物料放在物铅物料区域。 5.发板投入生产时,要注意检查该产品 PCB 板上是否有环保〝Logo〞或贴有〝无铅+软件版本号 〞字样的无铅标示, 与拉长同时确认 OK 后才投入流水线.存放、周转无铅环保产品使用的周转 车、物料架、防静电架要贴有无铅标示.6.插件员工要注意作业使用的物料、作业指导书上均贴有无铅标示,在 10 栋生产无铅产品时, 物料盒上要贴有无铅标示。在 4 栋生产无铅产品时,物料盒无需加贴无铅 LOGO。 7.作业前每位员工要求戴好接地良好的防静电手环。作业指导书及 BOM 单上均有无铅及 ROSH 标 示,各物品代号带有 L 字识别环保电子材料。 8.QC 检查:QC 补料时,不得随意在废组件盒中找物料补上(应经拉长和 IPQC 确认是否为无铅物 料).9.过炉放载具:要注意载具上要贴有或刻有无铅及标示,载具要及时清洁干净,无铅环保产品对 干净要求比较高。 10.取板、卸夹具要注意取板时轻拿轻防,严禁堆板、叠板、甩板。避免基板碰撞等制程不良。 11.剪脚:作业时注意剪钳不能撞、碰到周边零件,不能碰撞焊点避免造成锡裂.零件脚允许露出 PCB 底板 1.0-1.5MM。除特殊零件要求,按具体作业指导书规定。 A.补焊线在过波峰后进行剪元件脚作业时, 剪脚工位必须用剪脚罩,将 PCB 板放在透明罩内进 行剪脚作业,以防元件脚飞溅伤人,或落在其它 PCB 板的插槽(座)内,流水线及地面上,作业 工具可使用斜口剪钳或气剪.B.手拿板略倾斜与桌面成 45 度,剪钳顺着引脚排列方向剪。 C.剪脚完成或下班时,需将元件脚倒在回收箱内,不得将元件脚直接扫在流水线或地面上.D.当天补焊线若无剪脚作业,需将剪脚罩放置于料架.12.剪脚工位作业注意事项: a.元件脚长一般控制 1.0--1.5mm,若有特殊要求见相关的作业指导书.b.不可剪到零件脚焊锡点,以免零件脚裂锡。 c.剪脚一定要按照左图示放入剪脚罩中操作,并且剪脚罩中不可放板卡或其他杂物。 d.不能把双手放在剪脚罩外,以免残脚飞溅伤人,或落在其它PCB 板的插槽(座)内,流水线及 地面上。 13.修补: 波峰焊后焊接不良的产品需要维修时, 作业铅要求将工作台面清洁干净.要注意使用的 无铅烙铁、烙铁海绵、锡线、助焊剂、环保水为无铅专用及贴有无铅的标示,并与有铅使用的 工具隔离开,以免混用.无铅烙铁温度设定在 360℃~380℃,焊接每个点时间控制在 3 秒。 14.补焊工位作业时,严禁敲打、甩 RoHS 环保烙铁,标准作业是焊接作业时烙铁头沾有多余的锡 或氧化物,请在环保烙铁海绵上擦拭烙铁头。这样可以去除锡渣及氧化物,员工不必考虑其它 因素,严格安标准作业有效维护烙铁头及烙铁的寿命。 15.刷板、清洁:要注意工作台面要求清洁干净,使用的防静电刷、环保清洁水、要贴有无铅标 示。
七、清洗作业规范: 1.清洗作业员工要求佩带防静电带或防静电手套,避免损坏元器件; 2.将待清洗的 PCB 板整齐地摆放在提篮中,主板等大板类摆一层,小卡类摆放不超过四层,应 竖放并且不要焊锡面背对背放; (注: 若主板上的 DB 头等插座引脚较长且锋利容易划伤 PCB 板及 元件,清洗时必须用报废板将相邻两主板隔离。 )
3.将装满 PCB 板的提篮放入超声波清洗机中进行清洗;清洗机各参数设定,可见《清洗机操作 工艺规范》 。 4.超声波清洗完成以后,将提篮中的 PCB 板取出,整齐地摆放在料筐内; 5.从料筐内取出 PCB 板,对 PCB 板表面进行目视检查,应无残留松香、污渣、白粉、水印、黄 点、锡珠等不良; 6.如发现有不干净之处,用牙刷蘸少许环保水(比重 0.85-1.05g/cm2 ,无色透明液体)对该 处进行手工刷洗,时间约为 3-5 秒钟,并用干布或毛刷擦干净,注意环保水不能蘸太多而影响其 他干净之处; 7.如发现有锡珠存在,用针尖将它挑掉; 8.PCB 板在 SMT、DIP 工段生产以后,要求在当天以内完成清洗,防止腐蚀 PCB 板而导致清洗不 干净; 9.浸泡板时,PCB 板浸在环保水中的时间不能超过 30 秒,以避免时间过长腐蚀元器件。 10.变压器、继电器、蜂鸣器、电池、各种标贴、保险管、电位器、大功率碳膜电阻以及特殊工 艺要求的元器件不能进行超声波清洗,必须采用手工清洗(手工清洗参照步骤 6) ; 11.对于免清洗的 PCB 板(有 DIP 后焊元件的 PCB 板) ,除特殊工艺要求外,必须采用手工刷洗后 焊元件的焊点部位及其他有不干净之处(手工清洗参考步骤 6) ; 12.环保水带有腐蚀性,清洗过程中注意检查元件外表有否损伤(如:电容缩皮、电阻色环脱落、塑胶件熔化等) 。 13.作业过程中注意保护眼睛及皮肤,防止环保水溅入眼睛内。 (12)点胶:要求热溶胶枪贴有无铅标示,溶胶是环保材料。注意胶强的温度不能过高,以免自动 溢出溶胶造成浪费。点胶要求不能有拉丝、量不能过多、均衡。 (13)QC 检验:按照公司外观检验标准及 IPC-A-610D 来检验环保产品,注意产品上要贴有无铅环 保标示.(14)周转下一制程,要注意使用的周转车、防静电箱等均要贴有无铅标示。严格与有铅产品区分 开.以免造成污染.(15)DIP 导入无铅制程时,生产线、设备、工作台面、工具、夹具要求严格清洁干净。
八、板卡摆放、周转注意事项 1 半成品用防静电托架的摆放。 板边 1cm 内无零件的板卡在楼层间,车间内及生产线周转时可用防静电托架装,装板时方 向朝同一侧,每槽放一片,若有体积大、高的元件,可隔一或两个槽放一片,板与板间必 需留有间距不可碰到一起 (长度超过 35cm 的板不可用防静电托架摆放,必需用周转箱,以 免板变形)。 2.半成品用周转箱、防静电泡棉的摆放。 2.1 板边 1cm 内有元件的板卡在楼层间周转时必需放于周转箱中。 2.2 板卡放置在非刀卡箱中进行周转时,PCB 应朝同一方向放置,且板与板间以防静电泡棉 隔开。 2.3 板卡放置在刀卡箱中进行周转时,一个卡槽内放置两块板,反面相对且用防静电泡棉隔 开.2.4 板边 1cm 内有元件板卡在作业过程中因堆板需要暂存或在线别间周转时,必需用防静电 泡棉隔开平放于台面。 3.防静电泡棉的使用要求: 3.1 25*16cm<板尺寸≤25*32cm,使用 25*32*1cm 防静电泡棉。较小板卡可多块摆放于防静
电泡棉上.3.2 板尺寸≤25*16cm,使用 25*16*1cm 防静电泡棉。 3.3 板尺寸>25*32cm,使用 36*26*1cm 或 40*26*1cm 防静电泡棉。 3.4 在工作台面叠放时,最高不可超过三层,若超过,拉长即需调整工位分配,使各工位间 相对平衡。 3.5 板卡的摆放方向必须一致,由拉长或组长指定各工位板卡的摆放顺序,下工序作业前检 查状态是否与指定的状态相同。 4.板卡的周转: 4.1 用周转箱周转时,堆放总高度不可超过 2.5m(即 60cm 高度的周转箱只能放 4 层),且箱与箱 结合处需以宽胶带固定,搬运过程中需扶住周转箱以保持其平稳。 4.2 在楼层间用托架和周转车周转时,每层架上只能放一层托架,且需用泡棉卡条将板上侧卡 住或用高温胶纸将板卡与托架缠住,以免运输过程中震动导致板卡碰撞,跌落。 4.3 用防静电泡棉隔开的板在线别间周转时,叠放于周转车上最高不可超过四层。且推拉时需 注意保持周转车的平衡,以防板滑动、跌落。 4.4 在 4 幢和 10 幢间周转时,若遇雨天,需以收缩膜缠住周转车或周转箱,以防淋雨或漏雨.九.10 栋与 4 栋产品、半成品周转注意事项: 1.4 栋 SMT 若存在有铅的电脑主板、LEA、ADSL 周转到 10 栋时,使用托架或红色珍珠绵叠放于 周转车周转。注意凡是周转 10 栋的半成品一律使用红色珍珠绵防护。 2.4 栋 SMT 周转无铅的半成品到 10 栋生产有铅插件时,使用托架或红色珍珠绵叠放于周转车 周转 (所有从 10 栋转到 4 栋的周转车必须清扫干净才能用于无铅使用, 10 栋转到 4 栋的 从 静电托架必须清扫干净才能用于无铅使用) 。 3.10 栋 HSMT 周转无铅半成品到 4 栋生产无铅插件时,使用黑色的珍珠绵叠放于周转车周转或 使用 4 栋无铅专用静电托架周转。 4.10 栋 DIP 周转有铅的半成品到 4 栋测试时,使用红色的珍珠绵存放于周转箱周转。并在周 转箱外注明“有铅专用”字样(到条码打印组打印“有铅专用”标签) ,0km、4.2km、老化、维修及组、包装等各工序都必须使用贴有“有铅专用”字样的周转箱进行周转,用完之后由 包装线派人将“有铅专用”字样的周转箱退回 10 栋 3 楼。 5.4 栋有铅的产品转 10 栋维修或重工时,有铅产品使用红色珍珠绵存放于周转箱周转。并在 周转箱外注明“有铅专用”字样。 6.10 栋生产的有铅 LEA 产品转到 4 栋清洗、LEA 测试、包装时,使用红色珍珠绵叠放于周转车 周转(注:LEA 产品的有、无铅清洗必须在海外产品的组装线体上两边分开作业,其中有、无清洗工具如手套、毛刷、环保水瓶等由拉长统一管理发放,以防污染) ;LEA 包装使用的 有、无铅手套、电批头等由拉长统一管理发放,以防污染。
7、各工段使用的外箱标示单要求:有铅产品使用原来的标示单(无“Pb”标记) ,无铅产品使 用新的标示单(有“Pb”标记) 。
十、无铅/恒温烙铁使用与管理 1.使用无铅/恒温烙铁时,需先确认烙铁的电源线及静电接地线是否联接良好,然后打开电源 开关,等待烙铁升温到设定工作温度后,才可以作业。 2.无铅/恒温烙铁: 焊接 SMT 零件时温度设定为:330℃±10℃, 焊接 DIP 零件温度设定为:370℃±10℃.维修工位温度设定为:350℃±10℃.最高温度:380℃,使用无铅烙铁焊接零件时间:最多 3~5 秒,循环次数:2 次。直径为 1MM 以上的单一焊点受热时间不得少于 2 秒.1.IPQC 每天对各生产线开线或换机种前,要求对生产线所作业使用的无铅/恒温烙铁进行温 度检测。 2.无铅/恒温电烙铁温度测定,被检测的烙铁预热 5 分钟后,将烙铁头置于烙铁温度测试仪之感温 热隅上,待温度显示恒定之后,即可读取温度显示值,IPQC 详细记录“恒温烙铁温度测量记录 表”.3.IPQC 在生产线检测到不符合或达不到焊接要求的无铅/恒温烙铁,立即要求作业员停止使用并 要求更换新的烙铁头方可作业。并书面通知该车间的负责人或物料员将不合格的无铅/恒温烙铁 退回工具仓库维修。 4.生产线依据实际生产需求开出《工具申请领用单》到工具室领用,在生产线发现不合格的无铅 /恒温烙铁温时,在烙铁上做好不良标示并退回工具室。 5.工具室收到生产线退回的不良的、不符合焊接要求的无铅/恒温烙铁温时,及时通知工具主管 联系供应商处理。无铅/恒温烙铁温放置在工具室要做好不良品、良品标示 无铅/恒温烙铁温烙铁头的更换与管理 1.作业时,烙铁头有出现氧化变黑焊接不上锡、烙铁头出现空洞等不良时立即更换烙铁头。 2.生产线到工具室更换烙铁头时, 需工具主管确认后并在领用单上签名, 工具室发放烙铁头时注 意确认领用单上是否有工具主管确认。 3.工具室保管好生产线退回来的烙铁头,集中放置管理,由工具主管确认不能修复的烙铁头, 再统一报废处理.修复烙铁头可使用 Weller 的 WPB
1、QUALITEK 的 DELTA 或烙铁头保护剂修复烙 铁头。 无铅/恒温烙铁的使用焊接流程图
无铅/恒温烙铁烙铁禁止的动作 1.焊接时不可用力挑或挤压被焊接之物体、焊盘.2.无铅烙铁不可接触到有机物如塑料、润滑油、化合物…等.3.不可用粗糙面之物体磨擦烙铁头.不可加塑料、油脂类等任何化合物于沾锡面。
4.作业时严禁甩、敲打无铅烙铁头,以免损伤及减短烙铁头的使用寿命。因为电镀的关系,烙铁 头绝对不要用刀锉或磨削烙铁头; 1.烙铁头产生氧化物及松香残留物时,在湿海绵上擦拭将余锡及脏物去除干净,海绵保持 50%滋 润状态.2.海绵加水状态是,海绵泡于水中,捞起后用手掌拧海绵至不会滴水为止。 3.烙铁用完后加锡于烙铁头尖端,使整个烙铁头尖端包覆住一层锡。 4.保持烙铁头表面一直有锡涂覆,只有在使用前才擦拭,并且用完后立即加锡保养.5.如果烙铁头不上锡,利用助焊剂和清洁海绵来清洁烙铁头表面.6.在关闭烙铁电源之前给烙铁头加锡,型成盘鼓起的焊锡。不要将烙铁头上多余的焊锡去除,这 些多余的锡会在烙铁头回热的情况下保护上锡表面,防止氧化.1.勿施压过大,在焊接时,请勿施压过大,否则会使烙 铁头受损变形。只要烙铁头能充份接触焊点,热量就可以 传递。另外选择合适的烙铁头也能帮助传热。
2.不使用无铅/恒温烙铁时,应该将烙铁放在焊铁架上,以免烙 铁头受到碰撞而损坏。
选择合适的烙铁头 1.选择正确的烙铁头尺寸和形状是非常重要的, 选择合适的烙铁头能使工作更有效率及增加烙铁 头之耐用程度。 选择错误的烙铁头会影响焊铁不能发挥最高效率, 焊接质量也会因此而减 低。 2.烙铁头之大小与热容量有直接关系,烙铁头越大,热容量相对越大,烙铁头越小,热容量也 越小。进行连续焊接时,使用越大的烙铁头,温度跌幅越少。此外,因为大烙铁头的热容量高, 焊接的时候能够使用比较低的温度,烙铁头就不易氧化,增加它的寿命。 3.短而粗的烙铁头传热较长而幼的 烙铁头快,而且比较耐用。扁的、钝的烙铁头比尖锐的烙铁头能传 递更多的热量。一般来说,烙铁头
尺寸以不影响邻近组件为标准。选择能够与焊点充份接触的几何尺寸能提高焊接效率。
选用活性低的助焊剂 活动性高或腐蚀性强的助焊剂在受热时会加速腐蚀烙铁头,所以应选用低腐蚀性的助焊剂。 注意:切勿使用沙纸或硬物清洁烙铁头。 活 组 性 低 腐 蚀 性 低
第13篇:制程检验员岗位职责.2
机加工青阳分厂制程检验员岗位职责:(江 伟)
每日:
1、严格按“首检操作流程”对员工送来首件产品进行检验并记录;
2、负责制程检验所用量具管理,进行日常维护、校准工作;
3、对已检有质量问题的产品及时隔离并做好标识 ,并在流转卡上签字滞留;
4、负责对现场各工序产品质量进行巡检;
5、对不良品及时填写每日质量问题反馈单和不合格品报告单,对接收产品按车间开《产品交接单》并在下班后找车间管理人员签字,相关联交车间管理人员;
6、对员工的完工产品抽检合格后在流转卡相应工序栏上签字;
7、负责对待发热处理产品的签单,检查流转卡热处理前各工序是否完工,如有异常反馈至检验组长和车间管理人员并隔离标示;
8、及时反馈并制止制程中发生的产品质量问题;
9、负责在进料检验员下班后外协单位来料检验,合格后入库核对,对异常及时处理并在交接班记录中注明;
10、当班首检记录表在下班后交车间管理人员存档,并反馈当班员工首检执行情况;
11、做好交接班记录,和责任区域6S工作;
12、下班前检查核对本班次滞留产品名称、数量与交接单、报告单、质量报表、实物是否吻合,如有差异及时处理;
13、做好两班交接,对当班发生的产品质量异常情况进行沟通;
14、完成上级领导安排的其他工作任务;
每周:
1、每周一参加车间早晚会,对上周发生的产品质量问题进行宣贯培训;
2、每周二参加机加工青阳分厂例会,总结汇报各车间上周产品质量状况及检验组工作情况;及时落实例会相关工作并反馈;
每月:
1、每月根据机加工青阳分厂安排,进行月底盘点并做好不良品的处理工作;
2、对本月质量记录进行整理、标识、归档;
第14篇:IPQC制程巡检工作内容
IPQC制程巡检工作内容
一.产前工作准备
1.根据生产计划,确定生产机型的BOM及ECN与在线物料是否一致,确定检验规范;
2.上线物料是否符合产品BOM要求,根据产品BOM及ECN核对上线物料种类是否齐全,型号及规格尺寸是否正确?
3.是否悬挂SOP,排拉是否按SOP工序流程安排?
二.制程控制中工作内容
1.配合生产做首件确认,首件对料OK,没有经过测试不准过炉,接收首件及完成首件时,须签名和注明具体时间;
2.认真按时填写巡检报表和确认仪器点检表。检测记录静电环,烙铁温度,助焊剂比重及漏电测试及电批扭力1次/2H;
3.仪器、治具是否正常;确定在仪校有效期内;确认设置的参数与产品要求一致,在线员工是否有点检OK样品及NG样品?是否有做点检记录?
4.新产品、新员工是否重点巡查,特采、代用、试产、让步放行的必须重点稽核、记录情况及结果反馈;
5.仪器定位摆放,产品无堆积,轻拿轻放,员工是否自检、互检合格品才下拉;
6.不合格品是否有标识,不合格品是否准时记录;
7.任何来料及作业不良造成物料无法正常使用,要及时开具《品质异常联络单》反馈给相关单位并进行追踪;
8.测试与外观检验工位不良比例超过3%时要求产线停线;
9.检验报表记录是否完整,清晰,是否一目了然,是否每小时核算记录一次“总数”,“不良数”;10.有客诉及退货情况是否了解及跟进。返工情况必须跟进、统计不良及结果反馈,保留三现“现状”“现物”“现场” ;
11.客户对产品标准放宽及对某一项功能、外观全部接受时需要求客户进行表单签字确认或签限度样.;
12.下班前统计好报表,每天早上7:50分开早会,每周星期五晚上19:00开品质周会。
上述工作内容都清楚明确,且严格执行到位。 签名:
第15篇:制程工程师 PE相关说明
制程工程师 英文Proce Engineer简称PE,制程工程师也叫工艺工程师。
制程工程师是制定整个生产流程,分配各个部门的任务,负责制造过程中的各个细节,并制定WI或OI(标准作业指导书)的制程文件,对制程进行管理和控制。制程工程师掌管整个生产各种装配元件及辅助材料的选型与验证,工治具的发明与制作。
制程工程师提高生产效率以及生产良率,降低报废率以及耗材与人力成本。属于整个制造过程的核心人物。
工作内容
一、制作及更新新产品的BOM,并为新产品准备相应的物料;
二、制作新产品的生产工艺流程,标准工时的计算帮助PES安装和调试新产品所需要的设备;
三、对IQC(进料检验)抽检不良的料件进行评审,然后对不良的料件或图纸提出ECR,并且对ECN的发行及追踪;
四、整机的安装,然后通过做各种评估测试(设备和物料方面),使其达到性能最佳;
五、不断改善工艺流程,提高产品的产量及质量,降低生产周期;
六、每天统计产品的良率,及时发现良率低的原因并提出解决方案;
七、各个部门进行沟通,了解产品的最新状况及各个部门遇到的问题,并帮助解决问题;
八、发明制作各种生产辅助工治具,提高作业效率良率。
九、撰写作业指导书(OI或WI),用以指导产线作业;
撰写SOP(标准作业程式)以及各类制程管控文件,用以明确生产流程步骤,保证稳定生产,逐步提高。
发展前景
一个好的PE是很需要耐心和吃苦精神的,当然,还有很多很基础的知识。如果一个公司正常的话,PE是很累的,很累的话也就意味着要解决很多问题,所以还是有很大的成长性的。
制程与工艺是PROCESS翻译成中文的两种不同说法,其实一样,不过涉及很多方面,从新产品导入,Bom与工艺文件制作,工艺的控制与改善,直到成品半成品的出货。应该说做这个职位能为以后更高层次的发展能够打下很好的基础,很多经理(Managers)都是从制程工程师(Proce Engineer)出身的。
1.物料清单(Bill of Material, BOM),是指产品所需零部件明细表及其结构。具体而言,物料清单是构成父项装配件的所有子装配件、零件和原材料的清单,也是制造一个装配件所需要每种零部件的数量的清单。
物料清单表明了产品→部件→组件→零件→原材料之间的结构关系,以及每个组装件包含的下属部件(或零件)的数量和提前期(Lead Time)。这里,“物料”一词有着广泛的含义,它是所有产品、半成品、在制品、原材料、毛坯、配套件等与生产有关的物料的统称。
制程工艺
制程工艺就是通常我们所说的CPU的“制作工艺”,是指在生产CPU过程中,集成电路的精细度,也就是说精度越高,生产工艺越先进。在同样的材料中可以制造更多的电子元件,连接线也越细,精细度就越高,反之,CPU的功耗也就越小。
制程工艺的微米是指IC内电路与电路之间的距离。制程工艺的趋势是向密集度愈高的方向发展。密度愈高的IC电路设计,意味着在同样大小面积的IC中,可以拥有密度更高、功能更复杂的电路设计。微电子技术的发展与进步,主要是靠工艺技术的不断改进,使得器件的特征尺寸不断缩小,从而集成度不断提高,功耗降低,器件性能得到提高。芯片制造工艺在1995年以后,从0.5微米、0.35微米、0.25微米、0.18微米、0.15微米、0.13微米、90纳米、65纳米45纳米32纳米一直发展到目前最新的22纳米,而16纳米制程工艺将是下一代CPU的发展目标。
计算公式:以当前处理器的制程工艺乘以0.714即可得出下一代CPU的制程工艺,如90*0.714=64.26,即65纳米。
提高处理器的制造工艺具有重大的意义,因为更先进的制造工艺会在CPU内部集成更多的晶体管,使处理器实现更多的功能和更高的性能;更先进的制造工艺会使处理器的核心面积进一步减小,也就是说在相同面积的晶圆上可以制造出更多的CPU产品,直接降低了CPU的产品成本,从而最终会降低CPU的销售价格使广大消费者得利;更先进的制造工艺还会减少处理器的功耗,从而减少其发热量,解决处理器性能提升的障碍,处理器自身的发展历史也充分的说明了这一点,先进的制造工艺使CPU的性能和功能一直增强,而价格则一直下滑,也使得电脑从以前大多数人可望而不可及的奢侈品变成了现在所有人的日常消费品和生活必需品。
总体来说,更先进的制成工艺需要更久的研制时间和更高的研制技术,但是更先进的制成工艺可以更好的提高中央处理器的性能,并降低处理器的功耗,另外还可以节省处理器的生产成本,以便降低售价。
制程能力
所谓的制程能力是指工序在一定时间里,处于控制状态(稳定状态)的实际工作能力。制程能力指数是指制程能力满足产品质量标准要求(规格范围等)的程度,或是工序在一定时间里,处于控制状态(稳定状态)下的实际加工能力。它是工序固有的能力,或者说它是工序保证质量的能力。这里所指的工序,是指操作者、机器、原材料、工艺方法和生产环境等五个基本质量因素综合作用的过程,也就是产品质量的生产过程。产品质量就是工序中的各个质量因素所起作用的综合表现。对于任何生产过程,产品质量总是分散地存在着。若工序能力越高,则产品质量特性值的分散就会越小;若工序能力越低,则产品质量特性值的分散就会越大。
在管理状态的制程上,该制程具有达成品质的能力,称为制程能力。正确地维持作业的条件或标准且在计数上、经济上良好且安定的制程上,量测产品的品质特性,通常以 或有时仅以6 来表示。
制程能力指标(proce capability indices ( 与 )):制程能力指标是一些简洁之数值,用来表示制程符合产品规格之能力。 指标之值可视为制程之潜在能力,亦即当制程平均值可调到规格中心或目标值时,制程符合规格之能力。 指标之值与 指标类似,但将制程平均值纳入考虑。制程能力分析(proce capability analysis):在产品生产周期内统计技术可用来协助制造前之开发活动、制程变异性之数量化、制程变异性相对於产品规格之分析及协助降低制程内变异性。这些工作一般称为制程能力分析(proce capability analysis)。
制程检验员
岗位职责
过程检验员岗位职责
1、负责委外加工的半成品(SMT加工完成)进行首检工作(依据BOM和工艺文件);
2、负责厂内成板段完成后成品的首检工作(依据BOM和工艺文件);
3、二楼的PQC负责MC产品出货包装首样检验工作;
4、巡检过程中各道半成品的抽检工作(依据作业指导书以及工艺文件);
5、巡检过程中各仪器点检记录和机器维护记录的检查工作;
6、产品加工过程中的方法以及过程的检查(依据作业指导书和工艺文件);
7、各道5S的执行情况;(此项包括产品的摆放,隔离,区分,标识等);
8、各道出现批次不良品的标识,隔离;
9、一楼自有产品的PQC出货时抽检成品;
10、一楼自有产品的PQC 出货时全检所有出货成品的配件;
11、二楼MC产品的PQC在测试完成后抽检测试完成后的半成品;
12、二楼MC产品的PQC 在包装时抽检在线包装成品;
13、各车间维修记录的录入;
14、首件完成后的记录;
15、制程品质异常的提出(抽检批次不合格)和协助QE处理各道因为不良率超过界限值提出的品质异常单;
16、一些临时交办的事宜;
工作内容
1、首检工作:产品切换、员工调岗时作首检;依图纸、检验标准和检验指导书进行检验;判定是否合格,可否批量生产。
2、制程巡检工作:依规定定期对加工过程进行抽检;检核是否依工艺标准、检验标准、作业指导书作业;
发现制程品质问题与隐患;协同相关人员对问题进行改善;填写检验记录。
3、制程不良品处置:查核不良品原因、数量;提出不良品处理方式(报废、返修等);协同制造、技术人员研究改善对策。
4、品管知识掌握:依ISO9000:2000程序行事;熟练掌握抽样方法的检测工具的使用方法;熟练掌握品质检验标准并严格执行。
第16篇:生产制程质量控制程序管理办法
生产制程质量控制程序管理办法
1、目的
通过对生产过程中的工序产品、成品质量的控制,确保不合格的产品不转序,进而确保产品质量。
2、范围
本办法适用于各部门生产过程中及仓库物料、库存产品质量控制。
3、职责
3.1 品质部负责生产过程工序产品、最终产品的检验控制。 3.2 品质部负责生产过程中的质量信息的收集、汇总和反馈。 3.3 品质部负责生产过程中检验状态标识。
3.4 品质部负责编制产品质量改进计划及完成情况的验证及考核。
3.5 品质部负责生产过程中的不合格品的及时鉴别、标识和记录,并负责组织其职责范围内的不合格品的评审。
3.6 品质部负责新产品及更改产品的质量检测记录,参与验证、试装、评审等生产准备过程的质量控制。
3.7 品质部负责提供作业指导书、产品技术条件等文件。 3.8 品质部负责模具最终书面验收及模具技术状态鉴定。 3.9 品质部负责检查各生产部门的日常工艺纪律执行情况。
3.10 品质技术部负责制订或组织制订不合格产品的返工(修)工艺技术方案。 3.11 仓库负责不合格品的处置,定制隔离、登帐、保管、及办理相关手续。 3.12 仓库负责库存产品储存、运输质量控制。
3.13 仓库、生产部门负责生产过程中工序间的运转储存及入库产品的转运质量控制。 3.14 生产部门负责生产过程中的产品自检质量控制。
4、工作程序
4.1 制程控制
4.1.1 品质部负责向生产单位提供生产制造标准及相关图纸、工艺卡。
4.1.2 生产单位按生产制造标准要求调整模具或生产工艺,确保后续产品符合工艺要求。
4.1.3 各生产单位严格落实产品首件检验机制,自检合格后交品质部进行首件检验。 4.1.4 品质部要严格按图纸、工艺卡、检具、样件进行首件检验,检验合格后,贴首件合格证做标识,并填写“检验记录单”。 4.1.5 首件检验合格后操作者应把首件放置在首件区,然后方可批量生产。 4.1.6在批量生产过程中,操作者应随时自检,以首件架上的工序产品作为自检依据,防止批量不合格品的发生。
4.1.7在批量生产过程中,质检员一般在1小时内进行一次巡检,填写“检验记录单”。巡回检验不合格时必须第一时间勒令操作者即刻停止生产,并通知相关生产主管及技术人员处理。
4.1.8 生产过程有机器或模具维修调整、工艺改变的,必须重新进行首件确认,并在第一时间替换之前首件。
4.1.9 五金及注塑件生产时,所有工序完成后,质检员应对该产品进行最终检验,填写“产品检验记录单”,检验合格后,粘贴产品入库“合格证”,注明产品名称、数量、日期并加盖检验章(合格证应粘贴在工位器具上,并清除旧标识)。 4.1.10 冲压车间生产时应尽量安排同一产品几道工序同时生产,为避免批量不合格品的发生,冲压作业员生产时必须不超过30PCS自检一次,下工序员工负责对上工序进行复检;专职质检员对末道工序使用检具检验时,必须同时对前道或前几道工序产品进行检验。
4.1.11 冲压产品首件检验时机:
a)每批产品生产开始,操作者自检合格的第一件产品。 b)设备调整后,操作者自检合格的第一件产品。 c)调整或更换工装后,操作者自检合格的第一件产品。 d)改变原材料、毛坯、工序后,操作者自检合格的第一件产品。 4.2产品运输控制
1、在制品、半成品和未入库的的成品由生产车间进行转运;库存产品由仓库负责运输。
2、在转运及运输过程中要注意防止磕碰、划伤、损坏、变形并保护产品标识和有关检验、实验状态标识,防止丢掉或被擦掉。4.3 产品贮存控制
4.3.1 生产现场的在制品、半成品应建立适宜的贮存场地,设置衬物垫,产品不能落地,应码放整齐、稳定,防止贮存过程中锈蚀、变形、损坏。 4.3.2 冲压车间必须使用合理的工位器具码放整齐,以便运输。
4.3.3 经检验合格入库的产品,由库管人员用规定的相应工位器具,码放在适宜的场地、库房、货架上。在保证运输工具通行的前提下应码放整齐,排列有序,并防止贮存过程中的锈蚀、变形、损坏。
4.3.4 库存产品应有完整的产品标识和检验、试验状态,不同状态产品要分开存放,做到储存记录清晰、完整、帐、卡、物相符
4.3.5 库存产品由库管人员每月检查一次,做好“库存产品巡检记录”,出库产品应做到先入先出。 4.4 不合格品的控制
4.4.1生产过程中发生的不合格品质检员应督促生产作业员及时分开摆放并做好醒目标识,质检员在相应记录单上做好记录。
4.4.2评审:生产过程中以及后期挑拣发现的不合格品由品质技术部会同生产部相关人员组织评审,根据不合格品状态或用户反馈信息的产品,由质检员开具“品质异常单”,交品质技术部现场技术人员,由技术人员在生产现场提出处置意见。当批量较大,会严重影响最终产品性能,或用户反映强烈的产品,质检员开具“品质异常单”,由厂部提出处置意见,上报公司主管领导作最终处置。 4.4.3不合格品的处置
4.4.3.1不合格品的返工(修),由品质技术部制订不合格产品的返工(修)工艺技术方案,由生产车间负责返工(修)。
4.4.3.2返工(修)后的工序产品、半成品,成品必须交专职质检员复检,专职质检员复检并在相应的记录上做好复检记录,返工(修)合格的产品方可转序或入库。4.4.3.3不合格品让步使用,必须经产品使用和品质部认可。
4.4.3.4不合格品有明显缺陷不能返工(修)或返工(修)不经济时,授权人员应在“不合格品通知单”处置意见栏填写“报废”,同时注明致废原因,由品质部核实后经厂长以上领导批准方可进行报废。4.5产品质量改进
4.5.1品质技术部根据用户反馈的质量指标及生产过程中发现的质量问题,分析原因,制订产品整改措施计划。
4.5.2每月初品质技术部对上月质量指标完成情况进行分析,废品损失原因分类,损失严重的产品。提报相关单位分析出致废原因(人为、模具、材料等)以便整改。 4.5.3厂部针对重点品质缺陷以书面形式落实的品质整改方案,责令各责任单位要按要求执行,按期完成回执。
5、奖惩方案
5.1 冲压部当月成品总量不良品返修率低于5%,报废率低于0.2%,奖励主管/五金工程500元,组长/质检员200元,物料员100元;不良品返修率高于10%,报废率高于0.5%,处罚主管/五金工程500元,组长/质检员200元,物料员100元。 5.2 面板/组装车间当月成品总量不良品返工率低于0.5%,最高批次返工低于100台奖励主管500元,组长200元,物料员/质检员100元;不良品返工率高于1%,最高批次返工高于300台处罚主管500元,组长200元,物料员/质检员100元。 5.3 所有不合格产品如未经正常程序私自报废的,对当事员工处以5元/件罚款(员工罚款最高100元/次),当事部门组长罚款2倍,当事部门主管罚款3倍。 5.4 对于厂部以书面形式责令落实的品质整改方案未能如期执行的,当事部门主管第一次罚款200元,并回复具体落实时间,下次还未能落实的加倍处罚。
第17篇:SMT制程管理的重要性
我对国外SMT厂家的多年,发现在SMT应用上,他们有多项工作做得不足够,其中一项是制造过程的管理工作。早前,[电子工业]的主编和我谈到我以往系列文间提及的制程管理应用概念,相信国内厂家也会用得着。因而我特写本篇来谈谈这方面的概念。
制程管理,译自英文中的Proce Management一词。由于我们把焦点放在SMT的制造技术上所以我把Proce译成(即制造过程)。其实Proce Manage-ment所涵盖的范围更广。本广只就SMT制造有关的范围加以探讨。
从THT到SMT的管理需求变化
制程管理,并不是专为SMT而同设的。但要较成功的应用SMT这门技术,正确的推行有必要的。制程管理虽不是门新的管理技术,但它得人们认识、重视、有效应用并比SMT这门技术来早。也正为这原因,许多由THT(插件技术)提升SMT的厂家并没有意识到在管理上需要做改革的工作。在THT制造环境下,忽略制程管理并不会为制造商带来太大的问题;但对於SMT制造工作而言,尤其是进入微间距和采用现今BGA和倒装片(Flip-Chip)之类技术的情况下,制程管理是不可或缺的管理工具。
制程管理为何对SMT应用那么重要?回答这问题,们得了解THT和SMT之间存在许多不同的地方,尤以下下旬 几项最为显著:
1、微型化-SMT发展的动力,主要是突破旧有组装技术对产品微型化的限制。由于THT本身的技术局限,不断提升微型化的程度。
2、质量因素-THT和SMT两者的组装技术不大相同,影响质量的因素也大分别。虽然在许多方面,SMT组装质量已证实比THT更及更可靠,但SMT保证中工作比THT较为复杂。
3、自动化-SMT的发明变带来了高度的自动化,此亦是SMT生产效率比THT更高的原因。
以上三点所带出的信息是:SMT成品检查不易进行;成品寿命或可靠性的变化幅度大;制程工艺对成品的质量影响日益深刻;返修成本和代价高;即时诊断和改正生产误差的重要性提高等等。而这些对制造商不利的因素正是需要制造管理来解决。 在THT制造管理的环境下,人们并不注重制程功能(Proce Capability)、制程整合(Proce Integration)等的应用和管理。一般做法是在试产时把设备调校到配合绝大部分的组装工作,当达到相当的合格率后就接入正式生产。及后,在生产线上设立了因定的检查站,把发现的不良品抽出返修 。本文为了方便解说,把以往这种简单的制造-检查-返修或淘汰的-贯做法称为‘制造管理’,有以区别本文提倡的’制程管理’,用以区别本文提倡的‘制程管理’。’制造管理’注重防止不良产品离厂,而‘制程管理’则把重点放在把制造方法加以合理化和优化(防止 不良产品出现是随这方法自然而来的)。‘制造管理’,在SMT生产中有以下几点不理想的地方:
1.不能照顾到成品寿命保证的问题;
2.生产效率难以达到最优化的状态,成本遂难以降低廉;
3.生产稳定性较差;
4.难以进行长期的改进;
5.由於组装基本变更和微型化,即使是同样的工作在SMT应用上也不易进行。
在市场对质量要求日益增高,对产品价格要求低,以及同行竞争日益增高,对产品价格要求低,以及同行竞争日益激烈的今天,如果厂商对上述问题仍坐视不理,继续沿习THT一贯的做法,不对生产管理加以改革,实在不是明智之举。
制程管理对SMT应用的帮助
制程管理方法如何避免或减低制造管理中如上述提到的那些问题呢?
首先制程管理在观念上有彻底而重要的改变、那就是不提倡检查,更不容忍错误发生。以往,制造管理相当大量的检查工序、检查活动,不论对成品的质量,或对生产的效率都有不良的影响。我们不难发现在许多工厂中,除非成品的不良率很高,否则一般如只有几个百份比的,在交货的压力下,都因检查-返修工作能应付而不加以追究。其实这方面的浪费,详细的计算也是相当可观的,在成本上一般绝非可以忽略的;而在质量学的观念上,任何返修工作都可能给成品质量添加了不稳定的因素。
但这可能还是其次,对SMT成品寿命或可靠进行研究都会了解到,成品寿命和可靠性是不能从一般的生产检查中得到任何住处,加以分析就能获得。视程度而定,不良品的出现,很有可能是产能或制程能力(Proce Capability)不足的一种表现。如果生产线的制程界限(Proce Window)不能配合成品的设计要求,头号题就不是只出现不良品和浪费资源那么简单了。在不良(或不够好)的制程下生产的成品,具有寿命代名词危险性,但不是所有的缺陷都能在生产线上的检查工序中被发现的。这就解释了一些成品在用户使用不久后便失效的原因。我想大家都能想象这类情况对公司或品牌的影响,这才是真正的危机所在。虽然目前仍没有十全十美的寿命保证生产方法,但制程管理在这方面的处理,通过其设计、调制、监控、改进四大步骤,在效益上较制造管理方法大大的提高了。 由于较缺乏制程管理中的调制管理以及灵活而深入的监控 工作、制造管理下的生产能力的稳定性一般都较差。而这也是对优化和改进发展的一大事故,和在好些方面都处于难以突破的局面。制程管理中对制程能力的制定和应用有较严格的管制,而稳定性是制定制程必须考虑到的因素,并且是首要的工作之一。对生产能力有了实在的了解和稳定的控制后,改进和优化工作才能接着进行。
在了解制程管理和制程管理的过程中,也带来了设备的配置、改进设计的学问和全面改进的好处。由于制程管理中重要的一节是制程整合(Proce Inetegration),而在处理制程整合的工作中必须对设备技术和产品的生产设计有很好的了解和配合,这就要求技术人员在这些方面进行学习、研究、了解和应用。而此做法也正好迎合SMT对技术整合的依赖性。也只有通过对这些全面的学习应用,才能达到长期的改进,才能作出最优化、最低成本的生产作业。
另一个制造管理日益难以应付的问题是SMTR 快速微型化。微间距IC、0402和0201矩形件、微型BGA、Flip-Chip等的出现已对检查工作造成不便,甚至带来了不实用的压力。但如果我们在这问题上作根本的考虑,问题其实也不怎么存在。检查作业是项没有附加价值的工作,为会么我们在生产过程中需要检查?这便是因为生产能力 稳定性不足面不能有足够信心确保成品质量的。其实如上面所提到的,检查作业并不能最有效的确保寿命和质量(甚至误导而使我们相信成品具备足够的寿命)。既然检查作业是花费而又不完整的工作,那是否有更好的做法呢?制程管理就是个可能的代替方法。在成熟的技术上、良好的制程管是有可能废除某些检查作业的。虽然我们知道不会有十全十美,但如果通过制程管理而在某一工序上能达到制程能力掼标(Proce Capability)为2以上时,你是否还需要检查作业?我们一直沿用的检查作业,很多时候是因为没有学习和使用制程管理法,而不是毫无选择的做法。
制程管理,是一门先质后量的管理。在未能保证品质的情况下提高产量,只会造成浪费和损失(材料、时间、设备使用、能源的浪费和公司名誉上的损失)。乍看之下,采用制程管理似乎会带来生产投入较慢、交货期较不理想的问题。其实这情况只有在学习的阶段会出现。一个成熟的制程管理系统,在生产接入的时间上是能很快速的。而当投入生产后,其在免除浪费上所回收的利益,却是制造管理所望尘莫及。所以真正的制程管理是项质、量兼收,稳定优化的管理方式。
什么是制程管理
制程管理,好些工厂把它当作只是工序的制定和执行。此所以许多工厂管理都以为本身有采用这方面的管理;其实真正有用的市 程管理远较此复杂。它包括了四大主要部分:制程设计、制程调制设定、制程监控、制程改进。其中制程监控又可细分为监督和控制两部分。以上这些都必须完整的包含在整个制程管理的活动中,缺乏任何一项都不能算是推行制程管理。此外,制程管理并不是独立运作的一门管理技术。它也必须配合产品设计、设备技术和质量水平要求来进行。让我们来看看它们之间的关系。制程设计,这里所指的不只是制造过程的工序(如锡膏印刷),还包括工序中所需的工艺参数(如刮刀压力、速度、模板分离参数、印刷间隔等等)的订立。这工作在新的管理应用中是和产品设计同步进行的、通过使用并行工程(Concurrent Engineering)概念和做法来实现。制程设计受限于现有设备的特性、功能以及厂内对品质的要求,所以必须制定设备在这方面的极限值,而后加以配合来设计。如果一家工厂拥有好些不同档次的设备,则管理上须牺牲某些较好的制程能力,或采用较复杂的生产管理安排。制程设计是整个制程管理中至关重要而相当复杂 的一步。要求技术人员对工艺、设备、设计有很好的认识,以及部门间良好的沟通。由于制程设计受限于设备,对初次使用SMT的用户来说在处理上就有和现有SMT设备的用户不同的地方。这点读者须留意。
制程调制设定,是如何将制程设计的结果应用在生产线上的工作。这要求技术人员对设备的特性、功能以及如何操作有很好的了解。设计未必能一次完整无缺的把所有制程参数都定得最优最完善,这阶段工作也具微调改正的责任。同时,这阶段工作也对调制后的制程能力做计量,并初步检讨制程设计时定下的监控方法。以作为全面生产时开始的制程监控参照。也是设备保养维修部门日后技术目标的参照。
制程监控,是确保生产效益的和质量的重要活动。由于生产线上的变数很多,设备、人员、材料等等都有其各自许多变数,每天在不同程度上的互相影响,互相牵制着。如何能采取有效足够的监控又不会影响生产以及提高生产成本,是一项不易做得好的工作。另一和制造管理很不同之处,是真正制程管理注重于不良品的预防,而制造管理则流于对不良品进行返修改正。在制程管理方面,要求员工具备良好的测量知识、统计学知识、因果分析能力、以及对设备性功能的深入了解等等。
制程改进,也是制程管理技术优于制造管理技术的重要之一。制造管理,在生产演化的路程上进展太慢,甚至相对工发展来说是在退步。制程管理。由于通过较科学性的管理,由於不断的在收集生产资料、分析生产资料,以及注重包括设计在内的全程整合处理,对生产和选题的改进提供了十分有利的条件。有了这方面的活动、制程管理不单给工厂带来生产效率和质量,也同时带来不断往前改进的工具。
制程管理的应用,不应只停留在厂内。很多时候SMT工厂所处理的工作,只是限于电路板的组装(如组装加工厂),或由电路板的组装开始,到完整产品如电脑、VCD等。在这情况下,工厂所能控制的,也只是由原材料如元件的进货处理开始。但我们都知道,成品的寿命和质量包括了各元件的质量,厂内进行的组装质量也受元件质量的影响。其实在我的工作中就发现元件如基板等常是影响生产质量的主要问题之一。所以,在步向零缺陷的目标路程中,我们必须通过交流合作把制程管理推广到元件供应商处。这方面的工作当然自己厂内的更难执行,但却是应该努力的。
你还需要什么?
在制程管理中有一关键性环节,就是组织上应采或混合采用矩阵组织结构(Matrix Organization),这是制程有效与否相当依赖整体制程的关联性处理能力的缘帮。因此在厂内的组织上必须要有一个或一组能应付这类需求的人员(请参考上几期‘中国SMT厂家最解决的是什么问题?’的系列文章)。制程管理是一种管理方法,它并不会自动生效,所以你必须在执行时同时借助技术方法如工艺技术、设备技术等知识的支援,方能见效。没有这些方面的知识,低温 不可能的把制程管理应用得好的。
结语
在今天SMT市场中要确保竞争中,采用制程管理法是不可或缺的。国内许多SMT用户还未了解这门管理,遑论加以应用。这对眼光正确和行动迅速管理者是一个领先竞争对手的大好机会。 由于采用制程管理的优点,加以业内已存在拥有这方面知识经验者,尚欠的只是SMT用户是否意识其重要性,因此SMT业界采用制造管理只是时间的问题而已。但有一点可以肯定的,今日不行动就不能把握同伴的机会,他日可还落得为了不被淘汰而挣扎求存的境况。希望本文能让读者认识到为什么制程管理对SMT是那么重要,并把握国内目前正处发展情况的机会,立即开始进行改革工作。
第18篇:制程品质管控制度
----------------------------精品word文档 值得下载 值得拥有--------------- ------------------
1.目的
为了进一步提高进料及生产过程品质,规范品质作业流程,降低不良率和资源成本,特制定此制度。 2.适用范围
观澜工厂(以下简称为本公司)生产过程。 3.权责
3.1生产部:负责产品的生产、生产工具的保养、品质异常发生的改善执行以及品质控制。3.2品质部:负责产品的品质验证、品质异常的反馈、监控和改善效果追踪。 3.2工程部:负责产品质量、效率的验证,质量异常事故的分析和改善对策。 4.作业程序及说明、4.1软件下载/校准
4.1.1软件工程师必须依据生产工单使用相对应的下载软件、校准平台,并调试好设备和参数供操作人员作业。4.1.2生产拉长教导操作人员对产品的状态标识和静电防护,并每小时填写《工位报表》。 4.1.2所有机型使用的软件和校准平台由工程技转负责列出对应表,并及时更新可供查阅。 4.1.3IPQC每小时对此工位进行确认(产品的标识/不合格数据),并及时反馈给相应人员。 4.2上线前物料确认
4.2.1 生产依《PMC生产计划工单》,由物料组提前领料,物料必须与工单的BOM中的要求相符合,物料员在发料时应确认所有物料是否有原始物料标识,如仓库拆分包装发截料或者尾数物料,物料员应拒收,如发现有不符时要求仓库人员更换正确的物料。
4.2.2 物料员根据生产计划及BOM清单认真核对物料确认无误后,上到生产线,如当物料,为散料或未标识清楚规格描述的,必须经过工程、IPQC等多方确认无误后方可使用,并作好相应记录,以便追溯。 4.3机身标与彩盒标核对
4.3.1 工程部打标员根据生产计划将标打印出来后分拉别整理放好,由生产线物料员领至产线,送检至品质部IPQC处,IPQC根据各机型做货细节核对标签,核对准确无误后发至产线使用,如发现有问题如错误、模糊、多字、少字现象将标退回重新打印。 4.4开始生产时准备工作
4.4.1开始生产前品质部IPQC确认电批扭力、烙铁温度都在规格范围内;
4.4.2开始生产前工程部技术员对生产线仪器进行点检确认如耦合测试仪测试偏差;4.4.3开始生产前生产部对生产线员工到位情况进行确认同时进行静电环点检; 4.5首件检验作业
4.5.1各相关准备工作完成后,由在线拉长对每班/每工单/每开线首件完成品之外观和性能进行确认(其中含人、机、料、法、环)。。
4.5.2 生产线拉长在IPQC核对物料无误的情况下开始生产,生产最初5PCS产品进行检验确认,确认无误会送检品质部IPQC进行首件检验;
4.5.3 IPQC收到首件产品时根据做货细节对产品进行检验,同时完成首件检验确认表的填写,确认无误后送检驻厂品质进行检验。 4.6正常作业程序时
4.6.1 IPQC需对所有工序段巡回检验与稽核(含人、机、料、法、环); ----------------------------精品word文档 值得下载 值得拥有--------------- ------------------
4.6.2生产现场是否悬挂SOP,是否和生产机型相对应,作业人员是否按SOP进行操作;4.6.3生产中的换料状况确认,更换新物料上线时必须对物料的正确性进行核对; 4.6.4 所有设备参数(如烙铁温度、电批扭力等)是否正常,是否有员工私自调整现象; 4.6.5各相关静电防护措施是否确实执行;
4.6.6制程中之不良品是否与良品区分,并放置于指定区域;4.6.7特殊材料(如主板、屏、等)的作业是否符合其性能要求; 4.6.8所有报表是否如实、准确,填写是否及时; 4.6.9相关材料储存环境及摆放是否符合质量要求;
4.6.10生产过程中作业规范是否符合作业要求如漏检、错检;
4.6.11生产过程中各工序堆积不得超过5PCS,超过则需用托盘装起待处理;
4.6.12生产过程中各检验人员是否按要求项目检查,有无打上自己的记号标识,并用打数器记录检验数量;
4.6.13制程中进行巡回检查时需将点检数据实测值记录在《IPQC巡检记录》上,如发现不符合项以IPQC工程巡查项目与对策发出,由该线体责任人进行对策。5.1异常处理,参考《不合格控制及纠正预防程序》 5.1.1备料异常: IPQC人员经与BOM或相关文件数据检验,发现料况异常时,立即通知相关人员,且知会生产部与品管拉长级以上管理人员确认后,换上正确材料。 5.1.2首件异常: IPQC人员发现首件异常时,立即知会在线拉长、在线工程师及品管拉长级以上人员,并开出品质异常单,确认后请责任人员分析异常原因,提出改善对策,IPQC将结果记录于「产品首件记录表」上,IPQC复核OK后方可生产。 5.1.3生产过程中异常: IPQC人员巡检时从人、机、料、法、环对各段进行确认,异常时立即反映给相关人员,由责任人提出原因分析与对策。
5.1.4 品质IPQC的巡检过程中发现漏检、漏贴等现象,经发现需对产线线长及操作员进行处罚,第二次发现需对主管进行处罚;以此类堆。此另QA在检验中发现漏贴、漏检,(在QA前的产品要求全部返工)如因生产制程引起的不良由生产部拉长给出长期改善措施,如因来料不良则由品质部IQC进行对策及给出长期改善措施。IPQC人员复核改善后之状况,如NG进行重新对策,OK则可正常生产。
5.1.5出现质量异常时,IPQC人员应及时向上反映,由品质拉长级以上人员会知工程部门,工程人员立即对质量异常进行分析;若为重大异常由主管级以上决定停线或立即召集相关部门召开MRB会议解决;IPQC追踪对策后之效果。 6.1 异常追踪
所有异常之改善对策,IPQC需复核之,若复核结果未改善或改善不彻底,需重新提出由责任单位完全改善为止;若预防措施中有对相关部品尺寸作修改或参数变更等类似问题,经工程部试作OK后,发出标准化文件。 7.1产品维修
7.1产品维修必须由经过专业培训上岗的维修人员方可进行;
7.2维修人员必须按照维修作业指导书进行操作,并在维修后检查维修结果是否OK,如无问----------------------------精品word文档 值得下载 值得拥有--------------- ------------------
题原标签保留统一由半成品工位投入维修品。 8.1 OQC抽检
8.1.2生产功能测试及扫码查码测试完成后,由生产拉长以批次100/批送检至OQC进行最终检验,现阶段品质OQC对产品进行外观及功能全检测试,在全检过程中发现同样功能不良超过3PCS时(含三台),不同功能现象超过5PCS时,同种功能连续超过三批时,此线体产品将停止检验,由OQC处至LQC处产品全部由该线体LQC重新进行检验后再次送检。8.1.3 QA检验过程中发现的不良问题点进行统计,以作为生产线体考核评估之依据。同批相同功能不良超过3PCS,不同功能超过5PCS,由品质部OQC开出品质改善对策书给到责任线体,并由责任人回复纠正措施,OQC跟踪改善效果。若叛定合格,则由生产部送驻厂QA进行成品检验。 9.1停线处理原则
9.1.1当IPQC核对生产线未按要求作业时如物料没有标识上线,导致IPQC无法确认物料来源及准确性而产线物料员又不能给出准确物料信息时IPQC有权利暂时停止生产。
9.1.2当在某时段或1小时内是因人员操作因素造成不良率﹥10%时,而对策1H内无有效对策时。
9.1.3当在某时段或在1小时内功能测试不良率﹥15%或单项不良率﹥5%时,而对策3H内无有效对策时。
9.1.4当生产在更换物料时没有反馈IPQC确认,出现用错物料,IPQC有权利暂时停止生产。10.1处罚原则
10.1.1当发现产线有漏作业工序如扫完码后不查码、不对标私自取消作业工序现象时处罚20元;
10.1.2当发现产线有漏检测试项目时如功能测试内其中一项不进行测试时处罚20元;10.1.3当发现产线有漏耦合测试时处罚20元;
10.1.4当发现产线有漏打螺丝时,而产线外观检验没有检出流入QA处者一同处罚20元 10.1.3当发现产线同一员工同样问题连续出现三次时;IPQC有权限以每次罚款20元的处罚开出罚款单交由该线体拉长确认后由品质部文员收回交财务部生效。
10.1.4 当发现产线操作员及相关人员拿产品不轻拿轻放者每次处元10罚款,多次提醒未改者处罚50元/次
10.1.4 QA在全检由LQC检验OK的机器时,批次合格率必须达90%以上,不合格率超出10%处罚20元(不包含INT现象)
10.4.5 驻厂QA抽检严重缺陷每批以100元进行处罚,品质QA负责70%与产线负责30%责任。
10.4.6 如因人为因素导致客户投诉,没按正常下机或返修流程导致不良流至客户处责任人处于100元一台坏机的罚款(QA和产线并罚)!
11.1 在清尾机器,产线在生产中一定要按流拉细节操作,以免造成出现漏加工、错加工;送检时一定知会QA注明,QA对清尾机器加严检验; 12.1 奖励制度
12.1.1 每个岗位发现前一岗位出现漏现象者奖励50元。
12.1.2 产线人员发现品质人员没有按照检验规范要求者奖励50元。
11.1相关文件 ----------------------------精品word文档 值得下载 值得拥有--------------- ------------------
11.1.1 《产品监视和测量控制程序》 11.1.2《不合格控制及纠正预防程序》 12.1相关记录
12.1.1《维修记录表》 12.1.2《在线检测日报表》
12.1.3《IPQC工程监查项目与对策》 12.1.4《品质异常单》 12.1.5《IPQC巡检记录表》 12.1.6《罚款单》
拟定: 审核: 批准:
第19篇:先进半导体制程与材料选择
半導體科技 >雜誌導讀 >技術專文
先進半導體製程與材料選擇
作者:宋健民/中國砂輪企業股份有限公司總經理 日期:2008/12/10 來源:半導體科技
人類的物質文明可以說是建立在「材料科技」上,從史前的石器時代,到發明文字後的鐵器時代,或從近代的塑膠時代,到現在的矽晶時代,都是材料科技的里程碑,而物質文明的巔峰極緻將為「鑽石時代」...工欲善其事,必先利其器,鑽石,在現今環境裡,不再只是首飾,在工業應用可是極為重要的礦材,在一般工業用途最常見用於切割,為了在車床上做良好的切削,車刀本身也應具備足夠的強度、硬度、而且耐磨、耐熱。其中尤以鑽石刀具,常用於高級表面加工時,使用圓形或表面有刃緣的工業用鑽石來進行光製,得到更為光滑的表面。
鑽石時代
鑽石不僅質地堅硬,也早已成工業製造中不可或缺的超級磨料(每年使用1,000公噸),它同時也是特性最優越的半導體!鑽石性能遠超過現在的主流矽晶。「鑽石」更已用在矽晶半導體的生產上(如台灣領先世界的鑽石碟)。此外,鑽石可成為矽晶積體電路(IC)最好的絕緣體及CPU最快的散熱面,有如下述。
摩爾定律
人類科技進步最快速的產品,即為積體電路(Integrated Circuit或IC)。1965年Intel的共同創始人Gordon Moore,曾大膽預言電腦CPU上的電晶體數目會以倍數成長,這個所謂的摩爾定律 (Moore’s Law),迄今仍以每18個月成長1倍的高速持續挺進。由於電晶體的倍數成長已超過40年,2007年Intel推出的Penryn4核心晶片上竟有高達8億2,000萬個電晶體。
圖一:摩爾定律使IC內電路的線寬急速變窄,而其厚薄的差異更只有線寬的1/10,這種設計規格,使製程的困難度大幅提高,因此IC電路極小時,電流信號(Signal)與亂流雜訊(Noise)就難以區分。
45 nm IC 由於電晶體越來越多,它的尺寸越來越小,而聯結電晶體的電路(Interconnect)也越來越密。上述的Penryn晶片線寬已小至45 nm,相當於較小的濾過性病毒(Virus)。可以這麼形容,Penryn是藥片大小的晶片,其上密佈接近中國人口總數,但比病菌小10倍的電路開關。
2007年,只有Intel及台積電(TSMC)有能力量產45nm的IC。但全球的其他主要半導體大戶,都加入IBM聯盟(Consortium)合作發展45nm的IC製程,預計在今年許多聯盟成員將陸續導入量產45nm的IC。
圖二:2007年Intel推出以High K Metal Gate的Penryn晶片(45nm)。
半導體的三國演義
值得注意的是,IBM不僅將移轉45nm的技術給晶圓代工的韓國三星(Samsung)及新加坡特許(Chartered Semiconductor),更將技術賣給了中國的中芯。
中芯已開始規劃在深圳成立研發中心,及建設8吋和12吋兩座晶圓廠,準備接收IBM領先世界的技術。中芯本身也開始在12吋晶圓上生產65nm的IC。台積電及聯電雖是晶圓代工的龍頭,但面對IBM的技術輸出,將會被北、中、南的低價製造者聯合夾殺。Intel早看出國際無力封殺中芯,因此就進行「以華制華」,它正緊鑼密鼓在大連建立12吋晶圓廠,將在2010年量產90nm的IC。可嘆的是台灣目前仍只准8吋晶圓帶180nm的技術登陸,以原始的武器和先進的對手「境外交戰」。
中國已成為世界最大的晶片市場,2010年中芯規模將超越聯電,其製造成本會低於台積電。台灣晶圓代工主導世界的時代可能結束。台積電應和聯電聯盟或合併,組成「台聯」對抗中、韓、新的3面包抄。台積電更應和中芯停止互控,在法庭外合解,雙方甚至可討論如何分工生產,以華人晶片佔據中國市場。「台聯中」可和Intel及IBM聯盟演出「三國演義」,這樣台灣就可以持續主導未來的晶圓代工。
圖三:IBM聯盟展示HKMG所製32nm IC的晶圓。圖中的聯盟成員代表包括IBM、Freescale、AMD、Samsung、Chartered Semiconductor、Infineon等公司。
High K Metal Gate
世界晶圓大戰的下一個關鍵,乃是發展32nm的製程技術。當電晶體的Gate Gap進入這個「次病毒」的領域時,其電極(多晶矽)的電阻太大,而且電流不穩,必須改用金屬(Metal Gate)。更有甚者,絕緣層(二氧化矽)變得太薄(<1nm),只有不到10個原子的堆疊高度,這時電極的電子便會穿隧過去 (Tunnel Through),其結果為不僅造成漏電,而且使電晶體的開關信號難以辨認。
Intel為了解決這個漏電問題,在設計45nm IC時就把電極改用鉿合金(Hf Alloy),而其絕緣層則改為鉿化物(HfO2或HfC)。由於鉿化物的誘電率(Dielectric Constant或K)比氧化矽高得多,這種介金屬層的厚度可以加倍(>2nm),因此避免了穿隧的漏電。Intel的HKMG(High K Metal Gate)已用在Penryn的晶片上,其設計將延伸至32nm線寬的電晶體IC。IBM已驗證HKMG可用在32nm的SRAM晶片上。台積電雖成功的試製32nm的傳統IC,但尚未成功的開發HKMG。聯電仍未生產45nm製程,更惶論HKMG了。
圖四:電晶體漏電示意圖。
半導體的散熱
Intel雖以HKMG解決了穿隧的漏電問題,但卻有更多的電流,經矽晶本身漏掉。原來矽晶為半導體,並非絕緣層,當線寬細到45nm時,經矽流失的電流已高達1/3。為了阻絕漏電,法國的Soitec發展出氧化矽絕緣層墊在電晶體下。這種技術稱為絕緣底半導體(Semiconductor On Insulator或SOI)。
SOI已大量用在電晶體緊密的晶片上,例如NVIDIA的繪圖晶片、及Sony的遊戲晶卡都用SOI晶片。然而SOI解除漏電危機,卻惡化了另一個更大的問題,即目前半導體業束手無策的散熱瓶頸。晶片的生熱速度與熱源密度,已遠超過煮飯的電爐,所以用晶片煮蛋會比電爐快得多。過去摩爾定律除了加密電晶體外,也同時加速電晶體的開關速率。但當這個速率快到4 GHz時,電晶體就有燒毀之虞。Intel不能解決這個問題乃將單核心拆成雙核心。
Intel又將電晶體的時脈(Clock Speed)降下,再加大晶片把熱源分散。但這個轉進策略只是以空間換取時間,當線路的寬度更窄時,生熱的速率更快。Intel被迫只好將雙核心再拆成4核心,而8核心的產品也已經上路。這種多核心的設計無法將CPU的運算能力發揮盡致。台灣已製成鑽銅散熱片,其熱傳導率可倍於現今散熱最快的銅散熱片。這種快速散熱片可避免晶片分成多核心而可組回單核心使用。
鑽石底半導體
SOI以氧化矽阻電,但氧化矽卻同時阻擋了熱流,所以晶片的時脈更難提升,為徹底解決這個難題,台灣發明了鑽石底半導體(Semiconductor On diamond或SOD)。鑽石的熱傳導率(>1,000 w/mk)比氧化矽高10倍以上。尤有進者,鑽石的晶格是所有材料中最穩定的。以SOD製造32nm的IC不僅可以降溫、加速,還可以避免背景輻射所引發的亂流(Noise)。32nm電晶體的電流信號極為微弱,因此矽晶內自發的雜訊(Noise)會干擾開關狀態判別,SOD新技術則可把雜訊降到最低。
IC內的熱源,除了電晶體的開關及漏電外,也來自銅導線內電流所生電磁波彼此的干擾(RC Delay)。為了隔絕電磁波,銅線乃以低誘電(Low K或LK)材料製成。LK材料內含大量氣孔,所以非常脆弱。當線寬縮小到32nm時,LK材料的氣孔率大於50%。這種脆弱材料不僅難以蝕刻,更不能在CMP時拋光。
此外,LK材料也容易吸附水氣,變得更易於變質。幸虧台灣已發明先進鑽石碟(Advanced Diamond Disk或ADDTM)。CMP時ADD可以低接觸應力,快速拋光晶圓。LK材料也可使用鑽石和鐵氟龍的網路沈積生成,這樣不僅可以微影蝕刻,也不會吸附水氣。
全碳積體電路
電腦的中央處理單元(central Proce Unit或CPU),乃以矽晶製造電晶體(Transistor),再以銅線連接(Interconnect)。電晶體的開關乃以High K Gate (如Hf化合物)控製,而線路之間則以Low K Dielectric (如含HF的SiC)絕緣。
碳是奇蹟的材料,它可形成導電率比銅高的單晶石墨層(Graphene),石墨層可蝕刻成為奈米電路,層間可以奈米碳管導通。石墨和鑽石可以交互數層原子堆砌成超晶格(Supperlattice)。碳的超晶格具有極高的誘電(K)能力,但卻不會漏電,而且它可以在高電場下運作。這種未來材料可取代鉿化合物的High K Metal Gate。除此之外,碳可和氟形成鐵弗龍(Teflen)似的網狀結構,具有極低(K=2)的誘電力和極高的電阻,它可取代現行的Low K脆弱材質(如Black Diamond)。
上述的夢幻設計可組成全碳的電路,其性能將遠勝於現有的任何設計。全碳IC可延伸摩爾定律至線寬10nm以下。不僅如此,石墨及鑽石散熱速度超過銅的多倍。全碳CPU有內建的散熱系統,它可使電晶體的運作頻率遠高於4GHz。摩爾定律的CPU原來為單晶片,但因不能解決CPU散熱問題,於是拆成多核心,而靠加大面積避免熱源過度集中。
全碳CPU可使多核心重合成為單一晶片,讓摩爾定律回歸正統。
尤有進者,鑽石半導體比矽晶耐溫及抗壓,而且它的運算快速。鑽石的P型半導體可填入比矽晶更多的硼原子,而使電洞的濃度大增。鑽石的N型半導體可以鋰氮(LiN)滲透製成。鑽石半導體可和上述的全碳IC整合製成全碳CPU。由於鑽石是散熱極品,全碳CPU的體積會比矽晶小很多,但速度可高百倍。這種「神算機」可把人類的物質文明推上顛峰,進入永遠的鑽石時代。
台灣的科技向來尾隨西方的先行國家,但全碳CPU的發展可以領先世界。台灣政府若有遠見應該加速發展鑽石科技把缺乏資源的台灣建設成為「鑽石島」。摩爾定律所面對的漏電、散熱、拋光等難題都可以台灣的鑽石科技迎刃而解。
450mm大晶圓
晶圓生產的成本,受限於晶圓上的晶片多寡。台灣雖已加碼投資300mm晶圓廠成為最密集的生產國家,但Intel、TSMC、Toshiba、Samsung已在規劃試製450mm(18吋)的晶圓,預計在2012年導入量產。但這麼大的晶圓其直徑比線寬大數千萬倍,加上線路的電流對線寬的敏感度大增,晶圓表面在CMP拋光時其平坦度比300mm要求更高,目前的CMP技術根本辦不到。
圖五:Intel的Mike Goldstein手持矽粉燒結的450mm晶圓,及未來晶圓表面可能密佈電晶體(電流開關)的示意。這種大晶圓與小線寬(22nm)的比率可超過千萬倍(107x)。一片晶圓上旳電晶體總數將超過全球人口總數的百倍。
幸虧台灣推出ADD鑽石碟,可以把拋光墊表面修整得非常平坦但卻不溜滑,這樣就可把大晶圓快速拋光,而不傷及纖弱的銅導線路、與有氣孔的Low K絕緣及堅硬的High K Metal Gate。SST-AP/Taiwan
圖六:ADD的面相(左圖),其尖錐乃以微米鑽石在超高壓(6GPa)及高溫(1400℃)燒結製成。這是台灣產品壟斷全球獨一無二的設計。右圖為下一世代的IDD產品,它乃由氣相沈積的多晶鑽石構建而成,這也是台灣的獨門絕活。
作者
宋健民,現為中國砂輪企業股份有限公司總經理,亦為鑽石科技專利發明人。在CMP的領域,作者亦為台灣品牌DiaGrid鑽石碟及ADD鑽石碟的發明人,亦協助Applied Materials發展eCMP,現正協助韓國的SKC及台灣的IVT研究次世代的CMP Pad。
第20篇:质量管理IQC与制程整改建议
针对协作部门对于本部门两项投诉内容的改善意见和建议
2011年11月10日会后分析报告
报告人:颜 佳
针对协作部门对于本部门的两项投诉内容,11月10日上午本部门召开了内部通告会议,方经理传达了协作部门相关投诉内容,现场要求各生产车间QE工程师总结两方面的原因并做出改善意见和建议。现针对IQC重复发生来料不良以及生产线制程控制环节薄弱这两个投诉问题提出一些自己浅显的意见和建议,希望能够帮助部门内部的流程完善,一线品质人员的判定立场和原则得到提升。
首先,说一点题外话,但还是以质量管理的八项基本原则出发,强调过程和方法,一切变革,改善都需要由内而外。只有先解决了内部问题,才能够着手去解决外部问题。否则将是事倍功半,达不到预期效果。正如“其身正,不令而行。其身不正,虽令不从。”道理都是很浅显的。但是作为目前的质量管理部内部的队伍建设和整个氛围,都是各自为政,已经形成一个凡事先从外部找原因的思维定势。
所以,这里需要强调的是人与人之间的沟通及观念的提升,“天下事非一人之所能独力,事事欲有所为,必与其类同心共济”,搞好品质不是靠一个人或者几个人就能把事情做得好,也需要一个分工协作的过程,各个部门不一样,立场也就不一样,看问题的角度自然也不一样。所以这就对于质量管理人员来说,必须要具备接纳和换位思考的能力,只有接纳他,才能更好的改变他。
要解决这个问题,必须要统一认识,消除沟通失效,这就需要大量的培训和团队活动提升凝聚力和彼此的信任度。
其次,对于制程控制这一块,IPQC专业技能方面,目前仅停留在初级阶段,仅仅是对于产品比较熟悉,对于自身的职责不够清晰。制程中缺失数据监控环节,IPQC在生产全过程,行使的只是基本的现场巡查,抽检和不良判定三大基本职能。就判定这一方面,没有相关标准文件提供支持,造成在线IPQC该判不判,甚至不敢判的情况出现。试想一下,作为生产一线的IPQC而言,只有建议权,而没有行使权,所以我们无法要求他们主动去处理问题,解决问题。我们自然也就无法要求他们有很强的执行力。毕竟人员素质参差不齐。另外一点,我们是否有岗位说明书,是否有将该岗位的作业内容和职责告知该岗工作人员。
要解决这个问题,首先是标准化的建立,完善制程相关文件,以标准文件作为他们的作业支撑,提供给他们可以操作的准则做为依据,其次是充分放权,明确岗位权责,将相应的权利下放给相关岗位和人员,主管领导切实支持各方面工作并加以肯定,以激励他们正确的,有原则性的做出判定和敢于做出判定的能力。其三才是适时的加强专业技能方面的培训。否则我们的一线IPQC人员将变为使用工具的工具,操纵机器的机器,毫无价值可言。
另外,制程不在受控状态的情况,在鄙人刚到车间四天的时间以内,发生了两次,有作业指导书,而且作业指导书上面有相关工序要求,作业人员不按照作业指导书进行作业,现场IPQC不打单,不知会相关基层管理,只在现场对于作业人员进行纠正,而纠正之后仍不在受控状态,IPQC无任何对策,不了了之。那我们还做什么质量? 让你在生产线玩了吗? 有问题也不管,也不知道外部沟通协作,这跟闭门造车有什么分别? 作业指导书作为体系文件的一部分,我们将他视为他律,而在线人员的自律又体现在哪里? 脱离了自律的他律,就等于是白纸一张。
所以说,还是要强调一个全员参与的过程,我们在做品质的过程当中,与其他部门之间的沟通协作是必不可少的,前面谈的要先解决自身问题,但是在解决自身问题的过程当中,这种正常的沟通和协调是有必要的。而部门之间的配合程度,也在一定程度上决定了IPQC是否愿意反映问题。
要解决流程失控这个问题,不仅仅要对于生产全过程进行质量意识的灌输和培训,而更为重要的是人的自律问题。自律对于一线IPQC人员来说,是相当重要的。比如说,政府颁布的法律法规,你去触犯了,你就必须受到相应的惩罚,而且你颁布的惩罚越重,老百姓的自律性就越高。
其三,IQC重复发生来料不良这个问题,就质量管理部而言,首先要理清思路,从源头上着手,解决问题。建立健全供应商管理体系,从各个关键环节入手,对来料进行全面的掌控,只有将主动权掌握在自己部门手上,才能更高质量的保证生产用料的品质。
首先,在新产品研发阶段,专案工程师确认用料涉及到采购的,应向供应商索要承认书,确认该物料可用后,签字确认,并将承认书以及剩余的样本,交到IQC封样存档。该供应商入选IQC合格供应商名录。而由采购新开发供应商,样品应交研发部审核验证,再执行如上程序。
其次,新开发供应商,以降低独家供应商供货风险。保证每个元器件有2-3家合格供应商,可供挑选。这样做的意义,可以从性能,价格,交期三方面进行比较,控制成本的同时不降低产品质量,与供方互利。
其三,将采购的一系列的采购活动,纳入到供应商管理体系的管理当中来,采购活动发生的对象,必须为合格供应商名录之内的合格供应商。否则,IQC对于非在册的物料,有拒绝接收的权利。当然,对于特殊情况,必须作出让步接收的,必须由IQC开具书面材料,说明原因,并请相关人员签字确认,以便于追溯。
其四,在有条件的情况下,比如采购数量较大,尽量使用月结货款的方式,以便于IQC对于物料质量的判定,更具备主动权。另外在供销合同上,建议争取品质管理部门审核的权利,并约定质量方面的要求,可以使用扣款,罚款等方式进行控制。
其五,对于在录的合格供应商,在供货三次以上,无质量问题的情况下,IQC部门可以适度放宽检验标准AQL值。而对于来料检验不良的供应商,应加严AQL值进行检验。同一供应商出现两次来料检验不良,IQC对该供应商作删除合格供应商名录之处罚,并知会采购部门,不得继续采购活动。如需再次加入,必须重新送检,承认。
总之,作为IQC部门,必须充分掌控和健全合格供应商管理体系,使之成为一个闭环,方能更好的保证来料质量以及生产用料。但是,同时也就要求我们的IQC人员,有较强的专业技能和业务水平。整改和整顿的过程是漫长的,只有持续改进,就一定会有效果。当然,也需要内部和外部的各位同仁的大力支持。需要变革的推动者,坚定立场,获得高层的支持,充分发挥领导的作用。以上,仅是本人的一些意见和建议,仅作为参考,如有不当之处,还请批评,指正。
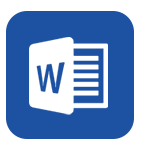