生产制程质量控制程序管理办法
1、目的
通过对生产过程中的工序产品、成品质量的控制,确保不合格的产品不转序,进而确保产品质量。
2、范围
本办法适用于各部门生产过程中及仓库物料、库存产品质量控制。
3、职责
3.1 品质部负责生产过程工序产品、最终产品的检验控制。 3.2 品质部负责生产过程中的质量信息的收集、汇总和反馈。 3.3 品质部负责生产过程中检验状态标识。
3.4 品质部负责编制产品质量改进计划及完成情况的验证及考核。
3.5 品质部负责生产过程中的不合格品的及时鉴别、标识和记录,并负责组织其职责范围内的不合格品的评审。
3.6 品质部负责新产品及更改产品的质量检测记录,参与验证、试装、评审等生产准备过程的质量控制。
3.7 品质部负责提供作业指导书、产品技术条件等文件。 3.8 品质部负责模具最终书面验收及模具技术状态鉴定。 3.9 品质部负责检查各生产部门的日常工艺纪律执行情况。
3.10 品质技术部负责制订或组织制订不合格产品的返工(修)工艺技术方案。 3.11 仓库负责不合格品的处置,定制隔离、登帐、保管、及办理相关手续。 3.12 仓库负责库存产品储存、运输质量控制。
3.13 仓库、生产部门负责生产过程中工序间的运转储存及入库产品的转运质量控制。 3.14 生产部门负责生产过程中的产品自检质量控制。
4、工作程序
4.1 制程控制
4.1.1 品质部负责向生产单位提供生产制造标准及相关图纸、工艺卡。
4.1.2 生产单位按生产制造标准要求调整模具或生产工艺,确保后续产品符合工艺要求。
4.1.3 各生产单位严格落实产品首件检验机制,自检合格后交品质部进行首件检验。 4.1.4 品质部要严格按图纸、工艺卡、检具、样件进行首件检验,检验合格后,贴首件合格证做标识,并填写“检验记录单”。 4.1.5 首件检验合格后操作者应把首件放置在首件区,然后方可批量生产。 4.1.6在批量生产过程中,操作者应随时自检,以首件架上的工序产品作为自检依据,防止批量不合格品的发生。
4.1.7在批量生产过程中,质检员一般在1小时内进行一次巡检,填写“检验记录单”。巡回检验不合格时必须第一时间勒令操作者即刻停止生产,并通知相关生产主管及技术人员处理。
4.1.8 生产过程有机器或模具维修调整、工艺改变的,必须重新进行首件确认,并在第一时间替换之前首件。
4.1.9 五金及注塑件生产时,所有工序完成后,质检员应对该产品进行最终检验,填写“产品检验记录单”,检验合格后,粘贴产品入库“合格证”,注明产品名称、数量、日期并加盖检验章(合格证应粘贴在工位器具上,并清除旧标识)。 4.1.10 冲压车间生产时应尽量安排同一产品几道工序同时生产,为避免批量不合格品的发生,冲压作业员生产时必须不超过30PCS自检一次,下工序员工负责对上工序进行复检;专职质检员对末道工序使用检具检验时,必须同时对前道或前几道工序产品进行检验。
4.1.11 冲压产品首件检验时机:
a)每批产品生产开始,操作者自检合格的第一件产品。 b)设备调整后,操作者自检合格的第一件产品。 c)调整或更换工装后,操作者自检合格的第一件产品。 d)改变原材料、毛坯、工序后,操作者自检合格的第一件产品。 4.2产品运输控制
1、在制品、半成品和未入库的的成品由生产车间进行转运;库存产品由仓库负责运输。
2、在转运及运输过程中要注意防止磕碰、划伤、损坏、变形并保护产品标识和有关检验、实验状态标识,防止丢掉或被擦掉。 4.3 产品贮存控制
4.3.1 生产现场的在制品、半成品应建立适宜的贮存场地,设置衬物垫,产品不能落地,应码放整齐、稳定,防止贮存过程中锈蚀、变形、损坏。 4.3.2 冲压车间必须使用合理的工位器具码放整齐,以便运输。
4.3.3 经检验合格入库的产品,由库管人员用规定的相应工位器具,码放在适宜的场地、库房、货架上。在保证运输工具通行的前提下应码放整齐,排列有序,并防止贮存过程中的锈蚀、变形、损坏。
4.3.4 库存产品应有完整的产品标识和检验、试验状态,不同状态产品要分开存放,做到储存记录清晰、完整、帐、卡、物相符
4.3.5 库存产品由库管人员每月检查一次,做好“库存产品巡检记录”,出库产品应做到先入先出。 4.4 不合格品的控制
4.4.1生产过程中发生的不合格品质检员应督促生产作业员及时分开摆放并做好醒目标识,质检员在相应记录单上做好记录。
4.4.2评审:生产过程中以及后期挑拣发现的不合格品由品质技术部会同生产部相关人员组织评审,根据不合格品状态或用户反馈信息的产品,由质检员开具“品质异常单”,交品质技术部现场技术人员,由技术人员在生产现场提出处置意见。当批量较大,会严重影响最终产品性能,或用户反映强烈的产品,质检员开具“品质异常单”,由厂部提出处置意见,上报公司主管领导作最终处置。 4.4.3不合格品的处置
4.4.3.1不合格品的返工(修),由品质技术部制订不合格产品的返工(修)工艺技术方案,由生产车间负责返工(修)。
4.4.3.2返工(修)后的工序产品、半成品,成品必须交专职质检员复检,专职质检员复检并在相应的记录上做好复检记录,返工(修)合格的产品方可转序或入库。 4.4.3.3不合格品让步使用,必须经产品使用和品质部认可。
4.4.3.4不合格品有明显缺陷不能返工(修)或返工(修)不经济时,授权人员应在“不合格品通知单”处置意见栏填写“报废”,同时注明致废原因,由品质部核实后经厂长以上领导批准方可进行报废。 4.5产品质量改进
4.5.1品质技术部根据用户反馈的质量指标及生产过程中发现的质量问题,分析原因,制订产品整改措施计划。
4.5.2每月初品质技术部对上月质量指标完成情况进行分析,废品损失原因分类,损失严重的产品。提报相关单位分析出致废原因(人为、模具、材料等)以便整改。 4.5.3厂部针对重点品质缺陷以书面形式落实的品质整改方案,责令各责任单位要按要求执行,按期完成回执。
5、奖惩方案
5.1 冲压部当月成品总量不良品返修率低于5%,报废率低于0.2%,奖励主管/五金工程500元,组长/质检员200元,物料员100元;不良品返修率高于10%,报废率高于0.5%,处罚主管/五金工程500元,组长/质检员200元,物料员100元。 5.2 面板/组装车间当月成品总量不良品返工率低于0.5%,最高批次返工低于100台奖励主管500元,组长200元,物料员/质检员100元;不良品返工率高于1%,最高批次返工高于300台处罚主管500元,组长200元,物料员/质检员100元。 5.3 所有不合格产品如未经正常程序私自报废的,对当事员工处以5元/件罚款(员工罚款最高100元/次),当事部门组长罚款2倍,当事部门主管罚款3倍。 5.4 对于厂部以书面形式责令落实的品质整改方案未能如期执行的,当事部门主管第一次罚款200元,并回复具体落实时间,下次还未能落实的加倍处罚。
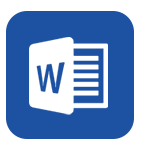